Food-grade plastics are extremely important in food and beverage packaging, storage, and production. Due to increasing safety regulations, food safety is becoming a priority among consumers, so selecting the right plastic for food applications is crucial now more than ever. In this post, we will discuss the food contact polymer materials that are most widely used in food-grade packaging, their material properties, and applications. This guide will also enable businesses to pinpoint the best materials that correspond with safety, durability, and regulatory compliance.
What Are Food-Grade Plastics?
Food-grade plastics are materials that have been tested and approved by a government agency (e.g., the Food and Drug Administration, the EU Food Safety Authority) for direct food/beverage contact use. They are free of chemicals, toxins, or contaminants that could harm food security.
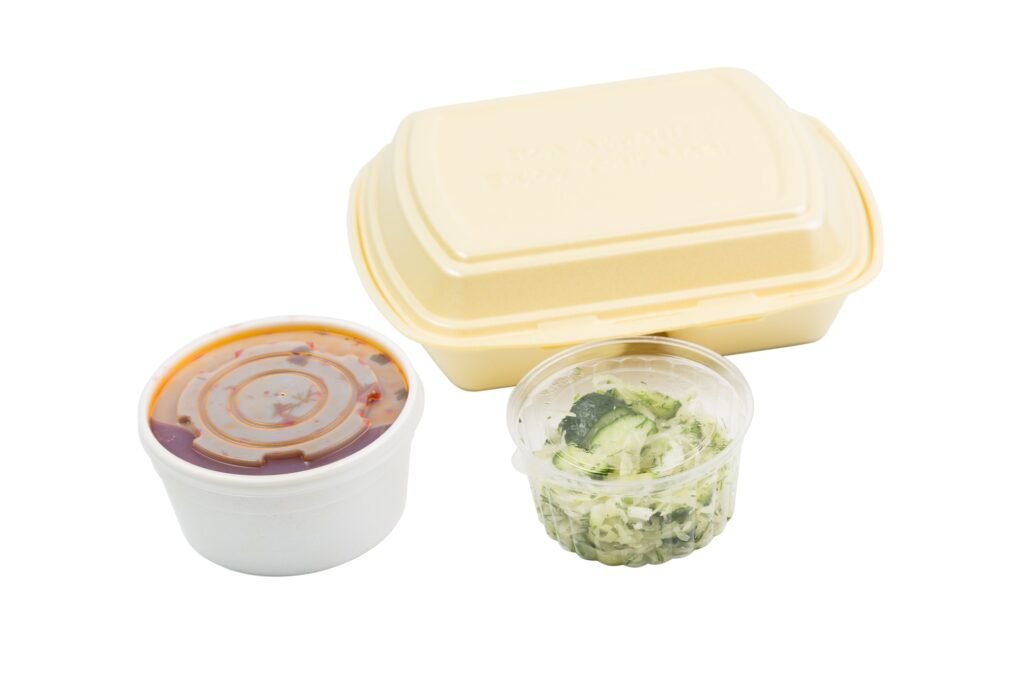
Food-grade plastic must pass rigorous safety tests and must ensure the following:
- Resistance to temperature variations
- Non-reactivity with food and drinks
- Durability for packaging, storage, and transportation
- Ability to maintain food freshness and prevent contamination
Now, let’s go through a few of the most prevalent food-grade plastic resins used in the food industry.
6 Common Food-grade Plastic Resins
- Polyethylene Terephthalate (PET)
- Polypropylene (PP)
- Add a high-density polyethylene (HDPE)
- Low-Density Polyethylene (LDPE)
- Polycarbonate (PC)
- Polystyrene (PS)
If you are looking to make plastic food packaging yourself, you need to ensure that you are working with materials that won’t react adversely to the food that will come into contact with them.
