Introduction
Steel is a critical material in mold making, offering a variety of types each with distinct properties suited for different applications. The selection of the right steel is vital to ensure the mold’s durability, performance, and efficiency, directly impacting the quality and yield of the final product. Sure, let’s delve into the steels used in mold making, their properties, and how to choose the appropriate steel based on the material and yield of the product.
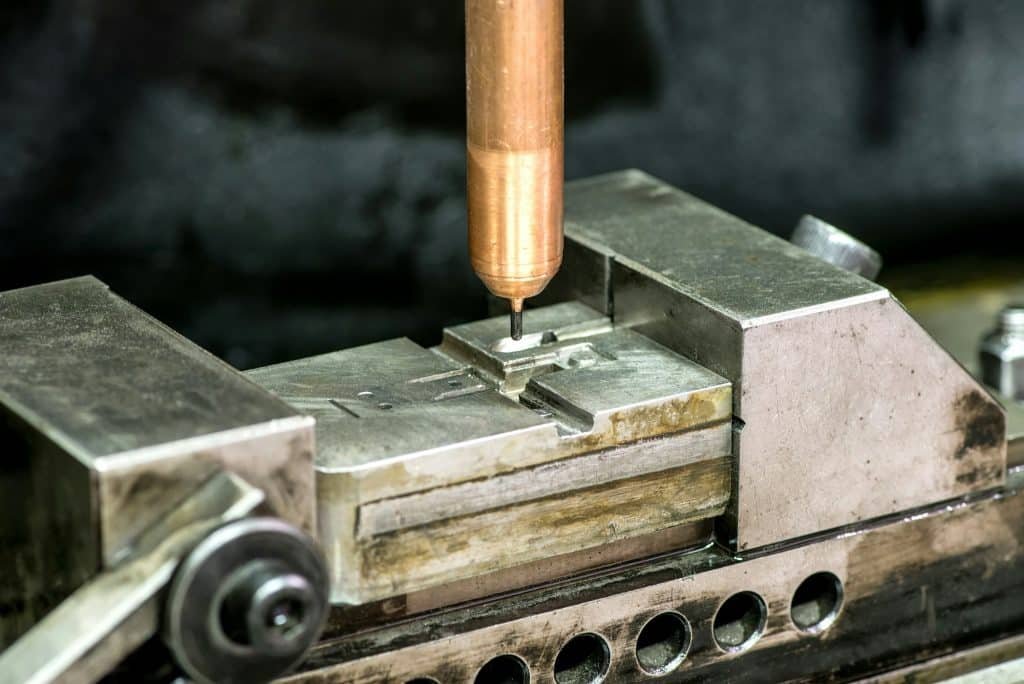
Types of Steel Used in Mold Making
- Carbon Steel
- Alloy Steel
- Tool Steel
- Stainless Steel
Each type of steel is chosen based on its unique properties, which include hardness, toughness, wear resistance, and machinability.
Carbon Steel
Carbon steels are widely used due to their affordability and availability. They contain varying amounts of carbon and can be divided into low, medium, and high-carbon steels.
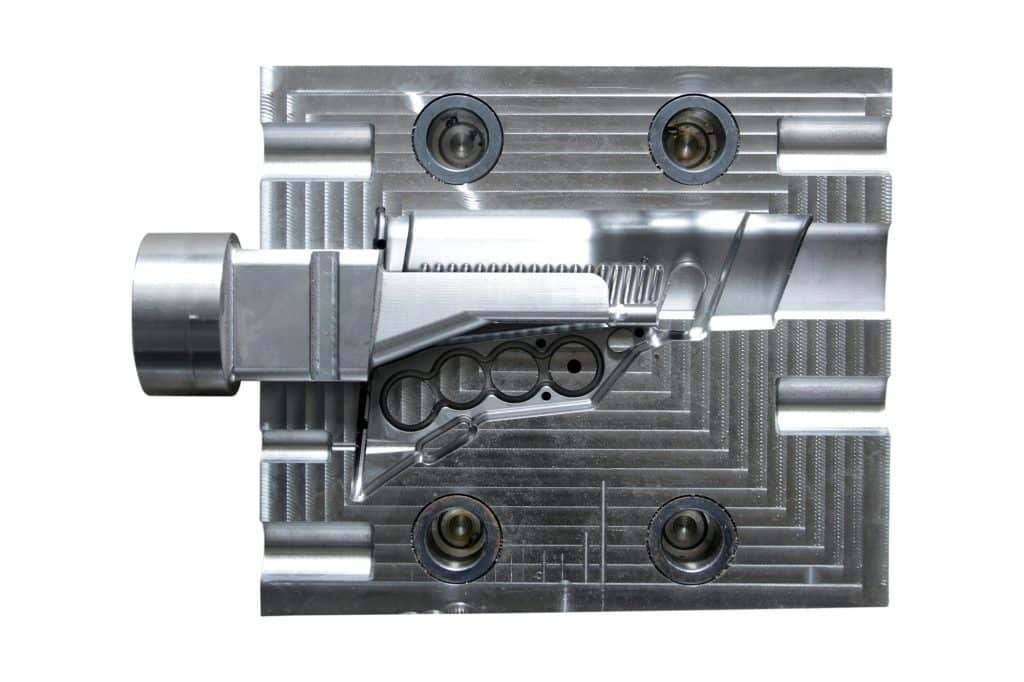
- Low Carbon Steel: Contains up to 0.3% carbon. It is relatively soft and easy to machine but lacks hardness and wear resistance.
