These materials are various types of metals as well as various formulations of plastics used in manufacturing, including injection molding, CNC machining, and others.
Each type of metal showcases distinct characteristics that impact its application in mold making, machining processes, and mass production. Suppose you are considering using metals for injection molding or CNC machining. In that case, this article will break down their properties, differences, and uses, ultimately giving you information on how to make the most of your manufacturing.
1. How Important is Choosing the Right Type of Metal
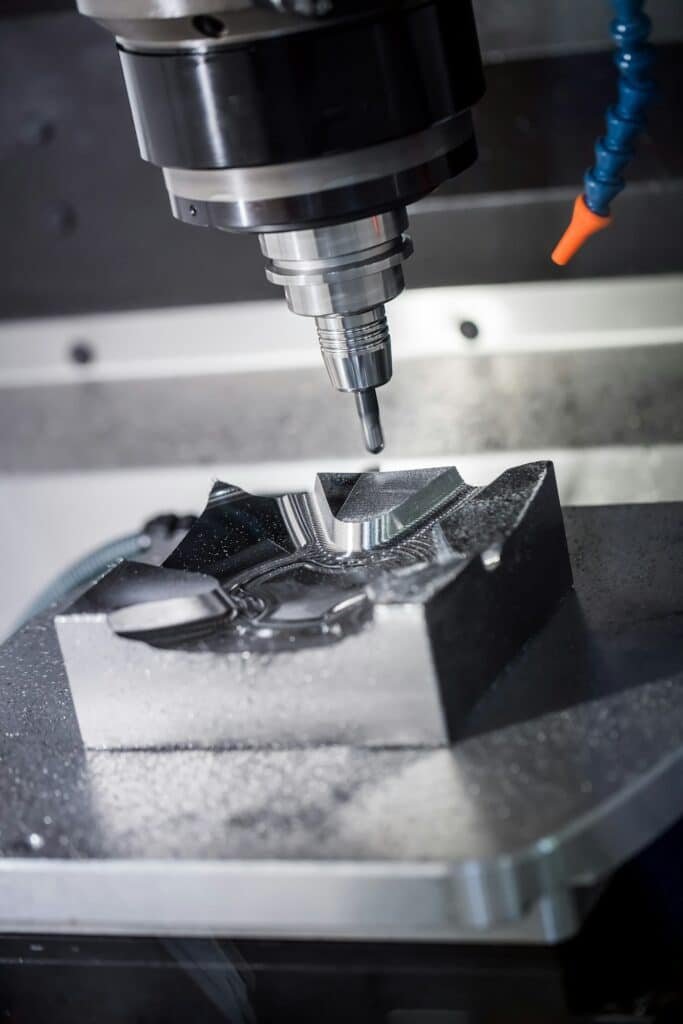
It is crucial that you select the correct type of metal for injection molding and CNC machining to produce high-quality, durable, and cost-effective products. It would be available if it meets certain criteria like strength, machinability, corrosion resistance, thermal conductivity, and so on. Knowing what affects the unique aspects of different types of metal enables better outcomes in prototype and mass production.
Molds for injection molding are made of hard and durable metals that can withstand high temperatures, pressure, and wear. Tool steel and aluminum are among the more popular materials.
These processes are fundamentally different, whereas CNC Machining is material removal to shape parts from a workpiece. Depending on the type of metal selected for CNC machining, precision, cost, and speed offered by the manufacturing process can significantly vary.
2. The 5 Most Common Types of Metal Used in Injection Molding and CNC Machining
A. Steel (Including Tool Steel)
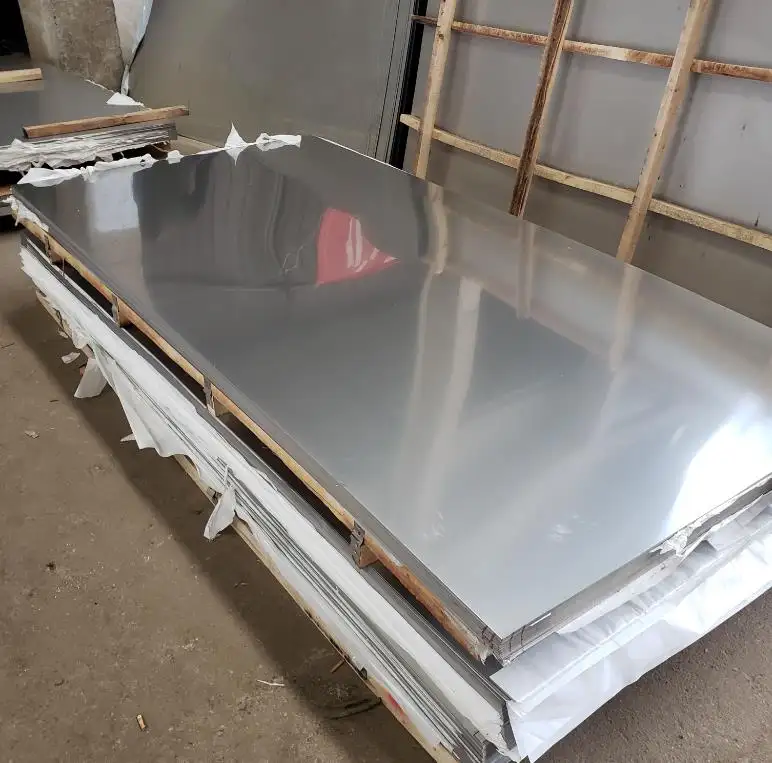
- Characteristics: Steel is the most widely used type of metal in injection molding and CNC machining due to its strength, durability, and resistance to wear and corrosion. Tool steels, in particular, are designed for high-performance applications.
