Introduction
Thermoplastic Polyurethane (TPU) injection molding has become a popular manufacturing process in industries requiring flexibility, durability, and excellent mechanical properties. TPU is a versatile polymer known for its elasticity, transparency, and resistance to oil, grease, and abrasion.
Here’s an article that dives deep into TPU injection molding, explaining the process, benefits, and applications, along with insights into its challenges and solutions.
What is TPU Injection Molding?
TPU injection molding is the process of creating molded components from TPU material using specialized machines. The process involves melting TPU pellets and injecting the molten material into a mold cavity, where it solidifies into the desired shape. TPU’s unique properties, including flexibility and resilience, make it ideal for a wide range of products.

Key Characteristics of TPU
Property | Description | Examples of Use |
Elasticity & Flexibility | Combines rubber-like elasticity with plastic toughness. | Shoe soles, watch straps |
Chemical Resistance | Resists oils, greases, and many chemicals. | Automotive seals, gaskets |
Durability | Performs well in harsh environments, offering long life. | Industrial belts, cables |
Transparency | Available in clear grades for aesthetic applications. | Phone cases, medical devices |
Wide Hardness Range | Can range from soft to rigid depending on formulation. | Protective covers, tubing |
Benefits of TPU Injection Molding

1. Versatility in Product Design
TPU’s ability to form complex shapes and structures makes it suitable for innovative designs.
2. High Strength-to-Weight Ratio
Products molded from TPU are lightweight yet durable, which is critical for industries like automotive and electronics.
3. Cost-Effectiveness
TPU injection molding is efficient for mass production, reducing material wastage and overall costs.
4. Enhanced Aesthetic Options
Its ability to produce clear or colored parts enhances product aesthetics.
5. Eco-Friendly Options
Recyclable grades of TPU are available, supporting sustainable manufacturing practices.
The TPU Injection Molding Process
1. Material Preparation
TPU pellets are dried to remove moisture, as it can affect the molding process and product quality.
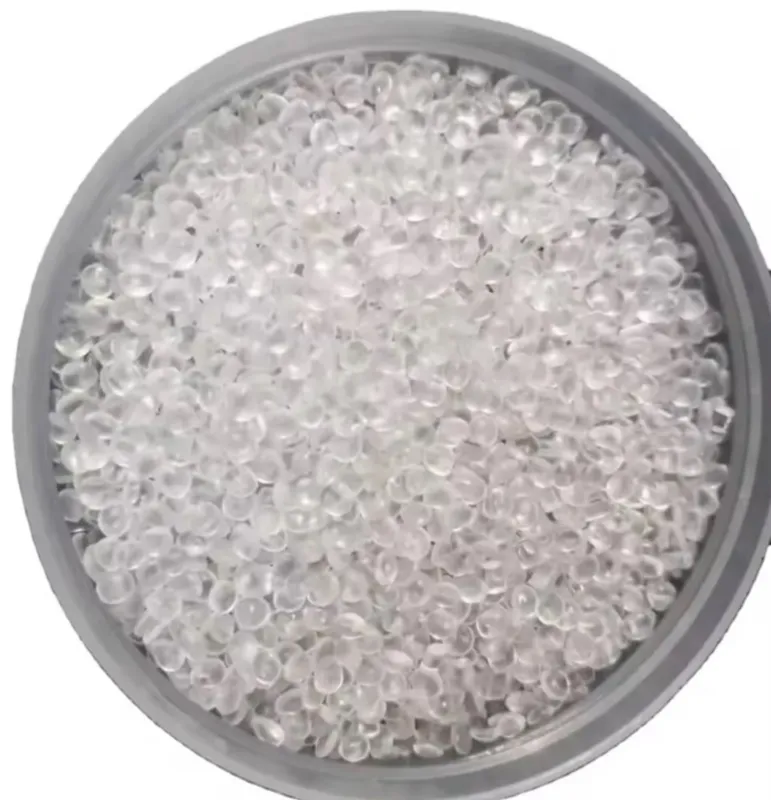
2. Melting the TPU
The TPU pellets are heated in the injection molding machine’s barrel until they reach a molten state.
3. Injection into Mold Cavity
The molten TPU is injected under high pressure into a pre-designed mold cavity.
4. Cooling and Solidification
The material cools and solidifies within the mold, taking the shape of the cavity.
5. Ejection and Finishing
The molded part is ejected from the mold and undergoes post-processing as needed, such as trimming or polishing.
Comparison of TPU with Other Materials
Feature | TPU | PVC | Silicone |
Elasticity | Excellent | Moderate | High |
Durability | Very High | High | Moderate |
Chemical Resistance | Resistant to oils & chemicals | Good | Excellent |
Temperature Range | -40°C to 80°C | -10°C to 60°C | -50°C to 250°C |
Recyclability | Recyclable | Limited | Not Easily Recyclable |
Common Challenges in TPU Injection Molding and Solutions
1. Material Moisture Sensitivity
- Challenge: TPU absorbs moisture, leading to defects like bubbles and voids.
- Solution: Proper drying of TPU pellets before molding.
2. Processing Temperature Control
- Challenge: TPU’s narrow processing temperature range can cause degradation.
- Solution: Use advanced machines with precise temperature controls.
3. Mold Design Complexity
- Challenge: TPU’s elasticity makes mold design challenging.
- Solution: Work with experienced mold designers to optimize cavity design.
4. Part Shrinkage
- Challenge: TPU parts may shrink inconsistently after molding.