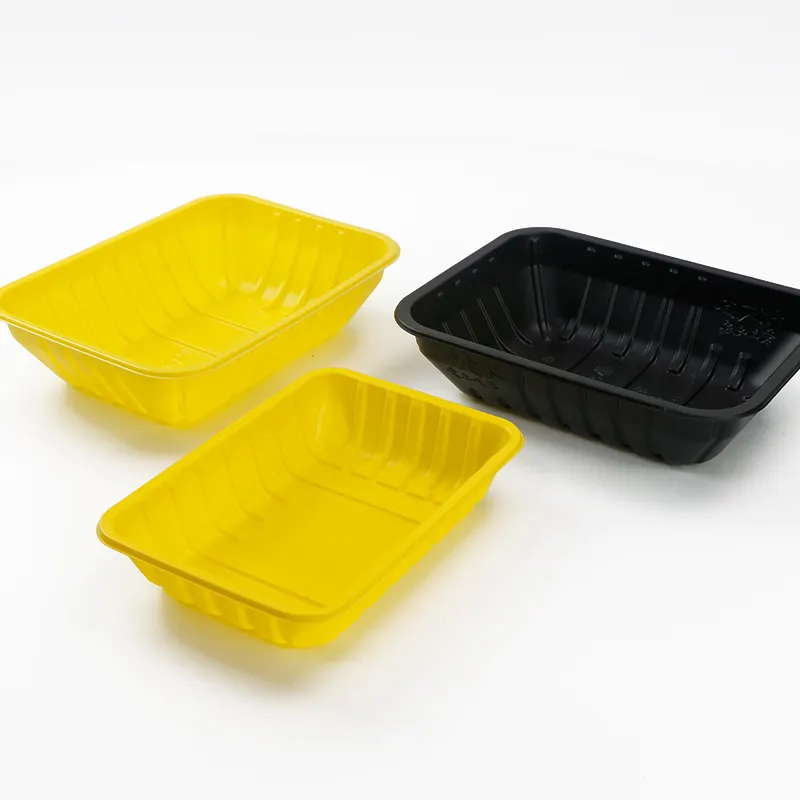
For plastic injection molding, those are referred to as food-grade plastic resins. These are resins that the Food and Drug Administration (FDA) has approved for contact with food. These are also referred to as food contact substances (FCS).
Here’s a guide for how to choose the right resin for you, with a breakdown of the different food-grade plastic resins available and their application recommendations:
Polyethylene Terephthalate (PET)
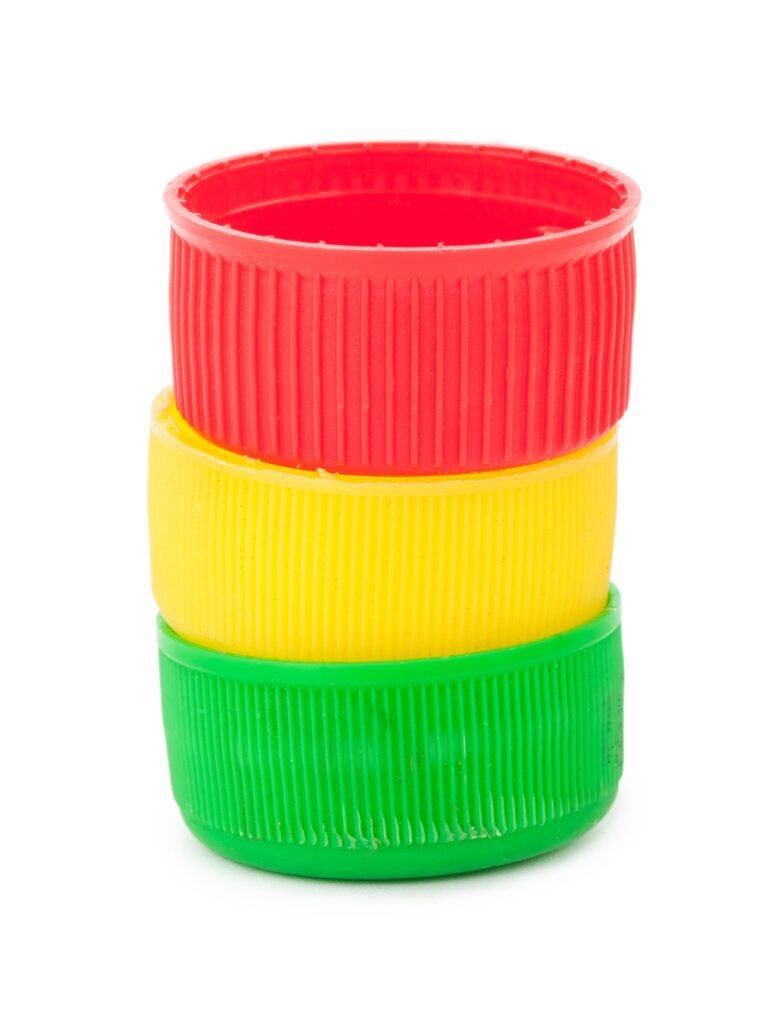
Polyethylene Terephthalate, or PET, is a widely used resin for food packaging. It is the second most widely used plastic for this type of application. PET is found in liter soda bottles, salad dressing bottles, peanut butter jars, and nearly every type of plastic food container you can imagine.
