1, PC/ABS injection mold process conditions:
It must be dried before processing. The humidity should be less than 0.04%, and the recommended drying condition is 90~110℃ for 2~4 hours.
The melting temperature is 230~300℃;
Mold temperature: 50~100℃.
Injection pressure depends on the plastic parts.
The injection speed needs to be as high as possible.
Chemical and physical properties: PC/ABS has the combined characteristics of both PC and ABS. For example, the easy processing characteristics of ABS and the excellent mechanical properties and thermal stability of PC. The ratio of the two will affect the thermal stability of the PC/ABS material. The PC/ABS blend also shows excellent fluidity. The shrinkage rate is about 0.5%.
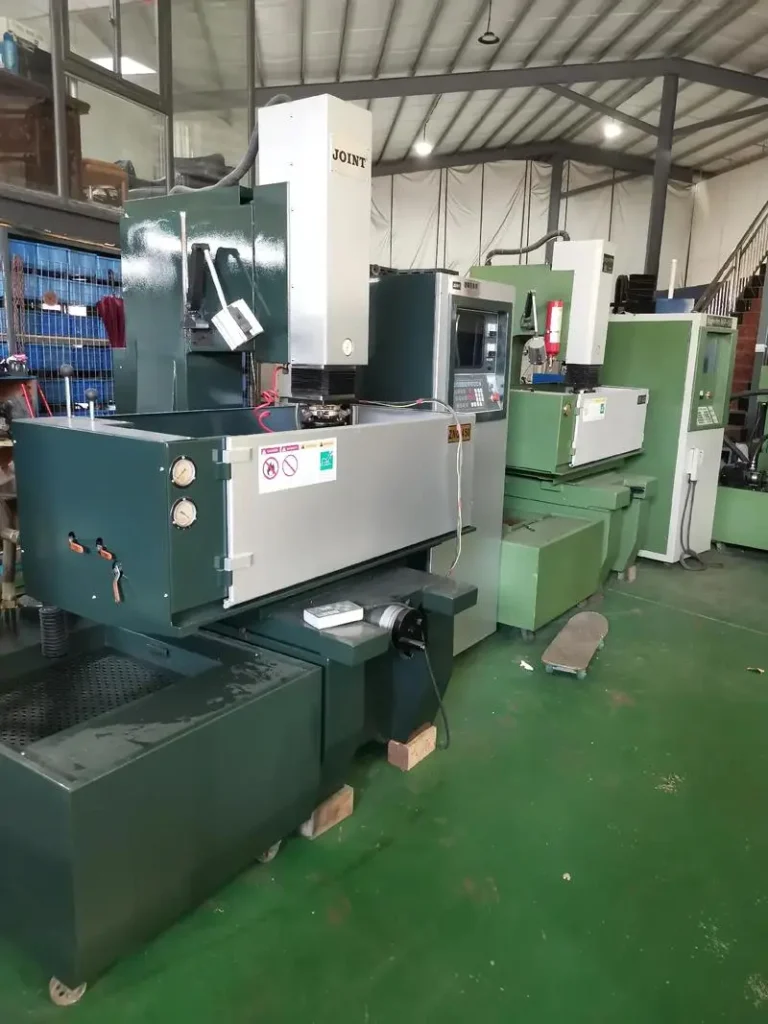
2, injection PC/ABS products common problems and solutions
a: The silver problem
Silver wire is the most common problem of PC/ABS materials, silver wire also known as silver grain, splash, material flower, etc., is the phenomenon of silvery white silk stripes along the flow direction on the surface of the product.
The main reason is the interference of the gas, which is mainly divided into three components: air: the air involved in the glue and injection stage; Moisture: moisture contained in the material itself; Pyrolysis gas: Gas produced by high-temperature hydrolysis/thermal decomposition.
How to solve:
First check whether the material is dry enough, after confirming that the material is dry enough, and then adjust the injection molding process to improve the silver wire defect. At the same time, poor injection of silver wire is also related to mold exhaust.
b: Flow mark problem
Flow marks are generated when the material is injected, the reason is that the material has poor fluidity, the flow marks are different from the silver stripes, and the appearance is not the same.
How to solve:
It can be avoided by increasing the temperature of the material to improve the flow, appropriately increasing the flow of the material in the mold, and reducing the injection speed.
c: Shrinkage hole and dent problem
A shrinkage hole is caused by insufficient material filling in the mold cavity.
Solution: Appropriately increase the mold temperature and material temperature to improve the flow of materials, extend the injection pressure holding time, increase the injection pressure, and increase the injection speed to improve the mold filling, you can also increase the size of the gate, heating the gate runner to reduce and eliminate the shrinkage of products;
Dents are caused by improper material temperature and improper product design, when the material temperature is too low, not only shrinkage holes occur, but also dents will occur, the material temperature is too high, the mold temperature is too high, which will make the molten material shrink too much when cooling, resulting in dents.
Solution: Increase the injection speed.
d: Warping deformation problem
The warping deformation of injection parts is due to the unreasonable design of parts, improper gate location, and unreasonable injection molding processing conditions, resulting in internal stress, uneven shrinkage or excessive, mold temperature is too high or mold temperature not uniform, resulting in mold mucous membrane release difficulties, or uneven cooling, the same will produce warping deformation;
How to solve:
Processing technology: lengthen the injection molding cycle, reduce the injection temperature, adjust the injection pressure and injection speed, reduce the ejection speed, increase the ejection area, and maintain the balance of the ejection force;
Product design: increase the wall thickness, add reinforcement reinforcement and rounded corners;
e: Markings
It is usually caused by the “melt rupture” caused by the expansion of molten material into the mold cavity during high-speed injection.
How to solve:
Molding process: to increase the material temperature, and nozzle temperature, slow down the injection speed to reduce the appearance of markings;
Mold: increase mold temperature, add overflow groove, increase gate size, and modify gate shape.
f: Pitting problem
How to solve:
1. Poor dispersion, add dispersant or oil, increase temperature, and add back pressure. Also, see if it is a mold problem. Use other materials.
2. Whether the baking material temperature time is sufficient. Adjust mold temperature properly.
g: Product “peeling” problem
The peeling problem of plastic products has a great relationship with the fracture of fluid caused by high shear force. At low shear stress or rate, the small disturbance caused by various factors is inhibited by the melt. However, under high shear stress or velocity, the disturbance in the fluid is difficult to restrain and develops into unstable flow. When a critical shear force is reached, the rupture of the fluid will be caused.

How to solve:
In terms of materials: because the poor peeling caused by the mixture needs to be eliminated in the first step, the PC and ABS components of their own are partially compatible, so in the modification process must be added appropriate compatibilizers to improve their compatibility;
Mold: The principle of mold design should be carried out in the direction of minimizing shear. In general, products with dense skin surfaces are more likely to produce a peeling phenomenon (caused by friction and shear between the melt in the cavity and the inner wall of the cavity during high-speed filling); At the same time, in the design of the gate, the size of the gate is too small, which will cause excessive shear when the melt passes through the gate, and then lead to the skin of the product surface;
Injection molding process: The main direction is to avoid excessive shear. When the product is difficult to fill, high speed and high pressure can be used to improve it, so in the actual injection molding process, you can also consider increasing the injection molding temperature/mold temperature, and improving the flow of materials to reduce the flow resistance in the actual filling process, to avoid excessive shear caused by high speed and high pressure.