今日の超競争的な製造環境において、競争優位を求める企業にとって、プロセスの改善は極めて重要である。特にコンシューマー・エレクトロニクスのような業界では、イノベーションとコスト効率は成功の要です。
スピーカーのプラスチック金型製造におけるコスト削減は、オーディオ業界において競争力を維持するために不可欠です。戦略的なアプローチを実施することで、メーカーは品質を損なうことなく効率を高め、費用を最小限に抑えることができます。このガイドでは、材料の選択から設計の改善まで、スピーカーのプラスチック金型の生産工程を最適化するためのさまざまなテクニックとベストプラクティスを紹介します。市場の要求を満たす高品質のスピーカー部品を提供しながら、業務を合理化し、無駄を省き、大幅なコスト削減を実現する方法をご覧ください。
今回は、スピーカー用プラスチック金型の製造コスト削減と作業効率向上のアイデアについて紹介する。

プラスチック金型は、最終製品の品質、耐久性、総合的な性能によって、スピーカーの製造に不可欠なものです。しかし、従来の金型製造方法では、一般的に多くのコストと時間を投資する必要があります。革新的なアプローチを導入し、技術開発を適用することで、メーカーは品質を損なうことなく、作業を簡素化し、コストを削減することができます。
スピーカー プラスチック金型設計
コスト削減への道のりは、詳細設計の最適化から始まります。最先端のCAD(コンピューター支援設計)ソフトウェアとシミュレーション・ツールを使用することで、メーカーはハードウェア金型を改良し、材料の塗布を防止して構造の完全性を確保することができます。これは材料の消費を抑えるだけでなく、金型の効率と寿命を向上させます。
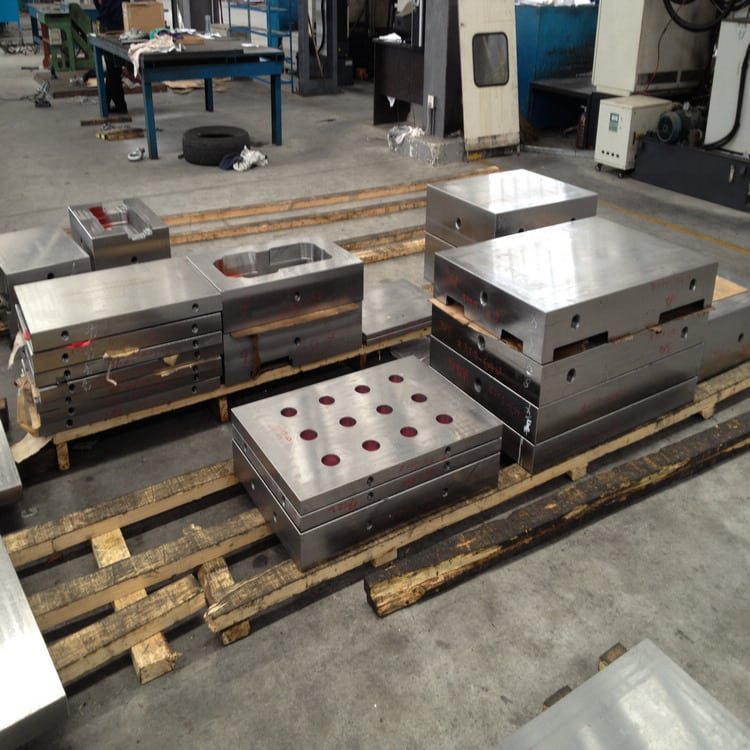
スピーカーのプラスチック金型の材質
適切な材料を選ぶことは、コスト効率と性能にとって特に重要である。代替材料や複合材料を検討することで、メーカーは品質をあきらめることなくコストを削減することができる。さらに、リサイクル可能な素材や環境に優しい素材を使用することは、持続可能な開発目標に沿ったものであり、長期的には材料費を削減することができる。
スピーカー プラスチック金型製造技術

3DプリンティングやCNCマシニングのようなトップレベルの生産工程を選択することは、コスト管理と生産効率の面で明らかな利点があります。これらの技術は、効率的なプロトタイピング、カスタマイズ、複雑なディテールを可能にし、リードタイムと商品コストを最小限に抑えます。
- 業界レポートによると、プラスチック射出成形の世界市場は2027年までに3900億ドルに達すると予測されており、生産工程の最適化の重要性が浮き彫りになっている。
- 研究によると、3Dプリンティングのような高度な製造技術を採用することで、市場投入までの時間を短縮しながら、製造コストを最大50%削減できる。
オートメーションと自動制御
オートメーションは、加工の簡素化と人件費の削減に主導的な役割を果たしている。ロボットシステムをマテリアル・ソリューション、射出成形工程、品質管理に組み込むことで、効率が向上するだけでなく、一貫した品質基準を確保することができます。さらに、自動化は人的ミスのリスクを減らし、オフィスのセキュリティを向上させます。
戦略的パートナー
金型の専門メーカーやサプライヤーと協力することで、社内では得がたい専門知識やリソースを利用することができます。外部の戦略的パートナーシップを利用することで、メーカーはサプライチェーンを最適化し、有利な価格交渉を行い、最先端の技術を入手し、最終的にコストを削減することができます。
文化の漸進的向上
継続的な改善の文化を創造することは、コスト管理と長期的な効率改善に不可欠である。従業員の参加意欲を高め、フィードバックや提案を求め、定期的な業績評価を実施する。問題に積極的に取り組むことで、製造業者はプロセスを反復的に改善し、常に時代の先端を行くことができる。
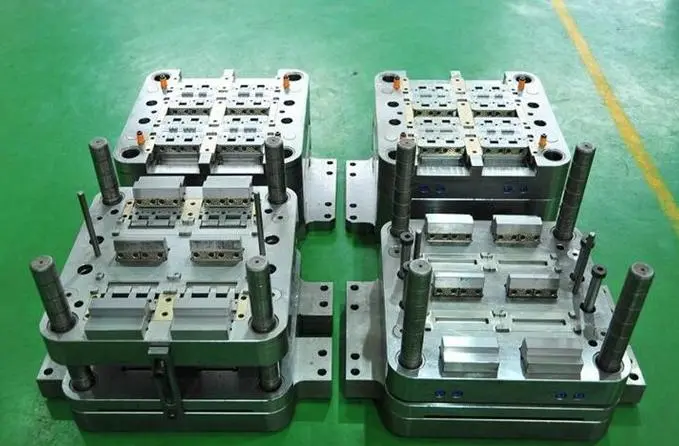
スピーカー プラスチック金型製造
ジャスト・イン・タイムの在庫管理、価値の流れの予測、改善手法などのリーン生産方式を導入することで、大幅なコスト削減と効率向上を実現することができる。無駄を省き、ワークフローを最適化し、資源を最大限に活用することで、製造業者はより細かく、より柔軟なプロセスを実現することができる。
結論
スピーカー用プラスチック金型の生産コストを削減するには、技術革新、戦略的パートナーシップ、継続的改善への取り組みを組み合わせる必要があります。設計の最適化、材料の革新、最先端の生産技術、自動化をベースに、メーカーは作業効率を高めながらコストを大幅に削減し、ダイナミックな売買が行われる電子市場の競争優位性を維持することができます。
キーワード:プラスチック金型製造、スピーカー製造、コスト削減、生産効率、設計最適化、材料選択、高度製造、自動化、共同パートナーシップ、継続的改善。