- Carbon Steel: Strong but susceptible to corrosion.
- Alloy Steel: Adds elements like chromium for enhanced strength and corrosion resistance.
- Tool Steel: Specifically made for cutting, shaping, and molding tools due to its hardness and resistance to high temperatures.
- Applications: Steel is frequently used for molds in injection molding and CNC machining, particularly in the automotive, aerospace, and industrial sectors. Tool steels like P20 and H13 are often chosen for high-performance molds.
B. Aluminum
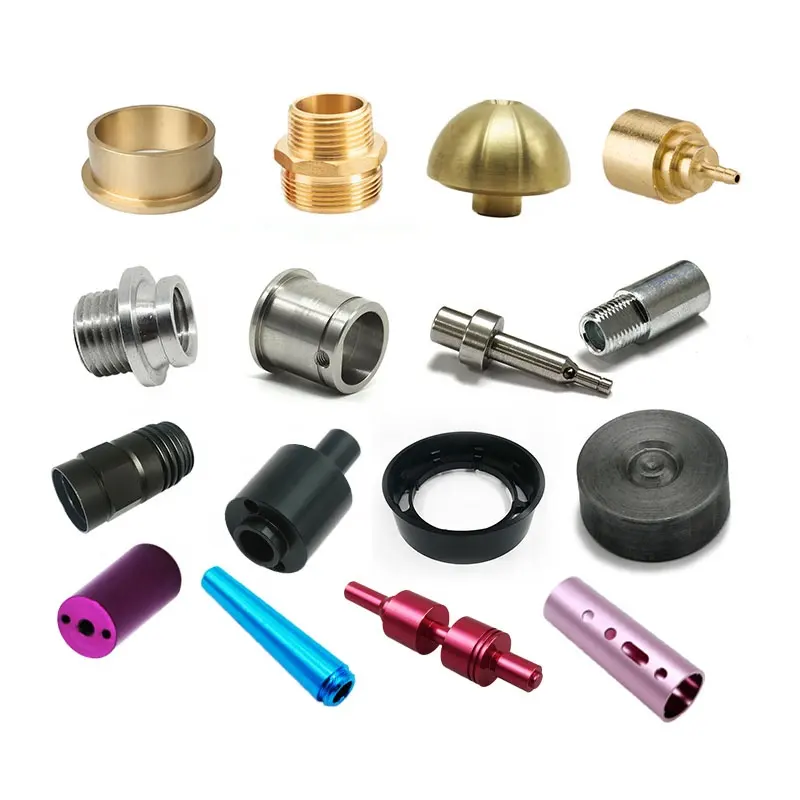
- Characteristics: Aluminum is lightweight, corrosion-resistant, and has good thermal conductivity, making it a popular choice for a variety of manufacturing applications. It is easy to machine and cost-effective.
- 6061 Aluminum: A versatile, high-quality metal that is commonly used in CNC machining.
- 7075 Aluminum: Known for its strength-to-weight ratio, making it ideal for aerospace and military applications.
- Applications: Aluminum is used in both injection molding and CNC machining. Aluminum injection molds offer quick turnaround times for low-volume production, while CNC machining often uses aluminum for high-precision parts in electronics, automotive, and aerospace industries.
C. Titanium

- Characteristics: Titanium is a lightweight, corrosion-resistant metal with exceptional strength, making it ideal for high-stress applications. It is used where both strength and low weight are critical.
- Grade 5 Titanium: The most commonly used titanium alloy, offering excellent strength and fatigue resistance.
- Applications: Titanium is primarily used in CNC machining for aerospace, medical, and military components. Its high cost limits its use in injection molding, but it is still relevant for specialized, high-performance parts.
