Stainless steel machining is a critical process in modern manufacturing, used across a variety of industries to create durable, high-precision parts.
Whether in aerospace, automotive, medical devices, or consumer products, stainless steel is valued for its strength, corrosion resistance, and aesthetic appeal. However, due to its hardness and unique properties, stainless steel machining requires specialized techniques and equipment to shape and form parts accurately. In this essay, we’ll delve into what stainless steel machining is, how it works, and the benefits it offers in production.

What is Stainless Steel Machining?
Stainless steel machining is the process of shaping stainless steel material into desired parts or components using various machining techniques. These processes may include milling, turning, drilling, grinding, and more. Stainless steel, an alloy primarily made of iron, chromium, and nickel, is known for its high resistance to corrosion, toughness, and strength, making it an ideal material for demanding applications.
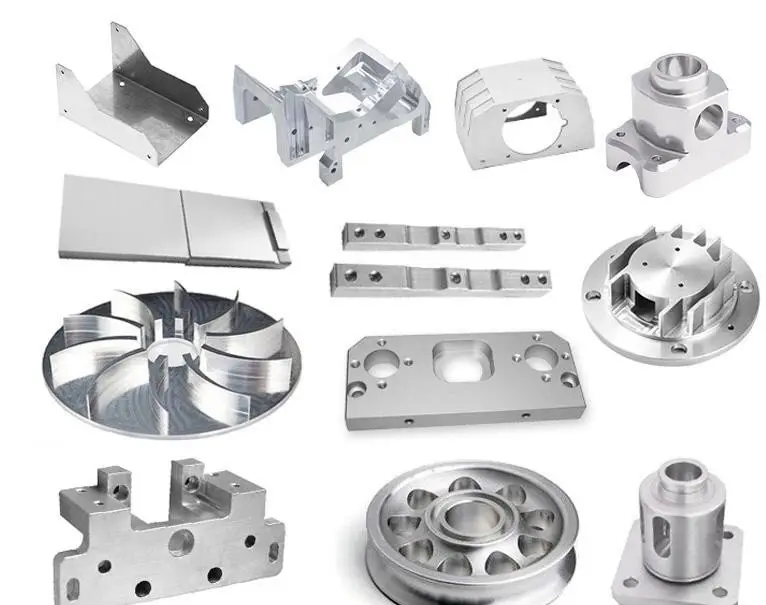
Because stainless steel is harder and more durable than many other metals, it requires precise control over cutting tools, speeds, and feeds to achieve the desired finish and dimensions. The most commonly used machining methods for stainless steel are:
- CNC Milling: This involves the use of computer-controlled machines to remove material from a stainless steel workpiece. It is commonly used for creating complex shapes, grooves, and cavities.
- CNC Turning: Involves rotating a piece of stainless steel material while a cutting tool is used to shape the metal. It is ideal for producing cylindrical or round components.
- Grinding: Grinding is used to smooth or polish stainless steel surfaces to precise dimensions. It’s typically used for finishing tasks or when high precision is required.
- Drilling: Drilling is employed to create holes or bores in stainless steel parts. Specialized tools are often used to prevent workpiece damage due to the hardness of stainless steel.
The stainless steel machining process requires knowledge of tool selection, cutting parameters, and cooling techniques to prevent overheating, which can damage both the workpiece and tools.
Key Types of Stainless Steel Used in Machining
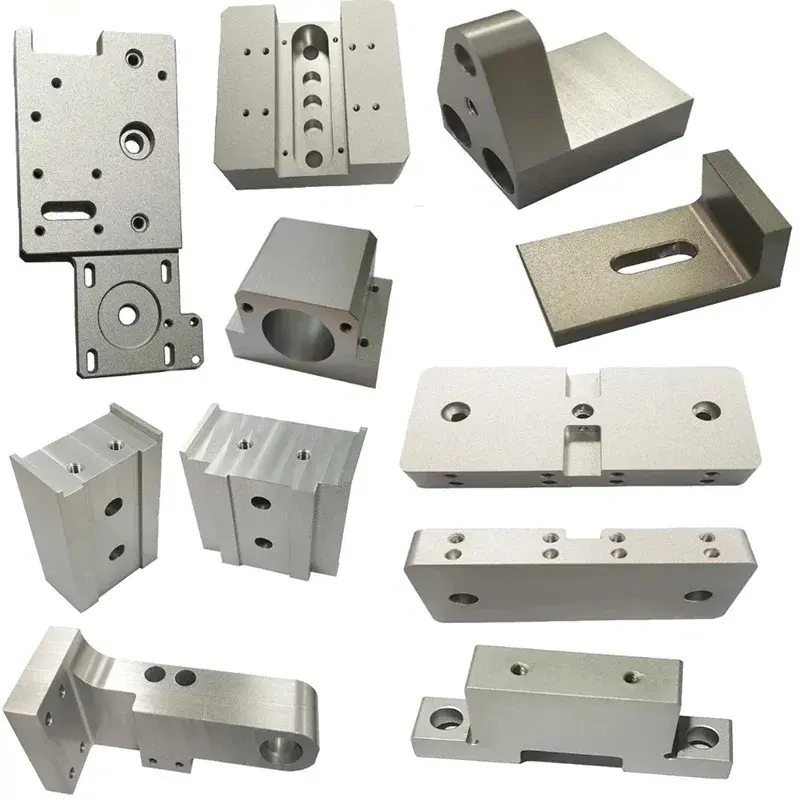
Stainless steel comes in a variety of grades, each offering different properties and machinability characteristics. Some of the most common types of stainless steel used in machining include:
- 304 Stainless Steel: One of the most common and versatile grades of stainless steel, 304 is non-magnetic and resistant to corrosion. It’s used in industries ranging from food processing to medical devices and is relatively easy to machine compared to other stainless steels.