PET is used to produce single-serving drinking bottles, microwaveable plastic containers, take-out containers, and single-use food trays. The FDA has also approved the use of virgin and recycled PET for these purposes.
That has led to its widespread use, even after recycling, because PET is safe when it touches food. It is biologically inert, which means the stuff has no reaction to anything it touches when ingested, handled with bare skin, or inhaled. It’s also a stable resin, so it won’t break down in the presence of food or beverages. It has excellent corrosion resistance and repels most microorganisms.
Polypropylene (PP)
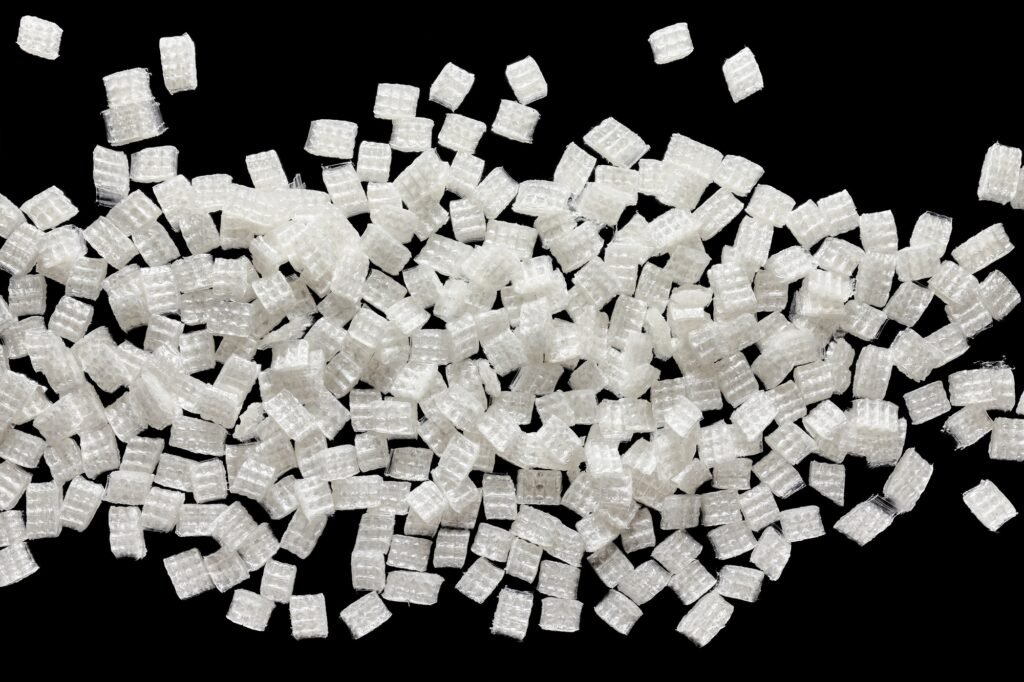
Another common plastic widely used in the food and beverage industry is polypropylene (PP). You probably have some PP plastic food containers in your fridge or cupboards right now! PP is commonly used to produce reusable food storage containers, like Tupperware. It’s also in plastic food containers and bins, such as ice cream and yogurt containers.
