Introduction
This guide covers six essential types of waterway channels for plastic molds, providing insights into their design and functionality. Understanding these designs can significantly impact your molding process, ensuring optimal cooling and material flow. Dive into our comprehensive waterway channels for plastic molds guide to enhance your manufacturing practices and product outcomes.
Plastic molding is a pivotal process in manufacturing, used extensively in producing various plastic products ranging from everyday household items to complex industrial components. One of the critical aspects of plastic molding is temperature control, achieved primarily through water channels within the mold. These channels ensure that the mold remains at a consistent temperature, essential for producing high-quality parts. The design of these water channels, or water lines, is crucial as it impacts the cooling efficiency, cycle time, and overall quality of the molded parts.
1. Straight Line Water Channels
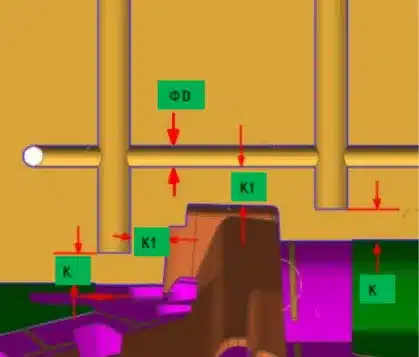
Straight-line water channels are the most basic type of cooling system used in plastic molds. They consist of simple, straight passages drilled into the mold, allowing water to flow directly from the inlet to the outlet.
Functionality
- Design: Simple and easy to implement.
- Efficiency: Limited cooling efficiency due to uniform distance from the mold surface.
- Application: Suitable for parts with simple geometries and where uniform cooling is sufficient.
Advantages
- Cost-effective and easy to manufacture.
- Minimal complexity in design and maintenance.
Disadvantages
- Inefficient for complex parts with varying thicknesses.
- Potential for uneven cooling and longer cycle times.
2. Conformal Cooling Channels
Conformal cooling channels follow the contours of the molded part, providing uniform cooling throughout the mold. These channels are often created using advanced manufacturing techniques such as 3D printing.

Functionality
- Design: Complex, customized to the part’s geometry.
- Efficiency: High cooling efficiency with reduced cycle times.
- Application: Ideal for intricate parts with complex geometries and varying wall thicknesses.
Advantages
- Provides uniform cooling, reducing warpage and improving part quality.
- Reduces cycle times significantly.
Disadvantages
- Expensive and complex to design and manufacture.
- Requires advanced manufacturing techniques and equipment.
3. Baffle and Bubbler Systems
Baffles and bubblers are used in areas where straight-line cooling channels are insufficient. Baffles are thin, flat pieces inserted into the water channels to direct the flow of water, while bubblers are small tubes that introduce water directly into the mold cavity.
Functionality
- Design: Incorporates additional components like baffles or bubblers within the mold.
- Efficiency: Enhanced cooling in specific areas of the mold.
- Application: Used in molds with deep or complex cavities where uniform cooling is challenging.
Advantages
- Improves cooling in hard-to-reach areas.
- Can be used in conjunction with other cooling methods for optimal results.
Disadvantages
- Increases the complexity and cost of the mold.
- Requires precise placement and design to be effective.
4. Spiral Water Channels
Spiral water channels wrap around the core or cavity of the mold, providing a large surface area for heat exchange.
Functionality
- Design: Spiral configuration around the mold components.
- Efficiency: Offers excellent cooling efficiency due to increased surface contact.
- Application: Suitable for cylindrical or conical parts.
Advantages
- Maximizes cooling efficiency by increasing surface contact.
- Can be designed to match the shape of the molded part.
Disadvantages
- More complex to design and implement compared to straight channels.
- Higher manufacturing cost due to intricate channel design.
5. Helical Water Channels
Helical water channels are similar to spiral channels but are designed in a helical pattern, often used in molds with cylindrical shapes.
Functionality
- Design: Helical pattern around the core or cavity.
- Efficiency: Provides even cooling with a large surface area.
- Application: Ideal for long, cylindrical parts like pipes or bottles.
Advantages
- Effective for long parts where uniform cooling is required.
- Reduces cycle times by enhancing heat exchange.
Disadvantages
- Complex design and manufacturing process.
- Higher initial costs.
6. Cascade Water Channels
Cascade water channels use a series of stepped channels that allow water to flow in a cascading manner, providing cooling in stages.
Functionality
- Design: Stepped channels that guide water flow in stages.
- Efficiency: Good for parts with varying thicknesses.
- Application: Used for molds where gradual cooling is beneficial.
Advantages
- Can handle parts with varying geometries effectively.
- Reduces the risk of thermal shock to the molded part.
Disadvantages
- More complex and costly to design.
- Requires careful planning and design to ensure effective cooling.
Conclusion
Effective cooling is critical in plastic molding as it directly affects the quality and efficiency of the production process. Each type of water channel design has its unique advantages and limitations, making it suitable for different applications and part geometries. Straight-line channels are simple and cost-effective, while conformal channels offer high efficiency for complex parts. Baffle and bubbler systems enhance cooling in specific areas, spiral, and helical channels provide excellent surface contact for cylindrical parts, and cascade channels are ideal for parts with varying thicknesses. The choice of water channel design is thus a critical decision in the mold design process, requiring careful consideration of the part geometry, production volume, and cost constraints.