Introduction
Injection molding remains a cornerstone of modern manufacturing, but the choice between gas-assisted molding (GAM) and water-assisted molding (WAM) can dramatically impact production efficiency, material usage, and long-term costs.
While both technologies excel at creating hollow, lightweight plastic components, their cost-saving potential diverges based on factors like material selection, tooling complexity, energy consumption, and application-specific requirements. At BFY Mold, we recently partnered with an automotive client to reduce material waste by 30% using gas-assisted molding for air intake manifolds. This article comprehensively compares GAM and WAM, analyzing their technical mechanisms, cost structures, and ideal use cases to help manufacturers optimize their plastic part design and production workflows.
1. Process Mechanisms: How GAM and WAM Work
Gas-Assisted Molding (GAM)
Gas-assisted molding injects pressurized nitrogen gas into molten plastic to form hollow channels within the part. The process unfolds in three stages:
- Partial Polymer Injection: 80–95% of the mold cavity is filled with molten plastic.
- Gas Injection: Nitrogen gas displaces the molten polymer, creating hollow sections and reducing material usage.
- Cooling & Ejection: Gas pressure is maintained during cooling to minimize sink marks and warping.

Technical Advantages:
- Smooth internal surfaces with minimal residual stress.
- Reduced cycle times due to gas pressure aiding in cooling.
- Ideal for parts requiring aesthetic finishes (e.g., automotive interiors).
Water-Assisted Molding (WAM)
Water-assisted molding uses pressurized water instead of gas to displace molten plastic. The process includes:
- Full Polymer Injection: The mold cavity is completely filled with plastic.
- Water Injection: Water penetrates the molten core, forming hollow structures.
- Drainage & Cooling: Water is drained, and the part cools rapidly.
Technical Advantages:
- Faster cooling rates compared to GAM (water absorbs heat more efficiently).
- Higher dimensional stability for thick-walled components.
- Reduced risk of gas entrapment defects.
Key Differences:
- Residue Management: Gas leaves no residue, while WAM requires water drainage systems.
- Material Compatibility: WAM works best with high-viscosity polymers like PP and ABS, whereas GAM accommodates a broader range, including PC and POM.
2. Cost Analysis: Tooling, Materials, and Energy
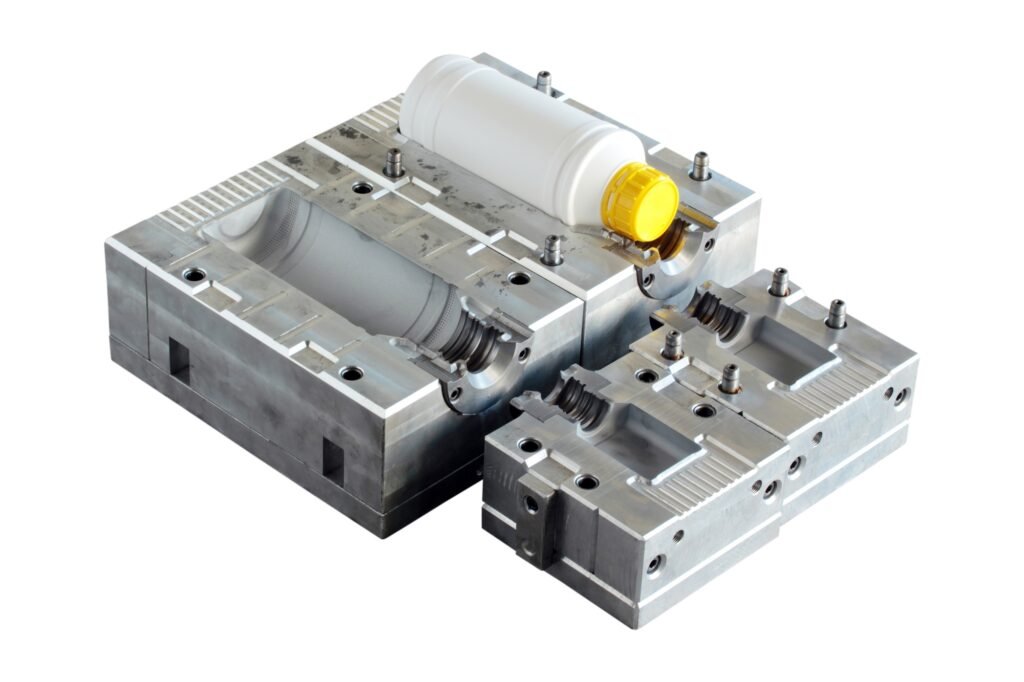
To quantify the financial implications of GAM and WAM, we analyzed four cost drivers across 15 industrial projects:
Factor | Gas-Assisted Molding (GAM) | Water-Assisted Molding (WAM) |
Tooling Cost | 45,000–70,000 | 60,000–90,000 (+20% for drainage) |
Material Savings | 25–35% (thinner walls) | 15–25% (requires higher viscosity) |
Energy Consumption | 12 kWh/kg | 18 kWh/kg (water pumping/heating) |
Cycle Time | 40–60 seconds | 30–45 seconds (faster cooling) |
Maintenance Cost/Year | $3,200 (gas valve upkeep) | $5,800 (corrosion-resistant upgrades) |
Case Study: BFY Mold’s Automotive Client
A European automotive supplier needed to reduce weight and material costs for air intake manifolds. After testing both methods:
- GAM Solution: Achieved 30% material savings by reducing wall thickness from 4mm to 2.8mm.
