オーバーモールディングでは、剛性の高い部品を慎重に位置決めし、拡張性を確保し、部品の歪みを防ぐための抜き穴を組み込む必要がある。
市場で人気が高まっているツーショット成形は、塗装の必要なく製品の美観を向上させるが、コストが高く、高度な技術が要求される。
2ショット成形やオーバーモールド成形のいずれにおいても、2種類のプラスチック複合射出成形が採用されています。まず硬質部品を成形し、次に軟質部品を成形するプロセスです。類似点はあるものの、これらは異なるプロセスです。以下、BFYの金型エンジニアがこれらの違いを説明します。
ツーショット成形とオーバーモールド成形の違い
A. ツーショット成形
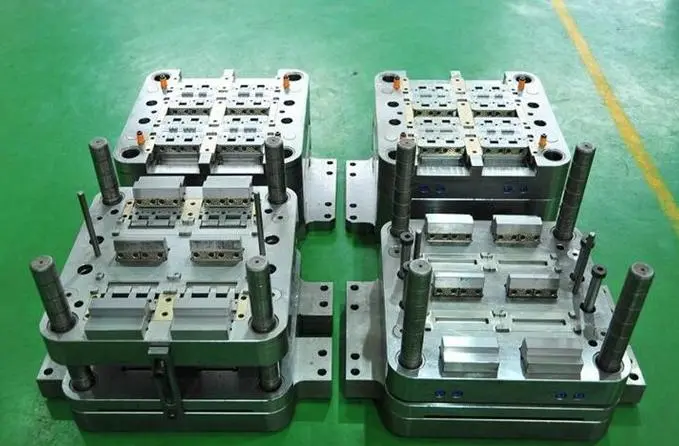
2種類のプラスチック材料を同じ機械に2段階に分けて注入し、単一金型で製品を成形するプロセスです。通常「デュアルマテリアル注入」と呼ばれ、通常は1つの金型セットで完了し、専用の2ショット注入機が必要です。
2色成形金型は、2種類の樹脂と色を1つの製品に統合し、組み立て工程と後処理を削減します。このアプローチは接着や印刷のコストを削減し、視覚的な魅力を高め、製品品質と価値を向上させます。さらに、滑り止め機能や人間工学的設計の向上といった機能も提供します。
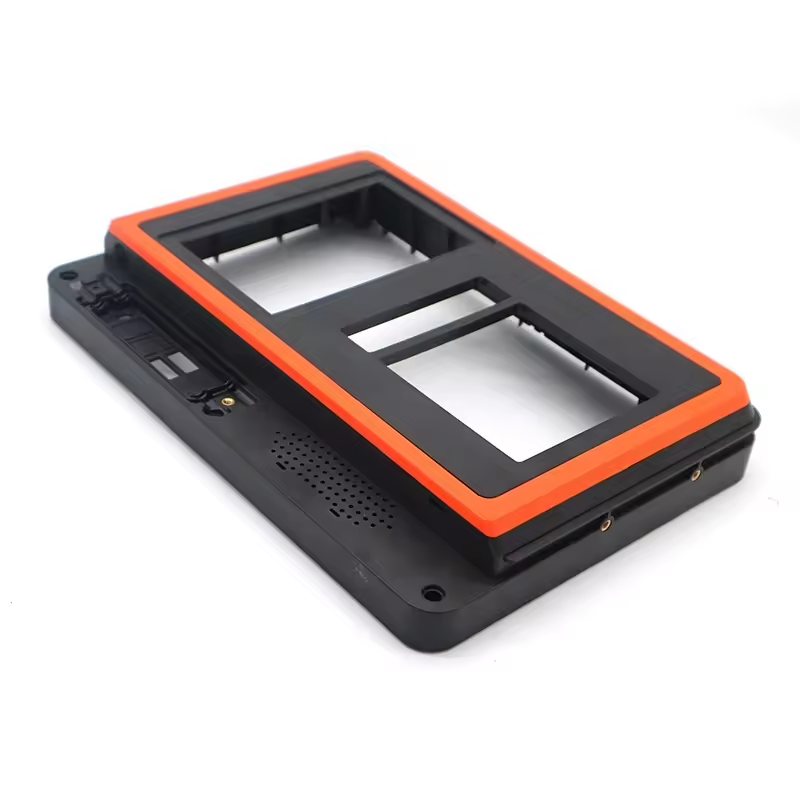
ツーショット射出は、オーバーモールドと比較して、高い製品品質、管理可能な変形、短いサイクルタイム、高い歩留まりを提供し、材料の無駄を7%削減し、製造コストを20%~30%削減する。
B. オーバーモールディング(二次成形)

2種類のプラスチック材料は、同じ機械で2段階成形を行うことはできません。1つの金型セットから製品が排出された後、別の金型セットで二次成形が行われます。したがって、この方法は通常、2つの金型セットを必要とし、専用の2ショット射出成形機は不要です。金型構造は単色射出成形金型と類似しており、主に材料の融合点を調整するために射出パラメーターを調整する方式を採用しています。
オーバーモールドは主に硬い素材の上に柔らかい素材を被せるもので、柔らかい部品にはTPU、TPR、硬い部品にはABS、PC、PPといった一般的な素材が使われる。
対照的な追加ポイント:
1. キャビティ形状は成形方法ごとに異なり、異なる製品を形成するが、コア形状は同一である。
2. 前後型を180度回転させた後、その位置合わせを確実に行う必要があります。この確認は設計段階において極めて重要です。
3. ピンホールの位置には注意が必要です。ピンホールの間隔は210mmと非常に狭くなっています。大型の金型の場合、射出成形機の射出長さが不足するため、金型内に延長ピンを設計し、追加のピンホールが必要になる場合があります。後部金型ベースには2つの定位リングを配置する必要があります。
4. 前型パネルとA板の総厚さは170mm未満であってはなりません。この射出成形機モデルの他の参照データ(大型および小型の型厚さ、ピンホール距離など)を慎重に確認してください。
5. 3プレート金型の場合、可能な限り自動排出用にゲートを設計し、特に軟質材料のゲートの排出可能性を確保する。
6. 前面スプルーの深さは65mmを超えてはなりません。上側スプルーの上端から金型胚の中心までの距離は、少なくとも150mm以上でなければなりません。

7. 2回目の射出成形時にキャビティ損傷を回避するため、最初に成形された製品の位置に空洞スペースを設計することを検討してください。ただし、2回目の成形時に高圧射出による変形の可能性を考慮し、各シールポイントの強度を確保してください。
8. 射出時に第一成形品の寸法をわずかに大きくして、第二成形品のもう一方のキャビティとの圧縮を強固にし、密封性を確保する。
9. 2回目の射出時のプラスチックの流れが、最初に形成された製品に影響を及ぼし、変形を引き起こす可能性があるかどうかを評価してください。その場合、改善策を検討してください。
10. AプレートとBプレートを閉じる前に、再配置時にフロントモールドスライダーまたはリフターが製品を損傷しないように確認してください。もし損傷の可能性がある場合は、AプレートとBプレートが最初に閉じ、その後スライダーまたはリフターがリセットされるように解決策を講じてください。
11. 均一な流れを確保するために、キャビティとコアの両方の水路を最適化し、バランスをとる。
12. 99%の場合、硬い部分から注入し、次に柔らかい部分を注入する。