In the world of plastic manufacturing, Injection Molding and Blow Molding are essential techniques that have transformed the production of numerous plastic products.
These methods play pivotal roles in shaping everyday items, from intricate components in electronics to common household containers. Each technique boasts its own unique set of advantages, catering to diverse industrial needs and product specifications.
I. Injection Molding: Precision in Complexity
Injection Molding, a stalwart in the realm of plastic manufacturing, is renowned for its precision and versatility. The process injects molten plastic into a mold, where it cools and solidifies to shape. It’s prized for precision in making intricate parts, crucial in industries needing complex designs and tight tolerances.
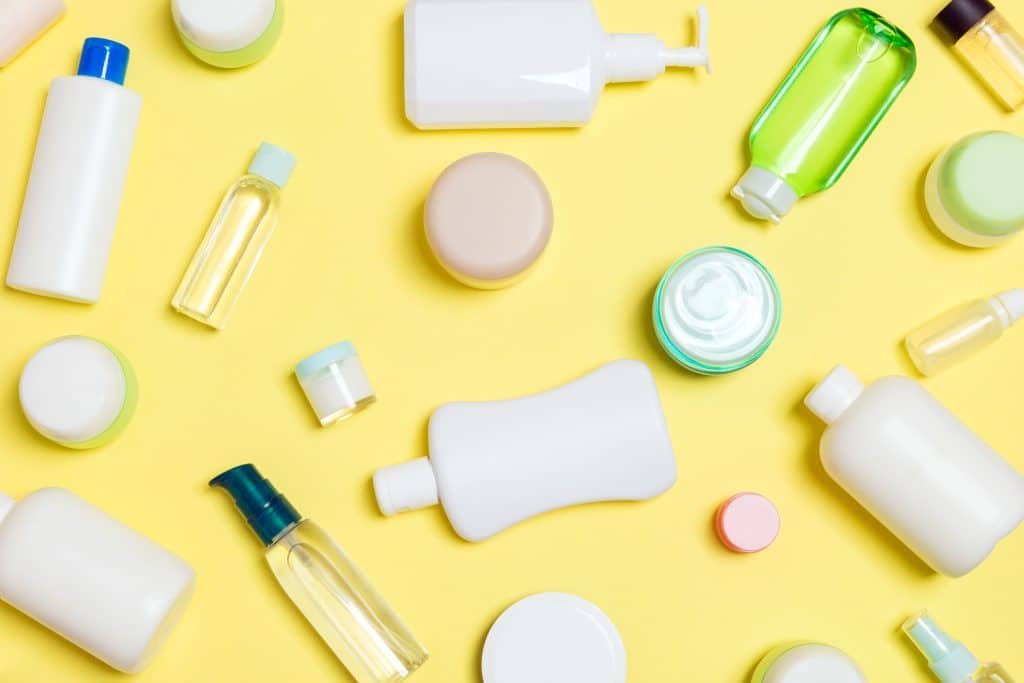
One of the standout advantages of Injection Molding lies in its ability to accommodate a diverse range of materials. This method accommodates thermoplastics, thermosetting polymers, and elastomers, offering manufacturers flexibility to select materials tailored to their product’s specific properties. The process also facilitates the incorporation of additives and reinforcements, enhancing the structural and functional attributes of the final product.
Additionally, Injection Molding excels in scalability, enabling mass production with consistent quality. The process’s efficiency and speed make it perfect for high-volume manufacturing, cutting production costs and ensuring consistency across large batches. Industries like automotive, medical, and consumer goods regularly use Injection Molding to produce intricate components and products with precise specifications.
II. Blow Molding: Forming Hollow Vessels with Efficiency
Blow Molding shines in making hollow items like containers and bottles. Here, a heated plastic tube is inflated within a mold, taking its shape as it cools. Blow Molding’s hallmark advantage lies in its efficiency in producing lightweight, durable, and cost-effective hollow products.
