How can you quickly and successfully try out the molds?
Many plastic parts products require new molds to be sampled and tested after mold opening. During the mold testing, we aim for prompt results and a smooth process to prevent delays and complications. How to complete the mold test during the mold test period? Here are two points we must know:
1. Mold designers and manufacturing technicians sometimes make mistakes. If we are not vigilant when trying out molds, small mistakes may cause big damage.
2. The result of the mold trial is to ensure the smoothness of future production.
Failure to follow proper steps and maintain accurate records during the mold trial can jeopardize the smooth flow of mass production. We emphasize more that if the mold is used smoothly, the profit recovery will be rapidly increased. Otherwise, the cost loss will be greater than the cost of the mold itself.

9 Precautions Before Mold Trial
1. Understand the relevant information of the mold
Obtain mold design drawings, analyze them thoroughly, and involve mold technicians in the trial process.
2. First check its mechanical coordination on the workbench:
Check for scratches, and missing or loose parts, and ensure proper movement towards the sliding plate. Examine for leaks in water channels and air pipe joints, and mark any restrictions on mold opening directly on the mold. Conducting these checks before hanging the mold can save time and prevent unnecessary disassembly later on.
3. Once all mold parts are confirmed to function correctly, choose an appropriate injection machine for testing. Pay attention when selecting.
(a) Injection capacity
(b) Width of guide rod
(c) Large departure
(d)Accessories
Whether the above is complete, etc. After everything is confirmed to be no problem, the next step is to hang the mold. When hanging, ensure that hanging hooks are not removed before locking all clamping templates and opening the mold to prevent loosening or breakage, which could lead to mold falling.
After installing the mold, meticulously inspect the mechanical actions of each part, including the slide plate, ejector pin, tooth extraction structure, and limit switch, to verify their proper functioning. And pay attention to whether the injection nozzle and the feed port are aligned. The next step is to pay attention to the mold-closing action. At this time, the mold closing pressure should be lowered. During manual and low-speed mold closing, carefully observe and listen for any irregular movements or abnormal sounds.
4. Increase the mold temperature:
Select an appropriate mold temperature controller based on the raw material performance and mold size to raise the mold to the required production temperature. After increasing the mold temperature, recheck the movement of each part to prevent jamming due to the steel’s thermal expansion. Pay close attention to sliding to avoid strain and vibration.
5. If the factory doesn’t follow an experimental plan, it’s advisable to adjust only one condition at a time during mold trials. This helps discern the impact of individual changes on the finished product.
6. Depending on the raw materials, roast them appropriately.
7. Use the same raw materials as much as possible for trial molds and future mass production.
8. Do not test the mold entirely with inferior materials. If there is a color requirement, you can arrange a color test together.
9. Problems such as internal stress often affect secondary processing. Secondary processing should be carried out after the mold trial and after the finished product is stable. After closing the mold slowly, adjust the mold closing pressure and operate it several times to check whether it is correct. Uneven molding pressure will prevent burrs and mold deformation in the finished product.
After completing the aforementioned steps, decrease the mold closing speed and pressure, and configure the safety buckle and ejection stroke. Subsequently, adjust the normal mold closing speed and pressure. If a limit switch with a larger stroke is present, slightly shorten the mold opening stroke and disable the high-speed mold opening action before the larger stroke. This precaution is necessary because the high-speed action stroke is longer than the low-speed one during mold loading. Additionally, adjust the mechanical ejector rod on the plastic machine to operate after the full-speed mold opening action to prevent deformation of the ejector plate or peeling plate due to force.
Check the following items before making the first mold injection:
(a) Whether the feeding stroke is too long or insufficient.
(b) Whether the pressure is too high or too low.
(c) Whether the mold filling speed is too fast or too slow.
(d) Whether the processing cycle is too long or too short.
To prevent the finished product from short shots, breakage, deformation, burrs, and even damage to the mold.
If the processing cycle is too short, the ejector pin will penetrate the finished product or the ring will be peeled off and the finished product will be damaged. This type of situation can take you two to three hours to get the finished product out.
If the processing cycle is too long, the weak parts of the mold core may be broken due to the shrinkage of the rubber material.
Of course, you cannot predict all the problems that may occur during the mold trial, but taking timely and fully considered measures in advance can help you avoid serious and expensive losses.