- Solution: Account for shrinkage in the design and use cooling techniques.
Applications of TPU Injection Molding
1. Automotive Industry
TPU is used for flexible components like seals, gaskets, and protective covers due to its durability and resistance to oil and abrasion.
2. Consumer Goods
Products like phone cases, watch bands, and sportswear components benefit from TPU’s flexibility and aesthetic qualities.
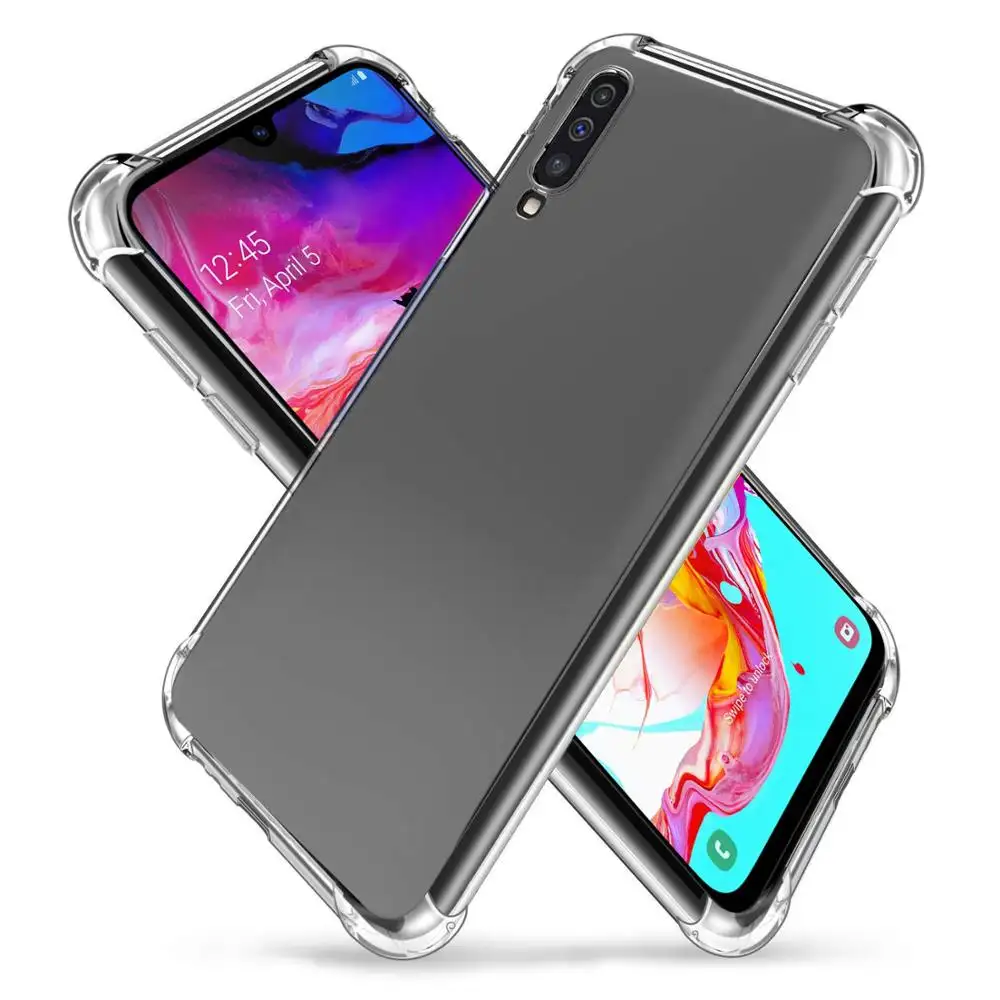
3. Medical Industry
Biocompatible grades of TPU are used for medical devices, tubing, and protective equipment.
4. Industrial Equipment
TPU is ideal for cable jackets, conveyor belts, and other industrial parts requiring resilience and wear resistance.
5. Footwear Industry
Shoe soles and inserts leverage TPU’s elasticity, comfort, and durability.
Why TPU is a Preferred Material for Injection Molding
1. Customizable Properties
TPU’s properties can be tailored by adjusting its composition, making it versatile for various applications.
2. Sustainability Options
Recyclable TPUs contribute to environmentally responsible manufacturing practices.
3. Compatibility with Multi-Material Molding
TPU can be combined with other materials for overmolding or multi-component products.
Working with BFY Mold for TPU Injection Molding
At BFY Mold, we specialize in delivering high-quality TPU injection molding solutions for diverse industries. With years of experience and advanced technology, we ensure precision and consistency in every project.
Our Services Include:
- Injection Molding Processing: Crafting products from TPU and other materials.
- Mold Manufacturing: Designing and fabricating custom molds for precise production.
- Mass Production: Efficiently handling large-scale orders.
- On-Demand Production: Catering to small batches and custom requests.
- CNC Machining and Mirror Spark: Enhancing mold precision and surface finishes.
Why Choose BFY Mold?
- State-of-the-Art Factory: Equipped with advanced machinery for high-quality production.
- Skilled Team: Experienced professionals committed to meeting customer needs.
- Quality Assurance: Stringent quality control processes to deliver defect-free products.
Conclusion
TPU injection molding offers unmatched flexibility, durability, and design possibilities, making it a go-to manufacturing solution across industries. By understanding the material’s properties, benefits, and challenges, businesses can leverage TPU’s potential for innovative and high-quality products. Partnering with an expert manufacturer like BFY Mold ensures the success of your TPU injection molding projects.