1. Polyphenylene Sulfide (PPS) Material Guide
Polyphenylene Sulfide (PPS) is a high-performance thermoplastic polymer with outstanding chemical resistance, dimensional stability, and thermal properties. It is used in applications that require durability, high thermal stability, and resistance to various harsh chemicals.
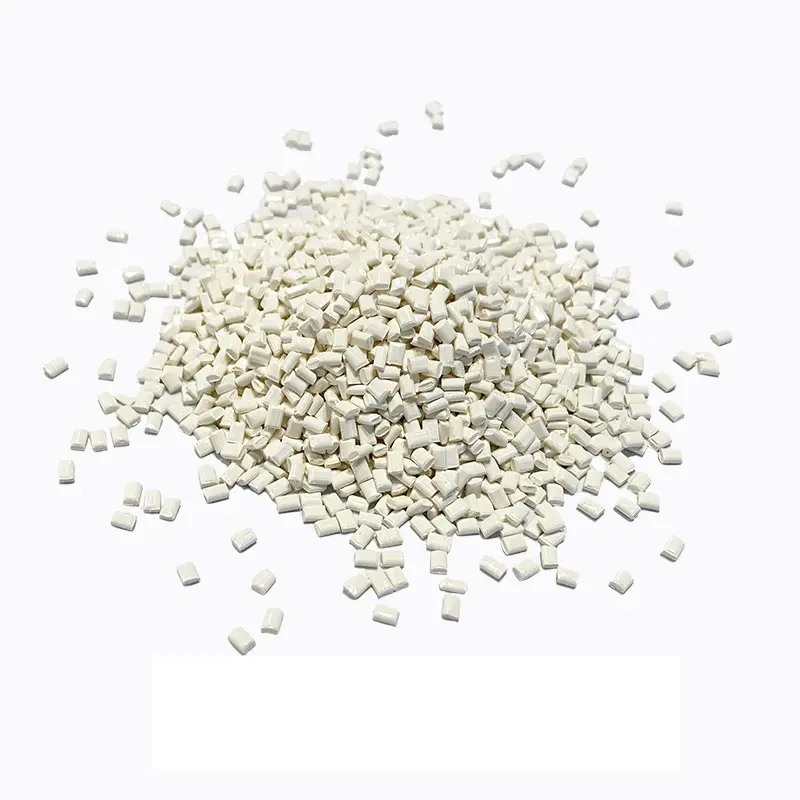
Key Features of PPS:
- Excellent Heat Resistance: PPS has excellent continuous temperature stability of up to 260°C (500°F), which is ideal for engineers in the automotive, aerospace, and industrial markets.
- Effective Chemical Resistance: It can resist many chemicals, acids, bases, and organic solvents.
- Low Shrinkage: The low shrinkage on the cooling of PPS provides dimensional accuracy and consistency.
- Electrical Insulator: PPS possesses excellent electrical insulation properties and finds applications in electronics and telecommunications.
Blends of PPS with glass fibers or other filler materials are commonly used to improve the material’s strength, stiffness, and other properties. Because of its versatility and performance characteristics, PPS is often the material of choice in many high-demand industries.
2. Key Characteristics of PPS Plastic
Knowledge of the specific features of PPS plastic is necessary for effective injection molding. PPS demonstrates high thermal stability, resistance to environmental factors, and mechanical properties.
Property | PPS Plastic |
Thermal Stability | Up to 260°C (500°F) |
Chemical Resistance | Excellent |
Mechanical Strength | High |
Electrical Insulation | Excellent |
Moisture Absorption | Low |
Shrinkage | Low |
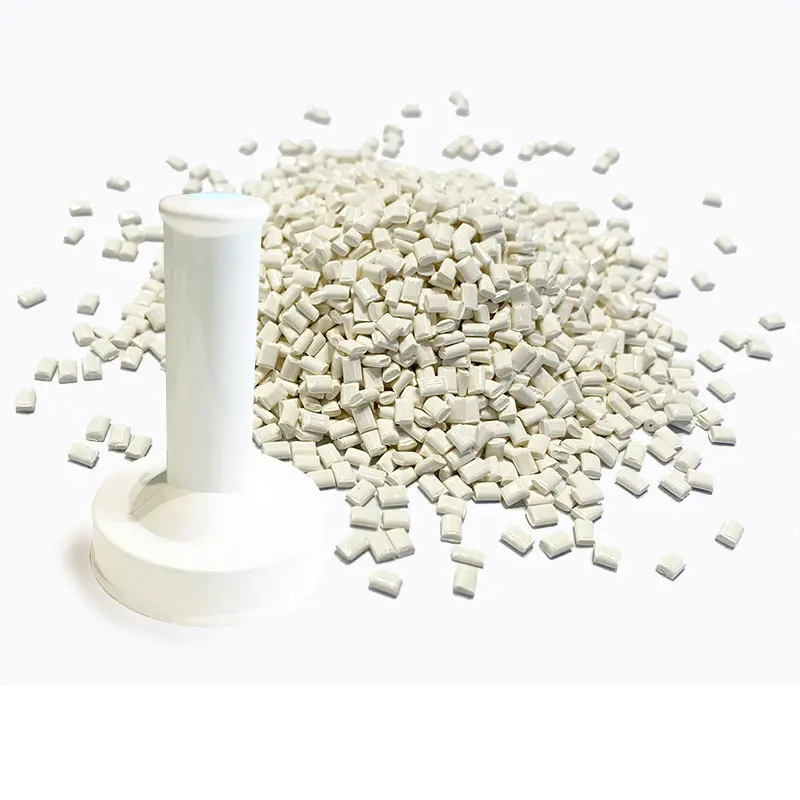
In-Depth Analysis:
- Thermal Stability: PPS is a game-changer in the automotive and aerospace sectors, where components face high-stakes environments. It can preserve structures at high temperatures.
