In today’s hyper-competitive manufacturing environment, improving processes is critical for companies seeking a competitive advantage. Especially in industries such as consumer electronics, innovation and cost efficiency are cornerstone drivers of success. In this article, we discuss the idea of reducing the production cost of plastic molds for speakers and improving work efficiency.

Plastic molds are essential in the manufacture of loudspeakers, depending on the final product’s quality, durability, and overall performance. However, traditional mold manufacturing methods generally require a lot of cost and time investment. By implementing innovative approaches and applying technological developments, manufacturers can simplify operations and reduce costs without compromising quality.
Optimal design
The journey to cost reduction begins with detailed design optimization. With cutting-edge CAD (computer-aided design) software and simulation tools, manufacturers can improve hardware molds to prevent the application of materials to ensure the integrity of construction. This not only reduces the consumption of materials but also improves the efficiency and life of the mold.
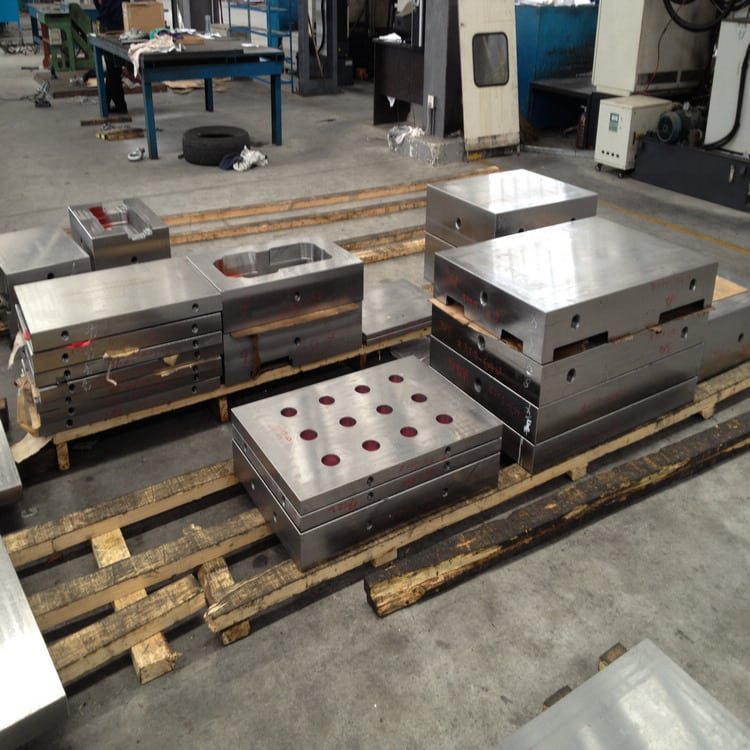
Material type
Choosing the right material is particularly important for cost efficiency and performance. By exploring alternative materials and composite mixtures, manufacturers can reduce costs without giving up quality. In addition, the use of recyclable or environmentally friendly materials is in line with the Sustainable Development Goals and can reduce material costs in the long run.
Advanced manufacturing technology

Choosing top production processes such as 3D printing or CNC machining has obvious advantages in terms of cost control and production efficiency. These technologies enable efficient prototyping, customization, and complex detailing to minimize lead times and commodity costs.
- According to industry reports, the global market for plastic injection molding is projected to reach $390 billion by 2027, highlighting the significance of optimizing production processes.
- Studies show that adopting advanced manufacturing techniques such as 3D printing can reduce production costs by up to 50% while accelerating time-to-market.
Automation and automated control
Automation is playing a leading role in simplifying processing and reducing labor costs. Integrating robotic systems into material solutions, injection molding processes, and quality control not only increases efficiency but also ensures consistent quality standards. In addition, automation reduces the risk of human error and improves office security.
Strategic partner
Working with a specialist mold manufacturer or supplier gives you access to expertise and resources that are hard to come by in-house. Through the use of external strategic partnerships, manufacturers can optimize the supply chain, negotiate favorable prices, obtain the most advanced technology, and ultimately reduce costs.
Gradual improvement of culture
Creating a culture of continuous improvement is critical to managing costs and improving efficiency over the long term. Motivate employees to participate, ask for feedback and suggestions, and carry out regular performance appraisals, which are conducive to identifying shortcomings and improving areas. By proactively addressing problems, manufacturers can iteratively improve processes and stay ahead of the curve.
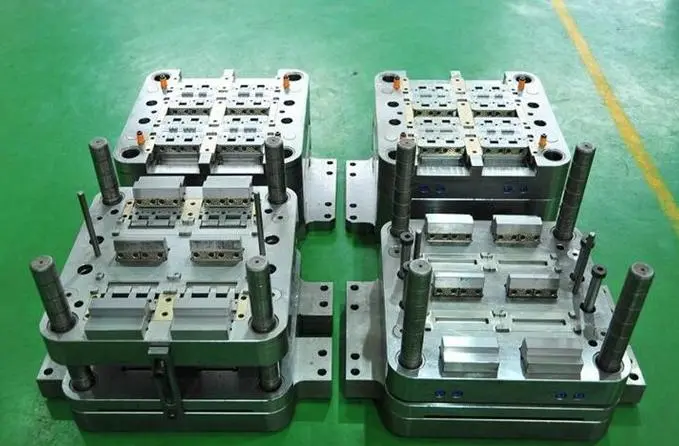
Lean production
Implementing lean manufacturing practices such as just-in-time inventory management, value stream projection, and improvement methods can yield significant cost savings and efficiency gains. By eliminating waste, optimizing workflows, and maximizing the use of resources, manufacturers can achieve finer, more flexible processes.
Conclusion
To reduce the production cost of plastic molds for speakers, it is necessary to combine technological innovation, strategic partnerships, and a commitment to continuous improvement. Based on design optimization, material innovation, cutting-edge production technologies, and automation, manufacturers can significantly reduce costs while increasing work efficiency and maintaining the competitive advantages of dynamic buying and selling electronic markets.
Keywords: plastic mold production, speaker manufacturing, cost reduction, production efficiency, design optimization, material selection, advanced manufacturing, automation, collaborative partnerships, continuous improvement.