Introduction
Injection molding defects cost manufacturers up to 15% in material waste and 20% in delayed deliveries annually. From sink marks to warping, even minor issues can cascade into costly recalls—especially in regulated industries like medical devices and automotive.
Drawing from BFY Mold’s analysis of 10,000+ production runs, this guide dissects the top 5 injection molding defects, their root causes, and actionable solutions backed by real-world data. Equip your team to reduce scrap rates and optimize cycle times.
1. Sink Marks: Causes & Corrections
What It Looks Like: Localized surface depressions, often near thick ribs or bosses.
Common location: home appliance shell reinforcement, automotive interior installation column.
Root Causes:
- Insufficient packing pressure (material shrinkage during cooling).
- Excessive wall thickness variations (e.g., 4mm rib vs. 2mm base).
- High mold temperature slowing cooling.

BFY Mold’s Fixes:
- Increase Packing Pressure:
- Increase the filling pressure from the default 50% to 70-80% and maintain it for 5-10 seconds (refer to the material data sheet).
- Case: In producing a power tool shell, the pressure holding pressure is adjusted from 60MPa to 75MPa, and the shrinkage rate is reduced from 8% to 1.5%.
- Redesign Part Geometry:
- The thickness of the reinforcement is controlled at 50-60% of the thickness of the main wall (such as 3mm of the main wall → 1.5-1.8mm of the reinforcement).
- Optimize Cooling Channels:
- Adding a follow-up waterway to the thick-walled area reduces the cooling time by 30% (e.g., from 15 seconds to 10 seconds).
Verification criteria: Test dimensional stability according to ASTM D955. Shrinkage depth <0.05mm is qualified.
2. Warping: When Parts Lose Shape
What It Looks Like: Bent or twisted geometries, especially in flat parts.
High-incidence materials: semi-crystalline plastics (PP, nylon), glass fiber reinforced materials.
Root Causes:
- Uneven cooling rates (e.g., top/bottom mold temperature difference>15°C).
- Residual stress from high injection speeds.
- Fiber orientation mismatch in reinforced plastics.
BFY Mold’s Fixes:
- Balance Cooling System:
- Use an infrared thermal imager to detect mold temperature differences and adjust the water flow rate to make the temperature difference <5°C.
- Case: A drone propeller uses a symmetrical cooling design, reducing the warpage from 0.8mm to 0.2mm.
- Reduce Injection Speed:
- Reduce the injection speed from 90% to 60–70% to reduce shear stress (for nylon + 30% glass fiber).
- Annealing Post-Processing:
- Reduce the injection speed from 90% to 60–70% to reduce shear stress (for nylon + 30% glass fiber). Anneal high-temperature materials such as PEEK (20°C above Tg, hold for 2 hours) to release internal stress.
Data Comparison:
Conditions | Warpage (mm) | Production yield |
Original | 0.75 | 72% |
After optimization | 0.18 | 95% |
3. Short Shots: Incomplete Filling
What It Looks Like: Parts missing sections, especially in thin areas.
Typical scenarios: thin-wall electronic connectors (less than 0.5 mm), multi-cavity molds.
Root Causes:
- Low melt temperature (material viscosity too high).
- Inadequate venting (trapped air prevents flow).
- Insufficient injection pressure/velocity.
BFY Mold’s Fixes:
- Increase Melt Temp:
- ABS fluidity increases by 40% from 230°C to 250°C (degradation risk needs to be monitored).
- Add/Expand Vents:
- The depth of the exhaust groove is increased from 0.015mm to 0.025mm (for PC material).
- Auxiliary exhaust inserts are added to the parting surface.
- Switch to High-Flow Materials:
- Ordinary PP melt index 15g/10min → High flow PP melt index 35g/10min (such as Sabic PP67MH6).
Emergency treatment plan: When a short shot occurs, immediately check the status of the nozzle heating ring and the check ring.
4. Flash: Excess Material on Part Edges
What It Looks Like: Thin plastic fins along parting lines or ejector pins.
High-risk processes: multi-color injection molding, silicone encapsulation.

Root Causes:
- Excessive injection pressure/clamping force mismatch.
- Worn mold components (e.g., damaged parting surfaces).
- Low-viscosity materials (e.g., LSR liquid silicone).
BFY Mold’s Fixes:
- Adjust Clamping Force:
- Calculate the required clamping force using the following formula: projected area (cm²) × material pressure (MPa) × safety factor 1.2.
