In the fast-paced world of modern manufacturing, the ability to quickly and efficiently produce high-quality prototypes and short-run production parts is essential. Rapid injection tooling has become a cornerstone of this capability, allowing for the swift creation of molds that facilitate the production of plastic parts. Central to the success of this process is the selection of appropriate materials for tooling. This guide will explore the materials used in rapid injection tooling, their properties, advantages, limitations, and practical considerations to help you choose the best rapid injection tooling materials for your specific needs.
Understanding Rapid Injection Tooling
Rapid injection tooling, also known as rapid tooling, combines the principles of injection molding with the speed and flexibility required for fast prototyping and short-run production. Unlike traditional injection molding, which can take weeks or even months to create a mold, rapid tooling significantly reduces lead times, making it possible to produce parts in a matter of days.
The process involves creating a mold using a master pattern, which can be made from various materials, including aluminum, steel, or polymer composites. This mold then injects molten plastic, creating the desired parts. The choice of tooling material is crucial as it affects the quality, durability, and cost of the final product.
Types of Materials Used in Rapid Injection Tooling
Metallic Materials
Aluminum
- Properties and Benefits: Aluminum is lightweight, has good thermal conductivity, and is easy to machine. These properties make it ideal for rapid tooling, as it can be quickly processed and cooled, reducing cycle times.
- Common Applications: Aluminum molds are often used for prototyping and low-volume production runs where high precision and quick turnaround are required.
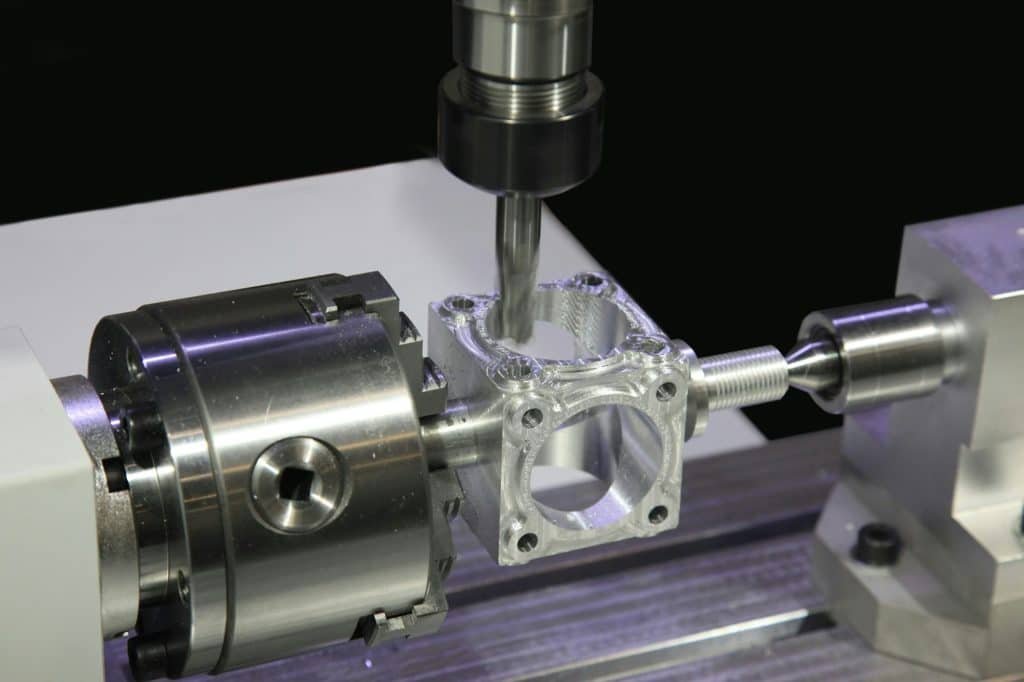
Steel
- Types of Steel Used: Common types include P20, H13, and stainless steel. Each type has different properties that can be leveraged depending on the application.
- Durability and Performance: Steel molds are more durable than aluminum molds and can withstand higher pressures and temperatures. They are suitable for medium to high-volume production runs and for parts that require intricate details and high tolerances.
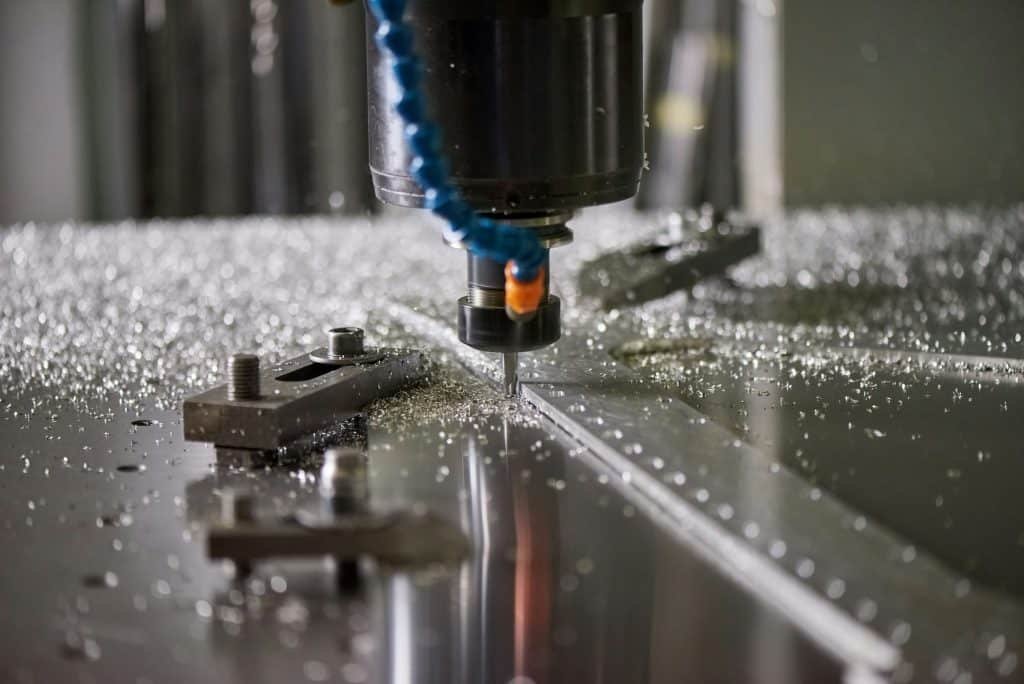
Polymeric Materials
Epoxy
- Advantages and Limitations: Epoxy is a versatile material that can be used to create durable molds quickly. It is less expensive than metal molds but may not withstand the same level of wear and tear.