- Chemical Resistance: PPS’s ability to resist corrosion and degradation caused by acids and solvents makes it suitable for chemical processing equipment and components used in harsh environments.
- Mechanical Strength: One key characteristic of PPS is its toughness and durability. It is also known for its high tensile strength and wear resistance, which are essential for parts subject to physical stress.
- Electrical Insulation: Due to its good dielectric properties, PPS is used in applications where electrical insulation is needed, such as connectors, switches, and capacitors.
3. Understanding the PPS Injection Molding Process
PPS injection molding is a versatile and efficient manufacturing process that produces complex parts using PPS resin. It involves several steps, from melting the material to cooling and ejecting the piece.
PPS Injection Molding Steps:
- Material Preparation: PPS resin is typically dried before molding to prevent moisture absorption, causing defects such as bubbles or discoloration.
- Heating: The PPS resin is heated to its melting point (about 280 °C-300 °C) in an injection molding machine.
- Injection: The molten PPS is injected into the mold cave using high pressure to form the desired part.
- Cooling: The mold is cooled, and the PPS solidifies into the shape of the mold.
- Ejection: Finally, once the part has cooled to a certain point, it is ejected from the mold, and the process begins again.
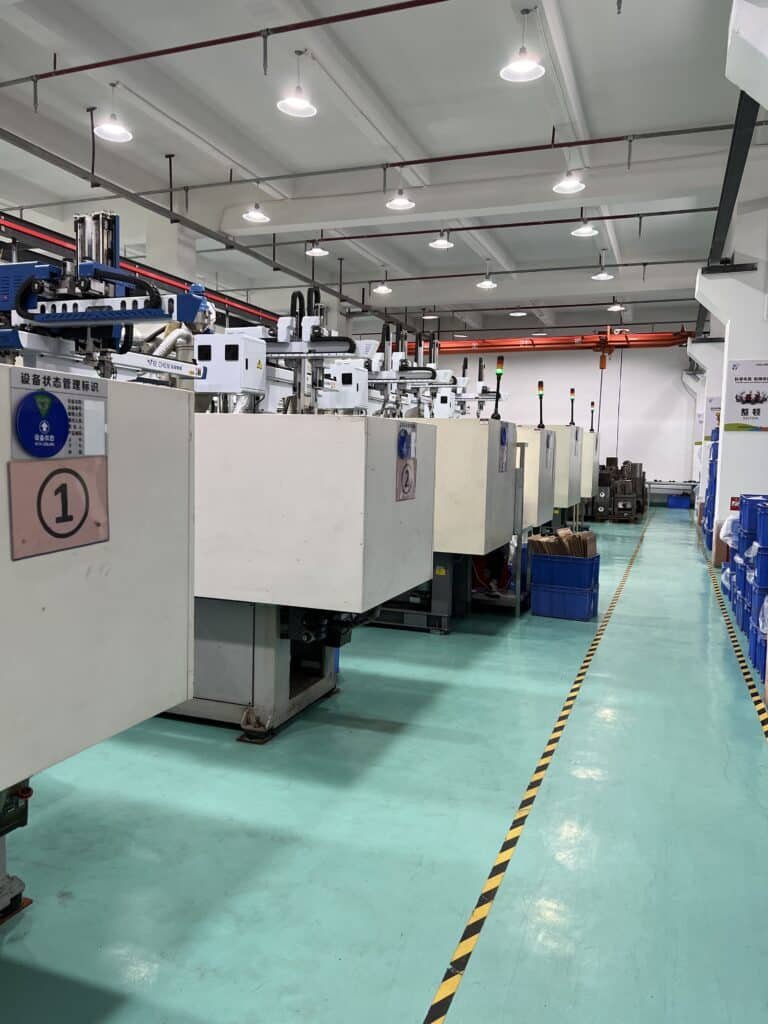
Molding Equipment:
- Injection Molding Machine: Dedicated apparatus that melts and injects PPS into the mold cavity.
