プラスチック製造の世界では、射出成形とブロー成形は、数多くのプラスチック製品の製造を一変させた不可欠な技術である。
これらの方法は、電子機器の複雑な部品から一般的な家庭用容器に至るまで、日用品を形作る上で極めて重要な役割を果たしている。それぞれの技術は独自の利点を誇り、多様な産業ニーズや製品仕様に対応している。
射出成形:複雑さの中の精密さ
射出成形は、プラスチック製造の雄であり、その精度と多様性で有名である。溶融プラスチックを金型に注入し、冷却固化させて成形する。射出成形は、複雑な部品を作る際の精度の高さで珍重されており、複雑な設計や厳しい公差を必要とする業界では極めて重要な工程となっている。
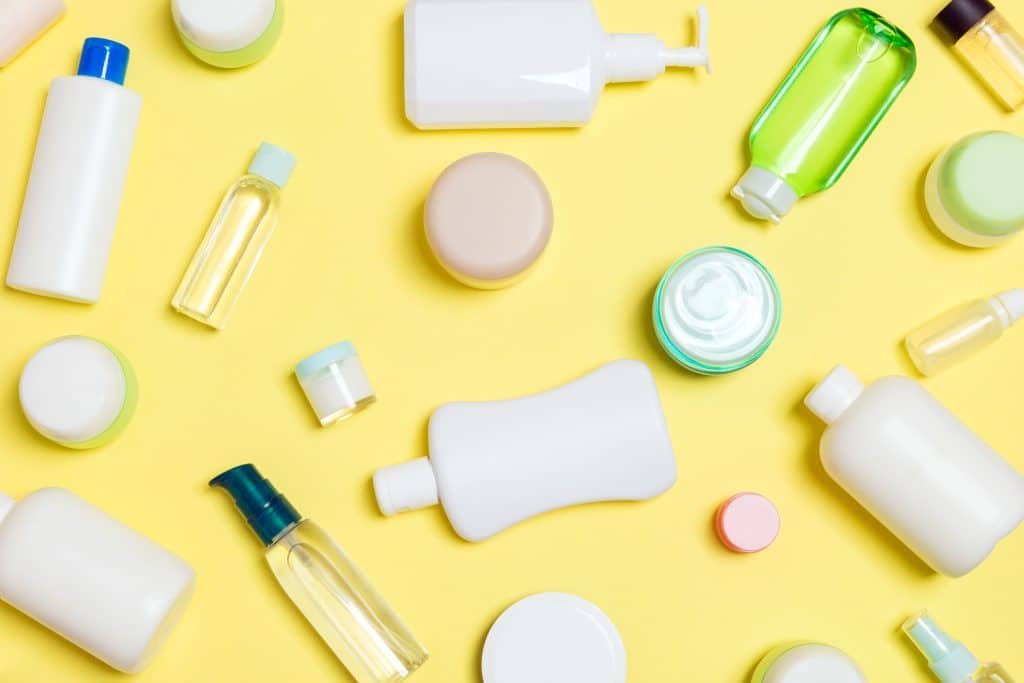
射出成形の際立った利点のひとつは、多様な素材に対応できる点にあります。この方法は、熱可塑性プラスチック、熱硬化性ポリマー、エラストマーに対応し、メーカーが製品固有の特性に合わせた材料を柔軟に選択できる。また、この製法は添加剤や補強材の組み込みを容易にし、最終製品の構造的・機能的特性を向上させる。
さらに、射出成形は拡張性に優れ、安定した品質の大量生産を可能にします。このプロセスの効率性とスピードは、大量生産に最適で、生産コストを削減し、大量ロットの一貫性を確保します。自動車、医療、消費財などの業界では、精密な仕様の複雑な部品や製品を生産するために射出成形が定期的に使用されています。
ブロー成形:中空容器を効率的に成形
ブロー成形は、容器やボトルのような中空のものを作るときに輝く。ここでは、加熱されたプラスチックチューブが金型内で膨らまされ、冷えるにつれて形を成していく。ブロー成形の特長は、軽量で耐久性があり、費用対効果の高い中空製品を効率よく製造できる点にある。
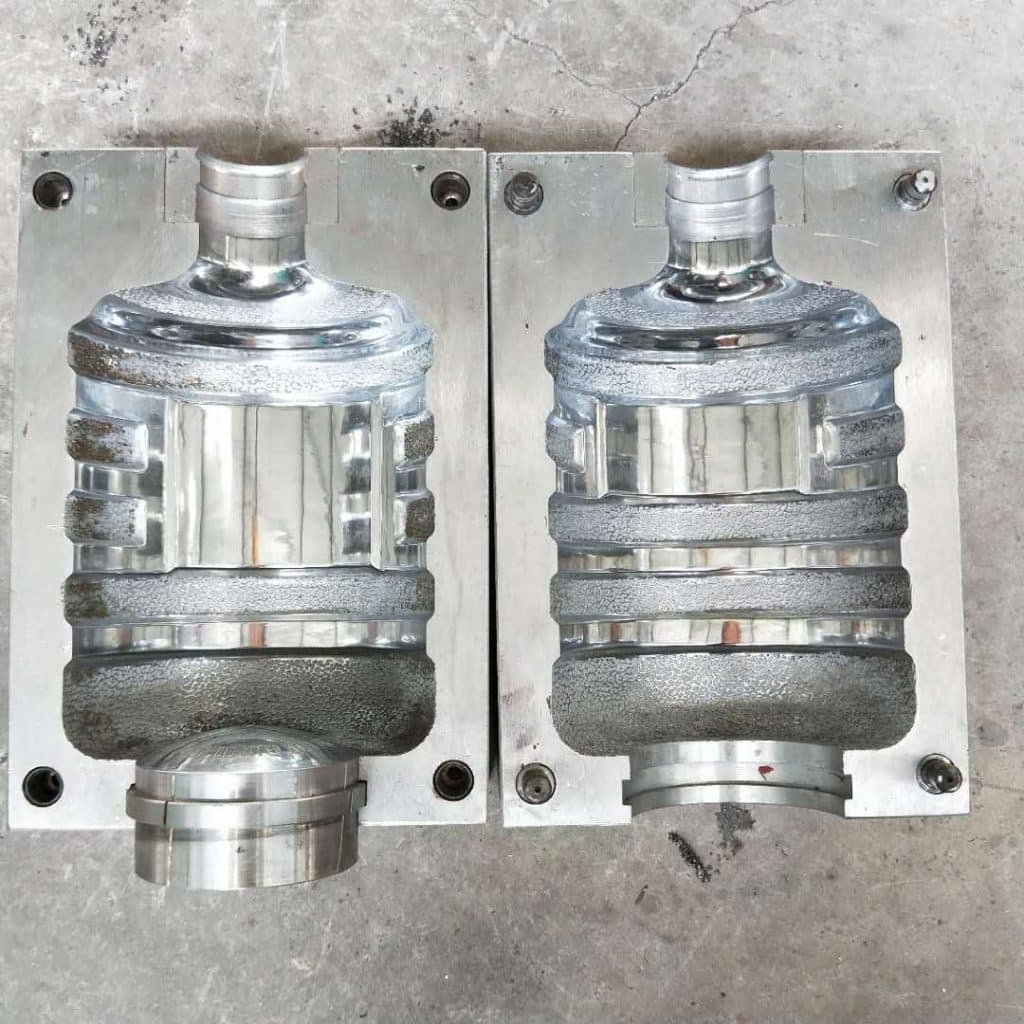
