Hot Runner vs Cold Runner: How to Choose?
When it comes to injection molding, the choice between hot and cold runner systems can significantly impact production efficiency, costs, and the overall quality of the molded products. Both systems have their advantages and limitations, but knowing which one suits your needs best requires an understanding of how they work and what they offer. This article will guide you through the key differences, benefits, and considerations for choosing between hot and cold runner systems.
Understanding Cold and Hot Runner Systems
The runner system in injection molding is responsible for directing molten plastic from the injection molding machine to the mold cavities. There are two main types of runner systems: hot runner and cold runner.
- Cold Runner System: In a cold runner system, the plastic flows through unheated channels into the mold cavities. Once the plastic cools, the runner solidifies and is ejected along with the part. These runners often need to be manually removed or separated from the part after molding, which adds an extra step in the process.

- Hot Runner System: A hot runner system, on the other hand, uses heated channels to keep the plastic in a molten state until it enters the mold cavities. This eliminates the need for ejecting solid runners and reduces material waste. Hot runner systems are typically more complex and costly upfront, but they can offer greater efficiency in the long run.

Hot Runner vs Cold Runner: Choosing the Best Fit for Your Product
Deciding between a hot and cold runner system depends on several factors, including the specific requirements of your product and your manufacturing goals. Here’s how the two systems compare:
- Material Waste: Cold runner systems produce waste in the form of solidified runners that must be discarded or recycled. This can increase material costs. Hot runner systems minimize material waste by keeping the plastic molten throughout the process, making them more eco-friendly and cost-effective in high-volume production.
- Cycle Time: Hot runner systems generally result in shorter cycle times since there’s no need to wait for the runners to cool and be ejected. Cold runner systems can lead to longer cycle times due to the cooling and additional processing of the runners.
- Complexity and Maintenance: Cold runner systems are simpler and easier to maintain since they don’t have the heating elements required in a hot runner system. Hot runners, however, require more precise temperature control and maintenance, which can add to production downtime if issues arise.
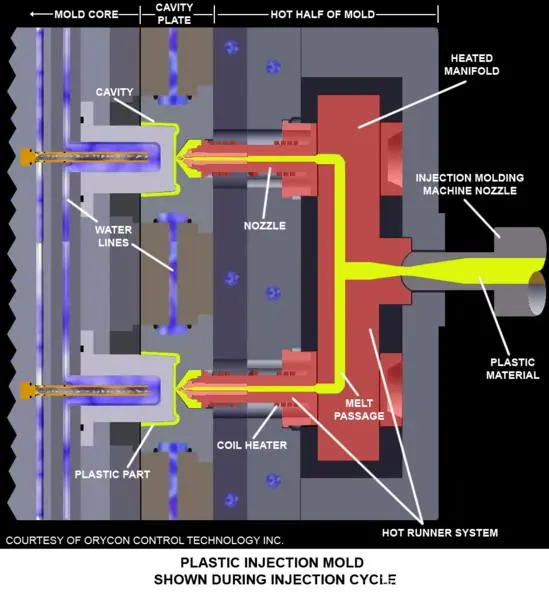
- Part Aesthetics and Quality: Hot runner systems tend to produce better-looking parts with fewer surface defects, as there are no runners or gates that can leave marks on the product. Cold runner systems may lead to imperfections, such as gate marks, especially in high-precision applications.
Key Factors When Deciding Between Hot and Cold Runners
To make the best decision for your product, consider these essential factors:
- Production Volume: For high-volume production runs, a hot runner system is often more economical in the long run despite its higher initial cost. The reduction in material waste and faster cycle times can lead to significant savings over time. For smaller production runs, cold runner systems may be more cost-effective since they are less expensive to set up.
- Part Design and Size: If your product design requires intricate details or a high level of surface quality, a hot runner system may be the better choice, as it provides more consistent molding with fewer imperfections. Cold runner systems can be suitable for less complex designs where surface quality is not a primary concern.
- Material Choice: Some materials are more compatible with cold runner systems, while others may benefit from the continuous heating provided by hot runner systems. For example, materials that are prone to degradation at higher temperatures may not perform well in a hot runner system.
- Cost Considerations: Hot runner systems come with a higher upfront cost due to the added complexity and heating components. Cold runner systems, by contrast, have a lower initial investment but may lead to higher material waste costs over time. Balancing your budget with long-term efficiency is key.

