導入:
射出成形に適切な材料を選択することは、製品の性能、価格、耐久性に大きく影響します。ABS素材とポリカーボネート(PC)という2つの熱可塑性プラスチックは、その強度と適応性の高さから、自動車、電子機器、消費財などの業界で際立っています。では、プロジェクトのニーズに合うのはどちらなのでしょうか?この記事では、ABSとPCの主な違いを探り、強度、耐熱性、費用対効果、最適な使用用途などの材料特性を分析します。
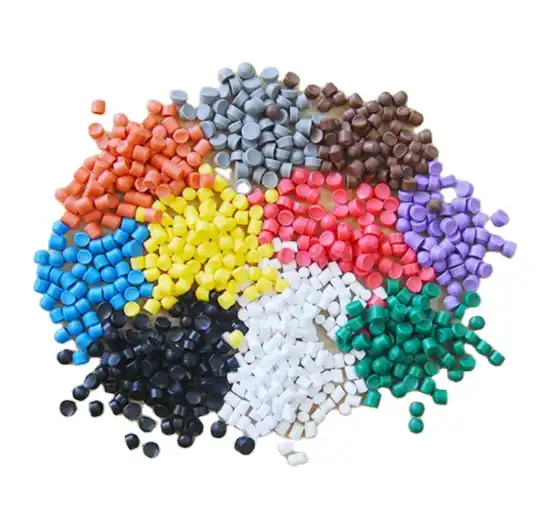
射出成形の台頭:
射出成形は、19世紀後半に誕生して以来、目覚しい進化を遂げてきた。射出成形は、当初は単純で小規模なものを作るためのものだったが、今では複雑で精密な部品を作る高度な技術となった。射出成形は、プラスチックを溶かして金型に注入し、冷却して目的の形状に成形する。この方法は大量生産に最適で、複雑なデザインや複雑な部品を作ることができる。
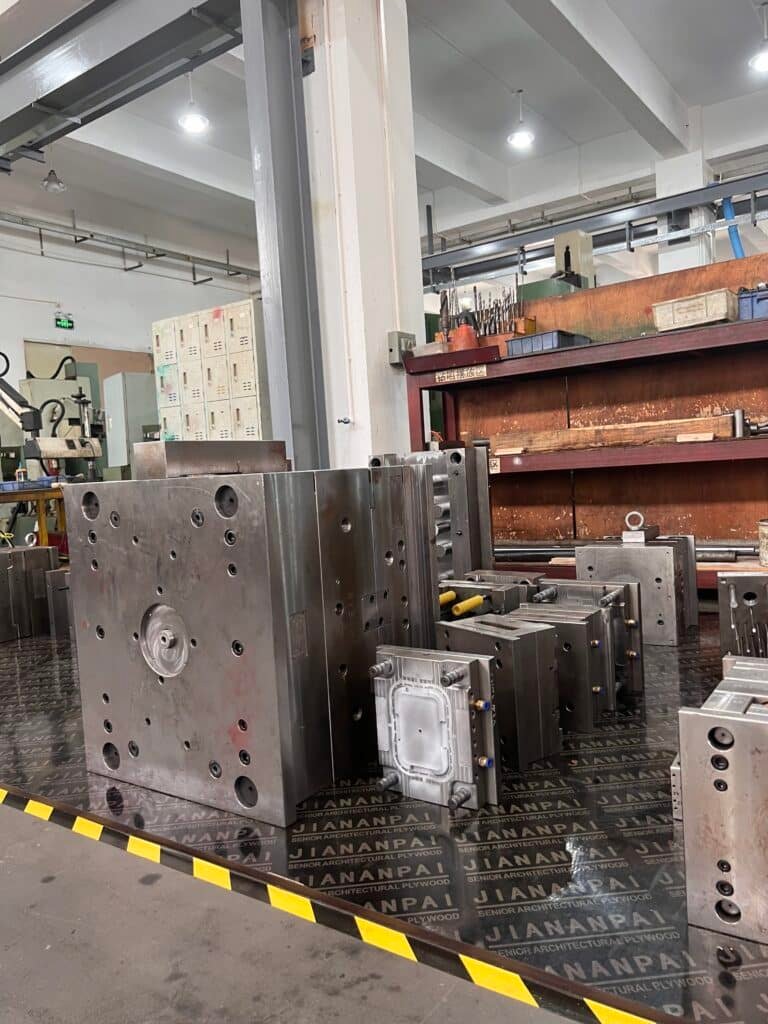
射出成形金型
PCとABS素材:デュアルパワーハウス:
ポリカーボネート(PC)とアクリロニトリル・ブタジエン・スチレン(ABS)は、プラスチック業界において傑出した素材であり、それぞれが多様な用途に不可欠な独自の特性を誇っている。
ポリカーボネートは、その優れた透明性、高い耐衝撃性、耐熱性が珍重され、透明性と耐久性の用途によく選ばれています。その汎用性は、高温に耐え、寸法安定性を維持する能力が最も重要な光学部品、電子筐体、自動車部品にまで及んでいます。
一方、アクリロニトリル・ブタジエン・スチレン(ABS)は、その堅牢性、優れた耐衝撃性、機械加工性で知られている。ABSは強度と柔軟性のバランスが取れており、消費財から自動車内装まで幅広い用途に適している。成形や後加工が容易であることも、製造におけるABSの魅力をさらに高めています。
射出成形プロセス:
射出成形工程は、精度と制御の複雑なダンスである。それは、PCであれABSであれ、原料プラスチックを小さなペレットに造粒することから始まる。これらのペレットは、加熱されたバレルに供給され、粘性のある溶融状態に溶かされる。材料が最適な粘度に達すると、高圧で金型の空洞に注入され、金型の隅々まで確実に充填される。金型は通常、スチール製かアルミニウム製で、最終製品の形状と特徴を決定する。

金型設計
溶融材料が金型内で冷却されると固化し、所望の形状になる。温度、圧力、冷却速度を注意深く制御することは、所望の特性を達成し、反りや収縮などの欠陥を避けるために不可欠である。冷却が完了すると金型が開き、新しく成形された製品が現れる。射出成形は非常に効率的でスケーラブルな製造プロセスである。
さまざまな業界への応用:
射出成形とPCやABS素材の組み合わせは、さまざまな産業で無数の用途を見出してきた。自動車では、これらの素材がダッシュボードやボディ部品の強度(ABS)と透明性(PC)を高めている。電子機器では、PCの耐熱性とABSの絶縁性により、筐体やコネクターに使用されている。
また、PCやABSは玩具、家電製品、家庭用品の製造にも使用されており、消費者向け製品における汎用性を示している。医療分野でも、無菌で耐久性のある部品を製造する上で、これらの材料の利点を享受している。幅広い用途は、PCやABS材料を使った射出成形がいかに現代の製造業の要求に適応し、確実に応えられるかを示している。
結論:
PCとABS素材の射出成形を掘り下げてみると、それらが現代の製造業に大きな影響を与えていることは明らかです。そのユニークな特性と精密な射出成形技術との組み合わせは、自動車部品から電子機器まで、無限の可能性を提供します。