What Is Polyethylene?
Polyethylene (PE) is not only the most widely used plastic in the world but also accounts for 34% of global plastics production. Polyethylene is made from ethylene monomer (C₂H₄), which has a simple molecular structure and is widely used in various industries. There are three main types:
- Low-Density Polyethylene (LDPE): Flexible and translucent.
- High-Density Polyethylene (HDPE): Strong and chemically resistant, used for milk cans and fuel tanks.
- Linear Low-Density Polyethylene (LLDPE): known for its flexibility and toughness, used in stretch film.
Backstory: Discovered by Imperial Chemical Industries (ICI) in 1933, polyethylene quickly changed how it was packaged and produced; it was inexpensive and easy to mold into any shape.
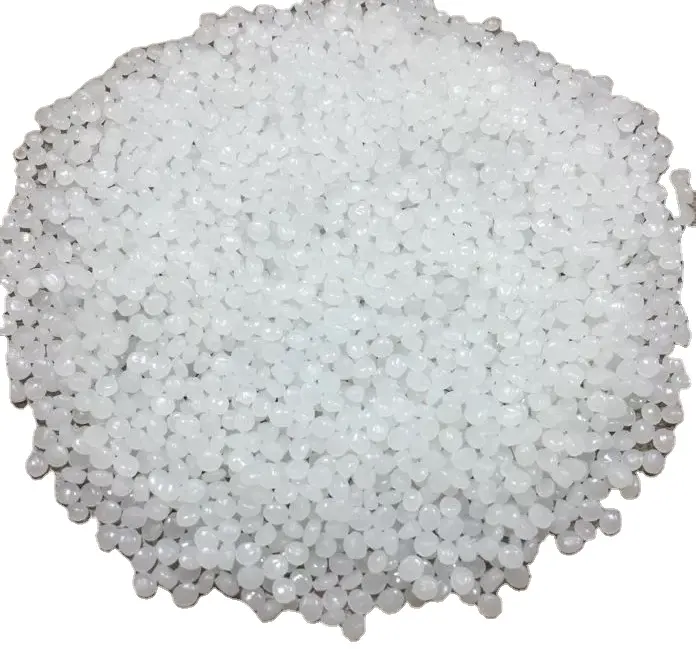
Composition and Molecular Structure
PE’s properties hinge on its branching and crystallinity:
Type | Branching | Crystallinity (%) | Applications |
LDPE | High branching | 40–50 | Plastic wraps, tubing |
HDPE | Minimal branching | 70–85 | Pipes, automotive parts |
LLDPE | Short branches | 50–60 | Agricultural films, lids |
Science Deep Dive:
Polymerization Methods:
- High-Pressure Process (LDPE): Ethylene polymerizes under 1,000–3,000 atm, creating branched chains.
- Ziegler-Natta Catalysis (HDPE): Low-pressure process yields linear chains with higher tensile strength.
Manufacturing Safety of Polyethylene Plastic
PE production uses extreme conditions to polymerize ethylene gas. Safety protocols are a must:
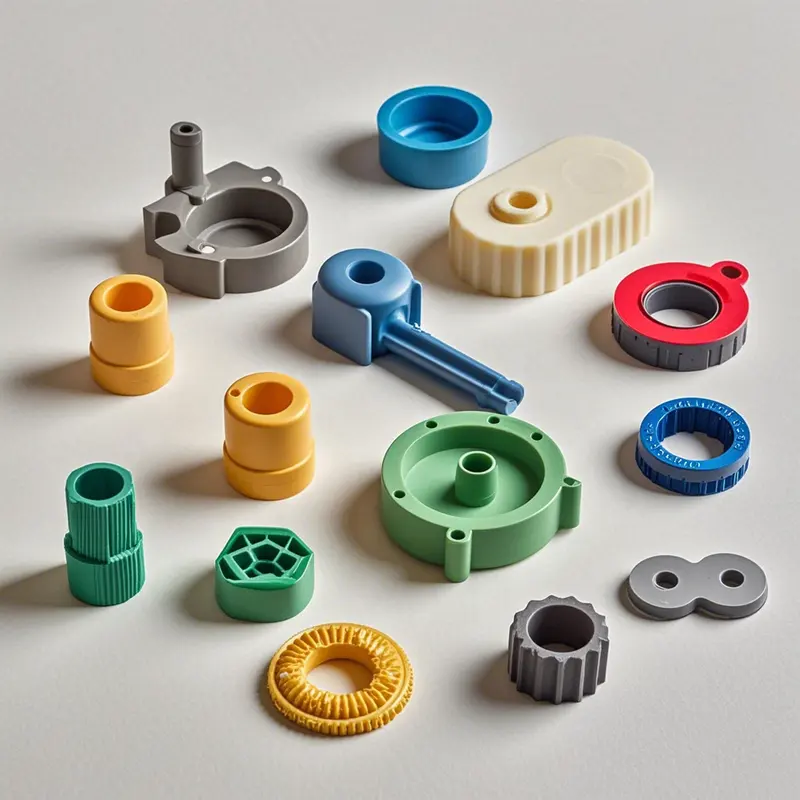
1. Ethylene Gas Handling:
- OSHA PEL: 200 ppm (parts per million) for 8 hours
- Flammability range: 2.7-36% in the air (NFPA standard).