D. Copper and Copper Alloys
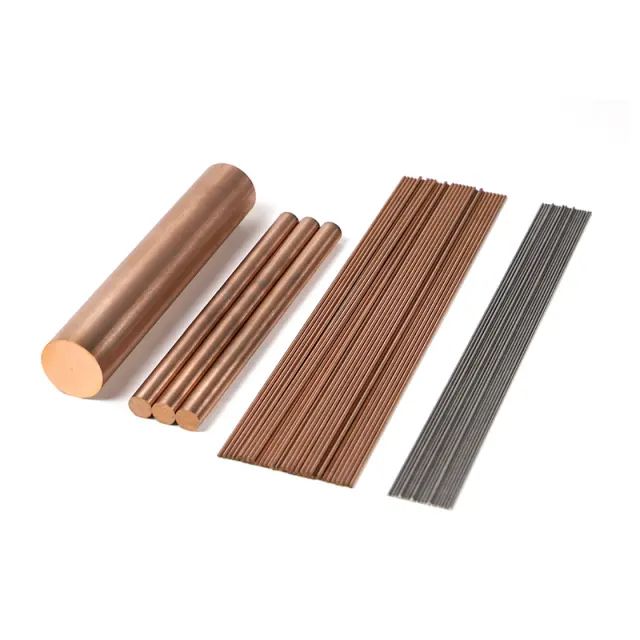
- Characteristics: Copper is highly conductive and resistant to corrosion, making it essential in electrical applications. Copper alloys like brass and bronze provide additional strength and versatility.
- Brass: Offers good machinability and corrosion resistance, often used for decorative and plumbing parts.
- Beryllium Copper: Known for its strength and electrical conductivity, making it ideal for electrical connectors and components.
- Applications: Copper alloys are commonly used in CNC machining for electrical components, heat exchangers, and connectors. In injection molding, copper alloys are used for parts requiring excellent conductivity and corrosion resistance.
E. Stainless Steel
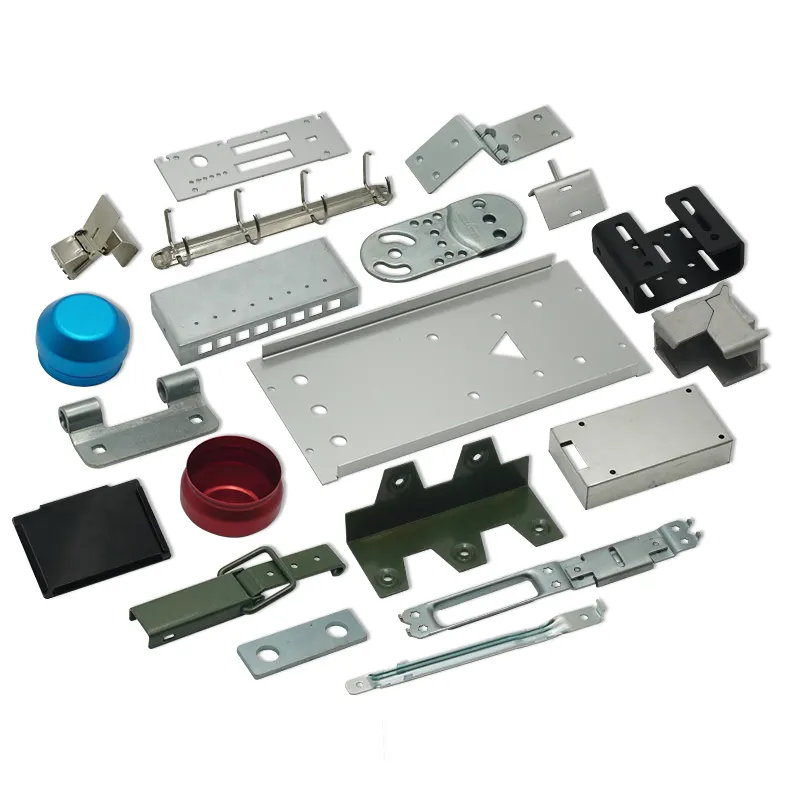
- Characteristics: Stainless steel is known for its high resistance to corrosion, strength, and durability. It is a versatile type of metal that can withstand extreme temperatures and is highly resistant to rust and corrosion.
- 304 Stainless Steel: Commonly used for its good corrosion resistance and formability.
- 316 Stainless Steel: Known for its superior resistance to corrosion, making it ideal for medical and food-related industries.
- Applications: Stainless steel is used in both injection molding and CNC machining for creating long-lasting, durable parts in industries such as medical, food, and automotive.