- Molds: Molds, usually made of steel or aluminum, must withstand high pressures and temperatures. The quality of the final product is an important factor in designing a mold.
4. PPS Injection Molding Parameter Optimization
Process parameters must be optimized to achieve the best results when injecting PPS. Modifying the injection parameters, temperature, and cooling times can improve component quality and reduce defects.

Key Process Parameters:
- Injection Pressure: The pressure required for injecting PPS (polyphenylene sulfide) into the molding cavity is generally within 60-120 MPa, depending on the complexity of the part and material flow rate.
- Injection Temperature: To ensure a good material flow into the mold cavity, the recommended injection temperature for PPS is between 280°C and 300°C.
- Mold Temperature: Mold temperature is a key factor in part quality. A temperature of 80 °C-120 °C mold is used for cooling and shrinkage.
- Cooling Time: It can also cooperate, but primarily, the longer the cooling time, the more likely it will not deform and dimensional inaccuracy.
Optimizing Parameters:
For the best solutions, you should:
- Temperature Controllers to Keep Mold and Material Temperatures Stable
- Vary injection rates according to part complexity to minimize defects, such as voids or incomplete filling.
- Adjust cooling times to optimize between part quality and production efficiency.
5. Post-Processing Techniques for PPS Parts
Some components also require tolerance or surface quality, which is only achieved after the PPS injection molding process. Techniques used in post-processing can enhance and optimize functionality, aesthetics, or overall part performance.
Common Post-Processing Techniques:
Trimming: Byproducts from molded pieces are removed to maintain clean edges and smooth surfaces.
Annealing: It involves heating parts to a particular temperature and leaving them cool slowly to reduce internal stresses and improve dimensional stability.
Coating: PPS parts can also be coated or surface treated to improve wear resistance or appearance (e.g., painting, electroplating).
Based on the earlier definition, PPS naturally provides the following features: Assembly: PPS parts can be assembled with other components in some applications.
6. PPS Injection Molding: Key Applications
PPS injection molding is utilized in various industries requiring high-performance characteristics in demanding applications, including automotive, electronics, aerospace, and many others.
Applications Relative to the Industry:
- Automotive: Due to its excellent high-temperature and chemical resistance, PPS is used in various parts of the fuel system, sensors, electrical connectors, and other under-the-hood components.
- Electronics: Because of its excellent electrical insulation, PPS is a preferred option for connectors, housings, and insulators in the electronics industry.
- Aerospace: Due to its lightweight and toughness in extreme environments, PPS is frequently molded into parts that include brackets, housings, and structural components.
- Medical Devices: These are used in medical equipment housings and components requiring high chemical and thermal resistance, like diagnostic devices and sensors.
Specific Use Cases:
- Automotive Connectors: The high heat resistance and chemical durability of PPS make it ideal for use in electrical connectors in automotive applications.
- Power Electronics: The excellent dielectric properties of PPS find applications in power converters and circuit boards.
- Extruded industrial supplies: PPS manufactures pumps and valves in industrial settings because they can resist corrosive chemicals.
7. Four Key Points to Note in PPS Injection Molding
Although PPS is a great material for certain properties, injection molding must be done with care to avoid defects that can detract from part quality.
Key Considerations:
- Mold Design: Mold design is essential for consistent part quality, minimized warping, and uniform heating and cooling.
- Drying of the Material: PPS is hygroscopic, so it must be dried completely before molding to avoid defects caused by moisture absorption.
- Injection Speed: PPS has a high viscosity, so the injection speed must be controlled to avoid problems such as air traps or insufficient filling.
- Mold Wear: The two surfaces can wear out due to friction. High-grade steel or mold coatings extend the life of the mold.
Why Choose BFY Mold For PPS Injection Molding
BFY Mold is a trusted name in injection molding and mold manufacturing. With our own factory and cutting-edge equipment, we offer services such as mass production, on-demand production, CNC machining, and mirror spark processes. We specialize in providing high-quality, custom solutions to the automotive, medical, and electronics industries.
Services We Offer:
- Injection Molding & Mold Manufacturing
- Mass Production & On-Demand Production
- CNC Machining & Mirror Spark
- Tailored Solutions for Complex Parts