Selecting the right material for CNC machining is a critical step that can significantly impact the final product’s quality, functionality, and cost. With a wide range of materials available, understanding their properties and applications is essential to make an informed decision. This guide will help you choose the most suitable material for your CNC machining project.
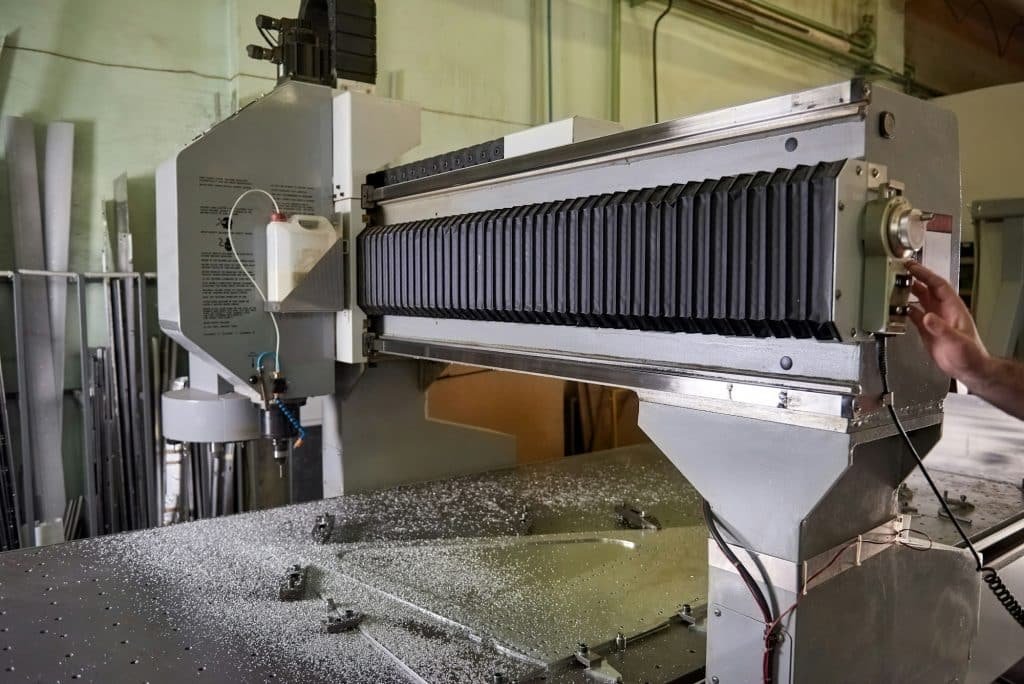
Understanding Material Properties
When selecting a material for CNC machining, consider the following properties to ensure it meets the requirements of your project:
- Strength and Hardness: These properties determine how well the material can withstand mechanical stresses. High-strength materials like steel and titanium are ideal for heavy-duty applications, while softer materials like aluminum are suitable for lightweight and moderate-stress components.
- Machinability refers to how easily a material can be cut, shaped, and finished. Materials like aluminum and brass have excellent machinability, making them popular choices for CNC machining.
- Thermal Stability: Materials must maintain their properties under varying temperatures. For high-temperature applications, materials like stainless steel or titanium are preferred.
- Corrosion Resistance: For applications exposed to harsh environments or chemicals, materials like stainless steel, titanium, and certain plastics offer excellent corrosion resistance.
- Weight: The weight of the material can affect the performance and efficiency of the final product. Lightweight materials like aluminum and certain plastics are ideal for aerospace and automotive components.
- Cost: Balancing material performance with cost is crucial. While high-performance materials offer superior properties, they can also be more expensive.
