Introduction to Plastic Molding
Plastic molding transforms polymer materials into functional components through various manufacturing techniques. At BFY Mold, we specialize in eight core processes that serve industries ranging from medical devices to automotive manufacturing. This comprehensive guide examines each method’s technical parameters, ideal applications, and economic considerations to help you select the plastic molding services.

1. Injection Molding: The High-Precision Workhorse
Process Details
- Material Preparation: Drying (2-4 hours at 80°C for hygroscopic resins)
- Melting Phase: Screw rotation at 150-400°C (material-dependent)
- Injection: 50-200MPa pressure into steel/aluminum molds
- Cooling: 15-60 seconds (depends on wall thickness)
- Ejection: Automated robotic removal
Technical Specifications
Parameter | Range | Industry Standard |
Cycle Time | 15-120 seconds | ISO 294 |
Dimensional Tol. | ±0.005-0.05mm | ASME Y14.5 |
Mold Life | 500k-1M cycles | SPI CLASS 101-104 |
Applications:
- Medical: Surgical instrument housings (ISO 13485 compliant)
- Automotive: Interior trim components (IATF 16949 certified)
- Electronics: Connector housings with 0.2mm wall thickness
Advantages:
- High repeatability (CpK >1.67 achievable)
- Complex geometries possible
- Multi-material options through co-injection
Limitations:
- High initial tooling investment ($15k-$250k)
- Limited economic viability below 1,000 units
2. Extrusion Molding: Continuous Profile Production
Process Breakdown
- Feeding: Granules enter barrel at controlled rate
- Plastication: Single-screw melting at 150-275°C
- Die Formation: Shape determined by tool geometry
- Cooling: Calibration tables with vacuum sizing
- Cutting: Flying saws for length control
Key Performance Metrics
Output Type | Speed Range | Tolerance |
Pipe/Tubing | 2-10 m/min | ±0.1% diameter |
Sheet/Film | 5-50 m/min | ±5% thickness |
Profile | 1-5 m/min | ±0.2mm cross-section |
Material Considerations:
- PVC: 60% of extrusion applications
- HDPE: For pressure pipes (PN10-PN25 ratings)
- TPE: Soft-touch profiles
BFY Mold Case Study: Produced 12km/month of medical tubing with consistent ±0.05mm ID control.
3. Blow Molding: Hollow Part Manufacturing