PP (Polypropylene) plastics are inert and stable, just like PET plastics. So, they don’t pose a health risk to users and don’t interact with liquids, acids, and bases—making them great for a wide range of foods. PP plastics (one of the most commonly recycled plastics) are also a food-safe material. They also have a high melting point, allowing them to be reused and heated.
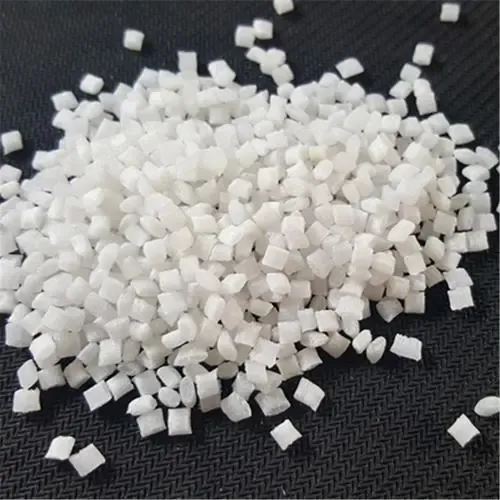
High-Density Polyethylene (HDPE)
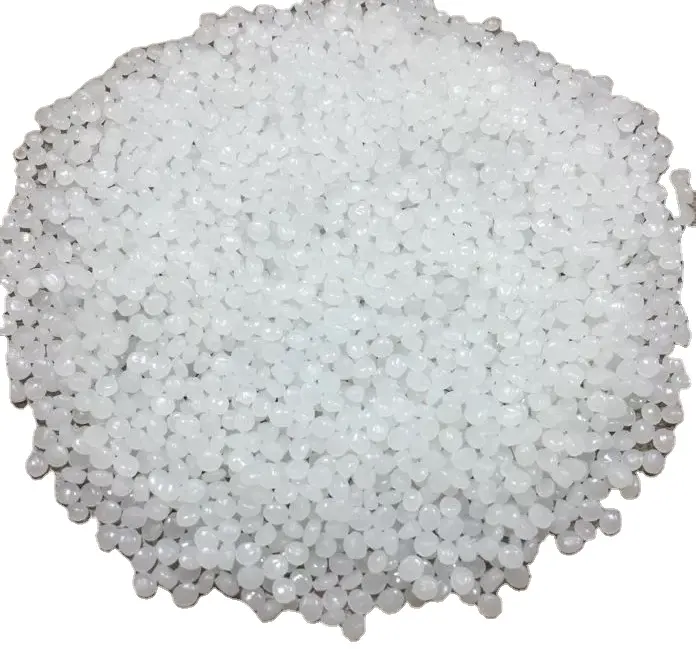
HDPE is a food-safe plastic commonly found in households. You see it in the juice and drink aisles of your groceries as the plastic bottles containing your favorite libations. It is also frequently used in the production of high-quality food buckets used in schools, food concessionaires, and restaurants.
HDPE resins are ideal for producing food and beverage containers that require very low moisture absorption and high chemical resistance. So, they’re typically used to hold drinks. Bonus: HDPE containers don’t leech coloring or chemicals into their contents, meaning they can hold beverages stably for quite a while.