- Medium Carbon Steel: Contains 0.3% to 0.6% carbon. It strikes a balance between hardness and ductility, making it suitable for molds requiring moderate strength and wear resistance.
- High Carbon Steel: Contains 0.6% to 1.4% carbon. It is very hard and wear-resistant but can be brittle. It’s used for molds that need high strength and wear resistance but are subjected to less impact.
Alloy Steel
Alloy steels are mixed with various elements such as chromium, nickel, and molybdenum to enhance their properties.
- Chromium-Molybdenum Steel: Known for its toughness and wear resistance. Commonly used in molds for plastic injection and die casting.
- Nickel-Chromium Steel: Offers excellent toughness, hardness, and resistance to heat and corrosion. Suitable for molds used in high-stress applications.
Tool Steel
Tool steels are specifically designed for use in the manufacturing of tools and dies. They are categorized based on their ability to retain a cutting edge, resistance to deformation, and longevity under high-stress conditions.
- A-Series (Air-Hardening): High chromium content provides excellent wear resistance and hardness.
- D-Series (High Carbon, High Chromium): Offers superior wear resistance and can be used in cold work applications.
- H-Series (Hot Work): Designed for high-temperature applications, maintaining hardness and strength at elevated temperatures.
Stainless Steel
Stainless steels contain at least 10.5% chromium, which provides excellent corrosion resistance. They are used in molds where corrosion resistance is a critical factor.
- Martensitic Stainless Steel: This can be hardened by heat treatment, providing good wear resistance and moderate corrosion resistance.
- Austenitic Stainless Steel: Known for its excellent corrosion resistance but lower hardness compared to martensitic types.
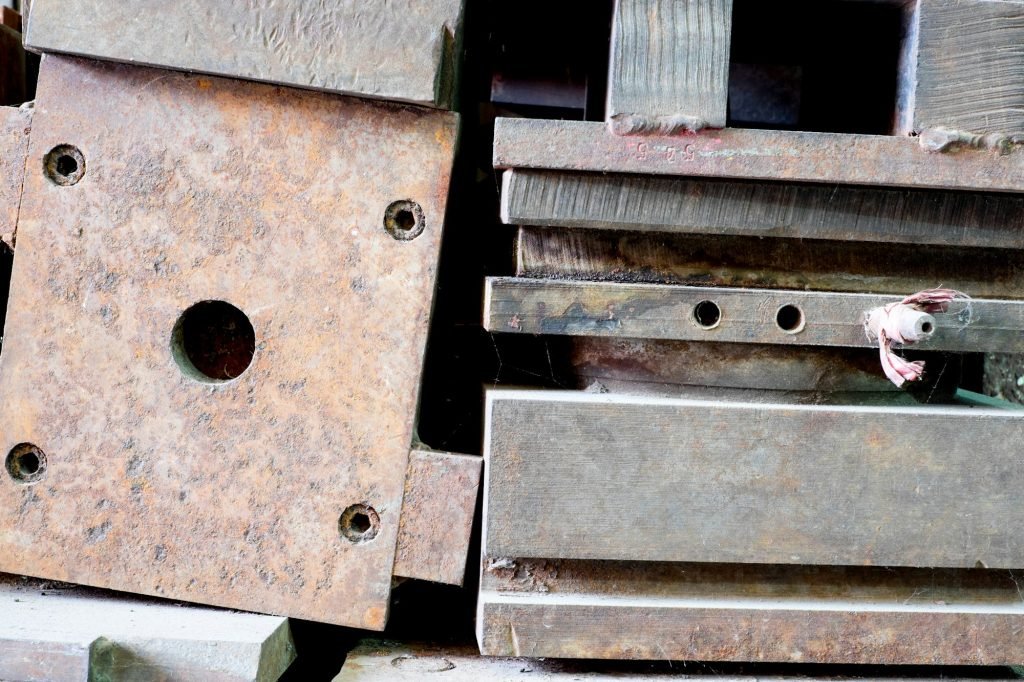
Hardness of Mold Steels
Hardness is a key factor in the performance of mold steels. It is measured using the Rockwell Hardness Scale (HRC) or Brinell Hardness Number (BHN). Here are typical hardness values for different mold steels:
- Low Carbon Steel: 70-80 BHN
- Medium Carbon Steel: 120-180 BHN
- High Carbon Steel: 200-300 BHN
- Chromium-Molybdenum Steel: 180-230 HRC
- Nickel-Chromium Steel: 250-350 HRC
- A-Series Tool Steel: 50-65 HRC
- D-Series Tool Steel: 55-62 HRC
- H-Series Tool Steel: 40-55 HRC
- Martensitic Stainless Steel: 40-50 HRC
- Austenitic Stainless Steel: 150-200 BHN
Choosing Steel According to Material and Yield
