Introduction
Extrusion and injection molding are extensively used by manufacturers to produce plastic products in an efficient and economical manner. Even though both processes uses molds and plastic materials, they are completely different processes with different applications and end-product design.
The correct level enables you to determine quality, production cost, and functionality. Let’s take a closer look at these two processes, putting them side by side to help you determine which is right for your manufacturing needs.
What Is Extrusion?
Extrusion is a process that can be used to create plastic continuous pieces by melting the plastic and inserting it into a mold.
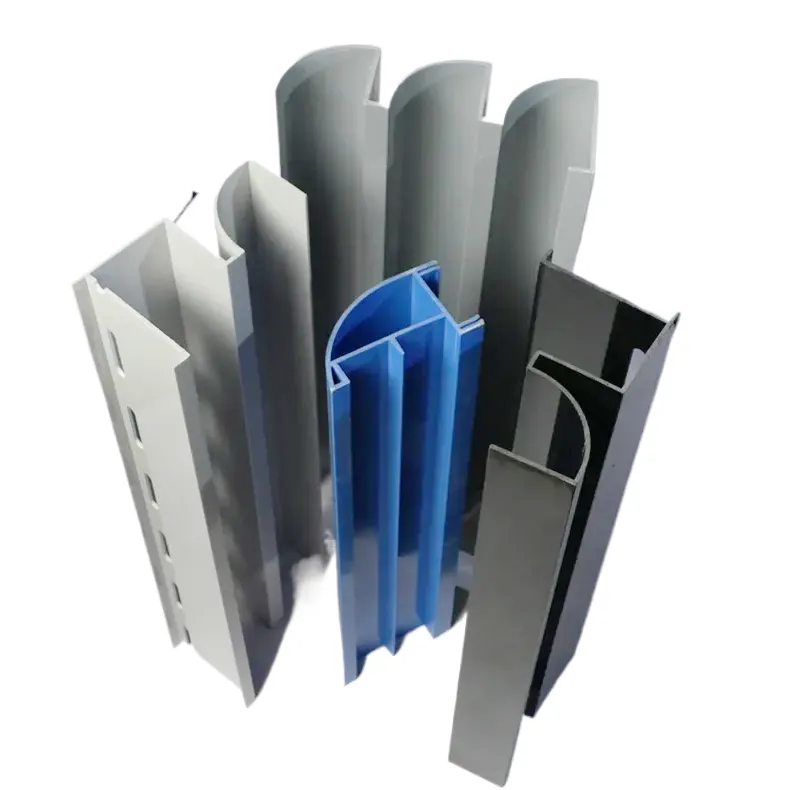
Key Steps in Extrusion:
- Feeding: Plastic pellets or granules are introduced into a heated barrel.
- Melt: Heat and pressure melt the material.
- Forming: The molten plastic is forced through a die and it takes a continuous shape.
- Cooling: The profile is cooled, solidified, and cut into required lengths.
Applications of Extrusion:
- Pipes, tubes, and hoses
- Frames and weatherstripping for windows
- Plastic films and sheets
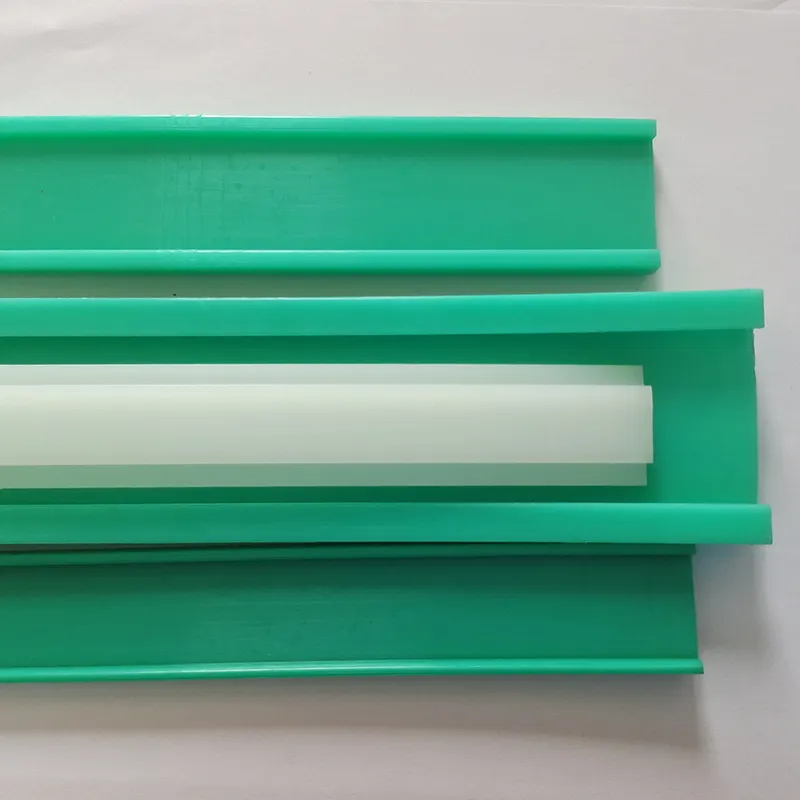
What Is Injection Molding?
