In the intricate world of manufacturing, the design of the injection mold plays a pivotal role in determining the final product’s quality, efficiency, and cost-effectiveness. Proper mold design is essential to avoid defects, reduce production costs, and ensure consistent output. We should know the critical considerations in designing an injection mold, focusing on undercuts, draft allowance, and wall thickness uniformity. Understanding these elements can help you achieve superior product quality and streamline your manufacturing processes.
Key Considerations in Injection Mold Design
1. Undercuts
Undercuts are features that prevent the easy ejection of a molded part from the mold. They are often necessary for complex geometries and can include threaded holes, side holes, or external undercuts. While undercuts add complexity to mold design, they enable the creation of intricate parts that would otherwise be impossible.

Managing Undercuts:
- Side-Actions and Lifters: These mechanisms are designed to move in and out of the mold to form and release undercuts. They add to the mold’s complexity and cost but are essential for specific designs.
- Collapsible Cores: Used for internal undercuts, collapsible cores retract during the ejection phase, allowing the part to be removed from the mold.
- Part Redesign: In some cases, simplifying the part design to eliminate undercuts can reduce mold complexity and cost. This approach requires a balance between design requirements and manufacturing feasibility.
2. Draft Allowance
Draft allowance refers to the tapering of vertical walls of the mold to facilitate the easy removal of the part. Without an appropriate draft, parts can stick to the mold, leading to defects and production delays.
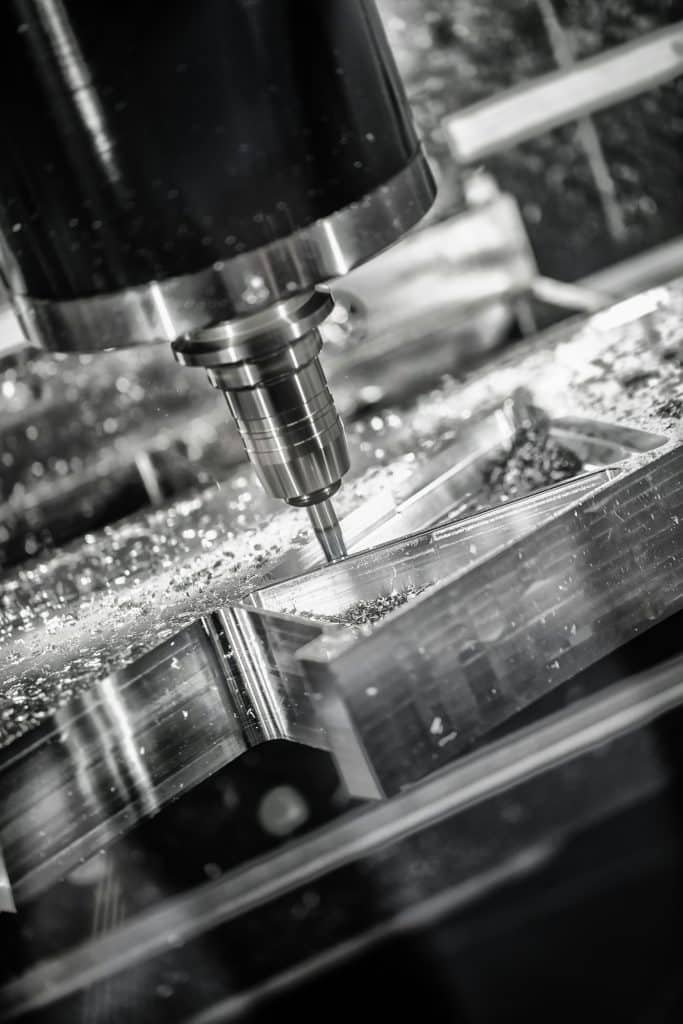
Key Points for Draft Allowance:
- Draft Angle: Typically, a draft angle of 1 to 2 degrees is sufficient for most parts. However, parts with textured surfaces may require a larger draft angle.
- Material Considerations: Different materials have varying shrinkage rates, which can affect the required draft angle. For example, materials with high shrinkage rates may need a larger draft to ensure easy ejection.
- Design Complexity: Complex designs with deep features or intricate details may necessitate higher draft angles to ensure the part is ejected without damage.
3. Wall Thickness Uniformity
Uniform wall thickness is crucial in injection mold design to ensure even cooling and reduce the risk of defects such as warping, sink marks, and voids. Inconsistent wall thickness can lead to differential cooling rates, causing internal stresses and compromising the structural integrity of the part.
Achieving Uniform Wall Thickness:
- Design Guidelines: Follow design guidelines that recommend uniform wall thickness throughout the part. This helps in maintaining consistent material flow and cooling.
- Ribs and Gussets: Use ribs and gussets to add strength to thin-walled sections without increasing the overall wall thickness. These features also help in maintaining uniform cooling.
- Simulation Tools: Utilize simulation software to predict the material flow and cooling behavior. This allows designers to identify and address potential issues related to wall thickness before the mold is manufactured.
Other Important Considerations
4. Gate Location
The gate is the point where the molten plastic enters the mold cavity. Its location can significantly impact the quality and aesthetics of the final part.
Optimal Gate Placement:
- Flow Path: Ensure the gate is placed to allow a balanced flow of material, minimizing the risk of air traps and weld lines.
- Cosmetic Considerations: Position the gate in a location that does not affect the appearance of the part, especially for visible surfaces.
- Ejection Efficiency: Place the gate to facilitate easy ejection and minimize the potential for part deformation.
5. Cooling System Design
Efficient cooling is vital for reducing cycle times and ensuring part quality. The design of the cooling system directly affects the mold’s performance and the quality of the molded parts.

Effective Cooling Strategies:
- Uniform Cooling Channels: Design cooling channels to provide uniform cooling across the entire mold. This helps in reducing cycle times and ensuring consistent part quality.
- Advanced Cooling Techniques: Consider advanced cooling techniques such as conformal cooling, which uses 3D-printed channels that conform to the shape of the part, providing more efficient cooling.
- Thermal Analysis: Conduct thermal analysis during the design phase to optimize the cooling system and identify any potential hotspots that could lead to defects.
BFY Mold: Your Partner in Precision Mold Design
At BFY Mold, we understand that meticulous mold design is the cornerstone of successful manufacturing. Our team of experts combines advanced technology with extensive industry experience to deliver injection molds that meet the highest standards of quality and precision. Whether you require complex geometries or high-volume production, we are dedicated to providing solutions that enhance your manufacturing processes.

Our comprehensive range of services includes:
- Injection Molding and Mold Manufacturing: Custom mold design and production to ensure precision and consistency in every part.
- Mass Production and On-Demand Production: Flexible production capabilities for both large-scale and specialized orders.
- CNC Machining and Mirror Spark: Advanced CNC machining and mirror spark services for high-precision parts and intricate designs.
With our factory and a commitment to excellence, BFY Mold is your trusted partner in achieving manufacturing success. Contact us today to learn how our expertise in injection mold design can transform your production processes and help you stay ahead in a competitive market.
Summary
Injection mold design is a critical aspect of the manufacturing process that requires careful consideration of various factors, including undercuts, draft allowance, and wall thickness uniformity. By understanding and addressing these considerations, manufacturers can achieve superior product quality, reduce production costs, and improve overall efficiency. BFY Mold is here to support you in navigating these complexities and delivering top-tier manufacturing solutions tailored to your needs.