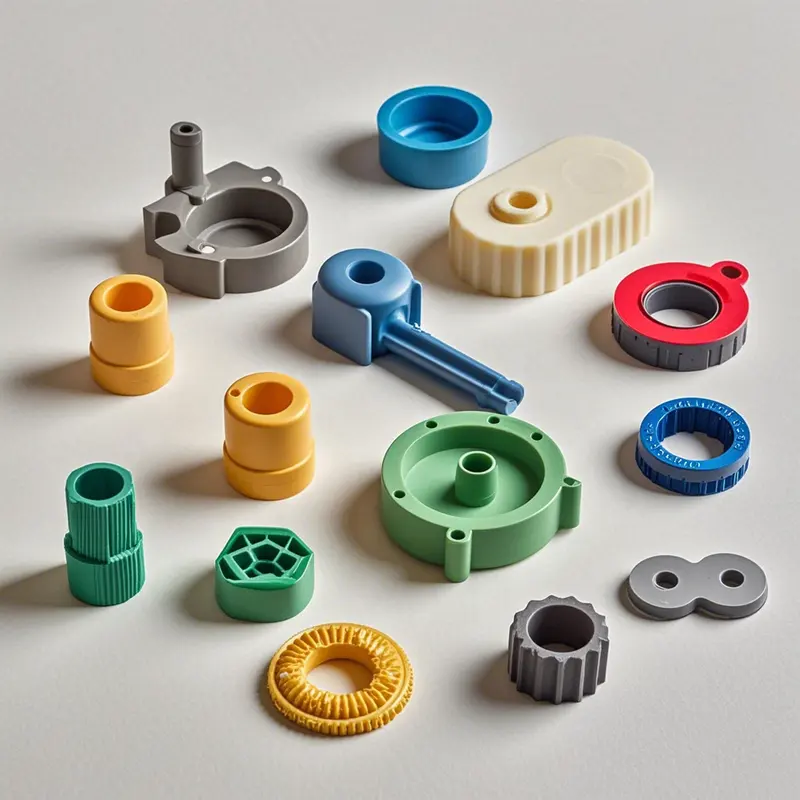
Low-Density Polyethylene (LDPE)
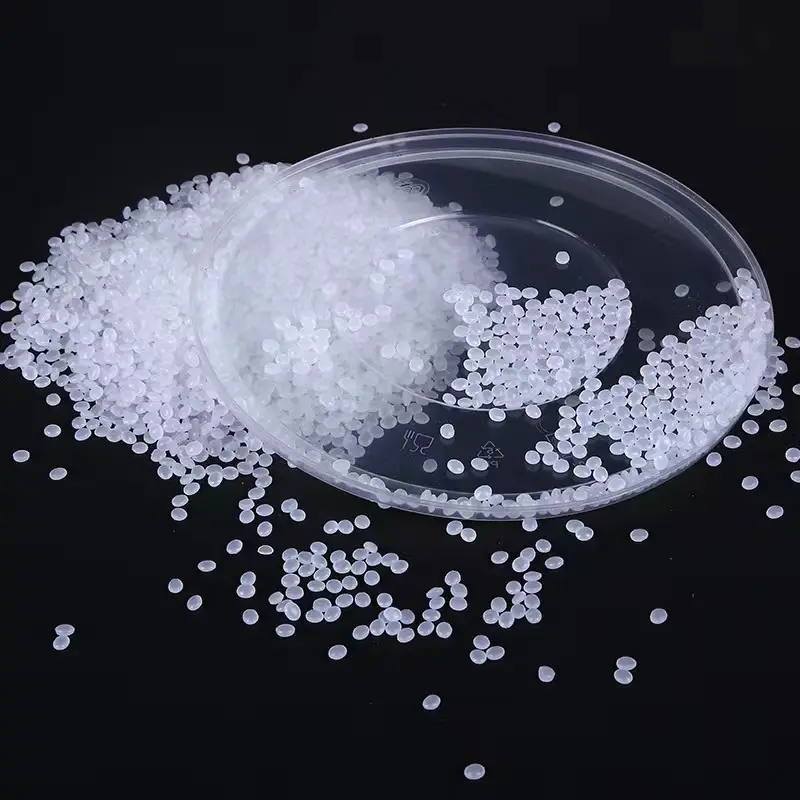
The LDPE resin is similar to but less rigid and durable than the HDPE plastics. So, it is favored for applications in which you want the packaging to be more ductile—think ketchup and mustard squeeze bottles, plastic wrap for veggie and meat products, six-pack rings, and so forth.
LDPE plastics, like HDPE plastics, have excellent chemical, impact, and wear resistance. They can also preserve food products for a long time without harmful materials and chemicals leaching into the food. Similarly, this helps deter microorganisms from entering or multiplying within the contained foods and beverages.