Injection molding is a manufacturing process in which molten plastic is injected into a mold to form individual parts that have specific shapes and features.
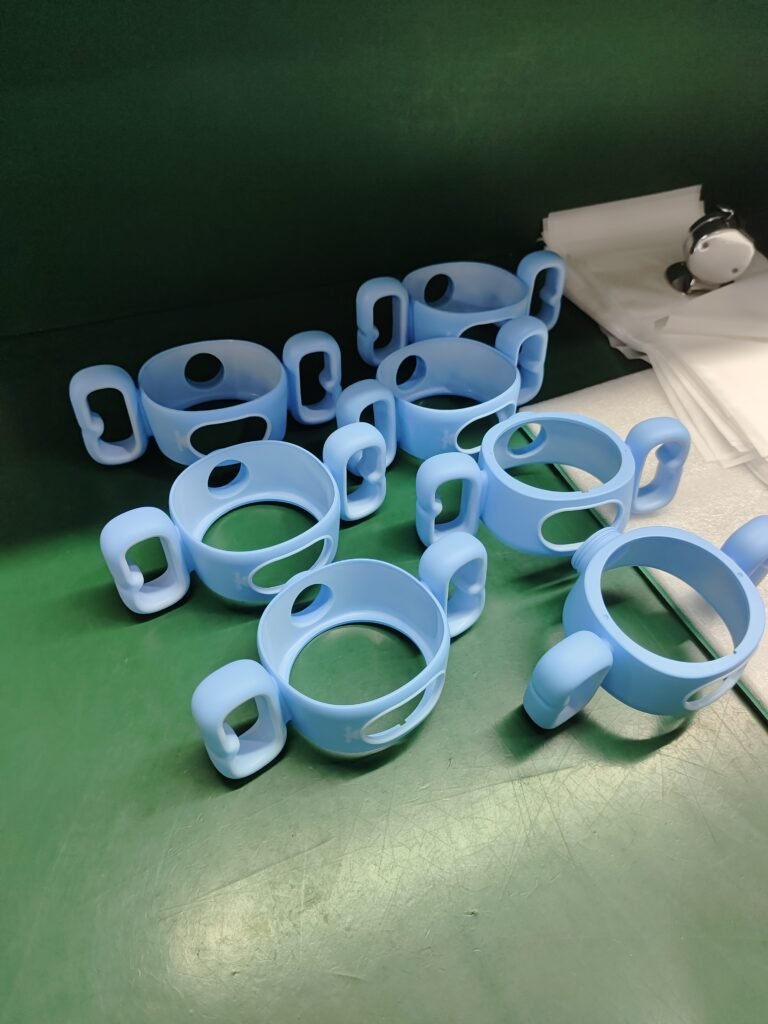
Important Processes in Injection Molding:
- The closing of the mold is referred to as clamping.
- Injection: In this step, the mold cavity is filled with molten plastic.
- Cooling: The material cools and hardens inside the mold.
- The finished part is removed from the mold (Ejection).
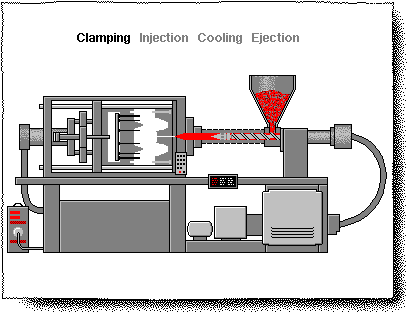
Injection Molding Applications:
- Automotive parts
- Medical devices
- Toys and containers are consumer goods

Injection Molding vs. Extrusion In-depth Guide
Let’s separate the differences between extrusion and injection molding into some categories for clarity.
