Cost Considerations in Injection Molding
Injection molding is a popular manufacturing process known for its efficiency and ability to produce complex parts with high precision. However, the costs associated with injection molding can vary widely based on several factors. Understanding these cost considerations is crucial for manufacturers looking to optimize their production processes and budgets effectively. Here, we delve into the key cost factors in injection molding, including material costs, machine costs, and labor costs, providing insights to help you make informed decisions.
1. Material Costs
Material costs are a significant portion of the overall injection molding expenses. The type of material used can greatly influence the cost, and selecting the right material involves balancing performance requirements with budget constraints.
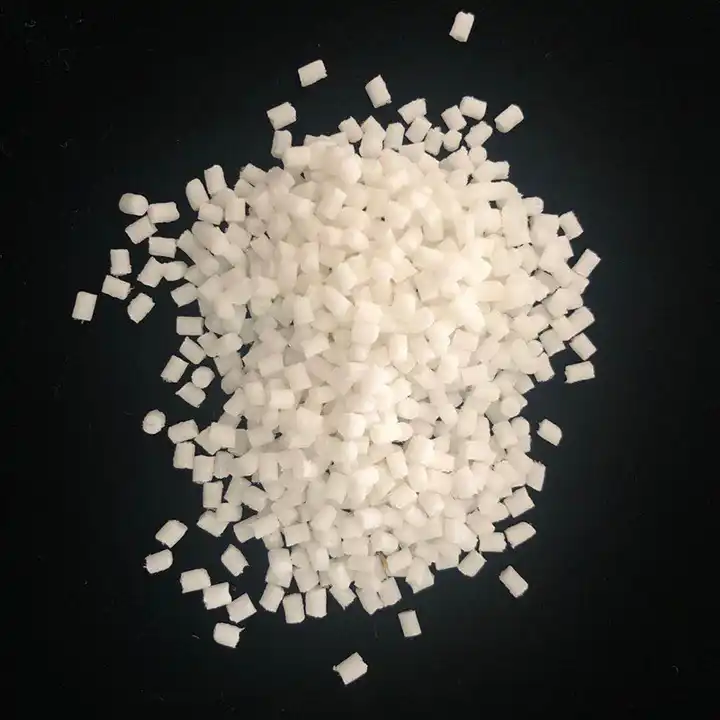
- Type of Material: Thermoplastics, thermosets, and elastomers each have different cost structures. Common thermoplastics like polypropylene and ABS are generally less expensive, while high-performance materials such as PEEK or medical-grade polymers can be much more costly.
- Material Properties: Materials with specific properties like high strength, chemical resistance, or biocompatibility often come at a premium. Evaluating the necessary material properties for your application is essential to avoid over-specifying and overspending.
- Material Waste: Efficient material usage and recycling can help reduce costs. Implementing strategies to minimize scrap and reusing regrind can lead to significant savings.
2. Machine Costs
Machine costs encompass the expenses associated with purchasing, operating, and maintaining injection molding machines. These costs can vary based on the machine’s size, capabilities, and technology.

- Machine Size and Tonnage: Larger machines with higher clamping force (tonnage) are typically more expensive to purchase and operate. Selecting a machine with the appropriate tonnage for your parts can optimize costs.
- Cycle Time: Faster cycle times can increase production rates and reduce per-part costs. Investing in advanced machines with optimized cooling systems and efficient automation can enhance cycle time performance.
- Energy Consumption: Energy-efficient machines can reduce operational costs over time. Look for machines with energy-saving features and consider the long-term savings on electricity bills.
- Maintenance and Downtime: Regular maintenance is crucial to prevent costly breakdowns and ensure consistent production. Investing in reliable machines and a robust maintenance program can minimize downtime and associated costs.
3. Labor Costs
Labor costs are another critical factor in the total cost of injection molding. These costs include wages for operators, technicians, and other personnel involved in the molding process.

- Automation: Implementing automation can significantly reduce labor costs by minimizing the need for manual intervention. Automated systems can handle tasks such as material feeding, part ejection, and quality inspection, leading to more consistent and efficient production.
- Skilled Labor: While automation can reduce labor costs, skilled technicians are still needed to set up, maintain, and troubleshoot machines. Investing in training and retaining skilled labor can improve production efficiency and reduce costly errors.
- Labor Efficiency: Streamlining workflows and optimizing production schedules can enhance labor efficiency. Implementing lean manufacturing principles and continuous improvement practices can help reduce labor costs while maintaining high-quality standards.
