アクリル射出成形製品は、その透明性と汎用性で人気がありますが、変形や気泡などの欠陥が発生しやすい場合があります。これらの問題にどのように対処するかを理解することは、製造工程で最適な結果を得るために非常に重要です。この記事では、このような欠陥を最小限に抑え、高品質の射出成形品を確実に製造するための実践的な解決策とベストプラクティスを探ります。
射出成形の過程で、製品に反りや変形が生じたとする。その場合、主に金型設計から解決すべきであり、成形条件の調整効果は少ない。
射出成形品の反りと変形の解決策
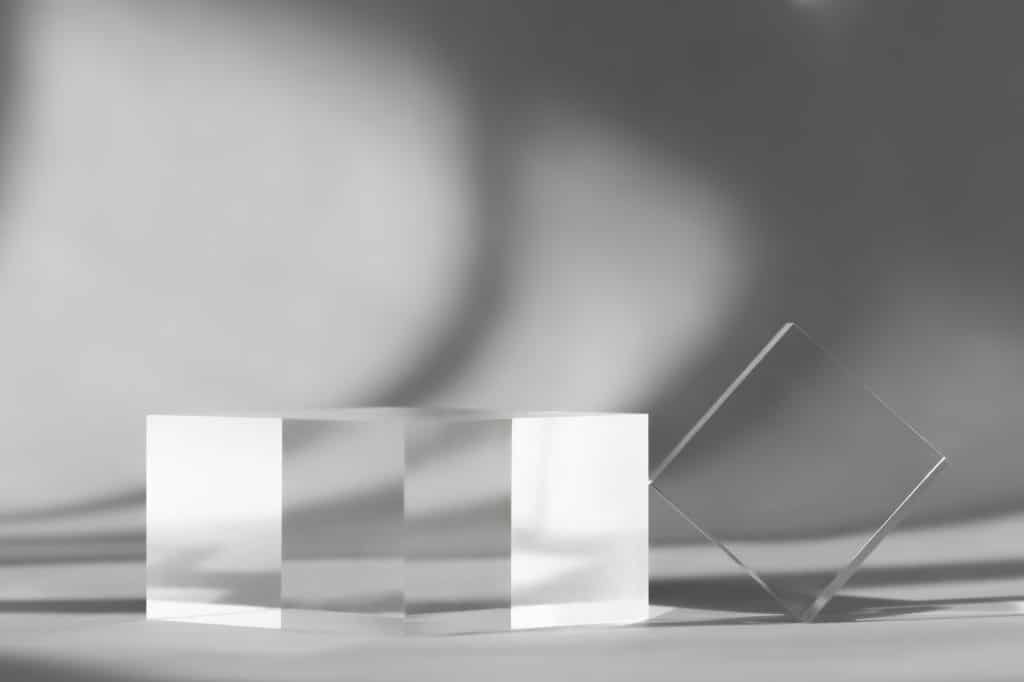
STEP1:成形条件による残留応力で変形する場合は、射出圧力を下げる、金型を高くして金型温度を均一にする、樹脂温度を上げる、アニールするなどの方法で応力を除去します。
STEP2:リリース不良による応力変形の場合は、プッシュロッドの本数や面積を増やし、リリース傾斜を設定することで解決できる。
STEP3:冷却方法が適切でなく、冷却時間が均一でない、または不十分な場合、冷却方法を調整し、冷却時間を延長することができます。例えば、冷却ループをできるだけ変形の近くに配置することもできる。
STEP4:成形収縮による変形に対しては、金型の設計を修正する必要がある。なかでも、製品の肉厚を一定にすることが重要である。やむを得ない場合は、製品の変形を測定し、逆方向にトリミングすることで金型を修正することもある。
収縮率の大きい樹脂、一般に結晶性樹脂(ASポリホルムアルデヒド、ナイロン、ポリプロピレン、ポリエチレン、PET樹脂など)は、非晶性樹脂(アクリル樹脂、ポリ塩化ビニル、ポリスチレン、ABS樹脂、AS樹脂など)に比べて変形が大きい。また、ガラス繊維強化樹脂は繊維配向があるため、変形も大きい。
泡の原因を解決する方法
製品の肉厚が厚くなると、中心部よりも外周部の冷却速度が速くなるため、冷却に伴って中心部の樹脂側が収縮して表面に膨らみ、中心部への充填が不十分となる。このような状況では真空気泡が発生しやすい。主な解決策としては
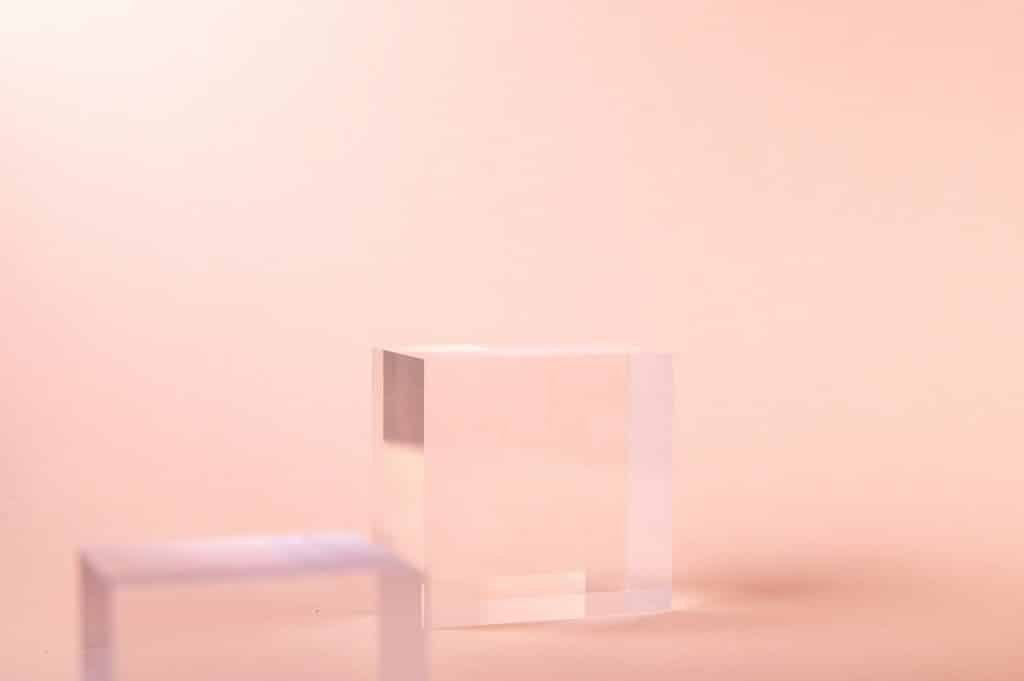
a) 肉厚に応じて、適切なゲートとランナーのサイズを決定する。一般的に、ゲートの高さは製品の肉厚の50~60%にする。
b) ゲートが密閉されるまで、一定量の補助注入材が残る。
c) 射出時間は、ゲートシール時間よりわずかに長くする。
d) 射出速度を下げ、射出圧力を上げる。
e) 溶融粘度の高いグレードの材料を使用する。
射出成形における揮発性ガスバブル問題への対応
a) 完全に予備乾燥する。
b) 分解ガスの発生を避けるため、樹脂温度を下げる。
c) 流動性不良による気泡は、樹脂と金型の温度を上げ、射出速度を上げることで解決できる。