Polycarbonate (PC)
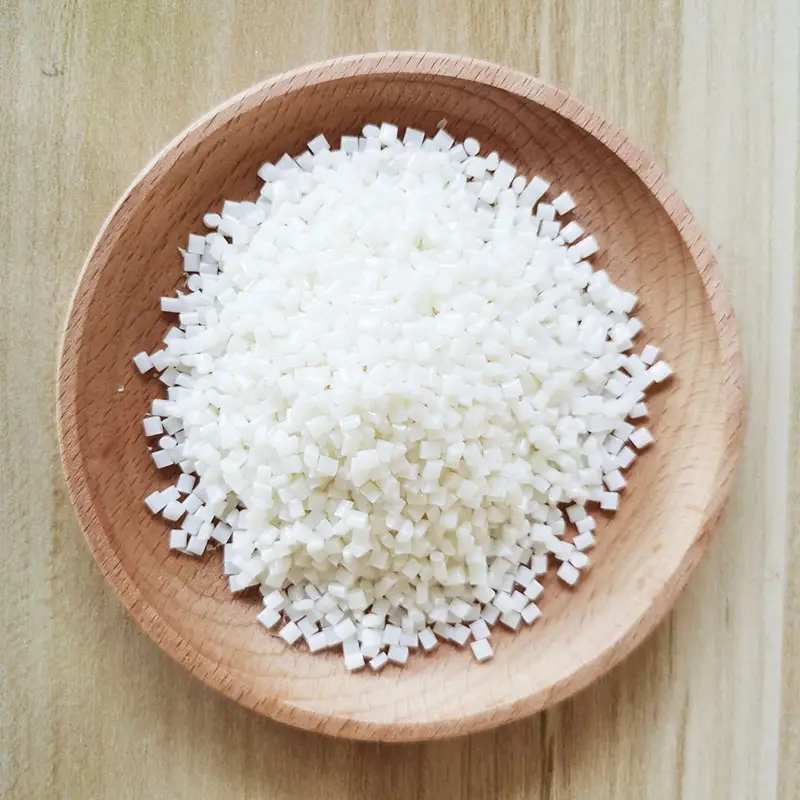
Also known as PC, it is a food-safe plastic resin occasionally used in the production of beverage containers. The most common uses are water-cooler bottles, baby bottles, sippy cups, reusable water containers, and the like. It’s prized for its clarity and especially durable plastic.
PC resin received a lot of scrutiny in the past, as many believed it was not food-safe because of certain components — especially BPA. The widely used substances were subject to extensive testing which showed that their constituents were consumed in extremely low quantities, and doing so posed no health risks.
Polystyrene (PS)

Polystyrene (PS) is a transparent, solid, and brittle polymer. It can be foamed into the plastic most of us know about or poured into molds to create a solid form. As foam, it’s a common material for disposable plastic cups, food trays, and fast food containers. In its solid state, it can be used to produce food containers and lids, egg cartons, and hot cups.
Like the other food-grade plastic resins on this list, PS is recyclable. This is recommended for plastic injection molding manufacturers because PS takes a long time to biodegrade.
