製品の色差は射出成形でよくある不具合で、付属品の色が違うため、射出成形機が一括廃棄されることも珍しくない。色差に影響する要素はたくさんあり、材料の樹脂、カラーマスターバッチ、カラーマスターバッチと材料の混合、射出成形品、射出成形機、金型などに触れます。そのため、射出成形の中でも色差のコントロールスキルは難しいスキルの一つとして認識されています。ここで詳しくご紹介しましょう。
機械と金型部品の衝撃を軽減する
プラスチック金型加工の主力製品に適した能力の射出成形機を選ぶには、射出成形機に材料の死角などのタイトルがあることを想定し、設備を入れ替える。金型鋳造装置、排気タンクなどは、金型の該当部分の補修金型で色の違いに対応できる。まず射出成形機と金型のタイトルを処理し、タイトルの複雑さを減らすために生産を整理する必要があります。

射出成形
原料樹脂とカラーマスターコントロール原料の影響を排除することは、色の違いに対処する鍵である。そのため、特に淡色製品を生産する場合、材料樹脂の熱安定性の違いが製品の輝き揺れに与える影響は無視できない。ほとんどの射出成形メーカーはプラスチックやカラーマスターバッチを自分で生産していないので、注目の焦点は生産管理と原料検査に置くことができる。それは倉庫の原材料の検査を強化することである。可能な限り同じ製品の生産では、同じメーカー、同じ商標マスターバッチ、カラーマスターバッチの生産を選択します。
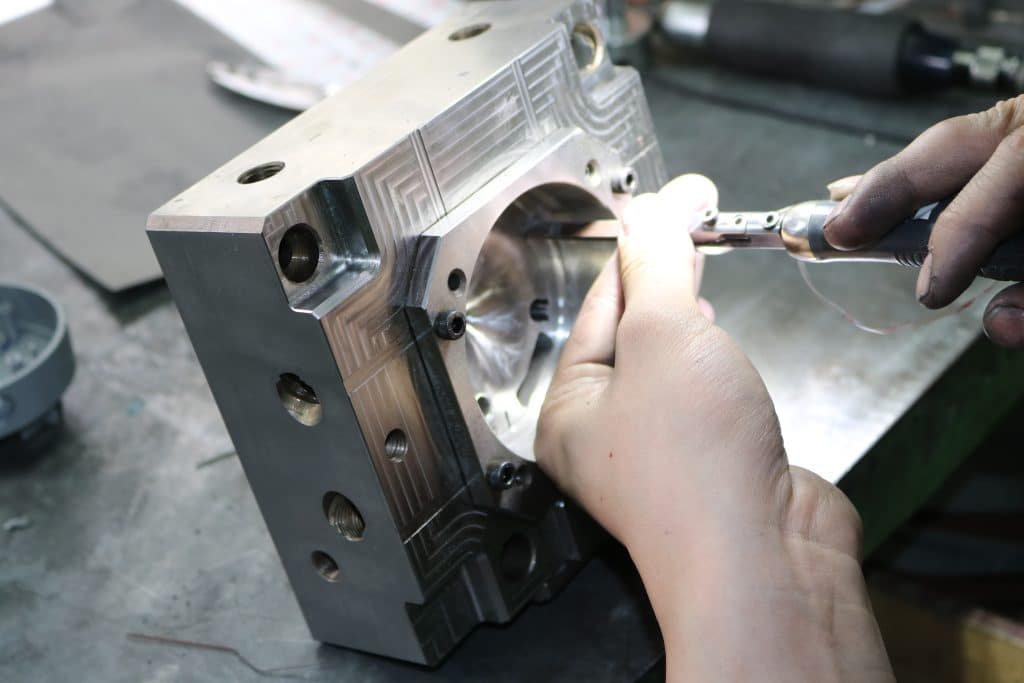
量産前のカラーテストの実施
この比較では、色差が大きくないことを前提に、バッチカラーマスターにわずかな色差がある場合、カラーマスターを最初から混合し、カラーマスター自体の混合ムラによって形成される色差を低減するために使用することができます。また、原料樹脂とカラーマスターバッチの熱安定性を確認する必要がある。熱安定性が確保できない場合は、メーカーに交換を勧める。
シリンダー温度がカラーバリエーションに与える影響を最小限に抑える

プラスチック金型加工工場の生産では、加熱リングが破損したり、加熱制御部が長時間制御不能になったりして、バレル温度が急激に変化し、色差が発生することがよくある。
このような理由による色差は判断しやすく、一般的な加熱リングの損傷や故障による色差は可塑化ムラを伴い、加熱制御部はガススポットやひどい変色、さらにはコーキングを伴うことが多い。従って、このような色差の発生確率を低くするためには、生産時に加熱部を頻繁にチェックし、損傷や制御不能の場合には適時に加熱部を交換することが必要である。