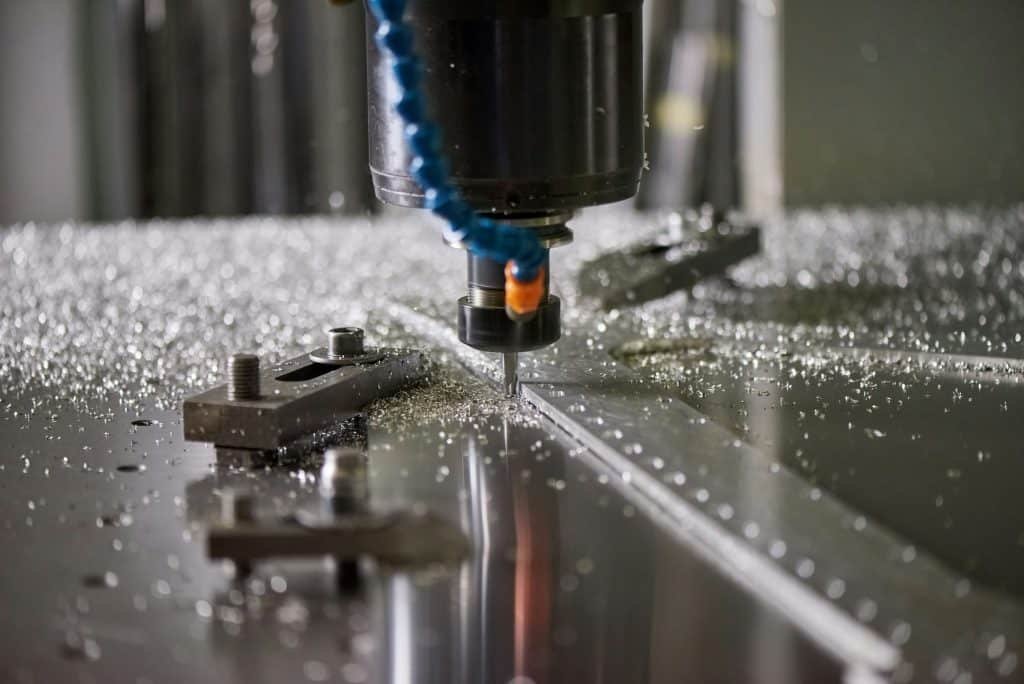
Common CNC Machining Materials
Here are some commonly used materials in CNC machining, along with their properties and typical applications:
- Aluminum:
- Properties: Lightweight, excellent machinability, good strength-to-weight ratio, and corrosion resistance.
- Applications: Aerospace components, automotive parts, consumer electronics, and prototypes.
- Steel:
- Properties: High strength, durability, and versatility. Available in various grades, including carbon steel and stainless steel.
- Applications: Structural components, machinery parts, tools, and medical devices.
- Brass:
- Properties: Good machinability, corrosion resistance, and electrical conductivity.
- Applications: Electrical connectors, plumbing fittings, and decorative hardware.
- Titanium:
- Properties: High strength-to-weight ratio, excellent corrosion resistance, and biocompatibility.
- Applications: Aerospace components, medical implants, and high-performance automotive parts.
- Plastics:
- Properties: Lightweight, corrosion-resistant, and versatile in terms of mechanical properties. Common types include ABS, nylon, and PEEK.
- Applications: Consumer products, medical devices, and lightweight structural components.
- Copper:
- Properties: Excellent electrical and thermal conductivity, good machinability, and corrosion resistance.
- Applications: Electrical components, heat exchangers, and plumbing.
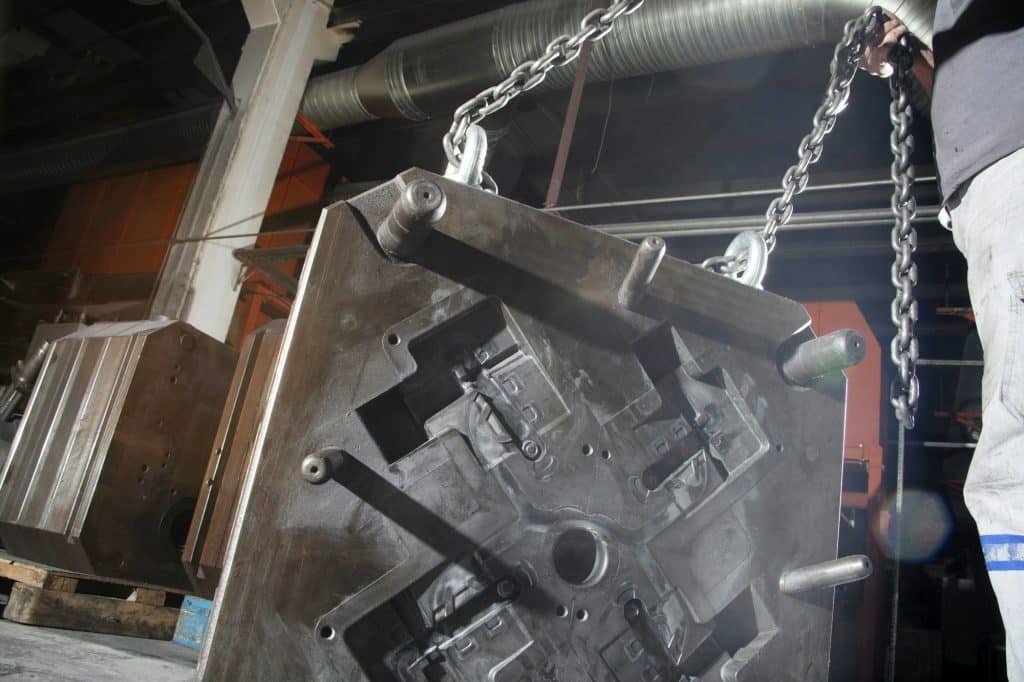
Factors to Consider When Choosing a Material
- Application Requirements: Understand the specific demands of your application, including mechanical stresses, environmental conditions, and regulatory standards.