Process Variations
Extrusion Blow Molding
- Parison extrusion
- Mold closure
- Air inflation (0.3-0.7MPa)
- Cooling (30-90 seconds)
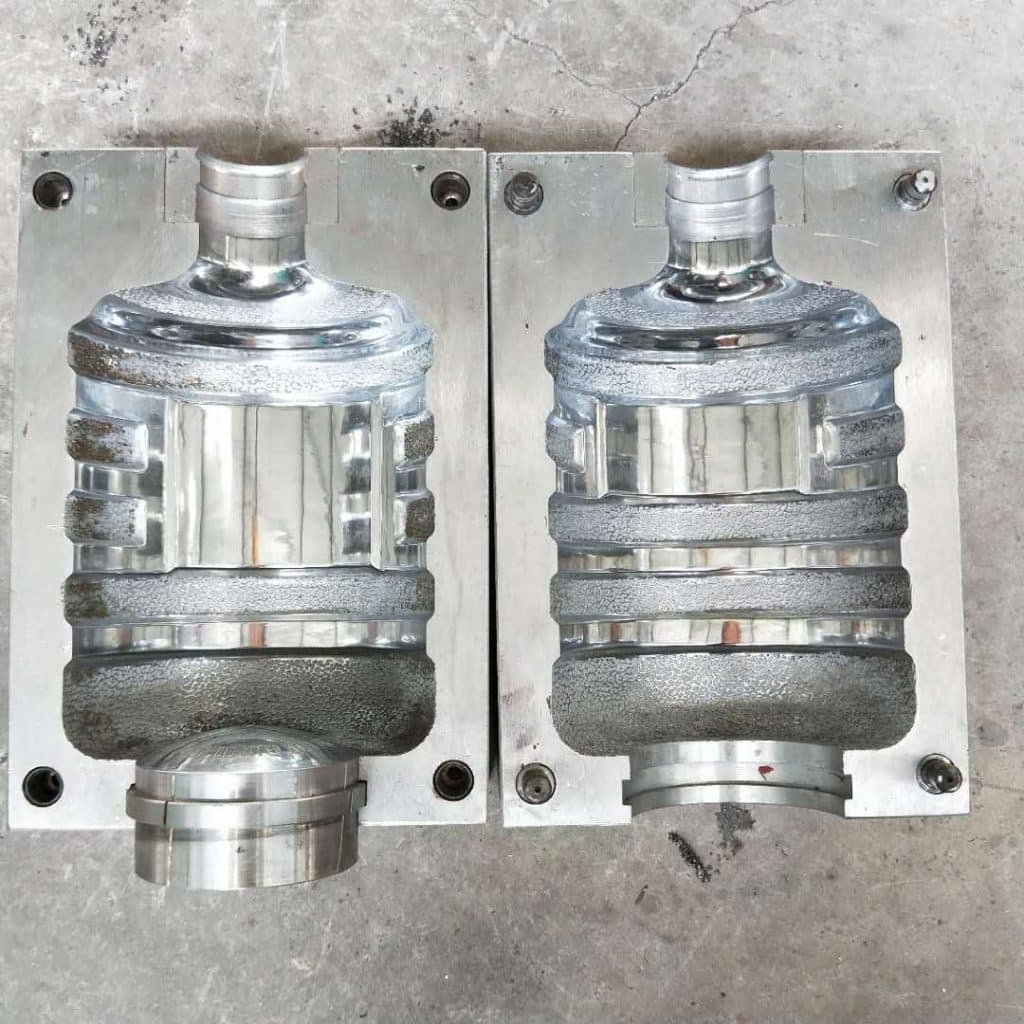
Injection Blow Molding
- Preform injection
- Transfer to blow station
- Stretch-blow orientation
Comparative Analysis
Factor | Extrusion BM | Injection BM |
Wall Control | ±15% | ±8% |
Neck Finish | Requires trimming | Injection-quality |
Output Rate | 200-500/hr | 100-300/hr |
Material Selection Guide:
- PET: Carbonated drink bottles
- HDPE: Chemical containers
- PP: Automotive ducting
4. Rotational Molding: Large, Seamless Components
Process Timeline
- Loading: Powder measured into mold (±1% accuracy)
- Heating: 300°C oven with biaxial rotation (6-12 RPM)
- Cooling: Water spray + air cooling phases
- Unloading: Manual/automated part removal
Design Parameters
Part Size | Mold Weight | Cycle Time |
<1m³ | 50-200kg | 20-40 minutes |
1-5m³ | 200-800kg | 40-90 minutes |
>5m³ | 800-3000kg | 2-4 hours |
Material Options:
- Polyethylene (90% of applications)
- Nylon (for fuel tanks)
- PVC (playground equipment)
5. Thermoforming: Thin-Walled Packaging Solutions
Process Flow
- Sheet Feeding: Roll-to-roll or cut sheets
- Heating: Infrared panels (150-200°C)
- Forming: Vacuum (0.5-0.9 bar) or pressure (3-6 bar)
- Trimming: Steel-rule dies or CNC routers
Quality Control Metrics
Defect Type | Prevention Method | Measurement Tool |
Webbing | Optimal prestretching | 3D laser scanner |
Thin spots | Pressure monitoring | Ultrasonic thickness gauge |
Dimensional warpage | Controlled cooling rate | CMM |
6. Compression Molding: Thermoset Specialization
Technical Sequence
- Preform Preparation: SMC/BMC cutting
- Mold Loading: 80-120°C preheat
- Curing: 100-200kg/cm² for 2-15 minutes
- Post-Cure: 1-4 hours at 150°C (optional)
Material Properties
Composite Type | Fiber Content | Strength (MPa) |
SMC | 25-30% glass | 80-120 |
BMC | 15-25% glass | 40-70 |
GMT | 30-40% glass | 100-150 |
7. Structural Foam Molding: Lightweighting Solution
Process Characteristics
- Weight Reduction: 15-30% vs solid parts
- Surface Finish: Class B SPI (textured)
- Dimensional Stability: ±0.3% after 24hrs
Equipment Requirements
