In the vast realm of manufacturing, the choice between injection molding and casting holds significant implications for product development and production efficiency. Both processes play pivotal roles in shaping a myriad of products we encounter daily, from intricate plastic components to metal alloys with complex geometries. Let’s delve into the depths of Injection Molding and Casting, dissecting their processes, applications, and nuances.
Understanding Injection Molding
Injection molding is a versatile and widely used manufacturing process, particularly in the production of plastic components. The process involves injecting molten material, usually thermoplastics, into a mold cavity. The material then solidifies, taking the shape of the mold. This method excels in producing large quantities of identical, high-precision components with intricate details.
Advantages of Injection Molding
High Precision and Detail
Injection molding allows for the creation of intricate and highly detailed components, making it ideal for products requiring precision and complexity.
High Production Speed
The automated nature of injection molding machines ensures rapid production cycles, making it an efficient choice for mass production.
Material Variety
Injection molding supports a wide range of materials, including various thermoplastics, making it adaptable to diverse product requirements.
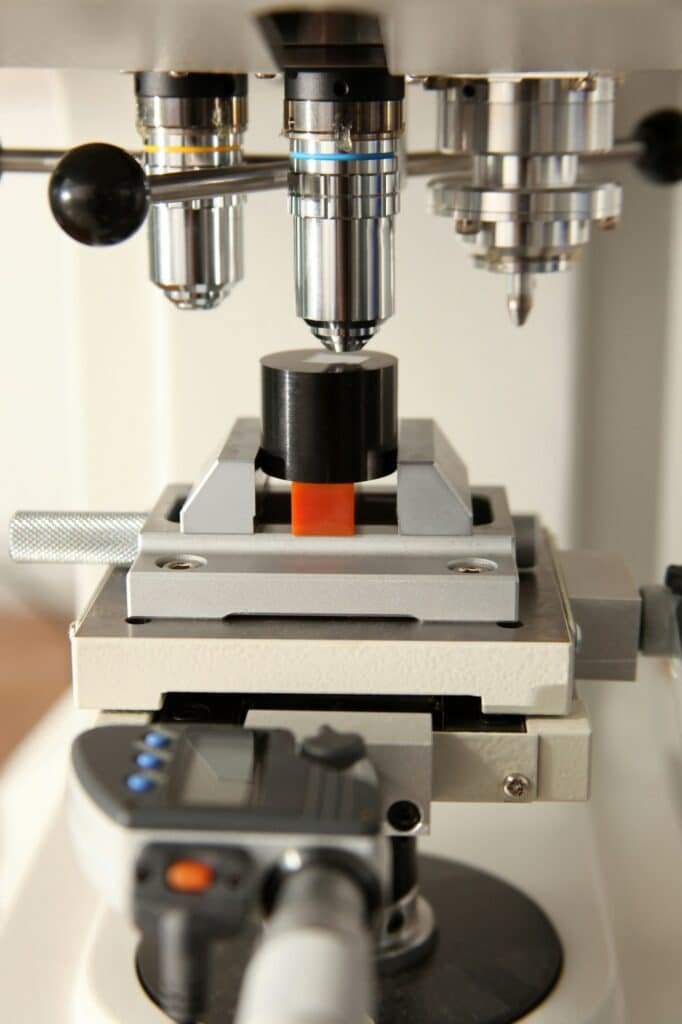
Understanding Casting
Casting, on the other hand, is a more traditional manufacturing method that has been used for centuries to create metal components. The process involves pouring molten material, such as metal or resin, into a mold. Once the material solidifies, the mold is opened, revealing the final product. Casting is known for its versatility, especially in the production of complex metal parts.
Advantages of Casting
Versatility in Material Choices
Casting supports a broad spectrum of materials, from metals like aluminium and bronze to resins and rubber, offering flexibility in material selection.
Low Tooling Costs
Unlike injection molding, casting molds are often less expensive, making it a cost-effective solution for smaller production runs or prototypes.
Complex Geometries
Casting excels in producing components with intricate and complex shapes, allowing for the creation of highly detailed and customized products.
Comparative Analysis
Cost Considerations
Injection molding is generally more cost-effective for large production runs due to its automated processes and faster cycle times. On the other hand, casting can be more economical for smaller runs or prototypes, where lower tooling costs offset the slower production speed.
Material Selection
While both processes offer versatility in material choices, injection molding leans towards thermoplastics, while casting embraces a broader range, including metals and various resins. The choice depends on the specific properties required for the end product.
Production Speed
Injection molding takes the lead in terms of production speed, making it ideal for industries where quick turnaround times are crucial. Casting, with its slower cooling and solidification processes, may be preferred for projects prioritizing customization over speed.
Conclusion
In the ever-evolving landscape of manufacturing, the choice between injection molding and casting hinges on the unique requirements of each project. Both processes bring distinct advantages to the table, catering to different scales of production, material needs, and design intricacies. As technology advances, these methods continue to shape the products we interact with daily, proving that the art of manufacturing is a dynamic journey with no one-size-fits-all solution.