Introduction to Injection Molding Machines
Injection molding machines are one of the most common types of equipment in the manufacturing industry, and they are used to produce plastic parts efficiently and in large quantities. From simple everyday items to complex components for high-tech industries, these machines are godsends. Therefore, it is important to familiarize yourself with their working principles, functionalities, features, and usability in process production to ensure optimal performance and the best possible results.
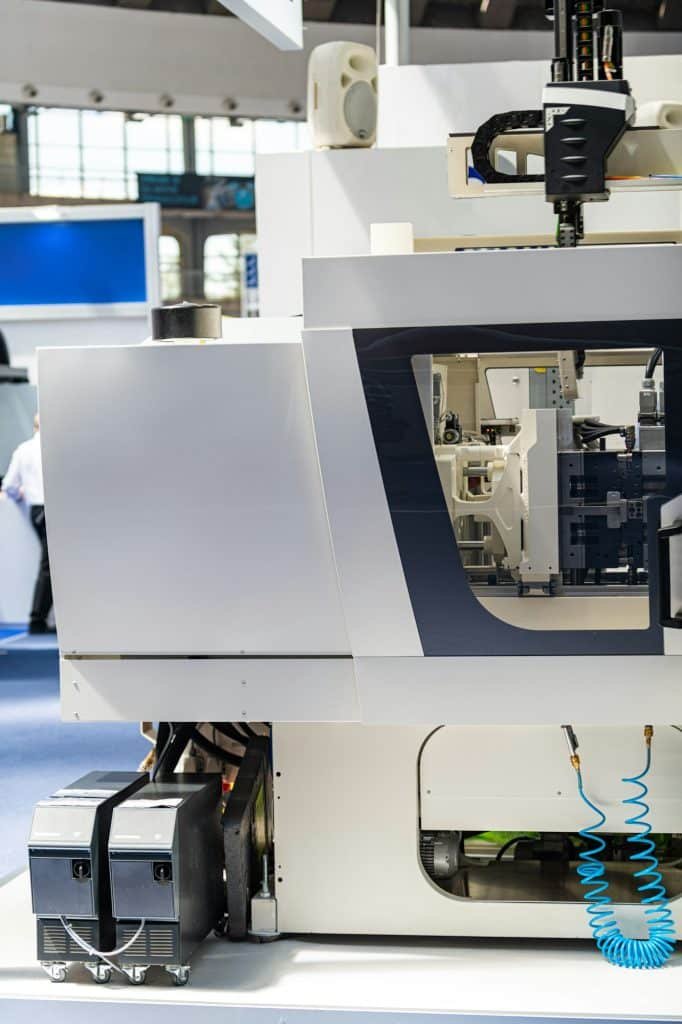
In this blog, we’ll cover:
- What is an injection molding machine
- Types of Injection molding machines
- Key features and components
- Benefits and applications
- How to choose the best machine for your job
What Is an Injection Molding Machine?
An injection molding machine is a device that melts plastic material and molds it into the desired shape. The process involves:
- Clamping – Holding the mold securely.
- Injection — forcer molten plastic into the mold.
- Cooling — Letting the plastic harden.
- Ejection – The process of removing the finished part from the mold.
These machines are used throughout industries, from automotive to medical devices to electronics and consumer goods, for their ability to provide consistent, high-quality parts at scale.
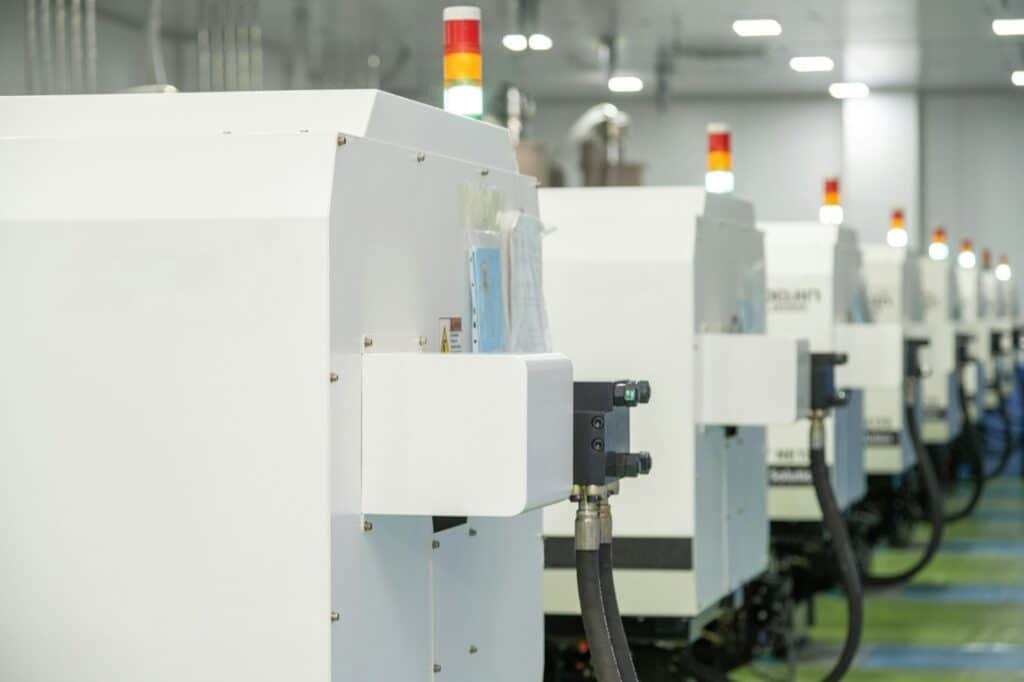
Injection Molding Machine types
1. Injection Molding Machines Hydraulic
A hydraulic machine — an industry standard for decades. They apply hydraulic systems to create the clamping pressure and therefore, work efficiently and are used for large parts or molds with several cavities.
Key Benefits:
- High clamping force
- Long-term economic for mass manufacturing
- Designed to withstand demanding uses
2. Electric Injection Molding Machines
Now, an electric machine uses Servo motors and is known to be precise and energy-efficient. They are used in industries where high accuracy is critical like medical devices and electronics.
Key Benefits:
- Energy-efficient
- Faster production cycles
- Low maintenance costs
3. Hybrid Injection Molding Equipment
Hybrid machines do a great job of blending hydraulic and electric, so you get the best of both technologies. They offer high clamping force with energy efficiency and accuracy.
Key Benefits:
- Versatility in applications
- Fair cost-performance ratio
- Well suited for parts of medium-high complexity
4. Micro Injection Molding Machines
Micro machines, which are used to create tiny, complex parts, are commonly used in the medical and electronics sectors, where precision is of utmost importance.
Key Benefits:
- Good accuracy for micro elements
- Compact and efficient
- Minimal material waste
Elements of an Injection Molding Machine
1. Injection Unit
Only a few components are typically involved in the injection unit, which melts and injects the plastic material into the mold. It consists of the barrel, the screw, and the nozzle.
2. Clamping Unit
This unit securely clamps the mold during the injection and cooling stages.
3. Control System
Most modern machines incorporate computerised control mechanisms enabling better monitoring and adjustments.
4. Mold
The mold is a highly engineered tool that shapes the final product. Precision in mold design is paramount in achieving the same output.

