射出成形は、複雑な形状や細かいディテールを持つプラスチック部品を製造するために広く使用されている製造プロセスです。射出成形では、部品全体の構造を作ることに主眼が置かれますが、部品の表面品質も同様に重要です。射出成形部品の表面処理は、その外観、機能性、耐久性を向上させ、様々な産業における美的要件や性能要件を満たす上で極めて重要です。
なぜ表面処理をするのか?
表面処理はいくつかの理由から不可欠である:
美観の向上:平滑仕上げ、光沢仕上げ、テクスチャー仕上げを行うことで、部品の視覚的な魅力を向上させる。
機能向上:耐摩耗性、耐食性、導電性、摩擦低減などの特性を向上させる。
接着促進:接着特性を向上させることで、塗装、コーティング、接着のための表面を整える。
清潔さと衛生:特に医療、食品、飲料産業における衛生要件を満たす。
識別とブランド:ブランドおよび製品識別に不可欠なマーキング、ロゴ、その他の特徴を認める。
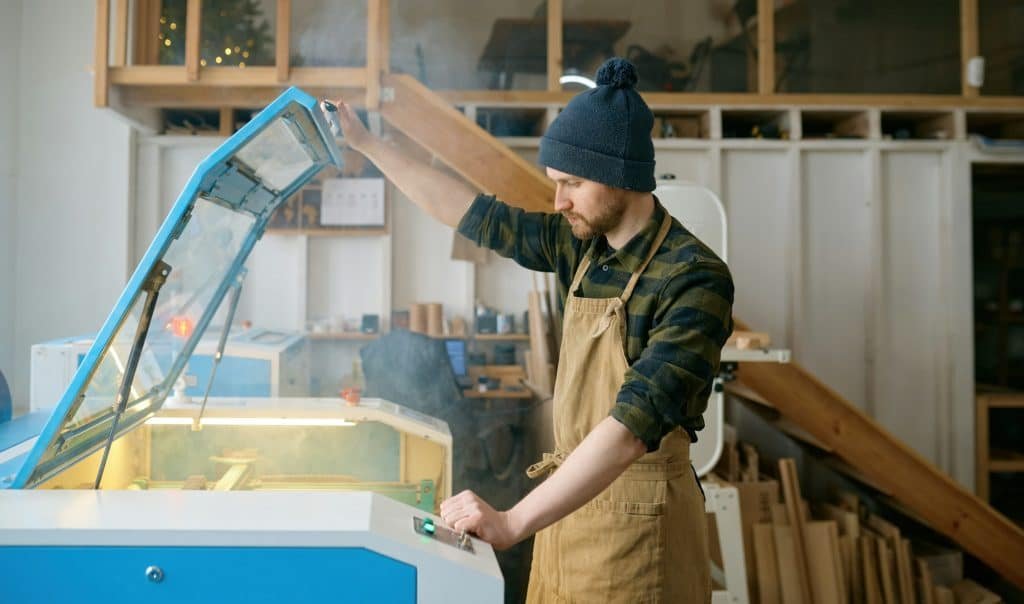
表面処理を決定する重要な要素とは?
射出成形部品の表面処理の選択には、いくつかの要因が影響する:
材料の種類: プラスチックの種類によって、さまざまな処理に対する反応は異なる。したがって、材料の組成によって適切な処理方法が決まる。
最終用途の要件: 環境暴露や機械的応力を含む部品の用途によって、必要な表面特性が決定される。
美的配慮: 色、質感、光沢度など、望ましい視覚的特性は、表面処理工程の選択に影響を与える。
コストと生産効率: 費用対効果と生産時間への影響は、どの処理を適用するかを決定する上で極めて重要である。
規制の遵守: 特に医療や自動車などの分野では、業界標準や規制の遵守が表面処理の選択の指針となります。

表面処理工程の分類
射出成形部品の表面処理工程は、いくつかのカテゴリーに大別することができる:
機械的治療
- 研磨:表面の平滑性と光沢を高める。
- ブラスト: 研磨材を使用してテクスチャーや粗さを作ること。
化学処理
- エッチング:テクスチャーやパターンを作るために化学薬品を使って表面を変える。
- 下塗り: 塗装やコーティングのための下地処理。
熱処理
- 火炎処理: 制御された炎が表面特性を変化させ、接着性を高める。
- プラズマ処理: プラズマを使用して表面を洗浄し、活性化する。
コーティング・プロセス
- 塗装: 美観と保護を目的とした着色塗料を塗る。
- 電気めっき: 導電性や耐食性を向上させるために金属の薄い層を形成する。
- パウダーコーティング: 耐久性と装飾性を備えた仕上げ。
専門治療
- UVコーティング: 紫外線でコーティング剤を硬化させ、硬く光沢のある仕上がりを実現する。
- 真空メタライゼーション: 装飾的または機能的な目的で薄い金属層を蒸着する。
結論として、表面処理は射出成形工程に不可欠であり、最終製品の品質、性能、市場性に大きな影響を与える。様々な要因や処理の選択肢を理解することで、メーカーは特定の業界のニーズや顧客の期待に応えられるよう、製品の表面を調整することができる。