Additional Considerations for Your Runner System Selection
There are a few more elements you might want to take into account when choosing between hot and cold runner systems:
- Lead Time and Setup: Cold runner systems are easier to set up and generally have shorter lead times. If your production timeline is tight, a cold runner system might be more suitable.
- Automation: If you’re looking to automate the process, hot runner systems integrate better with automation equipment due to the elimination of runner removal steps. This can lead to more efficient and streamlined production lines.
- Environmental Impact: The sustainability of your manufacturing process is an increasingly important consideration. Since hot runner systems reduce material waste, they are often seen as the more environmentally friendly option, especially when producing large quantities.
- Tooling Costs: While hot runner molds tend to have higher initial tooling costs due to their complexity, cold runner molds are simpler and cheaper to manufacture. However, the potential savings in material waste and production speed with a hot runner may outweigh the higher tooling investment over time.
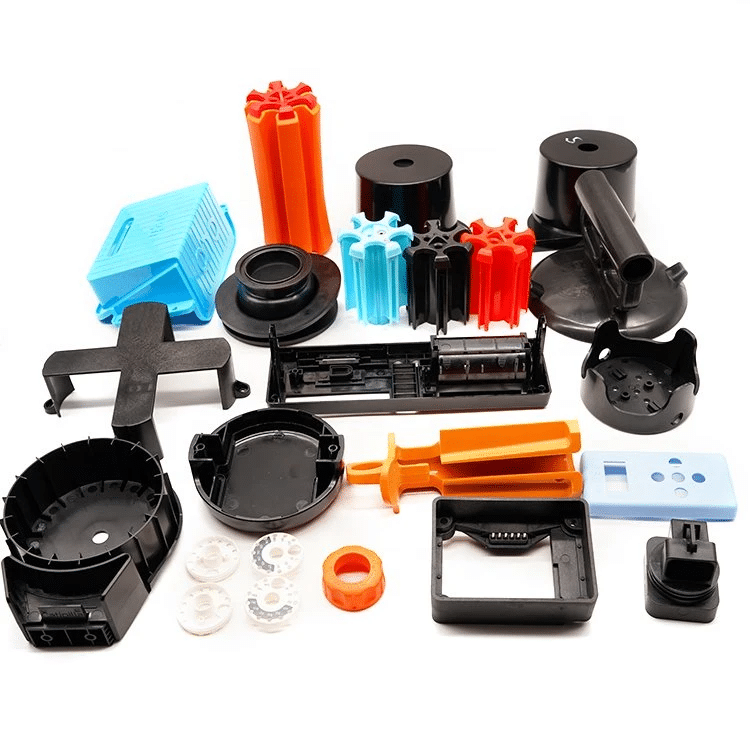
Top 10 FAQs for Supplier Selection & Cost Optimization
1. What are the key differences between hot and cold runner systems?
Hot runner systems maintain molten plastic in heated manifolds (reducing waste), while cold runner systems use solidified runners that are trimmed post-molding. Hot runners save 15–30% material but cost 2–3x more upfront.
2. Which industries benefit most from hot runner systems?
- Medical: High-purity parts (no runner contamination).
- Automotive: High-volume components like dash panels.
- Electronics: Thin-walled parts requiring precise fill rates.
3. How much does a hot runner system cost compared to a cold runner?
- Hot Runner: 20,000–100,000+ (depending on cavities and controls).
- Cold Runner: 5,000–30,000.
Hot runners offer long-term ROI via material savings but require a higher initial investment.
4. What are the maintenance challenges of hot runner systems?
- Thermal degradation: Requires annual nozzle cleaning (1,500–5,000).
- Heater failure: Replace cartridges every 2–3 years (200–800 each).
- Process control: ±1°C temperature stability demands advanced controllers.
5. Can cold runner systems handle high-temperature engineering resins?
Yes, but cold runners risk material waste (20–30% scrap) with high-cost resins like PEEK or Ultem. Hot runners are preferred for engineering plastics to reduce waste.
6. How do hot runner systems improve cycle times?
By eliminating runner cooling, hot runners reduce cycle times by 10–25%. Example: A 30-second cycle with cold runners drops to 22–27 seconds.
7. What quality issues arise with cold runner systems?
- Sink marks: Thick runners cool slower than parts.
- Gate vestiges: Trimming leaves visible marks on cosmetic parts.
- Material inconsistency: Recycled runner plastic degrades properties.
8. Are hybrid hot/cold runner systems viable for medium-volume production?
Yes. Hybrid systems combine hot runners for critical gates and cold runners for simplicity, cutting costs by 20–40% vs full hot runner setups.
9. How do I choose a supplier for hot runner components?
Verify suppliers offer:
- Custom manifold design for your part geometry.
- PID temperature control (±0.5°C accuracy).
- 24/7 technical support for troubleshooting.
10. What emerging technologies are shaping hot/cold runner systems?
- AI-driven flow balancing: Reduces part variation by 50%.
- 3D-printed manifolds: Cut lead times from 12 weeks to 3–5 days.
- Sustainable materials: Bio-based resins compatible with both systems.
Conclusion
Choosing between a hot and cold runner system is a crucial decision that depends on your production goals, budget, and the specifics of your product design. While cold runner systems are simpler and more affordable upfront, hot runner systems can offer significant long-term benefits in terms of efficiency, material savings, and product quality. Carefully evaluate your needs and consult with an experienced mold manufacturer to make the right choice for your injection molding process.
About BFY Mold
At BFY Mold, we specialize in injection molding processing and mold production, and manufacturing. Our services include mass production, on-demand production, CNC machining, and mirror sparking, all supported by our factory. We are committed to delivering high-quality, customized solutions to meet your specific project needs. Contact us to explore the best options for your injection molding requirements.