Advantages of Injection Molding Machines
- High Production Capacity: Ideal for mass-producing plastic components.
- Design Flexibility: Enables intricate shapes and designs.
- Material Versatility: Able to work with a broad array of thermoplastics and thermosets.
- Efficiency: It saves production time and material waste.
- Cost-Effective: Best suited for large-scale production, lowering the cost per piece.

How is Injection Molding Machines Used?
Injection molding machines are used in multiple industries, such as:
Automotive
Manufacturing of automotive parts including dashboards, bumpers, and interior trims.
Medical Devices
Making accurate, long-lasting components such as syringes, surgical equipment, and housings.
Electronics
Creating connectors, housings, and small components for consumer electronics.
Consumer Goods
Making toys, kitchenware, and common plastic products.
Injection Molding: How to Choose the Right Machine
- Material Compatibility: Check that the machine is capable of handling the material you wish to use.
- Part Size and Complexity: Ensure the machine’s clamping force and shot size meet your part needs.
- Production Volume: Choose a machine with enough capacity for the production requirements.
- Energy Efficiency: Choose electric or hybrid machines to lower operating costs.
- Budget: Be mindful of how much you’re spending upfront versus in the long run in terms of performance and maintenance.
Why BFY Mold, is a Way to Co-Ease with You

BFY Mold— Your Expert Service of Injection Molding & Mold Making We have our own factory and advanced equipment.
- Mass Production: All of the mass production scalable solutions.
- On-Demand Production: Flexible production schedules for unique requirements.
- CNC Machining and Mirror Spark: Precision tooling for superior results.
- Custom Mold Design: From prototyping to final production molds.
With a focus on quality and innovation, our team of experts is dedicated to providing you with the most reliable solutions at the most cost-effective prices.
Final Thoughts
Injection molding machines enable modern manufacturing, as they provide efficiency, versatility, and scalability for a wide range of applications. Knowing their types, features, and benefits will help you choose the correct ones for your production needs.
Trust in BFY Mold for your injection molding and manufacturing needs. Reach out to us and see how our new technology can support your project.