During the injection molding process, how to deal with the high temperature of the injection molding machine, you need to understand its harm and learn how to deal with it.
If the temperature rise of the injection molding machine is too high, there are five major hazards: mechanical thermal deformation, the viscosity of the oil is reduced, the rubber seal is deformed, the oil oxidation is accelerated, and the component pressure of the air is reduced.
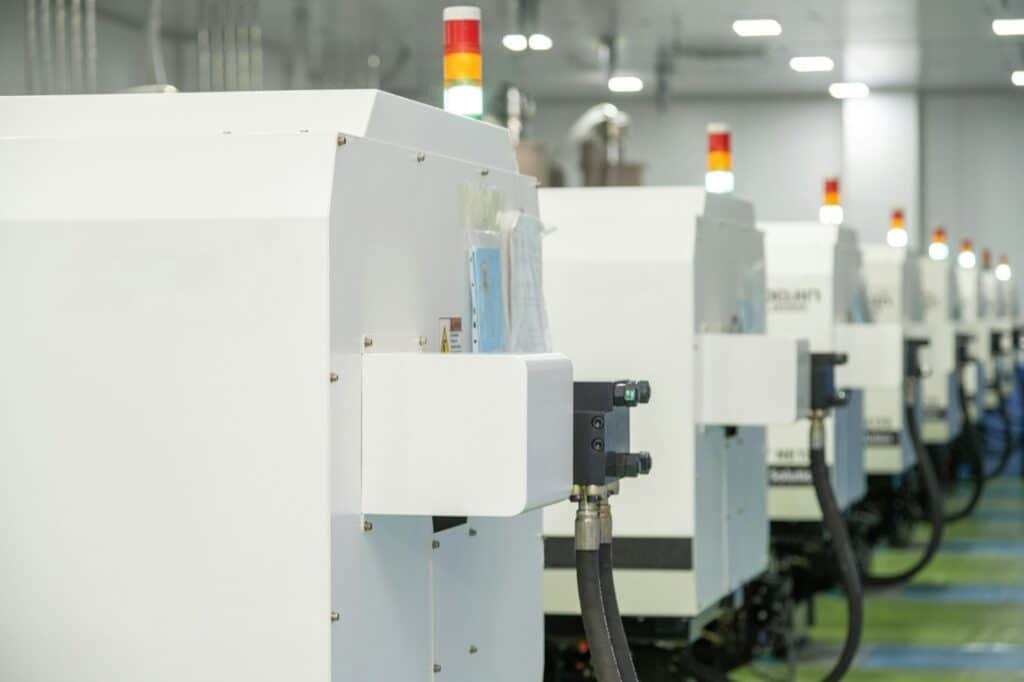
Hazards of high temperatures in the production
Thermal deformation of machinery
The moving parts with different thermal expansion coefficients in the hydraulic components are stuck because of the smaller matching gap, which causes the action failure, affects the transmission accuracy of the hydraulic system, and leads to the poor working quality of the parts.
Reduce the viscosity of the oil
The high-temperature rise of the injection molding machine will cause the viscosity of the oil to decrease, the leakage will increase, and the volumetric efficiency of the pump and the efficiency of the entire system will be significantly reduced. As the viscosity of the oil decreases, the oil film of moving parts such as the slide valve becomes thinner and cut, and the friction resistance increases, resulting in increased wear.
Deform the rubber seal
High temperature rise of injection molding machine will deform rubber seals, accelerate aging failure, and reduce sealing performance and service life, resulting in leakage.
Accelerate oil oxidation deterioration
The high-temperature rise of the injection molding machines will accelerate the oxidation and deterioration of oil, precipitate asphalt substances, and reduce the service life of hydraulic oil. The precipitates clog the damping holes and slot valve ports, resulting in the pressure valve being stuck and unable to operate, and the metal pipeline stretched and bent and even broken.