2. Additive Safety:
- Antioxidants: Irganox 1010 (phenolic) heat degradable
- UV Stabilizers: Light stabilizers (e.g., Chimassorb 944) protect against degradation from sunlight.
Case Study: A Louisiana plant used IoT gas sensors and automated shutoff valves to cut ethylene leaks by 75%.
Is Polyethylene Safe for Food?
FDA Compliance:
- HDPE: Compliant under 21 CFR 177.1520 for food containers, including repeated-use items.
- LDPE: Approved for food wraps (21 CFR 177.1520), but avoid temperatures >70°C.

Critical Tests for Food-Grade PE:
- Migration Testing: Ensures additives (e.g., slip agents) don’t leach into food.
- Heavy Metal Screening: Limits lead (<0.1 ppm) and cadmium (<0.01 ppm).
Human Health Risks of Polyethylene
While PE itself is inert, risks arise from additives and environmental degradation:
1. Microplastics:
- PE contributes 23% of ocean microplastics
- Ingestion is linked to inflammation in marine life; human impacts are under study.
2. Additive Hazards:
- Phthalates: Banned in food-contact PE but found in older products.
- BPA Alternatives: Newer HDPE uses non-estrogenic stabilizers like Tris(nonylphenyl) phosphite.
3. Safety Certifications:
- USP Class VI: For medical-grade PE (biocompatibility).
- NSF/ANSI 61: Certifies PE for potable water systems.
Polyethylene in Cosmetics: Skin Safety
PE is widely used in exfoliants and creams, but regulations vary:
- Microbead Ban: The 2015 U.S. Microbead-Free Waters Act prohibits PE microbeads in rinse-off cosmetics.
Current Uses:
- Non-Rinse Products: Lipsticks and lotions may still contain PE.
- Particle Size: Particles >5µm are considered non-penetrating.
Alternatives:
- Jojoba beads, rice bran, and silica are safer exfoliants.
Recycling Polyethylene: Processes and Challenges
Mechanical Recycling:
- Collection & Sorting: NIR sensors separate LDPE (#4) and HDPE (#2).
- Washing & Pelletizing: Removes contaminants (food residues, adhesives).
Chemical Recycling:
- Pyrolysis: Breaks PE into hydrocarbons for fuel (60–70% yield).
- Depolymerization: Converts PE back to ethylene (emerging tech, <10% commercial use).
U.S. Recycling Rates
Type | Recycling Rate | Major Applications |
HDPE | 32% | Bottles, pipes |
LDPE | 9% | Films, bags |
Is Recycled Polyethylene Safe?
FDA Standards for Recycled PE:
- Post-Consumer Resin (PCR): Must pass FDA’s “challenge test” simulating worst-case extraction.
Contaminant Limits:
- Heavy metals: <1 ppm
- Microbial counts: <100 CFU/g
Case Study: BFY Mold’s PCR HDPE meets FDA standards for food trays, achieving <0.5 ppm contaminants.