10 Main Steps of Mold Trial
To prevent unnecessary time and trouble during mass production, patience is essential to adjust and control processing conditions effectively. This involves finding optimal temperature and pressure settings and establishing standard mold trial procedures for daily operations.
1. Check whether the plastic material in the barrel is correct and whether it has been baked according to regulations (if different raw materials are used in trial molding and production, different results are likely to be obtained).
2. Ensure thorough cleaning of the material tube to avoid injecting bad rubber or debris into the mold, which could cause jamming. Verify that both the material tube and mold temperatures are suitable for the raw materials being processed.
3. Adjust the pressure and injection volume to produce a finished product with a satisfactory appearance. However, burrs should not be allowed. Especially when some mold cavity products are not completely solidified, you should think about it before adjusting various control conditions because the mold is filled. A slight change in the rate may cause significant changes in mold filling.
4. Be patient and wait until the conditions of the machine and mold stabilize. Even medium-sized machines may have to wait for more than 30 minutes. Use this time to review possible problems with the finished product.
5. The screw advancement time cannot be shorter than the solidification time of the gate plastic, otherwise the weight of the finished product will be reduced and the performance of the finished product will be compromised. And when the mold is heated, the screw advancement time also needs to be lengthened to compact the finished product.
6. Make reasonable adjustments to reduce the total processing cycle.
7. Run the newly adjusted conditions for at least 30 minutes until they are stable, and then continuously produce at least a dozen full-mold samples. Mark the date and quantity on the containers, and place them according to the mold cavities to test the stability of their actual operation. and derive reasonable control tolerances. (Especially valuable for multi-cavity molds).
8. Measure the continuous samples and record their important dimensions (the samples should be cooled to room temperature before measuring).
9. When comparing the measured dimensions of each mold sample, please note:
(a) Whether the dimensions are stable.
(b) Are there certain dimensions that tend to increase or decrease, indicating that the machine processing conditions are still changing, such as poor temperature control or oil pressure control?
(c) Whether the change in dimensions is within the tolerance range.
10. If the dimensions of the finished product do not change much and the processing conditions are normal, it is necessary to observe whether the quality of the finished product in each mold cavity is acceptable and the dimensions are within the allowable tolerance. Record the mold cavity numbers that are continuously larger or smaller than the average value to check whether the size of the mold is correct.
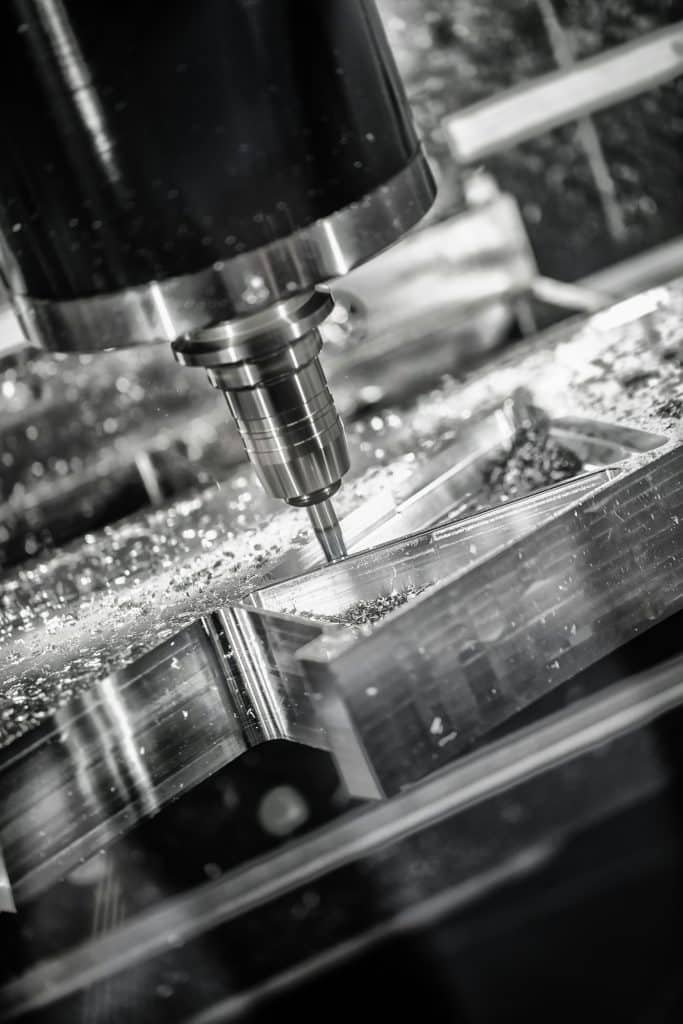
Record and Analyze Data
Record and analyze data to meet the needs of modifying molds and production conditions, and as a reference for future mass production.
1. Make the processing operation time longer to stabilize the melt temperature and hydraulic oil temperature.
2. Adjust the machine conditions according to whether the size of all finished products is too large or too small. If the shrinkage rate is too large and the finished product appears to have insufficient injection material, you can also increase the gate size for reference.
3. If the size of each mold cavity is too large or too small, correct it. If the size of the mold cavity and door is still correct, then you should try to change the machine conditions, such as mold filling speed, mold temperature and pressure of each part, etc., and check some molds. Whether the cavity filling is slow.
4. According to the fit of the finished mold cavity products or the displacement of the mold core, make individual corrections. You may also try to adjust the mold filling rate and mold temperature to improve the uniformity.
5. Check and correct the faults of the injection machine, such as defects in the oil pump, oil valve, temperature controller, etc., which will cause changes in processing conditions. Even the most perfect mold cannot perform well on a poorly maintained machine.
After reviewing all recorded values, keep a set of samples for proofreading and comparison to see if the corrected samples have improved.
Final Important Matters
Properly keep all records of sample inspection during the mold trial process, including various pressures during the processing cycle, melt and mold temperature, material tube temperature, injection action time, screw feeding period, etc. In short, all records that will be helpful in the future should be kept. Data that can be used to successfully establish the same processing conditions can be used to obtain products that meet quality standards.
At present, mold temperature is often ignored during mold testing in factories, and it is difficult to control mold temperature during short-term mold testing and future mass production. Incorrect mold temperature can affect the size, brightness, shrinkage, flow lines, and lack of material of the sample. If the mold temperature controller is not used, difficulties may arise in mass production in the future.

BFY Mold integrates product conception with product forming and mainly undertakes plastic mold product development, mold design and manufacturing, product injection molding, product surface treatment, and other services. With more than 20 years of production experience in mold design and mold manufacturing, the injection molding processing industry can create competitive molds for you. Contact us today for free drawing optimization.