How to Select Food-Grade Plastic Resin
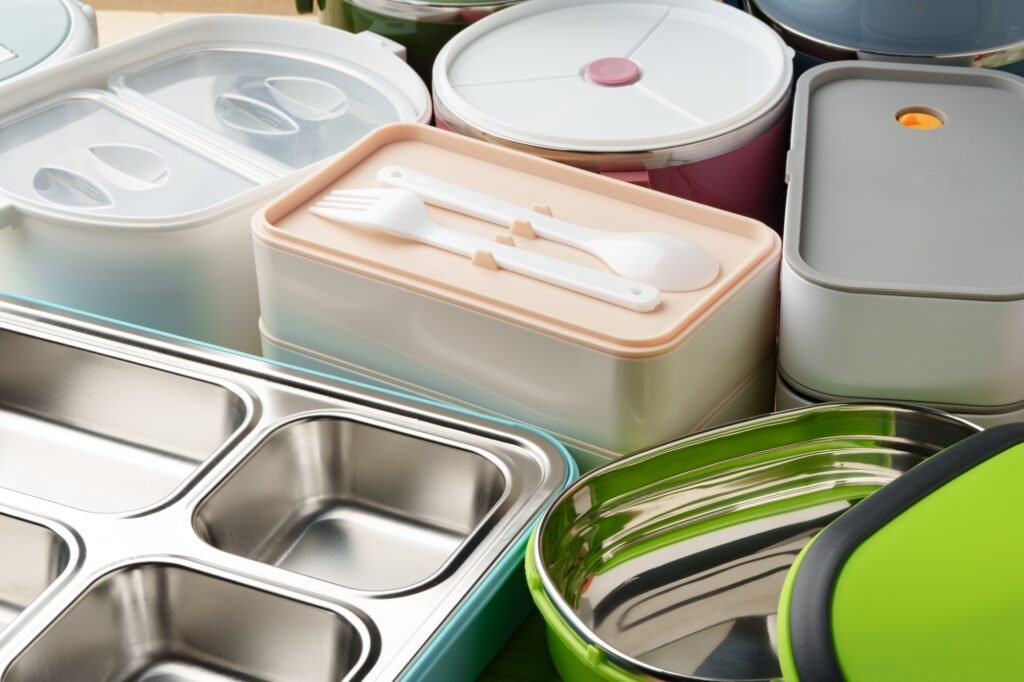
Here are some factors to consider when choosing a food-grade plastic for your application:
- Intended Use: Will the plastic contain hot food or cold? Is it meant to store things for a long term or be thrown away?
- Freshness and Safety: Ensure the chosen material meets relevant FDA or EU standards.
- Material Stability and Thermal Cycling: Choose plastics that possess environmental stress tolerance, like moisture or heat.
- Environmental Impact: If you can, choose recyclable or environmentally friendly plastics.
- Budget: Select materials that satisfy your budget constraints and production needs.
Top 10 FAQs About Food-Grade Plastic
1. What defines “food-grade plastic,” and how does it differ from regular plastic?
Food-grade plastics are certified to meet strict safety standards (e.g., FDA 21 CFR, EU 10/2011) for direct food contact. Unlike regular plastics, they resist leaching harmful chemicals, withstand repeated cleaning, and avoid additives like BPA or phthalates.
2. Which plastics are FDA-approved for food contact?
Common FDA-compliant plastics include:
- Polypropylene (PP): Microwave-safe containers.
- High-Density Polyethylene (HDPE): Milk jugs, cutting boards.
- PET: Beverage bottles.
- Silicone: Baking molds, utensils.
3. What certifications should a food-grade plastic supplier have?
Verify FDA compliance, EU 10/2011, NSF/ANSI 51, and ISO 22000 (food safety management). For global markets, check LFGB (Germany) or JHOSPA (Japan).
4. How do I ensure food-grade plastics won’t leach chemicals into products?
Suppliers must provide:
- Migration test reports (e.g., overall migration limit ≤10 mg/dm² in EU).
- Resin certifications confirm no harmful additives.
- Temperature resistance data (e.g., PP safe up to 120°C).
5. Can food-grade plastics be used in high-temperature applications?
- PP: Safe up to 120°C (short-term).
- Silicone: Withstands -40°C to 230°C.
- PEEK: For extreme heat (250°C+) in industrial food processing.
6. Are colored or recycled food-grade plastics safe?
- Colored plastics: Safe if dyes are FDA-approved and non-migrating.
- Recycled plastics: Must meet FDA 21 CFR 177.1520 for food-contact recycled PET/HDPE. Avoid post-consumer resins for high-risk applications.
7. What are the cost differences between food-grade and standard plastics?
Food-grade plastics cost 10–30% more due to:
- Higher purity resins.
- Compliance testing (e.g., heavy metal screening).
- Certifications and audits.
8. How do I verify a supplier’s food-grade claims?
- Request Certificate of Analysis (CoA) and Material Safety Data Sheets (MSDS).
- Audit their facility for GMP (Good Manufacturing Practices) compliance.
- Check third-party lab test results for migration and toxicity.