- 316 Stainless Steel: Known for its superior corrosion resistance, especially in marine environments, 316 is more difficult to machine due to its hardness but is favored for applications where resistance to harsh chemicals or saltwater exposure is crucial.
- 17-4 PH Stainless Steel: A precipitation-hardening stainless steel that provides a combination of high strength and resistance to corrosion. It is typically used in aerospace and medical industries and is more challenging to machine due to its hardness.
- 410 Stainless Steel: A martensitic stainless steel with good wear resistance and strength, often used in tools and machinery components. It is harder to machine than austenitic grades like 304 or 316 but offers superior hardness.
Each type of stainless steel has its own set of machining challenges, which require careful attention to cutting speed, tool material, and machining method to ensure a successful outcome.
Challenges in Stainless Steel Machining
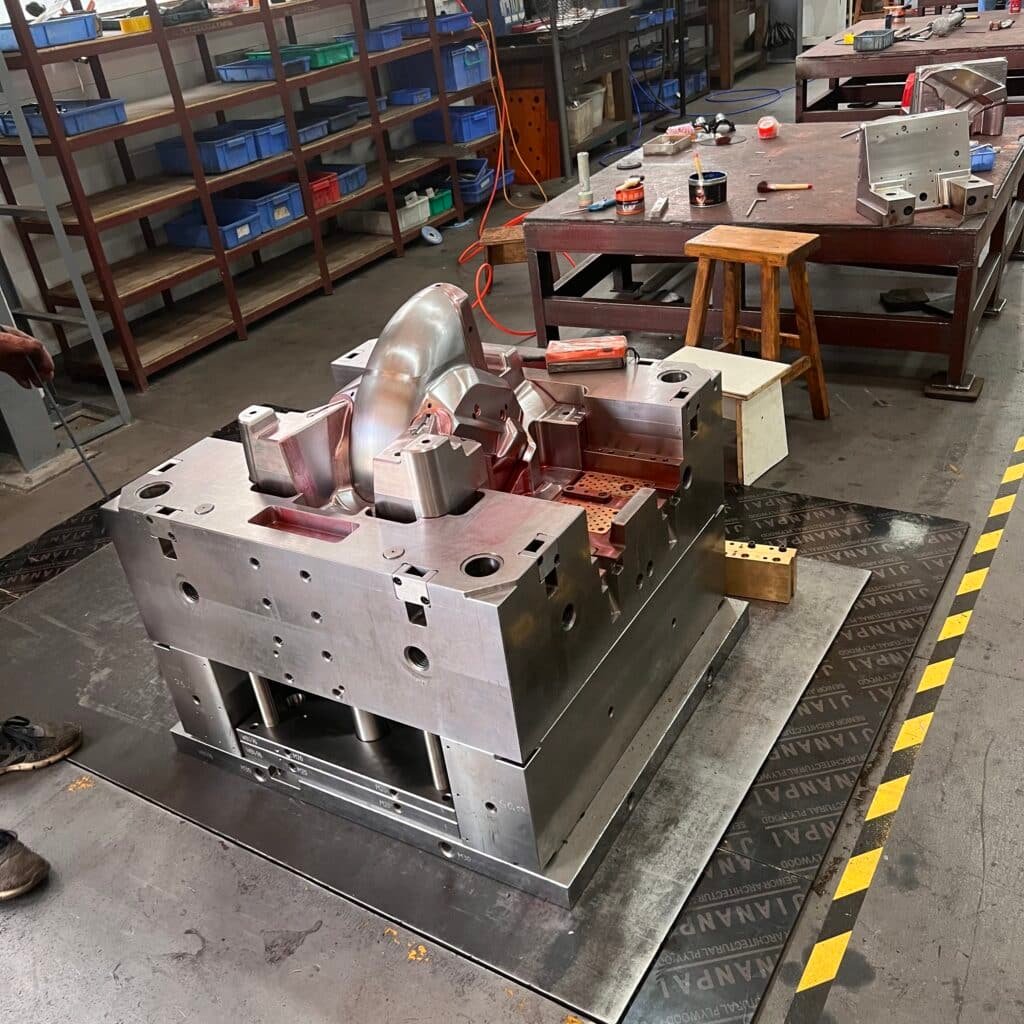
While stainless steel offers numerous benefits, it also presents challenges during the machining process:
- Tool Wear: Stainless steel is a hard material, and machining it can quickly wear down tools, especially if the wrong tools are used or if cutting speeds and feeds are not optimized. Special tool materials such as carbide and high-speed steel (HSS) are typically used to extend tool life.