The selection of mold steel is influenced by the type of material being molded and the desired yield of the product. Here are some guidelines:
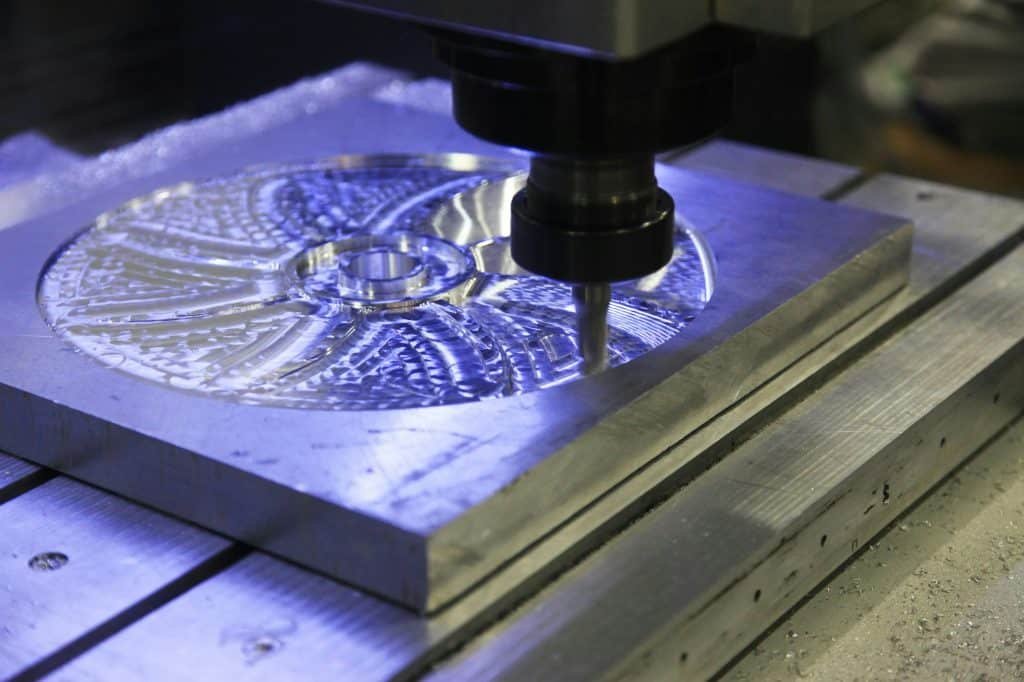
Material Being Molded
- For general-purpose plastics (e.g., polypropylene, polyethylene), medium carbon steel or A-series tool steel can be used due to their moderate hardness and wear resistance.
- For abrasive plastics (e.g., filled polymers), high carbon steel or D-series tool steel is preferred for their superior wear resistance.
- Metal Materials:
- For die-casting non-ferrous metals (e.g., aluminum, zinc), H-series tool steel is ideal as it maintains hardness at high temperatures.
- For harder metals (e.g., steel alloys), high carbon or alloy steels like chromium-molybdenum steel provide the necessary strength and wear resistance.
Desired Yield and Mold Longevity
- High-Volume Production:
- For molds expected to produce a high number of parts, tool steels with high wear resistance (e.g., D-series) are essential to maintain mold integrity over time.
- Chromium-molybdenum steel is also a good choice for its toughness and ability to withstand repeated use.
- Low-Volume Production:
- For lower production volumes, the cost-effectiveness of medium-carbon steels or low-carbon steels can be advantageous. They provide sufficient durability without the higher cost of more specialized steels.
- Precision and Surface Finish:
- When precision and high surface finish are required, such as in optical components or medical devices, stainless steels like martensitic stainless steel are suitable due to their corrosion resistance and ability to achieve a fine finish.
- For complex mold geometries requiring intricate details, A-series tool steels are preferred for their machinability and stability during heat treatment.
Conclusion
Choosing the right steel for mold making is a critical decision that affects the performance, durability, and cost-effectiveness of the mold. Understanding the types of steels available, their properties, and their hardness helps in making an informed decision. Factors such as the material being molded, production volume, and desired yield play crucial roles in this selection process.
By carefully evaluating these aspects, manufacturers can ensure that the chosen mold steel will meet the specific requirements of their application, leading to high-quality products and efficient production processes. Whether it’s for plastic injection molding, die casting or high-precision applications, the right steel ensures that the mold performs optimally, providing long-term reliability and value.