射出成形金型用の放電加工(EDM)は、精密なキャビティ金型製造において広く採用されています。
いわゆる「ミラーEDM」とは、表面粗さ値がRa 0.2μm未満で、表面に鏡面反射効果を有するEDMを指します。一部の精密加工におけるミラーEDMは、手作業による研磨工程を代替し、部品の品質を向上させるため、実践的な意義を有しています。
1. 加工の種類
電気放電加工の鏡面効果は、電気放電加工で生成されるカーボンブラック層と直接関連しています。加工対象部が迅速に均一なカーボンブラック層を形成できる場合、鏡面効果を容易に得られることを意味します。
2. 金型鋼
鏡面効果は、一部の金型鋼のEDMでは迅速に実現可能ですが、いずれにせよ、他の金型鋼では実現できません。さらに、金型鋼の硬度がより高いため、EDM鏡面効果がより優れています。
3. ミラー放電加工における電極の要件
鏡面放電加工(EDM)に一般的に使用される電極材料は銅とクロム銅であり、後者は電極の摩耗が少なくなります。銅材料を選択する際は、均一な組織と不純物の最小化が重要です。品質の悪い銅は、鏡面加工中に著しい電極の摩耗や表面のしわなどの異常現象を引き起こす可能性があります。銅合金電極は電極の摩耗を低減できるものの、満足のいく鏡面効果を得られません。
ミラーEDMの注意事項
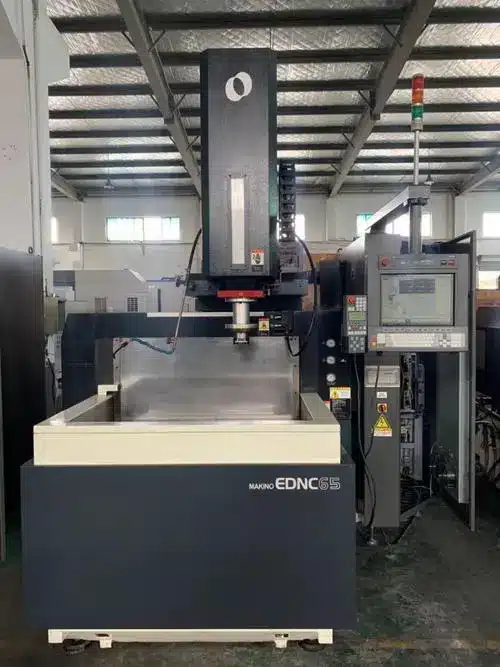
a. 鏡面EDMの加工余量を制御する
EDMプロセスは、粗加工から仕上げ加工までのプロセスです。まず、粗加工電極を使用して、一定の加工品質(寸法精度、形状精度、位置精度、表面粗さ)を確保しつつ、大量の金属を腐食させ、加工時間を短縮し、加工効率を向上させます。次に、仕上げ電極に交換し、より小さな放電エネルギーを使用して仕上げ加工を行います。粗加工であろうと仕上げ加工であろうと、複数の放電条件が使用され、電流も大きいものから小さいものへと変化し、深さ方向の送り加工で浅い部分を修復し、移動方向の修復で浅い側を修復します。
b. 鏡面加工における放電パラメータの適切な使用と加工制御
負極性処理を使用して処理では、いくつかの非主電気のパラメータの選択も非常に重要であり、従来の処理の選択は、いくつかの違いもあり、放電時間が長く設定するような、持ち上げツールの高さが短く、持ち上げツールの速度が速すぎることはできません、この設定の目的は、安定した小さなエネルギー電食プロセスを維持することである、ミラー処理では、それ自体が電食生成物の多くを生成しませんので、あまりにも多くの場合、ナイフリフティングアクションは、連続的かつ安定した放電を妨害する。
鏡面加工の電気腐食能力は非常に弱く、加工に時間がかかります。鏡面加工の寸法変化が非常に小さいため、実際には研磨の役割のみを果たしており、必要な表面粗さに達するまで加工を完了させれば十分です。したがって、CNC EDM工作機のタイミング加工機能を使用し、経験に基づいて加工時間を決定することができます。
c. 粉末混合技術を用いた広範囲加工により、鏡面加工効果を実現する。
混合粉末放電加工は、放電加工の面粗さを向上させる技術である。
いわゆる混合粉末EDMとは、加工液にシリコン粉末、アルミニウム粉末、クロム粉末などの微細粉末および関連する添加剤を添加し、加工表面に鏡面効果を得るための技術です。混合粉末加工技術を使用することで、同じ電気パラメーター条件下で、混合粉末加工技術を使用しない場合と比較して、より高速な加工速度(仕上げ時間を20~30%短縮)とより優れた表面粗さを得ることができます。EDMの大面積加工においては、顕著な改善効果が得られます。