Polyethylene vs. Other Plastics: Safety and Performance
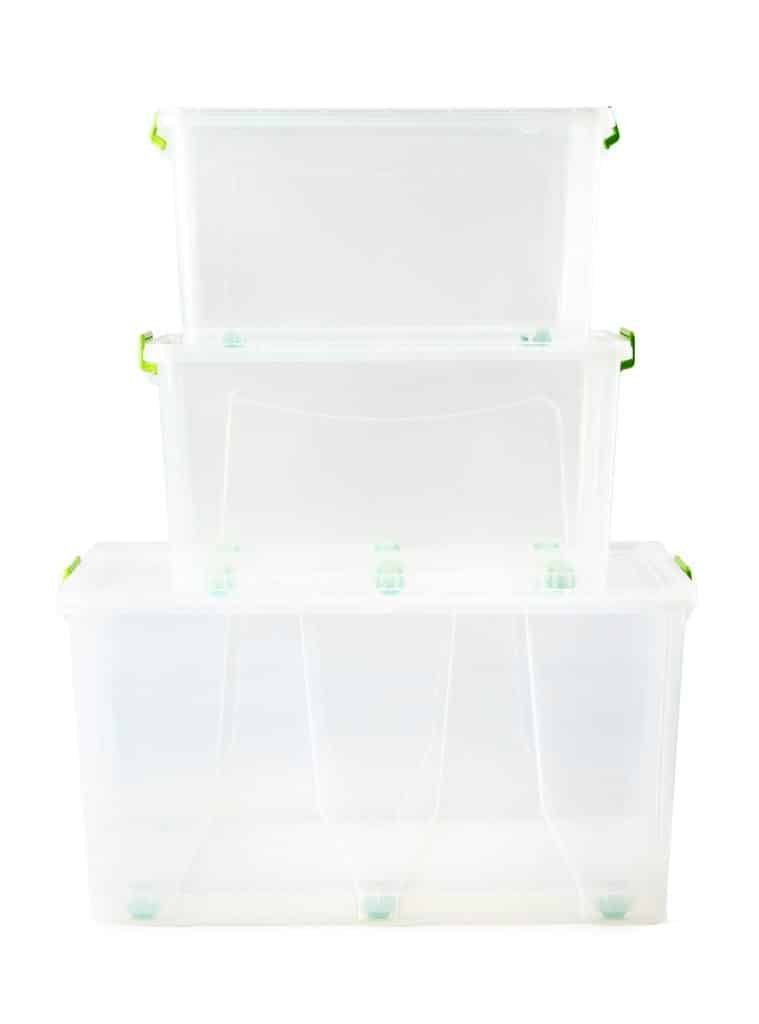
Plastic | Safety | Heat Resistance | Recyclability | Common Uses |
HDPE | High (FDA) | 120°C | High (#2) | Fuel tanks, bottles |
PVC | Low (phthalates) | 70°C | Low (#3) | Pipes, cables |
PET | Moderate (antimony) | 85°C | High (#1) | Water bottles |
PP | High (FDA) | 135°C | Moderate (#5) | Food containers |
Key Takeaway: HDPE outperforms PVC/PET in safety and thermal stability.
Polyethylene in Injection Molding: Industry Innovations
Applications:
- Automotive: HDPE fuel tanks resist hydrocarbons and reduce weight by 30% vs. steel.
- Medical: Sterilizable HDPE trays withstand 1,000+ autoclave cycles.
- Consumer Goods: LLDPE trash bins with UV inhibitors for outdoor use.

Advanced Techniques:
- Gas-Assisted Molding: Creates hollow HDPE parts (e.g., chair bases) with 25% material savings.
- In-Mold Labeling (IML): Embeds recycled PE labels directly into products.
Case Study: BFY Mold’s HDPE automotive panel reduced part weight by 22%, cutting CO2 emissions by 15% per vehicle.
Regulatory Landscape in the U.S.
1. Food Contact Regulations:
- FDA 21 CFR 177.1520: Specifies extractable limits for PE food packaging.
- California Proposition 65: Requires warnings if PE contains listed carcinogens.
2. Environmental Policies:
- Extended Producer Responsibility (EPR): Mandates PE producers fund recycling in 5 states.
- Recycled Content Laws: California requires 15% PCR in plastic bottles by 2025.
Future Trends in Polyethylene Use
1. Bio-Based PE:
- Derived from sugarcane (e.g., Braskem’s Green PE), reducing carbon footprint by 70%.
- Current Cost: 20–30% higher than fossil-based PE.
2. Smart Packaging:
- PE films embedded with RFID tags for supply chain tracking.
3. Chemical Recycling Expansion:
- Companies like Brightmark aim to recycle 100k tons of PE annually by 2025.
Conclusion
Polyethylene remains indispensable in manufacturing due to its adaptability, FDA compliance, and recyclability. For U.S. manufacturers, prioritizing HDPE and certified recycled PE aligns with sustainability goals while mitigating health risks. Rigorous adherence to FDA protocols and investment in advanced recycling technologies will drive long-term competitiveness.