- Work Hardening: Stainless steel has a tendency to work-harden when exposed to heat during machining. As the material deforms, it can become harder, making it more difficult to machine. To counteract this, it’s important to use the right cutting parameters and cooling techniques.
- Heat Management: The hardness of stainless steel means it generates a lot of heat during machining, which can cause thermal expansion or even damage the part. Coolants and lubricants are used to dissipate heat and ensure smooth cutting.
- Surface Finish: Achieving a smooth and uniform surface finish on stainless steel can be challenging due to its hardness and propensity to form burrs or rough edges. Post-machining processes like polishing or grinding are often required to achieve the desired finish.
- Cost: Stainless steel is a more expensive material compared to other metals like aluminum. This makes machining stainless steel more costly, particularly in mass production, as it requires higher precision, longer production times, and more wear-resistant tooling.
Despite these challenges, the benefits of stainless steel in terms of strength, corrosion resistance, and longevity often outweigh the difficulties of machining, especially for critical applications where reliability is paramount.
Advantages of Stainless Steel Machining
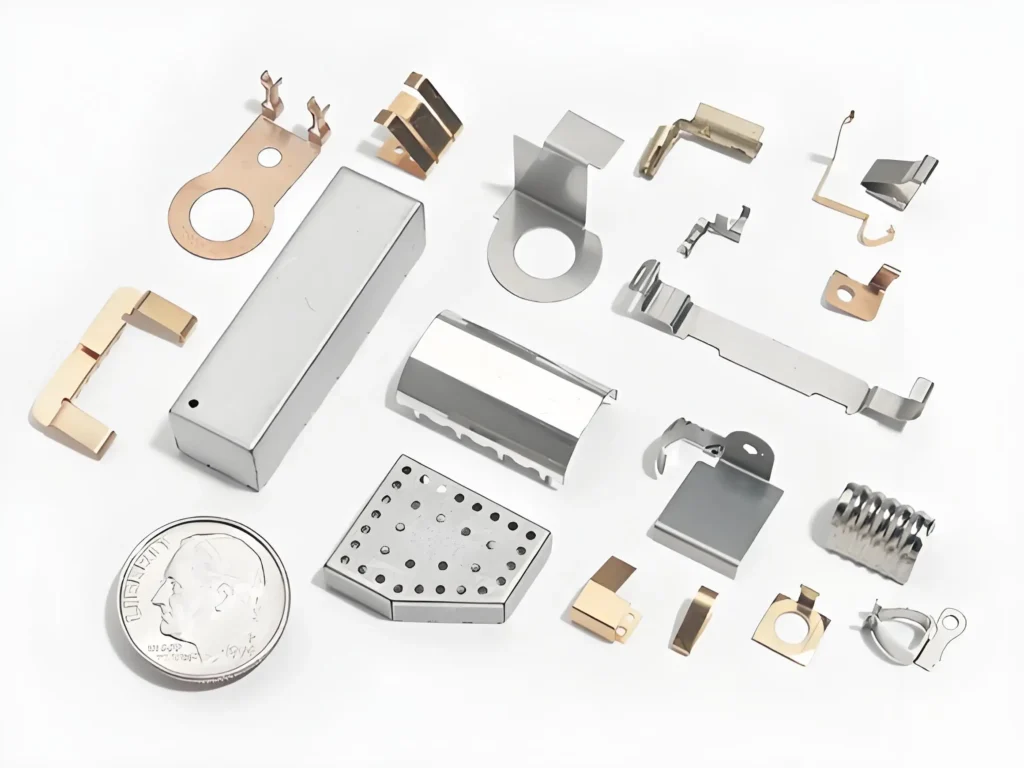
- Corrosion Resistance: Stainless steel’s ability to resist corrosion makes it ideal for use in environments that expose parts to moisture, chemicals, or extreme temperatures. This is particularly valuable in industries like aerospace, medical, food processing, and marine applications.
