In the dynamic landscape of manufacturing, non-standard customization has emerged as a revolutionary concept, reshaping the way products are designed and produced. This innovative approach to customization goes beyond traditional limits, allowing for unique modifications that cater to individual preferences. As we delve into the intricacies of non-standard customization, we will explore its impact on a fundamental manufacturing process: injection molding.
Defining Non-Standard Customization:
Non-standard customization is a paradigm shift in the customization spectrum, redefining how products are tailored to meet individual preferences. Unlike standard customization, which typically involves choosing from pre-set options, non-standard customization allows consumers to make unique and unconventional modifications to a product. It is a creative and innovative process that empowers individuals to express their uniqueness, transcending the limitations of mass production.
Understanding the Injection Molding Process:
Before delving into the impact of non-standard customization on injection molding, it’s essential to understand the basics of this widely used manufacturing process. Injection molding is a technique where molten material, usually plastic, is injected into a mold cavity. Once the material solidifies, the mold opens, and the finished product is ejected. This method is known for its efficiency, precision, and ability to produce high volumes of identical components.
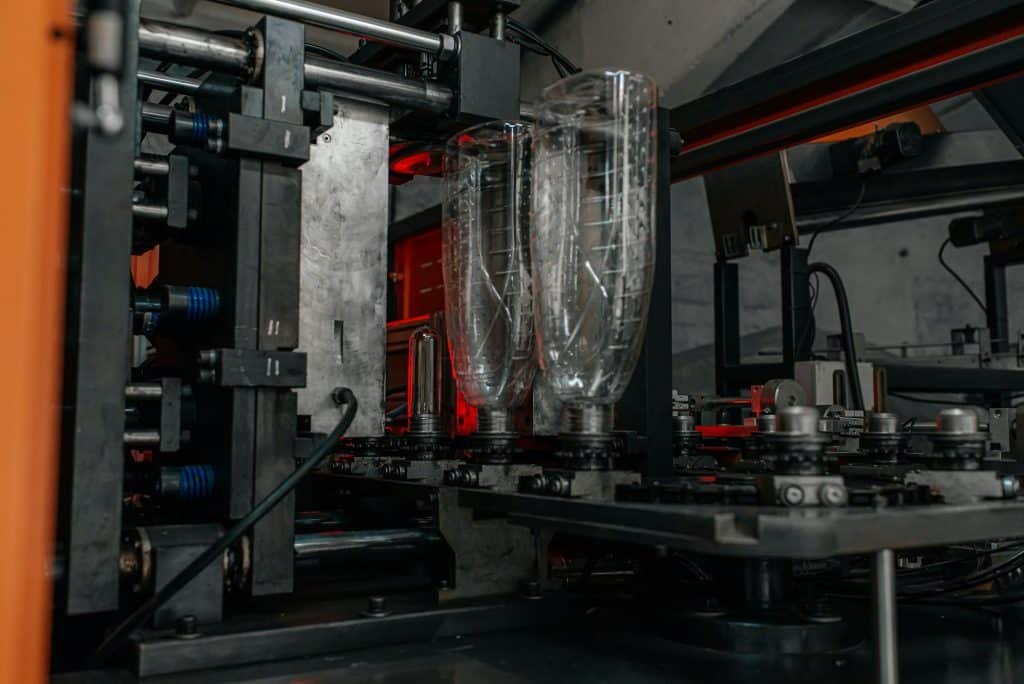
The Impact of Non-Standard Customization on Injection Molding:
1. Increased Complexity in Mold Design:
One of the significant impacts of non-standard customization on injection molding is the increased complexity in mold design. Traditionally, injection molding involves creating molds based on standardized designs for mass production. However, non-standard customization demands molds that can adapt to various unique shapes, sizes, and features. This complexity necessitates advanced engineering capabilities and a flexible approach to mold design.
2. Flexibility in Material Selection:
Non-standard customization often involves a diverse range of materials to meet specific design requirements. This flexibility in material selection presents challenges for injection molding, as different materials may have distinct processing requirements. Manufacturers must adapt their injection molding parameters to accommodate this diversity, ensuring that the final product meets the desired specifications.
3. Balancing Precision and Efficiency
Precision is paramount in injection molding, and non-standard customization introduces a delicate balance between precision and efficiency. Maintaining efficient production processes becomes a critical challenge as molds become more intricate to meet diverse customization needs. Striking the right balance ensures the injection molding process remains cost-effective while delivering high-quality, customized products.
4. Technological Advancements
The impact of non-standard customization on injection molding has driven technological advancements within the industry. Innovations such as computer-aided design (CAD) and computer-aided manufacturing (CAM) play a pivotal role in creating sophisticated molds that can cater to the intricacies of non-standard customization. Real-time monitoring and control systems have also been integrated to enhance the precision and efficiency of the injection molding process.
5. Quality Assurance Challenges
Non-standard customization introduces challenges in quality assurance, as each customized product may have unique specifications. Ensuring that the final products meet the required standards becomes a meticulous process, demanding thorough testing and inspection procedures. Manufacturers must implement stringent quality control measures to guarantee the integrity of customized components.

