1. Low-Pressure Injection Molding Overview
Low-pressure injection molding (LPIM) is a method of molding in which the material is injected into the mold in a low-pressure environment, unlike conventional injection molding. This process is used frequently for encapsulation of electronic components, and fragile elements, and for sealing air and gas.

2. How the Low-Pressure Molding Process Works
Low-pressure molding process Under the low-pressure molding process, thermoplastic materials such as polyamide (PA) are heated up and the molten materials are injected into a cavity. The high-low injection pressure minimizes the stress on the parts, making it one of the best results for delicate parts.
Steps in the Low-Pressure Molding Process:
- Material loading: Thermoplastics are melted in the machine.
- Mold Preparation: Clean and prepare molds, typically with release agents.
- Injection: The molten material is forced into a chamber under controlled pressure.
- Cooling: The component hardens as it cools in the mold.
- Ejection: Ejection is the phase where the molded product is removed.
3. Benefits of Low-Pressure Molding
Gentle Pressures Save Sensitive Parts: Protect the Components
- Reduced Cycle Times: Lower pressure requirement allows for faster cooling.
- Easier to Design Mold: Reduced pressures lead to less rigid molds.
- Sustainable: No more need for secondary encapsulation [Waste reduction]
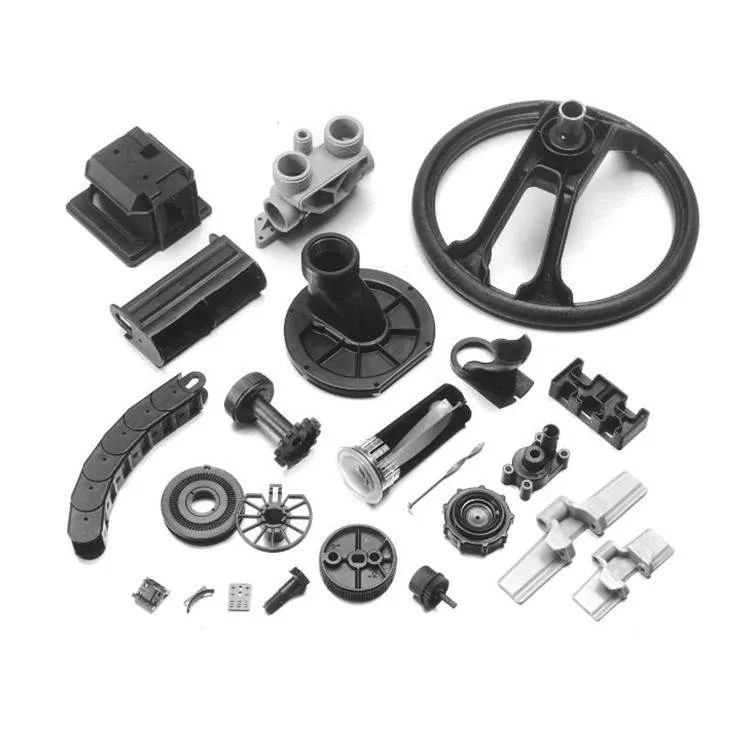
4. Disadvantages of Low-Pressure Molding
Low-pressure molding has advantages, but there are disadvantages:
- Material Restrictions: Not all thermoplastics are suitable, an example being only polyamide.
- Power Facility Cost – Specialized low-pressure materials can drive up costs.
- Low Details Precision: High geometries might not be possible.
5. Use Cases Across Industries
Cold-Element Molding & A variety of Low-Pressure Injection Molding Applications
- Electronics: Sensors, connectors, and circuitry encapsulation.
- Automotive: Covering wiring and delicate electronic components.
- Medical Devices: Sealed, biocompatible parts.
- Consumer Goods: Long-lasting, waterproof components of the appliances.
