New Energy
Within this rapidly evolving sector, injection molding has emerged as a vital manufacturing process. It is instrumental in producing high-quality, precise, and durable components required for new energy applications.
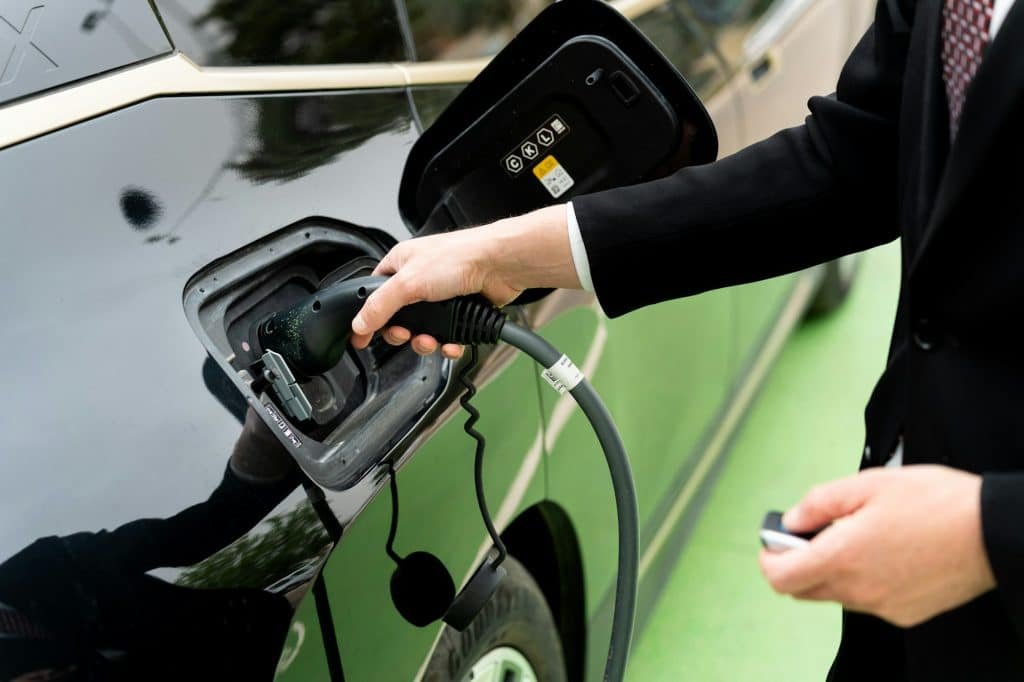
The Role of Injection Molding in New Energy
BFY Mold specializes in providing top-tier injection molding, mold design, mirror spark, and CNC machining services, tailored specifically for the new energy industry. Our advanced manufacturing techniques and commitment to precision make us a trusted partner for producing high-quality new-energy components.
Applications of Injection Molding in the New Energy Industry
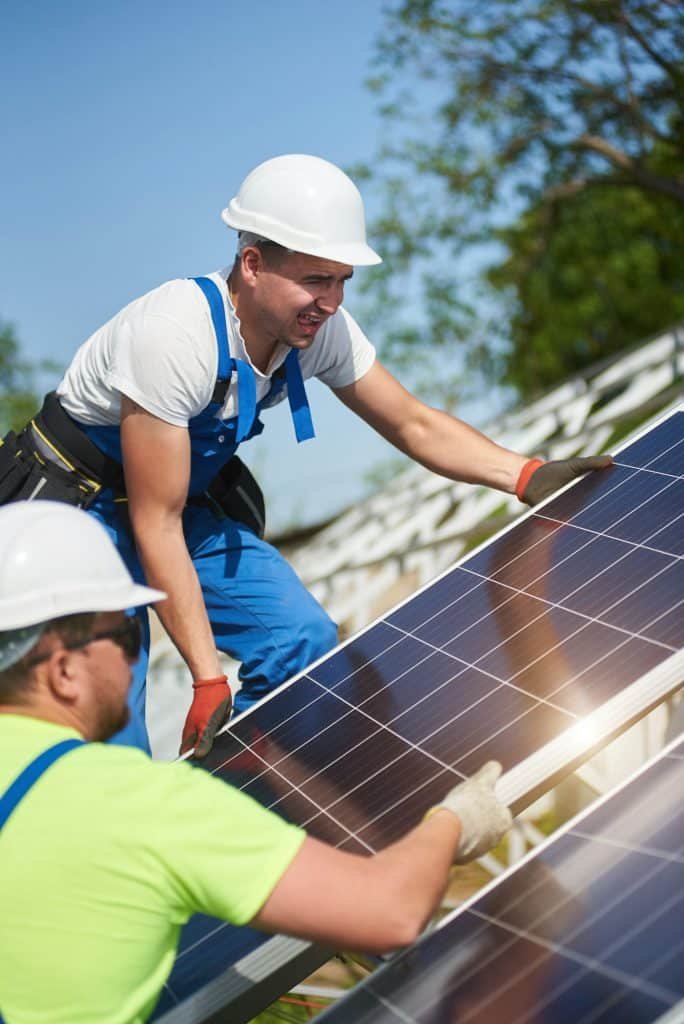
Injection molding is employed in various new energy applications, including:
- Solar Energy: Manufacturing of photovoltaic (PV) module components, such as junction boxes, connectors, and frames, which require precise and durable plastic parts.
- Wind Energy: Production of lightweight and strong components for wind turbine blades, housings, and electrical connectors.
- Electric Vehicles (EVs): Creation of battery housings, charging infrastructure components, and lightweight structural parts to enhance vehicle performance and safety.
- Energy Storage: Fabrication of enclosures, connectors, and insulation components for batteries and other energy storage systems.
- Hydrogen Fuel Cells: Production of components like bipolar plates, seals, and connectors that require high precision and chemical resistance.
Advantages of Injection Molding in the New Energy Industry
BFY Mold combines the strengths of injection molding and CNC machining to deliver comprehensive manufacturing solutions for the new energy industry, ensuring that our clients receive the highest quality products.
High Efficiency: Injection molding allows for the rapid production of parts, reducing lead times and accelerating the time-to-market for new energy products.
Design Flexibility: The process supports complex geometries and intricate designs, enabling the creation of innovative and optimized components.
Material Efficiency: Injection molding minimizes material waste through precise control of the molding process and the ability to recycle excess material.
Durability and Performance: Components produced through injection molding exhibit excellent mechanical properties, ensuring durability and reliability in demanding new energy applications.
Scalability: The process is easily scalable, making it suitable for both small-scale prototyping and large-scale production.

Custom Plastic Injection Molding for New Energy
A Comprehensive Guide to Choosing the Right Injection Molding Company
When it comes to producing high-quality plastic parts, choosing the right injection molding company is crucial....
Hot Runner vs Cold Runner Systems: Making Right Choice
Hot Runner vs Cold Runner: How to Choose? When it comes to injection molding, the choice...
7 Key Elements of Injection Mold Costs
When considering the purchase of an injection mold, especially for mass production of plastic parts, it's...