Benefits and Challenges:
1. Benefits
a. Diversification of Product Offerings:
Non-standard customization allows injection molding companies to diversify their product offerings, catering to a broader range of consumer preferences.
b. Market Differentiation:
Businesses that embrace non-standard customization can differentiate themselves in a competitive market, attracting customers seeking unique and personalized components.
c. Technological Innovation:
The challenges posed by non-standard customization drive technological innovation in the injection molding industry, leading to advancements that benefit the entire manufacturing sector.
2. Challenges
a. Higher Initial Costs:
The adoption of non-standard customization often involves higher initial costs due to the need for advanced mold designs and materials.
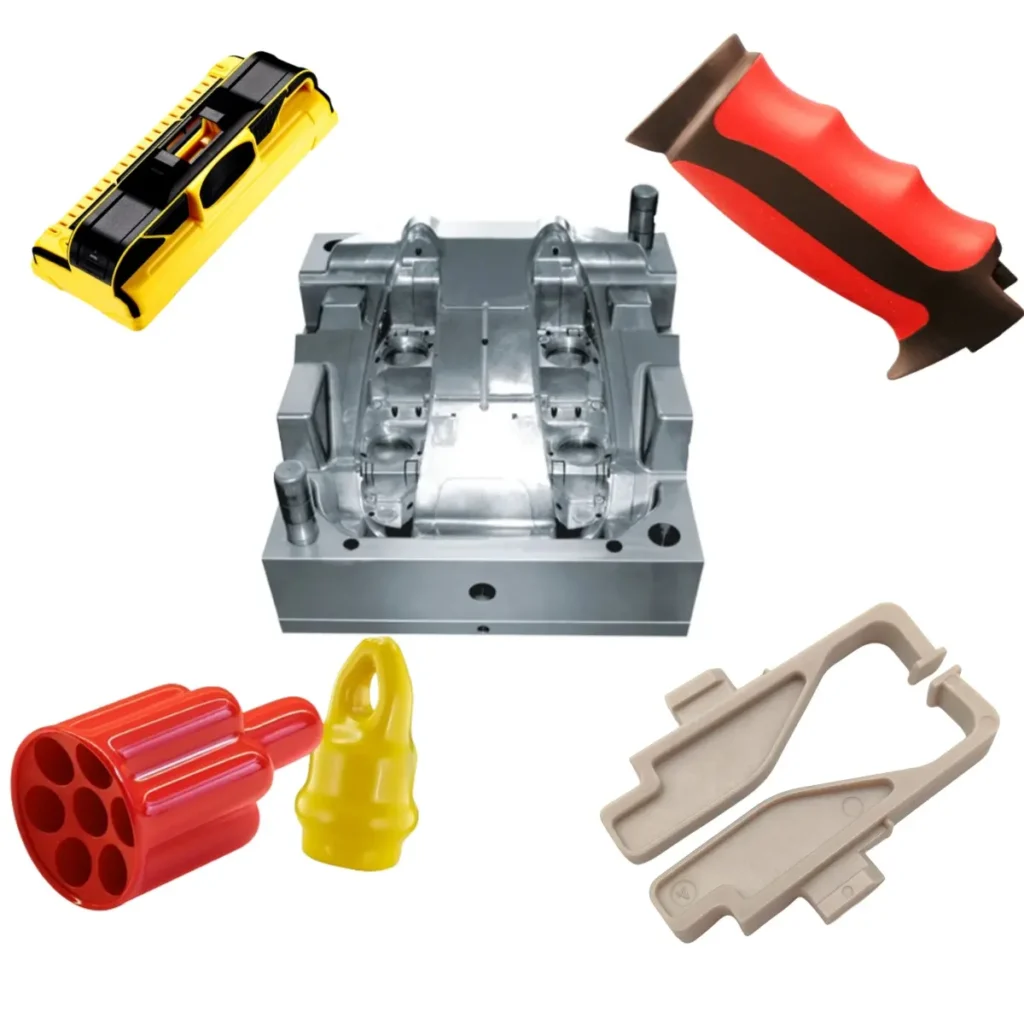
b. Extended Production Times:
The complexity of customized molds may lead to extended production times, challenging manufacturers to balance customer expectations with operational efficiency.
c. Skilled Workforce Requirements:
Non-standard customization demands a skilled workforce capable of handling complex mold designs and adapting to evolving technological trends. Ensuring a skilled workforce is crucial for the success of injection molding in the era of customization.
Conclusion
Non-standard customization is revolutionizing manufacturing by providing a platform for creative expression and individuality. Its impact on the injection molding process is both transformative and challenging, pushing the boundaries of traditional production methods. As the industry adapts to meet the demands of customized manufacturing, the benefits of diversification and market differentiation outweigh the challenges, propelling injection molding into a new era of technological innovation and consumer-centric production. As we move forward, the synergy between non-standard customization and injection molding promises a future where creativity and efficiency coexist, shaping the way we design and produce customized products.