Aspect | Extrusion | Injection Molding |
Process | Continuous process; creates long, uniform shapes | Cyclical process; produces discrete parts |
Material Use | Uses thermoplastics and thermosets, often with less waste | Ideal for thermoplastics; optimized material usage |
Product Types | Tubes, pipes, sheets, films, and profiles | Complex, detailed parts like gears, housings, and medical devices |
Tooling Costs | Lower tooling costs due to simpler dies | Higher tooling costs for intricate molds |
Production Volume | Suitable for high-volume, continuous production | Ideal for high-volume production of discrete items |
Precision | Limited to basic shapes | Highly precise for intricate designs |
Flexibility | Limited design flexibility | High design flexibility, including complex geometries |
Cooling Time | Typically faster due to continuous process | Cooling time can affect cycle duration |
Applications | Construction, packaging, and industrial products | Consumer goods, automotive, and medical components |
Key Benefits of Extrusion
- Blending of continuous flow: Suitable for uniform products and large-scale production.
- Min Tooling Cost: Lower tooling cost as compared to metal production.
- Material types: Usable with most types of polymers including recycled plastics.
Advantages of Injection Molding
- Intricate Patterns: Ideal for producing elaborate parts with fine details.
- High Precision: Provides reproducibility of quality across production batches.
- Scalable: Can be used for high-volume creation of distinct competitive goods.
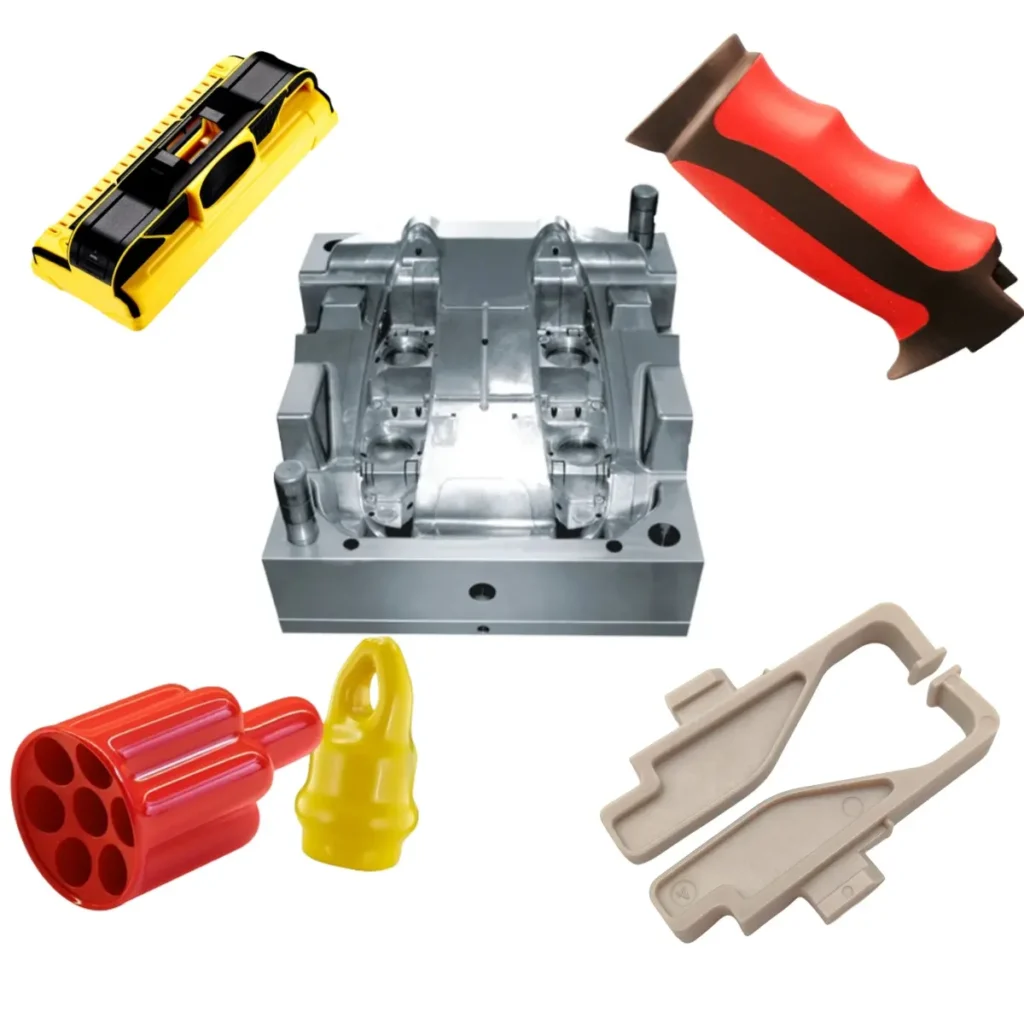
Choosing Between Extrusion and Injection Molding
The right process depends on several factors:
- Product Design: Use extrusion for continuous shapes and injection molding for intricate parts.