4. Tooling Costs
Tooling costs refer to the expenses associated with designing and manufacturing the molds used in injection molding. These costs can be substantial, especially for complex or high-precision molds.
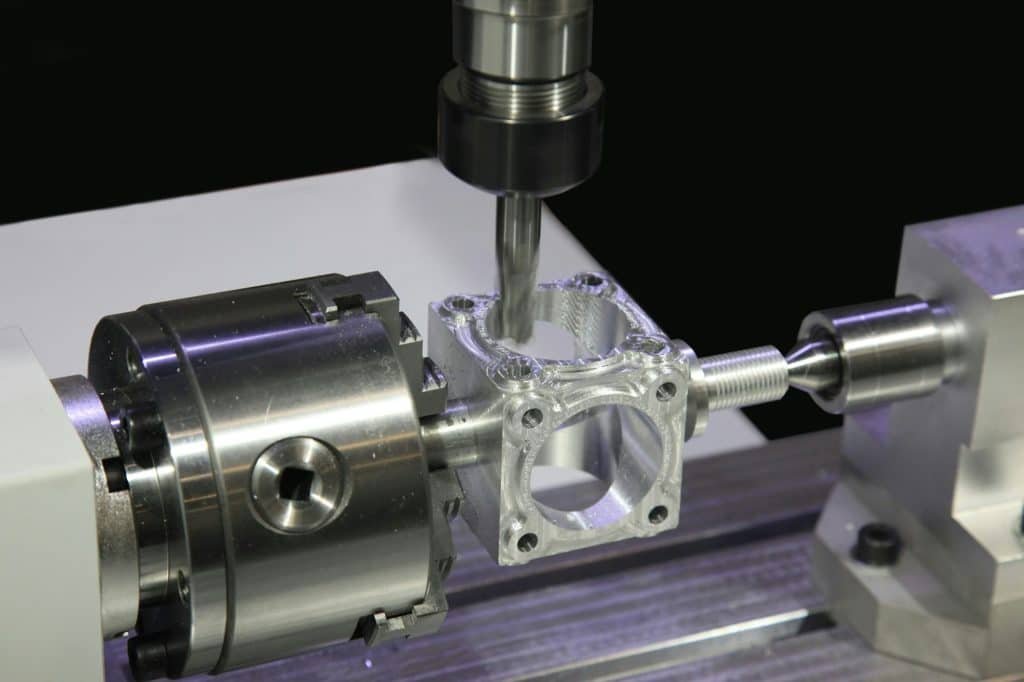
- Tooling Design: A well-designed mold is crucial for efficient production and high-quality parts. Investing in precision tooling with features like cooling channels and proper gating can reduce cycle times and minimize defects, leading to long-term cost savings.
- Material and Construction: The materials and construction methods used for the mold affect its durability and performance. High-quality materials and advanced manufacturing techniques can increase upfront costs but reduce maintenance and replacement expenses over time.
- Tooling Maintenance: Regular maintenance and proper storage of molds can extend their lifespan and reduce costs associated with repairs or replacements. Implementing a proactive maintenance program can help avoid unexpected downtime and expenses.
5. Overhead Costs
Overhead costs include indirect expenses such as facility costs, utilities, and administrative expenses. While these costs are not directly tied to production, they still impact the overall cost structure.
- Facility Costs: The cost of renting or owning a production facility, along with utilities like electricity, water, and heating, contribute to overhead costs. Optimizing facility layout and energy usage can help reduce these expenses.
- Administrative Expenses: Costs related to management, quality control, and other administrative functions also fall under overhead. Streamlining administrative processes and investing in efficient management systems can help control these costs.
6. Production Volume
The volume of parts produced can significantly influence the cost per part. Higher production volumes typically lead to lower per-part costs due to economies of scale.