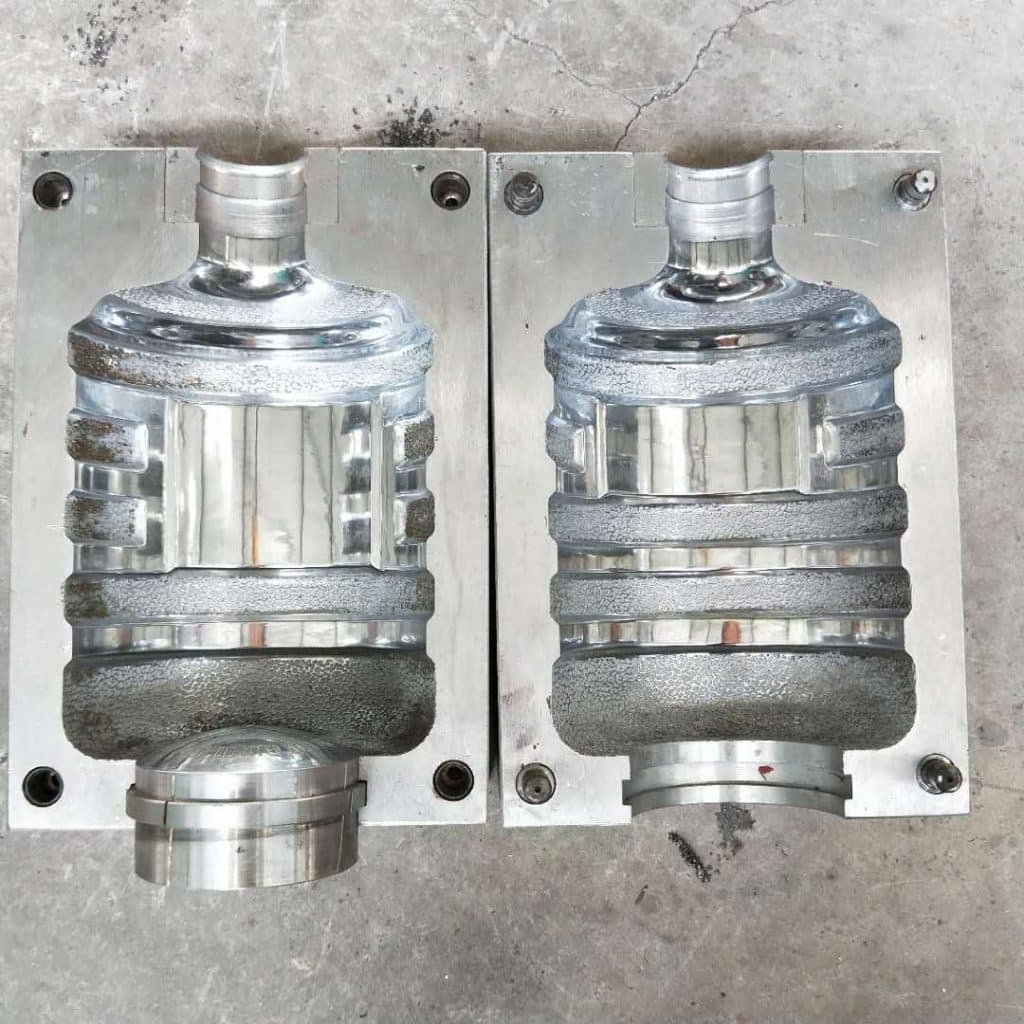
The primary advantage of Blow Molding is evident in its suitability for creating seamless, hollow structures. This makes it the method of choice for industries where containers, bottles, and packaging dominate the product landscape. The process excels in uniform wall thickness and offers the versatility to produce containers of various shapes and sizes, meeting the diverse demands of the packaging industry.
Blow Molding also scores high on resource efficiency. The technique optimizes material usage by focusing on the creation of hollow structures, reducing the overall weight of the product without compromising strength. This lightweight characteristic not only contributes to cost savings but also aligns with the growing emphasis on sustainability and eco-friendly practices in modern manufacturing.
III. Contrasting Strengths: Finding the Right Fit
While both Injection Molding and Blow Molding offer distinct advantages, the decision between them depends on the specific needs of the end product. Injection Molding excels at creating intricate, detailed, and highly precise components, making it ideal for industries where complexity is crucial, like electronics, automotive, and medical devices. Its ability to work with a variety of materials and handle large-scale production further cements its position in these sectors.
Conversely, Blow Molding excels in the production of hollow structures, making it indispensable for the packaging industry. Blow Molding’s efficiency in producing lightweight containers with consistent wall thickness meets the needs of the beverage, cosmetics, and pharmaceutical industries. Its resource-efficient approach not only cuts material usage but also supports the sustainability goals of modern manufacturing practices.
Conclusion: Striking a Balance in Plastic Manufacturing
In the ever-changing landscape of plastic manufacturing, Injection Molding and Blow Molding form a symbiotic relationship vital for meeting diverse industrial needs. Injection Molding’s precision and versatility cater to intricate designs and complex components, while Blow Molding’s efficiency and resource optimization make it the method of choice for hollow structures.
As industries continue to innovate and demand more from plastic manufacturing processes, the coexistence and complementary strengths of Injection Molding and Blow Molding ensure that the plastic products of tomorrow are not only functional and durable but also produced with unparalleled efficiency and precision.