- Durability and Strength: Stainless steel parts are known for their durability and strength, which is why they are preferred for heavy-duty applications such as machinery, automotive components, and structural elements.
- Aesthetic Appeal: Stainless steel’s bright, shiny finish is aesthetically pleasing and often used in applications where appearance matters, such as in kitchen appliances, medical devices, and consumer goods.
- Customizability: Stainless steel can be machined to tight tolerances, making it a versatile material for a variety of custom components. CNC machining allows for intricate designs and complex geometries that would be difficult to achieve with other materials.
- Longevity and Low Maintenance: Stainless steel parts are long-lasting and require minimal maintenance, reducing replacement costs and downtime in critical machinery.
- Health and Safety: Stainless steel is a non-toxic, hygienic material, which is crucial in industries like food processing and medical equipment manufacturing, where cleanliness and safety are paramount.
- High-Temperature Resistance: Certain grades of stainless steel can withstand extremely high temperatures, making them suitable for applications in aerospace, power generation, and industrial manufacturing.
Applications of Stainless Steel Machining
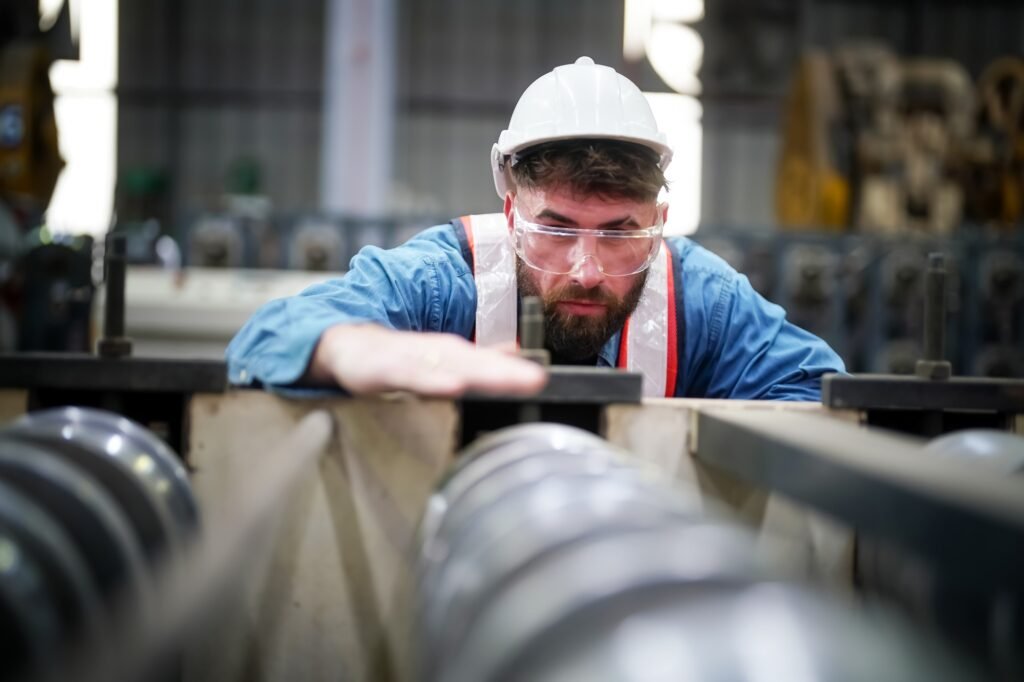
Stainless steel machining is used in a broad range of industries, including:
- Aerospace: Components such as turbines, valves, and brackets.
- Medical Devices: Surgical instruments, implants, and prosthetics.
- Automotive: Exhaust systems, engine components, and brackets.
- Food Processing: Food-grade machines, processing equipment, and storage tanks.
- Construction and Architecture: Structural elements, cladding, and architectural finishes.
Each application benefits from stainless steel’s unique combination of properties, including its resistance to wear, corrosion, and high temperatures.
About BFY Mold
At BFY Mold, we specialize in providing precision CNC machining and stainless steel machining services. With a fully equipped factory and years of expertise in injection molding and mold manufacturing, we offer custom solutions for a variety of industries. Our services also include mass production, on-demand production, CNC processing, and mirror spark, ensuring that we meet your specific manufacturing needs with the highest quality standards. Whether you need small or large-scale production, BFY Mold is your trusted partner for stainless steel and other metal parts machining.