Injection molding transparent products—such as optical lenses, medical device housings, or consumer packaging—demands meticulous attention to material purity, process precision, and surface finish integrity. Even minor imperfections like bubbles, flow marks, or haze can render products unusable, making every stage from material preparation to mold design critical.
This guide breaks down seven non-negotiable factors, including advanced drying protocols, mold temperature control, and optical-grade polishing techniques, to ensure crystal-clear results. Whether producing PMMA or polycarbonate components, these strategies minimize rework and align with industry standards for transparency and durability.
Surface Finish Standards for Transparent Product Clarity
Transparent plastics require strict surface quality standards due to their high light transmittance. Defects such as markings, pores, discoloration, and poor luster are unacceptable. Every aspect of the injection molding process—materials, equipment, molds, and product design—must meet stringent requirements.

Transparent Product Molding: Eliminating Haze & Bubbles
Transparent plastics typically have high melting points and poor fluidity. To ensure product quality, it’s necessary to fine-tune process parameters such as barrel temperature, injection pressure, and injection speed. This ensures the plastic fills the mold without causing internal stress, deformation, or cracking.
Material Drying for Transparent Polymer Integrity
Ensuring Material Purity
Impurities in the plastic can affect transparency. During storage, transportation, and feeding, materials must be sealed to remain clean. Moisture in raw materials can cause degradation when heated, so thorough drying is essential. Use a drying hopper and ensure the input air is filtered and dehumidified.
Equipment Cleaning for Transparent Product Purity
Cleaning Barrel, Screw, and Accessories
Prevent contamination by cleaning the screw and accessories with a screw cleaning agent before use and after shutdown. If a cleaning agent is unavailable, PE or PS resins can be used. During temporary shutdowns, reduce the temperature of the dryer and barrel to prevent degradation of the raw materials.
Mold Design for High-Gloss Transparent Products
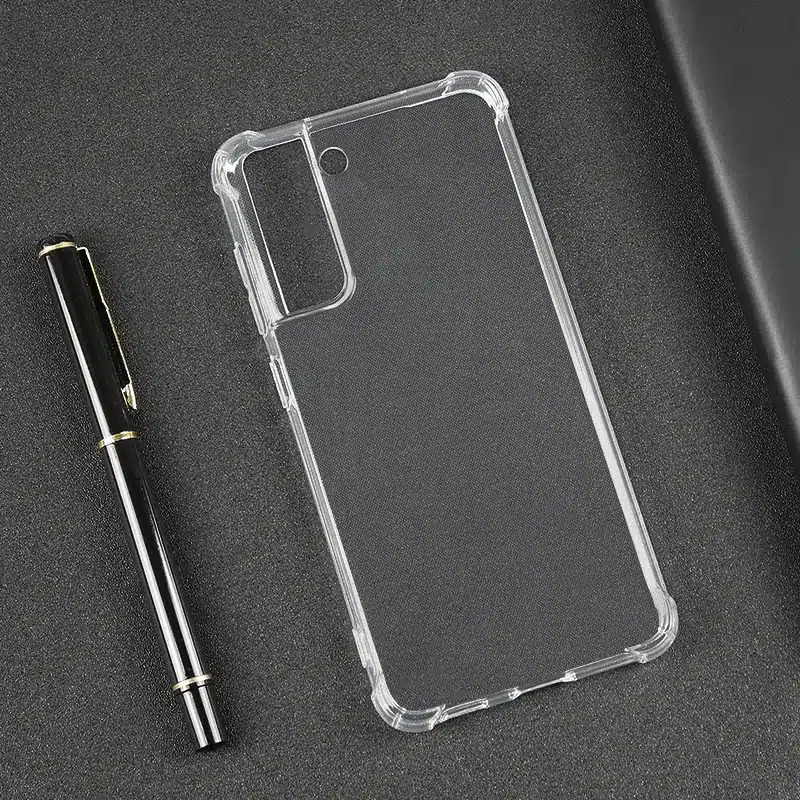
Designing for Quality
To avoid surface defects:
1. Ensure uniform wall thickness and sufficient demolding slope.
2. Gradually transition corners to avoid sharp edges.
3. Use wide, short runners and appropriately positioned gates with cooling wells if necessary.
4. Maintain smooth mold surfaces with low roughness and adequate venting.
Mold Surface and Wall Thickness
Mold surfaces should be smooth, with low roughness (preferably less than 0.8). Ensure adequate venting to discharge air and gases from the melt. Avoid overly thin walls, with a minimum thickness of 1mm, except for PET.
