1. What Is Wire EDM Cutting?
Wire Electrical Discharge Machining, often called Wire EDM, is one of the most accurate manufacturing processes. It’s known for creating complex shapes with high levels of detail at tight tolerances. Unlike some other cutting methods, wire EDM is free of direct mechanical contact, making it appropriate to machine hard materials and intricate parts that are more sensitive to distortion that can occur with machine tools.
In this article, we will discuss the principles of Wire EDM, the materials it can cut, its advantages, and the various applications it is used for. Then we will look at how Wire EDM compares to other types of EDM and its role in the precision machining space.
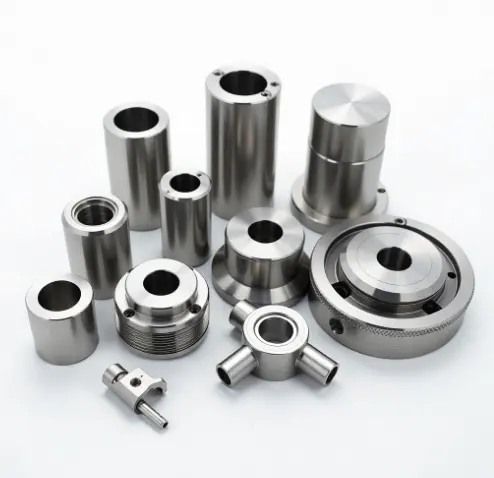
2. What Is Wire EDM?
However, wire EDM utilizes a thin brass wire as the electrode for Electrical Discharge Machining (EDM) to erode material from the workpiece. The wire is accurately traversed around the material based on a programmed path, which erodes the material system into the needed shape or design. Common applications of this process include cutting hard metals, complex shapes, and fine details.
The process works by firing quick electrical jolts between the wire and the material. These discharges produce heat to melt and vaporize the material in the cut path. The spent material is then washed away by a constant dielectric fluid flow.
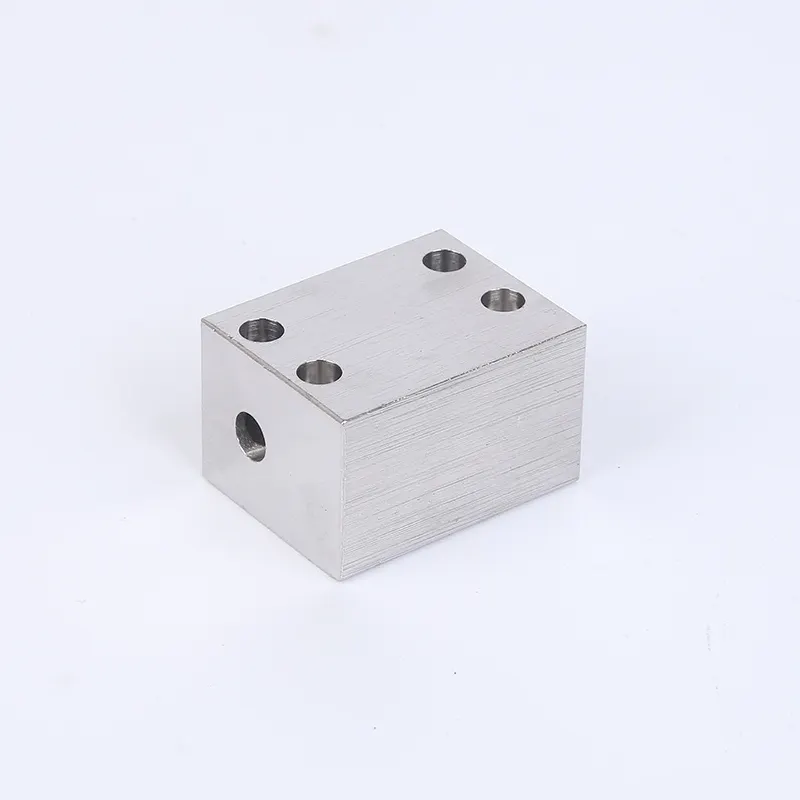
3. How Does Wire EDM Work?
There are several stages to the Wire EDM cutting process including:
As is the workpiece is fixed on a CNC and the wire is aligned. Usually, the wire is placed between two electrodes, and it goes through the workpiece and continues eroding it from the inside.