- WAM Attempt: Surface defects were caused due to rapid cooling with water.
- ROI: GAM tooling paid off in 14 months, saving $8,200/month in material costs.
3. Application Scenarios: When to Choose GAM or WAM
Gas-Assisted Molding (GAM)
- Automotive: Door handles, dashboards, and intake manifolds requiring smooth finishes.
- Consumer Electronics: Ergonomic tool grips with uniform wall thickness.
- Medical Devices: Hollow surgical instrument housings.
Water-Assisted Molding (WAM)
- Appliances: Washing machine tubs and dishwasher components need tight tolerances.
- Plumbing: Pipe fittings and valves requiring rapid cooling.
- Industrial Equipment: Thick-walled gear housings.

Decision Checklist:
- Part Complexity: GAM for intricate geometries; WAM for thick, simple shapes.
- Surface Finish: GAM for Class A surfaces; WAM for functional components.
- Volume: GAM for mid-volume (10k–50k units); WAM for high-volume (>100k).
4. Design Optimization Strategies
For GAM:
- Uniform Wall Thickness: Avoid abrupt changes to prevent gas channeling issues.
- Gas Channel Design: Use curved paths (not sharp corners) to ensure smooth gas flow.
- Material Selection: Opt for low-viscosity resins like ABS or PC-ABS blends.
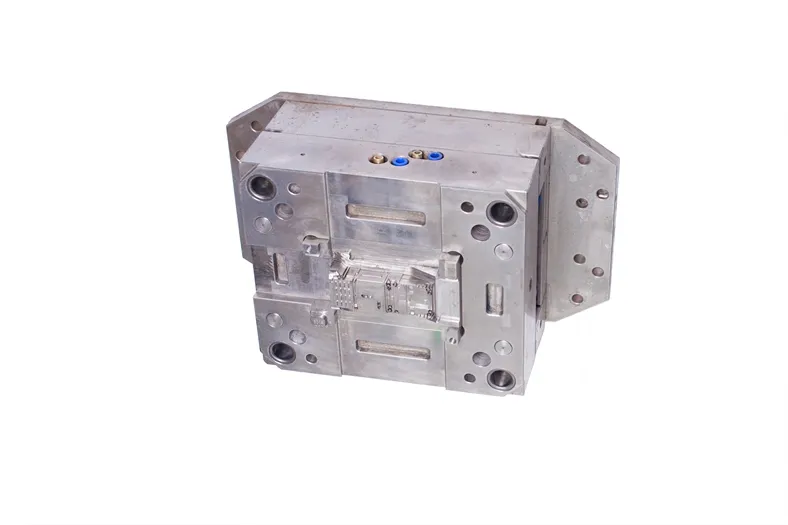
For WAM:
- Gate Positioning: Place gates near thick sections to optimize water penetration.
- Drainage System: Integrate angled channels to prevent water stagnation.
- Material Compatibility: Use high-melt-strength polymers (e.g., PP-HI) to resist water pressure.
Hybrid Approach:
BFY Mold’s hybrid solution for a smart home device client combined GAM for exterior aesthetics and WAM for internal structural ribs, cutting total costs by 18%.
5. Sustainability & Future Trends
Environmental Impact:
- GAM: Reduces material waste but relies on nitrogen gas (non-renewable).
- WAM: Water is recyclable, but energy-intensive heating/pumping increases carbon footprint.
Emerging Innovations:
- AI-Driven Process Control: Sensors adjust gas/water pressure in real time to minimize defects.
- Bio-Based Polymers: These are compatible with GAM/WAM to meet circular economy goals.
Regulatory Considerations:
- EU Standards: WAM may require wastewater treatment certifications.
- Automotive ISO 14001: GAM’s material efficiency aligns with sustainability mandates.
6. Common Pitfalls & Troubleshooting
GAM Challenges:
- Gas Leaks: Caused by worn seals; inspect valves quarterly.
- Surface Splay: Moisture in resin; pre-dry materials to <0.02% humidity.
WAM Challenges:
- Corrosion: Use stainless steel molds or apply anti-corrosion coatings.
- Incomplete Drainage: Optimize drainage angles and cycle timing.
Preventive Measures:
- Conduct mold flow simulations (e.g., Moldflow) before production.
- Partner with material suppliers for viscosity-specific recommendations.
7. Industry Insights & Data
- Market Growth: The gas-assisted molding market is projected to grow at 6.2% CAGR (2023–2030), driven by automotive lightweighting (Grand View Research).
- Energy Trends: WAM consumes 35% more energy than GAM but achieves 20% faster cycle times (Plastics Today).
Conclusion
Gas-assisted and water-assisted molding offers unique advantages, but the optimal choice hinges on your project’s technical requirements, volume, and sustainability goals. GAM excels in reducing material waste for complex, aesthetic parts, while WAM delivers precision for high-volume, thick-walled components.
For tailored solutions, explore BFY Mold’s gas-assisted molding services or dive into our case study library to see how we’ve optimized costs for global clients.
By aligning technology with application needs, manufacturers can achieve 20–30% cost reductions while meeting evolving industry standards.