Part Size | Clamp Force | Gas Injection System |
<5kg | 50-100 tons | Nitrogen |
5-20kg | 100-300 tons | Chemical blowing agent |
>20kg | 300-600 tons | Hybrid system |
8. Insert Molding: Hybrid Component Fabrication
Design Guidelines
- Insert Materials: Stainless steel, brass, ceramics
- Plastic Selection: PPS for high-temp, PEEK for chemical resistance
- Bonding Methods: Mechanical interlocks preferred over adhesives
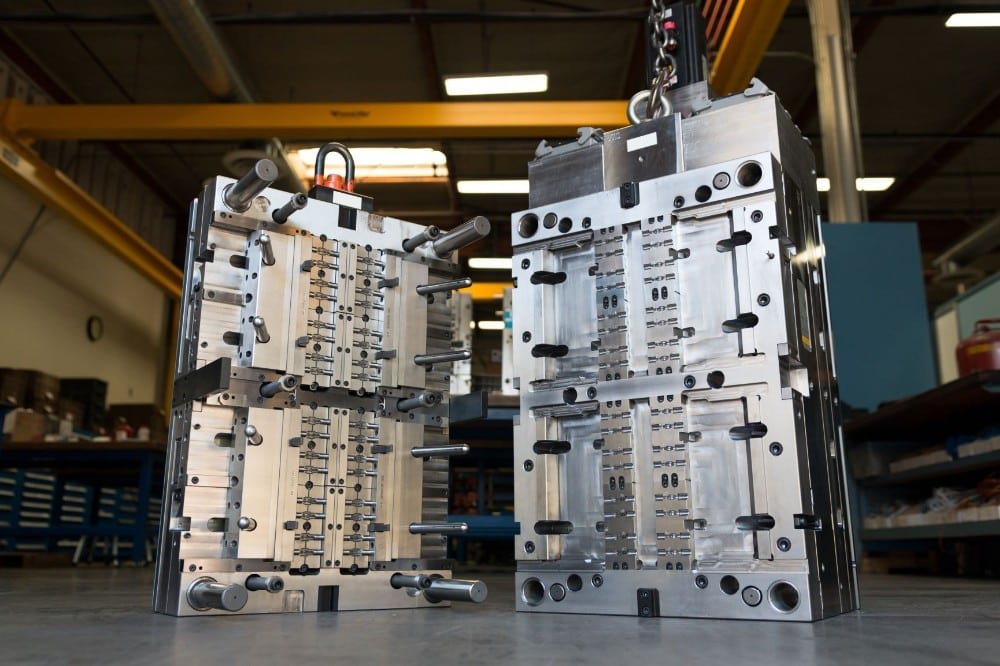
Quality Standards
- Pull Test Requirements: 50N minimum for medical devices
- Electrical Continuity: <0.5Ω resistance for connectors
- Hermetic Sealing: Helium leak test <1×10^-6 mbar·L/s
Comparative Process Selection Matrix
Process | Economic Volume | Tooling Lead Time | Material Options | Dimensional Accuracy |
Injection | 10k+ | 4-8 weeks | 200+ | ±0.005mm |
Extrusion | Continuous | 2-4 weeks | 30 | ±0.1mm |
Blow | 5k+ | 6-10 weeks | 15 | ±0.2mm |
Rotational | 500+ | 3-5 weeks | 10 | ±0.5mm |
10 Expert FAQs About Plastic Molding Services
Q1: How to choose between injection and compression molding?
A: Injection for thermoplastics (more than 1,000 units), compression for thermosets/composites.
Q2: What’s the minimum wall thickness for PE extrusion?
A: 0.1mm for films, 0.5mm for profiles.
Q3: Can blow molding achieve undercuts?
A: Limited to 5° draft angles without collapsible cores.
Q4: How to reduce sink marks in thick ribs?
A: Maintain rib-to-wall ratio ≤60% and use gas-assist.
Q5: What surface finish is possible with rotational molding?
A: Typically SPI C-1 to D-3, with texture replication up to 90%.
Q6: How accurate is thermoforming vs injection molding?
A: ±0.2mm vs ±0.05mm on critical dimensions.
Q7: Which process allows the fastest material changeovers?
A: Thermoforming (15-30 minutes between materials).
Q8: What’s the largest part possible with structural foam?
A: Up to 4m×2.5m×1m with 600-ton presses.
Q9: How to validate insert molding bond strength?
A: ASTM D4541 pull-off testing at 23°C and 85°C.
Q10: Why partner with BFY Mold for plastic molding services?
- 50+ molding systems from 5-600 tons
- In-house tooling with 25-day average lead time
- Material science lab for formulation testing