9. Can food-grade plastics be recycled or reused safely?
- Recycling: Look for symbols (e.g., PET #1, HDPE #2).
- Reuse: Only if undamaged and cleaned properly (e.g., dishwasher-safe PP). Avoid reusing scratched or warped containers.
10. What design considerations ensure compliance in food-grade plastic products?
- Smooth surfaces: Minimize crevices to prevent bacterial growth.
- Seal integrity: Prevent leaks in packaging (tested via ASTM F2095).
- Durability: Ensure resistance to detergents and abrasion (e.g., NSF 51 for food equipment).
Summary
First of all, food-contact plastic resins are the raw material which is responsible for the manufacturing of food-grade products. PET, HDPE, PP, LDPE, and more have certain properties that make them ideal for food storage, packaging, and transportation. Regulating the materials helps ensure not just maintaining product quality but also providing information on the chemical structures of the chosen materials and their safety, which, therefore, would protect consumers as well.
So, there you have it. These six materials are the most used food-grade plastics resins in the food and beverage industry. All of them have their suggested use and benefits to keep in mind.
About BFY Mold
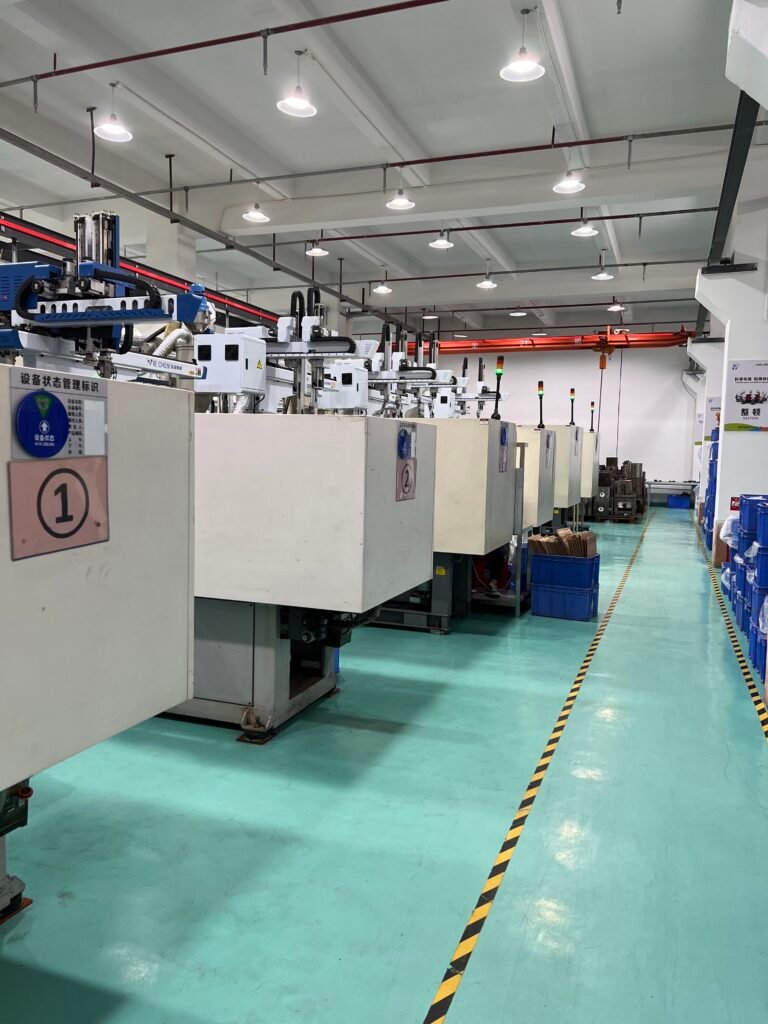
Injection Molding & Mold Manufacturer | BFY MOLD We have the best experience in fields such as mass production, on-demand production, CNC, and mirror spark processing. We have their very own high-end inventor, which creates all of their very own projects. From custom molds to large-scale production, BFY Mold is your trusted partner for outstanding results.
Contact us today to learn how BFY Mold can help you turn your food-grade plastic ideas into reality!