6. Low-Pressure Molding vs. Traditional Injection Molding
Feature | Low-Pressure Molding | Traditional Injection Molding |
Injection Pressure | Lower | Higher |
Material Compatibility | Limited | Broad |
Applications | Delicate/Encapsulation | Mass Production |
Tooling Cost | Lower | Higher |
Cycle Times | Faster | Slower |
7. Low-Pressure Molding — Things to Think About When Starting Projects
Keep these points in mind when designing a low-pressure molding project:
- Material Selection: Select thermoplastics that are compatible with the application.
- Part Design Because simple parts can lead to simple molds, they also can lead to lower costs.
- Don’t Go Too Complicated – Higher precision is not achieved due to less precision.
- Suitable Production Volume: Medium to low production runs.
8. Common Defects and Improvement Strategies in Low-Pressure Molding
Some defects in low-pressure molding and ways to address them include:
Defect | Cause | Improvement Strategy |
Warping | Uneven cooling | Ensure uniform mold temperatures |
Incomplete Fill | Low injection pressure | Increase injection speed/pressure |
Flash | Poor mold clamping | Improve mold fit and clamping force |
Air Bubbles | Trapped air in material | Degas material before injection |
9. About BFY Mold
BFY Mold is a trusted provider of injection molding and mold manufacturing solutions, offering services like mass production, on-demand production, CNC machining, and mirror spark. With our factory and years of expertise, we deliver precision-engineered parts tailored to your needs.
Top 10 FAQs About Low-Pressure Injection Molding
1. What is low-pressure injection molding, and how does it differ from traditional injection molding?
In traditional molding, low-pressure injection molding (LPIM) uses 20–200 psi pressure (vs. 1,000–30,000 psi) to encapsulate delicate components like electronics or sensors. It minimizes stress on fragile parts, reduces material waste, and enables faster cycle times (10–30 seconds).
2. What materials are compatible with low-pressure injection molding?
Common materials include:
- Thermoplastics: Polyamide (PA), thermoplastic polyurethane (TPU).
- Hot melts: Ethylene-vinyl acetate (EVA) for waterproofing.
- Silicones: For high-temperature resistance (up to 150°C).
3. What industries benefit most from low-pressure injection molding?
- Electronics: Encapsulating PCB boards, connectors, and wire harnesses.
- Automotive: Sealing sensors and LED lighting.
- Medical: Waterproofing implantable device components.
4. How does LPIM reduce production costs compared to traditional methods?
- Lower tooling costs: Aluminum molds cost 30–50% less than steel molds.
- Reduced material waste: Precise dosing cuts scrap by 15–25%.
- Energy savings: Low-pressure machines consume 40% less power.
5. What tolerances can be achieved with low-pressure injection molding?
LPIM typically achieves ±0.1–0.3mm tolerances, suitable for encapsulating sensitive electronics. For tighter tolerances (±0.05mm), hybrid processes with CNC finishing may be required.
6. How do suppliers ensure quality in low-pressure molding processes?
- Process validation: Mold flow analysis to predict voids or air traps.
- In-line inspections: Automated vision systems check for defects like incomplete filling.
- Certifications: ISO 9001 and IATF 16949 for automotive applications.
7. Can LPIM handle complex geometries or multi-material components?
Yes. LPIM excels at:
- Overmolding: Bonding thermoplastics to metals or ceramics.
- Micro-features: Encapsulating components with gaps as small as 0.2mm.
- Multi-shot molding: Layering materials for hybrid properties (e.g., rigid + flexible).
8. What is the typical lead time for low-pressure injection molding projects?
- Prototyping: 1–2 weeks with 3D-printed or soft molds.
- Production: 4–8 weeks (including mold fabrication). Expedited services reduce timelines by 30% for urgent orders.
9. How sustainable is low-pressure injection molding?
LPIM is eco-friendly due to:
- Recyclable materials: TPU and PA are widely recyclable.
- Energy efficiency: Lower machine power consumption.
- Waste reduction: <5% material scrap vs. 10–15% in traditional molding.
10. What post-molding services do suppliers offer for LPIM components?
- Conformal coating: Added moisture resistance for electronics.
- Laser marking: Permanent serial numbers or logos.
- Functional testing: Electrical continuity checks, IP67 sealing validation.