- Dope: Look at plastic types and mechanical properties.
- Production Volume: Extrusion is also great for continuous, high-scale, high-volume manufacturing, whereas injection molding is best for discrete manufacturing, large-batch production.
- Type of tooling: Determine tooling and production costs with your project requirements.
Industries & Applications
Although both processes serve a wide range of industries, they are used differently:
Industry | Extrusion Applications | Injection Molding Applications |
Automotive | Window trims, protective films | Bumpers, dashboards, and gear components |
Construction | Pipes, frames, and insulation materials | Fasteners, electrical housings, and fittings |
Packaging | Film, sheets, and containers | Lids, caps, and customized packaging |
Medical | Tubing and IV bag materials | Syringes, casings, and surgical tools |
Consumer Goods | Plastic furniture and storage containers | Toys, electronics, and kitchenware |
BFY Mold: A Trustworthy Partner for Your Injection Molding Project
BFY Mold provides superior manufacturing solutions in the following categories:
Mold Making and Injection Molding: Tooling and production capabilities.
Mass Production / On-Demand Production: Tailor-able “production line” services to fit your business requirements.
Our factory and staff also allow us to guarantee a project that meets all parameters for time and quality.
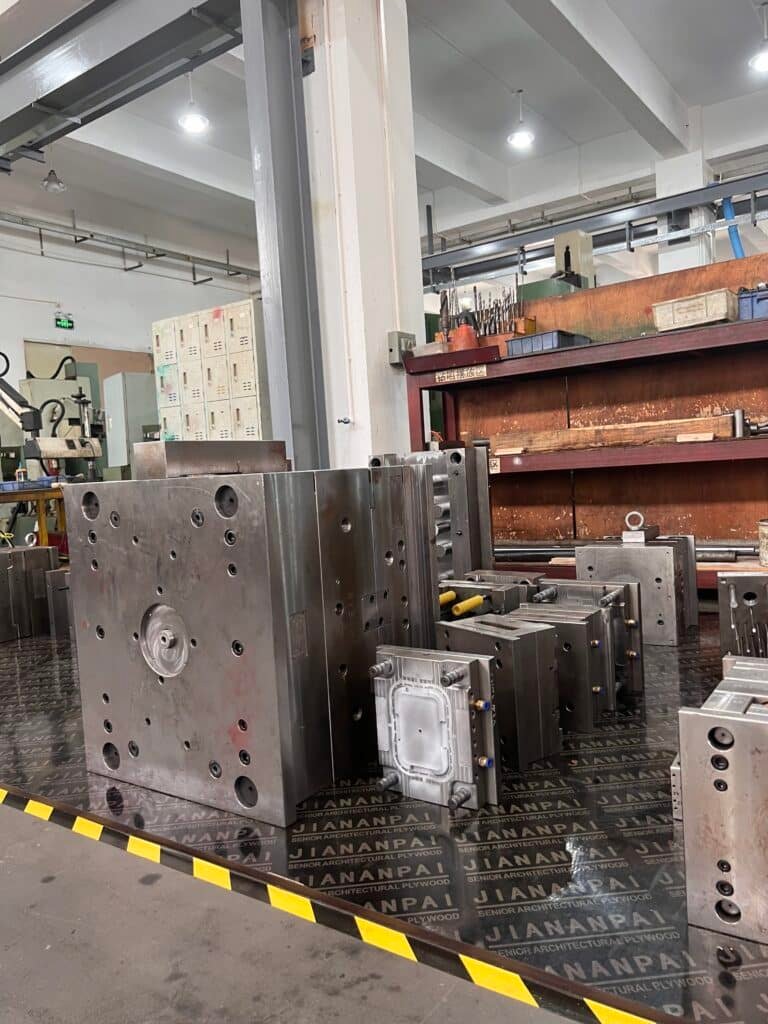
Final Thoughts
Extrusion and injection molding play an important role in modern manufacturing. Extrusion may be perfect for continuous profiles but injection molding is peerless when it comes to precision and complexity in part design. Knowing the distinctions and applications, you can opt for the best method for your task.
BFY Mold specializes in full-scale manufacturing for various industries. Ask us how we can manufacture your designs with cutting-edge technology.