Electrical Discharge: An electric charge is transferred between the wire and the workpiece producing a succession of sparking. The sparks then melt and vaporize the material along a predetermined cutting path.
Cooling and Flushing: A dielectric fluid, usually deionized water or oil, circulates through the cutting zone to cool the workpiece and remove debris.
Making the Cut: The wire, controlled by a CNC machine, moves along the programmed path to cut the part into the desired features or shapes. As there is no direct contact with the workpiece, the chances of distortion or tool wear are very low.
4. Key Components of a Wire EDM Machine
The Wire EDM Machine includes various parts that we will see how they function to make the cut precise:
- Wire: A fine, electrically conductive (typically brass or copper) wire that functions as the cutting implement.
- CNC Control: Computer numerical control (CNC) system that accurately guides the wire along the escape path.
- Workpiece: The piece that is being cut, generally metal or alloy.
- Dielectric Fluid: fluid (like deionized water) that cools the workpiece and takes away the eroded material.
- Power Supply: Provides the cutting electrical discharges.
The interaction of these elements allows Wire EDM to produce very precise cuts, even in hard or conductive materials, such as titanium, stainless steel, and hard alloys.
5. Materials Used in Wire EDM
The material processing ability of wire EDM is highly versatile. It works especially well for slicing through hard metals and alloys, such as:
- Tool Steel
- Titanium
- Stainless Steel
- Copper
- Brass
- Aluminum
- Carbon Steel
- Inconel

Wire EDM is equally effective on non-metallics, from graphite to ceramics, making it a versatile solution in industries ranging from aerospace to automotive to medical.
6. Tolerance in Wire EDM

Wire EDM has significant benefits, one being an enhanced tolerancing capability. Tolerances as tight as ±0.001 mm (0.00004 inches) can be achieved, depending on the machine and skill of the operator. This degree of precision is vital in industries where parts must meet exact specifications, including the aerospace and medical fields.
Because of its inherent precision, Wire EDM is the go-to process when tight tolerances are required, especially for complex features or difficult-to-machine materials.
7. Benefits of Wire EDM Cutting
Wire EDM has some substantial advantages over other machining techniques:
Wire EDM can cut veins and other shapes with tight tolerances, making it great for complex and intricate designs.
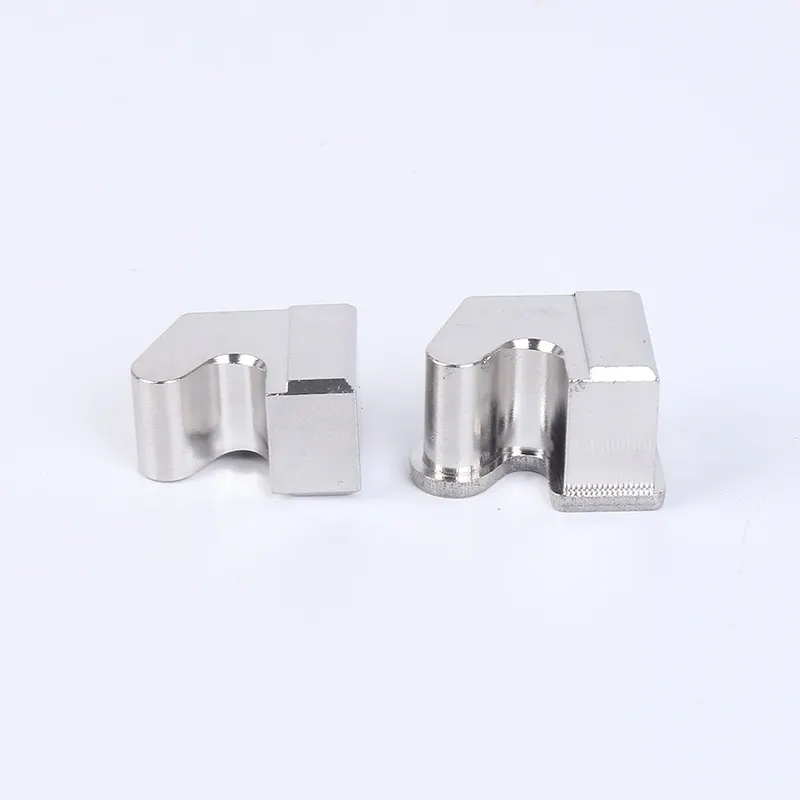
- No Wear in Tool: As there is no actual contact of a wire with the material, there is no wear and no dulling of the tool that may require expensive replacements.