Injection Parameters for Crystal-Clear Transparent Products
Optimal Injection Parameters
To minimize internal stress and surface defects:
1. Use a special screw and a temperature-controlled nozzle.
2. Use a higher injection temperature within the resin’s decomposition limits.
3. Apply high injection pressure to overcome the molten material’s viscosity, but not so high as to cause deformation.
4. Opt for low injection speed, preferably using slow-fast-slow multi-stage injection.
5. Keep pressure holding time and molding cycle short to avoid depressions and bubbles.
6. Use low screw speed and back pressure to prevent material degradation.
7. Precisely control mold temperature for optimal cooling and product quality.
Defect Prevention in Transparent Product Post-Molding
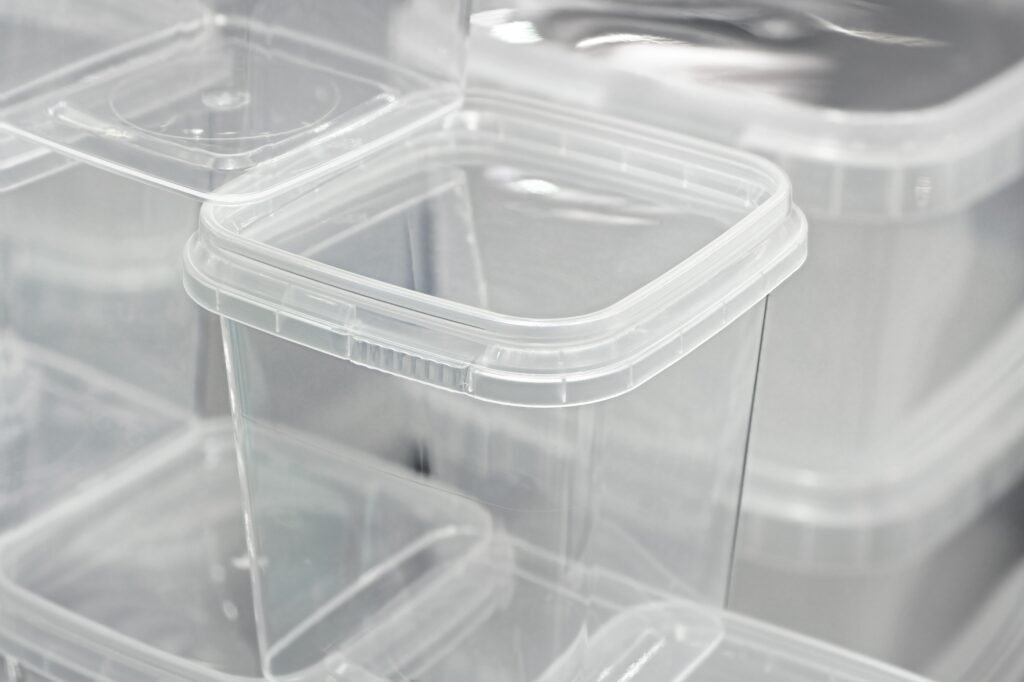
Use of Release Agents and Recycled Materials
Minimize the use of release agents to prevent surface quality deterioration. When using recycled materials, ensure they do not exceed 20%.
Post-Treatment of Products
Certain materials, like PET, require post-treatment to eliminate internal stress. PMMA should be dried at 70-80℃ for 4 hours, and PC should be heated at 110-135℃, with the duration depending on the product. PET must undergo bidirectional drawing to achieve good mechanical properties.