ブロー成形の明確な利点は、滑らかで中空の継ぎ目のない製品に見られる。ブロー成形は、製品の大半が容器、ボトル、包装である産業で好まれる方法です。このプロセスは、均一な肉厚と、包装業界のさまざまなニーズに適したさまざまな形状やサイズの容器を製造する柔軟性で際立っています。
ブロー成形は、資源効率でも高い評価を得ている。この技術では、中空構造を作ることに重点を置くことで材料の使用量を最適化し、強度を損なうことなく製品全体の重量を減らすことができる。この軽量化の特性はコスト削減に貢献し、現代の製造業における持続可能性と環境に優しい慣行の重視に合致している。
対照的な強み:最適なものを見つける
射出成形とブロー成形にはそれぞれ長所と短所がありますが、求められる最終製品に大きく左右されます。射出成形は、例えばエレクトロニクス、自動車、医療機器産業など、細部まで精度の高い小さな部品が必要な場合に最適です。材料の多様性と大量生産が可能であることが、これらの分野での優位性を確固たるものにしている。
一方、ブロー成形は中空構造物に関しては特に優れています(実際、ブロー成形なくして包装産業は成り立ちません)。ブロー成形は、飲料、化粧品、医薬品など様々な業界の需要に対応し、一定の肉厚を持つ軽量容器を作るための非常に効率的な方法です。その資源効率の高い方法論は、現代的な製造慣行の持続可能な目標を推進しながら、材料消費を削減します。
プラスチック製造におけるバランスの実現
射出成形とブロー成形は、どちらも進化し続けるプラスチック製造の世界に欠かせないものです。射出成形とブロー成形は、どちらもプラスチック製造のリーダー的存在であり、それぞれが特定の目的に対応し、特定のニーズを満たし、より高い収益性と信頼性を引き出すために作られています。
自動車産業から医療機器に至るまで、射出成形とブロー成形が調和して様々な産業の進化するニーズに応えることで、明日のプラスチック製品はこれらのプロセスのユニークな利点に依存している。