- Material Availability: Ensure the chosen material is readily available and can be sourced in the required quantities.
- Compatibility with CNC Processes: Some materials are more suited to CNC machining than others. Consider the compatibility of the material with your CNC equipment and processes.
- Surface Finish Requirements: Different materials offer varying surface finishes. Consider the aesthetic and functional requirements of the final product.
- Post-Machining Treatments: Some materials may require additional treatments, such as heat treatment or surface coating, to achieve desired properties.
Tips for Material Selection
- Consult with Experts: Work with material scientists or experienced machinists to get recommendations tailored to your project needs.
- Prototype Testing: If possible, create prototypes with different materials to test their performance in real-world conditions.
- Cost-Benefit Analysis: Weigh the benefits of high-performance materials against their costs to find a balanced solution.
- Stay Updated: Keep abreast of new materials and advancements in CNC machining technology that could offer better solutions for your projects.

10 Supplier-Centric FAQs for CNC Material Selection
1. What certifications distinguish high-quality CNC material suppliers?
Trusted suppliers hold ISO 9001 (quality management), AS9100 (aerospace), and ISO 13485 (medical). For precision-critical projects, ensure they have NADCAP accreditation for specialized processes like heat treatment.
2. How do suppliers ensure material traceability in CNC machining?
Reputable providers supply Mill Test Reports (MTRs) with batch-specific data, including chemical composition and mechanical properties, aligned with ASTM or EN standards.
3. Which materials balance cost and performance for prototyping?
- Aluminum 6061: $20–40/kg, ideal for structural testing
- POM (Delrin): $5–10/kg, replaces costly PEEK in non-critical applications
- Stainless Steel 304: $25–50/kg, corrosion-resistant for industrial parts
4. How do top suppliers reduce CNC material waste?
Advanced vendors use AI-powered nesting software to optimize raw material usage, achieving 92–95% efficiency compared to traditional methods.
5. What sustainable materials meet eco-friendly CNC requirements?
- Recycled Aluminum: 70%+ post-industrial content
- Bio-Based Plastics: Renewably sourced resins like PA11
- Dry Machining Alloys: Eliminate coolant use for cleaner production
6. What tolerances can suppliers achieve with different materials?
Material | Standard Tolerance | Precision Capability |
Aluminum 6061 | ±0.05 mm | ±0.01 mm (5-axis) |
Titanium Grade 5 | ±0.03 mm | ±0.005 mm (Swiss CNC) |
7. How to verify supplier claims about material properties?
Request third-party test reports covering:
- Tensile strength (ASTM E8)
- Hardness (Rockwell B/C scales)
- Surface roughness (Ra/Rz measurements)
8. Which materials support both prototyping and full production?
- 17-4PH Stainless Steel: Pre-hardened state reduces post-processing
- PEI (Ultem): Maintains performance from prototypes to 10,000+ units
- Tool Steel D2: Direct transition to injection mold tooling
9. What industry-specific materials do specialized suppliers offer?
- Medical: ASTM F136-compliant titanium for implants
- Automotive: AMS 2750-certified alloys for engine components
- Electronics: ESD-safe plastics like LDPE for circuitry housings
10. How do lead times vary between CNC material suppliers?
- Standard Metals: 3–5 days (domestic stock)
- Exotic Alloys: 2–3 weeks (global sourcing)
- Plastics: 48 hours (in-house inventory)
Conclusion
Choosing the right material for your CNC machining project is a crucial step that can influence the success of the final product. By considering factors such as strength, machinability, thermal stability, and cost, you can make informed decisions that align with your project requirements.

About BFY Mold
BFY Mold is a leading provider of plastic injection molding and mold manufacturing services. With our factory, we offer mass production, on-demand production, CNC machining, and mirror sparking. Our expertise ensures high-quality products tailored to meet your specific needs. Contact us today to learn more about how we can support your manufacturing projects.