- Capability for Cutting Difficult Materials: The wire EDM process can be used to cut hard materials such as hardened steel, titanium, and various alloys that may be hard to machine using conventional tools.
- Complex Geometries: Wire EDM excels at machining parts with complex geometries, tight tolerances, or manageable features that might be unachievable by other methods.
- Minimal Material Distortion: Since no physical cutting force is involved, the material is less likely to distort, making Wire EDM suitable for sensitive components.
8. Widespread Applications of Wire EDM
Due to its precision and ability to cut complex geometries, wire EDM is used in a variety of industries. Common applications include:
- Aerospace: Creating high-accuracy components like turbine blades, nozzles, and engine parts.
- Medical Devices: Developing exacting, fine parts for surgical instruments and implants.
- Tool and Die Making Producing molds dies, and other tooling with complex features
- Cutting automotive parts such as transmission gears, fuel injectors, and other components with extreme precision.
- Electronics: Anode parts, semiconductors, connectors, and other parts.
9. Wire EDM vs Traditional EDM: Key Differences
Wire EDM and traditional EDM both fall under the same general category of Electrical Discharge Machining, but they operate in different ways. Here’s a comparison:
Feature | Wire EDM | Traditional EDM (Sinker EDM) |
Cutting Method | Uses a wire electrode to cut the material. | Uses a shaped electrode to erode the material. |
Precision | High precision with tight tolerances. | Suitable for rougher cuts with less precision. |
Material | Ideal for cutting thin, complex parts. | Better for larger, bulkier parts. |
Shape Complexity | Can cut complex shapes and thin sections. | Limited to simple shapes or cavities. |
Speed | Slower compared to other machining methods. | Faster for rough cutting. |
10. Other Types of EDM Processes
In addition to Wire EDM, there are several other EDM processes widely utilized in precision machining:
- Sinker EDM: More commonly known as traditional EDM, this method utilizes a shaped electrode to remove material to create cavities; it is commonly used for mold and die production.
- EDM Hole Drilling: Similar to a wire EDM process but is used to make small, accurate holes in hard materials.
- Laser EDM: A type of EDM that uses laser energy to erode the material, commonly used for extremely hard metals or creating detailed cutouts.
Each type of EDM process has strengths depending on the material, complexity of the design, and production number.
11. Conclusion
Wired EDM cutting is a very versatile and accurate manufacturing process that has many advantages such as high precision, little wear of tools, as well as the ability to cut hard materials and complex shapes. Its uses include aerospace, medical devices automotive, and others. Wire-EDM is a reliable solution for challenging designs or difficult materials to produce high-quality, accurate parts.
12. About BFY Mold: Your Partner in Precision Manufacturing
At BFY Mold, we specialize in high-precision injection molding, mold manufacturing, and a variety of CNC machining services. Our factory is equipped with cutting-edge technology, including Wire EDM, CNC processing, and mirror spark, ensuring that we deliver the best quality products to our clients.
Our main services include:
- Injection Molding and Mold Manufacturing: Custom solutions for different industries.
- Mass and On-Demand Production: Tailored to your production needs.
- CNC Processing and Mirror Spark: Offering precision machining for high-quality parts.
- Wire EDM and Precision Cutting: Creating complex, detailed parts with tight tolerances.
Trust BFY Mold for all your manufacturing needs, whether it’s for prototypes or large-scale production. We are committed to delivering the highest quality and precision for every project.