- Case: A PP pallet with a projected area of 800cm² requires a clamping force: 800 × 35 × 1.2 = 336 tons → Select a 350-ton machine.
- Mold Maintenance:
- Polish the parting surface every 50,000 molds, and keep the Ra value below 0.4μm.
- Reduce Injection Speed:
- The LSR injection speed is increased from 50% to 30%, reducing the risk of overflow.
5. Flow Lines: Aesthetic & Structural Risks
What It Looks Like: Wavy patterns or discoloration along flow paths.
Commonly used in transparent parts (such as PC lampshades) and high-gloss surfaces.
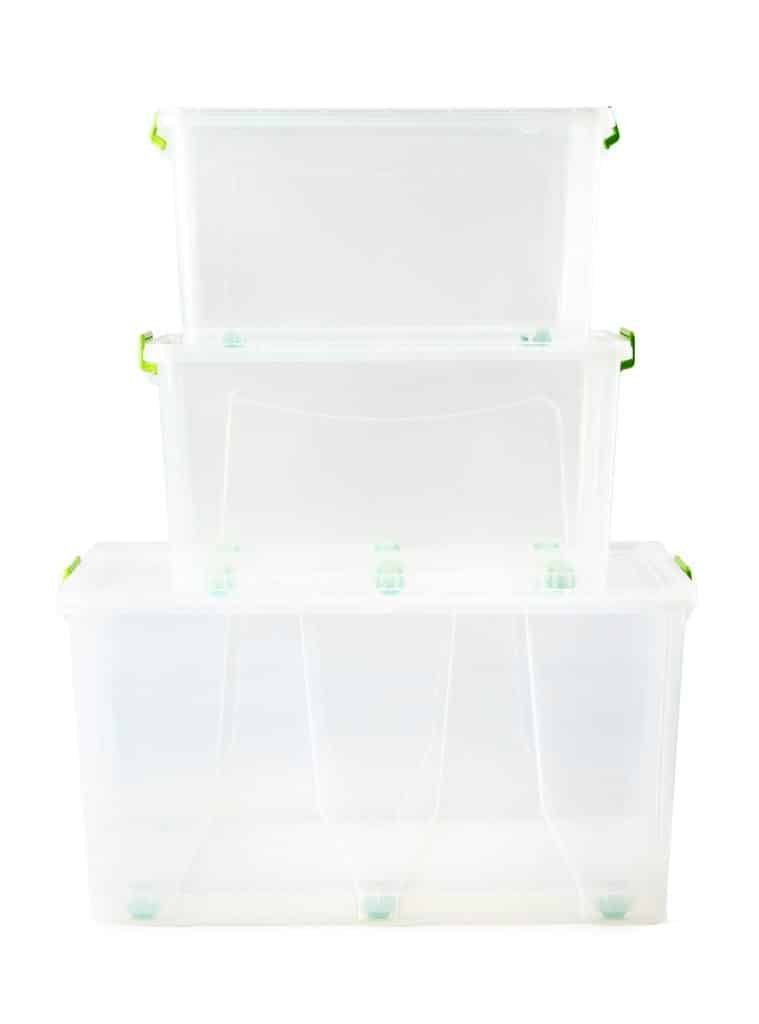
Root Causes:
- Melt temperature fluctuations (e.g., ±10°C fluctuations).
- Multi-gate interference causing flow front collisions.
- Contamination or moisture in the material.
BFY Mold’s Fixes:
- Stabilize Melt Temp:
- Check the heating coil and thermocouple to ensure the barrel temperature fluctuation is <±2°C.
- Optimize Gate Locations:
- Using mold flow analysis, the flow front temperature difference was controlled within 5°C.
- Pre-Dry Materials:
- Nylon dried at 85°C for 4 hours, moisture content <0.15%.
Customer case: The LED lens manufacturer reduced the flow mark defect rate from 12% to 0.3% by adjusting the gate position + mold temperature to 110°C.
BFY Mold’s Defect Prevention Toolkit
- Real-time monitoring system: On-machine sensors track pressure and temperature curves and automatically alarm when they deviate from the standard.
- Material database: Process parameter templates for 1000+ materials (such as holding time and cooling rate).
- Quick response service: Provide 24/7 process engineer support to remotely diagnose the root cause of injection molding defects.
Conclusion
Fix sink marks, warping, flash, and more with BFY Mold’s proven solutions to injection molding defects. Contact us and optimize production quality today.