The working quality of the components deteriorates
The high-temperature rise of the injection molding machine will cause the working quality of the components to deteriorate, and the dissolved air in the oil will escape, resulting in air pockets, which will reduce the working performance of the hydraulic system.
The ideal operating temperature of the hydraulic system should be between 45 degrees and 50 degrees because the hydraulic system is designed according to a selected pressure oil viscosity. However, the viscosity will change with the oil temperature, which will affect the working components in the system, such as cylinders and hydraulic valves. It is easy to reduce the control accuracy and response sensitivity, especially for precision injection machines. At the same time, too high a temperature will also accelerate the aging of the seal to harden and break.
If the temperature is too low, the processing energy consumption is large, so the running speed is reduced. Therefore, it is necessary to pay close attention to the working temperature of hydraulic oil. The reasons for the high oil temperature are various, but most of them are attributed to the failure of the oil circuit or the failure of the cooling system.
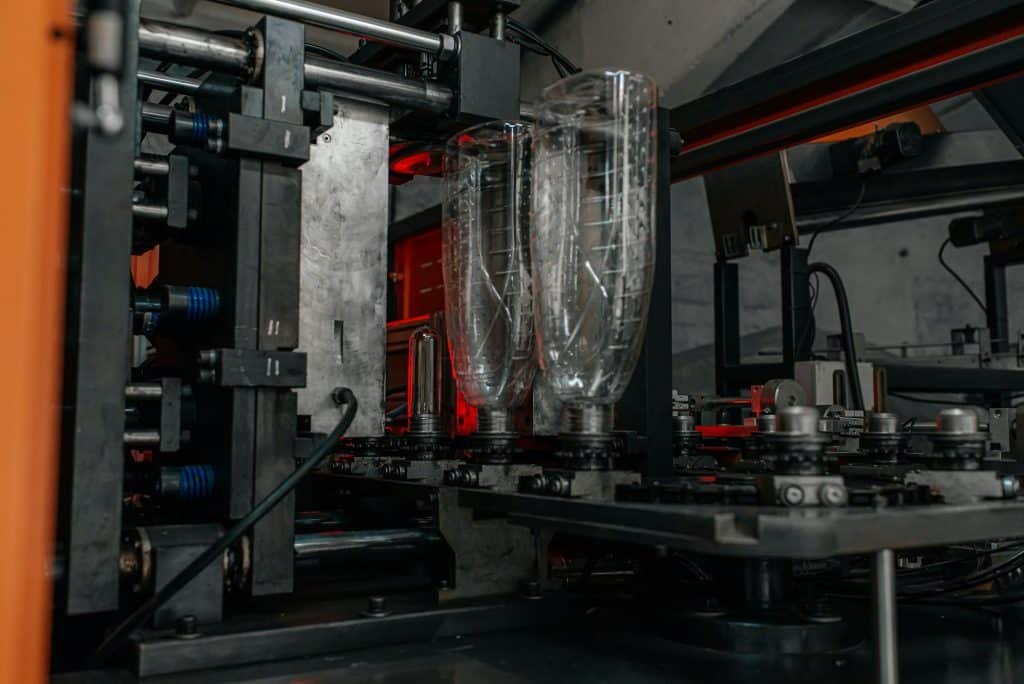
Injection molding machine overheat treatment method
(1) According to different load requirements, often check and adjust the pressure of the relief valve to make it just right.
(2) Reasonable selection of hydraulic oil, especially oil viscosity, in the case of conditions, as far as possible to use a lower viscosity to reduce viscosity friction loss.
(3) Improve the lubrication conditions of moving parts to reduce friction loss, which is conducive to reducing the workload and reducing heat.
(4) Improve the assembly quality and accuracy of hydraulic components and hydraulic systems, strictly control the matching gap of mating parts, and improve lubrication conditions. The sealing material with a small friction coefficient and the improved sealing structure are used to reduce the starting power of the hydraulic cylinder as much as possible to reduce the heat generated by the mechanical friction loss.
(5) Add cooling devices if necessary.