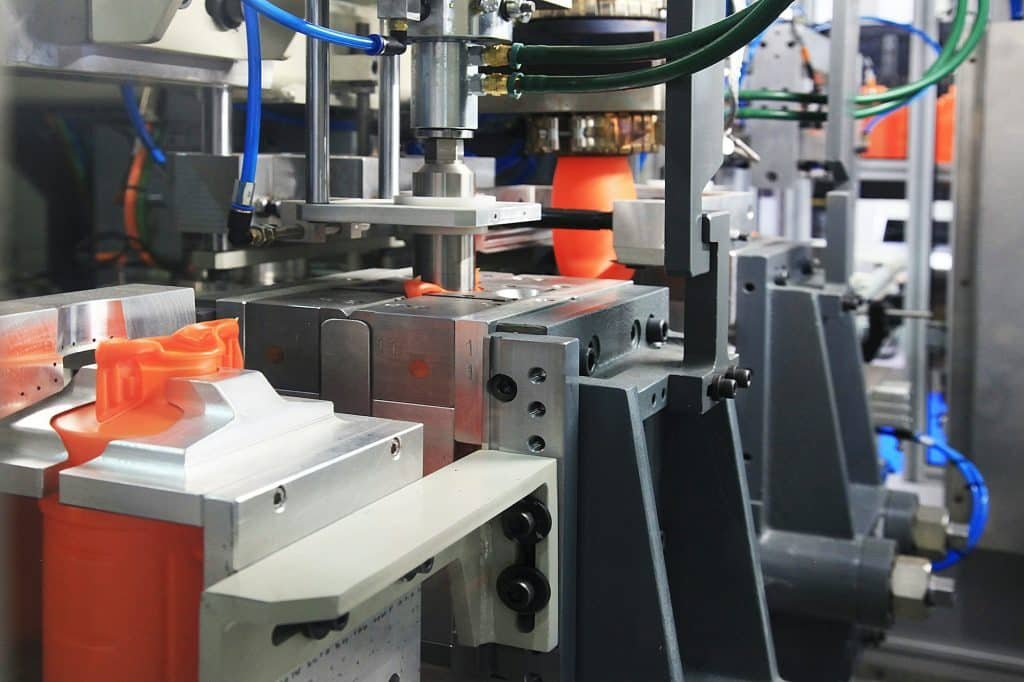
- Batch Size: Larger batch sizes can spread fixed costs over more parts, reducing the per-part cost. However, managing inventory and storage for large batches can introduce additional costs and challenges.
- Order Frequency: Frequent, smaller orders may result in higher per-part costs due to repeated setup and changeover times. Balancing order frequency with production efficiency can help optimize costs.
Summary
Understanding the various cost factors in injection molding is essential for manufacturers looking to optimize their production processes and budgets effectively. By considering material costs, machine costs, labor costs, tooling costs, overhead costs, and production volume, manufacturers can make informed decisions that balance quality and cost-efficiency.

About BFY Mold
At BFY Mold, we specialize in providing top-notch injection molding and mold manufacturing services. With our state-of-the-art factory, we offer mass production, on-demand production, CNC machining, and mirror spark services. Our team is dedicated to delivering high-quality, precision-engineered parts that meet the specific needs of our clients. Contact us today to learn how we can help you achieve your manufacturing goals.
10 FAQs for Cost-Efficient Injection Molding
1. How Does Material Selection Directly Impact Injection Molding Costs?
High-performance resins like PEEK (120–200/kg) triple the expenses compared to ABS (120–200/kg) triple the expenses compared to ABS (2–5/kg). Use glass-filled polymers to balance durability and budget.
2. What Mold Design Choices Reduce Long-Term Production Costs?
- Steel Type: H13 molds (500k+ cycles) vs. aluminum (5k cycles)
- Multi-Cavity Tools: Slash per-part costs by 40% for 10k+ volumes
3. How Does Production Volume Affect Per-Unit Pricing?
Quantity | Cost/Unit (ABS) | Tooling Cost Share |
1,000 | $8.50 | 65% |
50,000 | $2.20 | 12% |
4. Can Part Design Adjustments Lower Expenses?
Yes:
- Uniform wall thickness (1.5–3mm) cuts cycle time by 20%
- Draft angles ≥1° reduce ejection failures (saves $0.15/part)
5. What Hidden Costs Do New Manufacturers Overlook?
- Annual mold maintenance (3–5% of tooling cost)
- Material drying for hygroscopic resins ($0.50/kg extra)
6. How to Negotiate Better Pricing with Suppliers?
- Bundle orders for volume discounts (15–30% savings)
- Request T1 samples before full production runs
7. Which Automation Technologies Reduce Labor Costs?
Robotic sprue pickers trim cycle times by 12–18 seconds, saving $0.10–0.20/part.
8. How Does Supplier Location Influence Total Costs?
- Local (US/EU): $3–8/part (strict quality controls)
- Offshore: $1–3/part (+20% logistics/tariffs)
9. What Certifications Prevent Costly Quality Failures?
- ISO 9001: Reduces defects by 30%
- IATF 16949: Mandatory for automotive contracts
10. How Do Sustainable Practices Lower Expenses?
- Regrind programs (15–20% recycled material)
- Energy-efficient machines cut power use by 25%