3. Key Differences Between Types of Metal for Injection Molding and CNC Machining
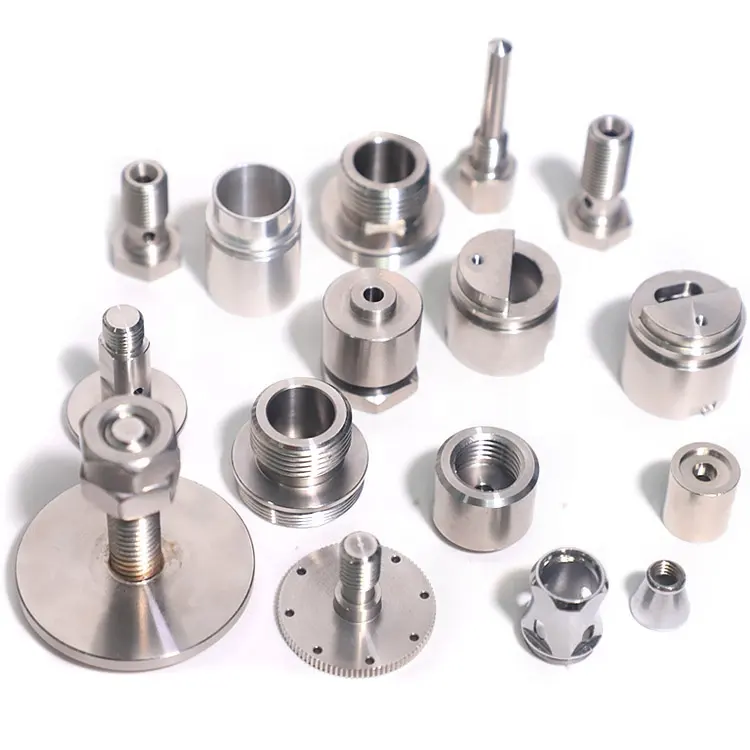
Property | Injection Molding Metals | CNC Machining Metals |
Strength | High (especially tool steel) | Varies (steel, aluminum) |
Thermal Conductivity | Important for heat dissipation | Crucial for machining speed |
Corrosion Resistance | Vital for mold longevity | Important for longevity and precision |
Machinability | Moderate (especially for steel molds) | High (aluminum, brass, stainless steel) |
Cost | Higher for tool steels | Varies by metal choice (aluminum is cheaper) |
Injection Molding: Tool steels are ideal where tooling life is important due to their wear resistance; aluminum is also used for shorter production runs.
Common materials used in CNC Machining include, But are not limited to: Aluminum, Brass, Stainless Steel, Copper, and Other Metals. These materials have the advantage of the ease of machining, as well as a wide variety of applications (e.g. Electronics, Aerospace).
4. Common Issues in Selecting the Right Type of Metal for Manufacturing
- Corrosion Resistance: Choosing the right metal material with corrosion resistance means no issues down the line wherein the mold or machined part is supposed to last.
- Machining: Certain types of metal, for example aluminum, have much more machinability so production takes less time and expenses than others. However, stronger metals, such as titanium, take longer and require more specialized tools.
- Material: Higher-performance metals (e.g., Titanium, specialty tool steels) may increase the cost of production. Manufacturers have to weigh material performance against budgets.
- Wear Resistance: For applications under heavy stress, such as molds in injection molding, materials like tool steel are essential to reduce wear and increase lifetime.
5. Frequently Asked Questions
1. What type of metal is best for injection molding?
The common materials used in injection molding include tool steels, with P20 and H13 being the most common due to their high strength, wear resistance, and temperature resistance.
2. Able to do CNC Machining on Aluminum?
Indeed, aluminum is extensively used in CNC machining due to its good machinability, strong strength-to-weight ratio, and affordability, especially in aerospace and automotive.
3. What are the advantages of Titanium for CNC Machining?
Titanium is known for its high strength-to-weight ratio and resistance to corrosion, so it is commonly used in aerospace, military, and medical components. However, it is a more expensive option than other materials.
4. Which type of metal is best for my manufacturing project?
What type of metal is best varies based on strength requirements, the part’s need for corrosion resistance, budget, and whether the metal will need to stand up to stress or be able to hold fine details.
5. CNC Machining – Which Metal is The Cheapest?
CNC machining is frequently the least costly option per part — good strength, machinability, and low component weight make aluminum a top choice for numerous applications.
Conclusion:
At BFY Mold, we specialize in mold manufacturing, injection molding, and CNC machining. Our expert team ensures that the type of metal selected for your project aligns with your needs for durability, precision, and cost-effectiveness. With our in-house production facilities, including CNC machining and mirror spark processing, we can deliver high-quality solutions for mass production, on-demand production, and custom projects.