- Specific Use Cases: Epoxy molds are typically used for prototyping and short-run production of parts with simple geometries.
Urethane
- Flexibility and Strength: Urethane molds are flexible and can be used to produce complex parts with fine details. They offer good resistance to abrasion and chemicals.
- Industry Applications: Urethane is often used in the automotive and consumer electronics industries for producing parts that require high precision and durability.
Selection Criteria for Rapid Injection Tooling Materials
Choosing the right material for rapid injection tooling depends on several factors:
Mechanical Properties
- Tensile Strength: The material’s ability to withstand pulling forces is crucial for molds subjected to high pressures.
- Hardness: Harder materials are more resistant to wear and deformation, making them suitable for high-volume production.
- Thermal Conductivity: Materials with high thermal conductivity, like aluminum, allow for faster cooling and shorter cycle times.
Cost Considerations
- Material Costs: Aluminum and polymeric materials are generally less expensive than steel. However, steel molds last longer and can be more cost effective for large production runs.
- Tooling and Production Expenses: The initial cost of creating a mold and the costs associated with maintenance and potential replacements should be considered.

Production Volume and Speed
- Material Suitability for Different Production Scales: Aluminum and polymeric materials are suitable for low to medium-volume runs, while steel is preferred for high-volume production.
- Impact on Production Timelines: Faster cooling times with materials like aluminum can significantly reduce production timelines.
Design and Complexity
- Material Adaptability to Complex Geometries: Polymeric materials like urethane are more adaptable to complex shapes and fine details.
- Tolerances and Precision: Steel offers the highest precision and is suitable for parts with tight tolerances.
Advanced Materials and Innovations in Rapid Tooling
Composite Materials
- Types of Composites Used: Composites combining metals and polymers can offer a balance of strength, durability, and flexibility.
- Performance Benefits and Trade-offs: While more expensive, composites can provide enhanced performance characteristics, such as improved thermal stability and reduced weight.
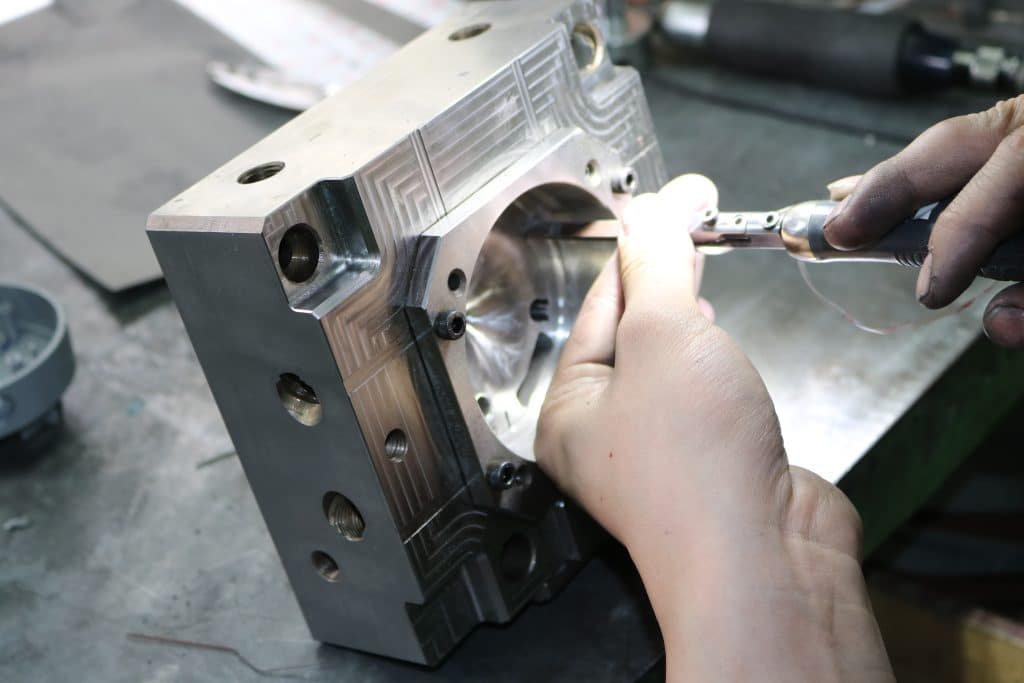
Additive Manufacturing Materials
- Integration with 3D Printing Technologies: 3D printing is increasingly being used to create master patterns or even final molds directly from high-performance materials.
- Case Studies of Hybrid Tooling Approaches: Combining traditional machining with additive manufacturing can lead to innovative tooling solutions that leverage the strengths of both methods.
Future Trends
- Emerging Materials in Rapid Injection Tooling: Research is ongoing into new materials that offer better performance and lower costs.
- Technological Advancements and Their Implications: Advances in material science and manufacturing technologies are continually expanding the possibilities for rapid tooling.
Practical Considerations and Best Practices
Material Handling and Storage
- Guidelines for Preserving Material Integrity: Proper storage conditions, such as temperature and humidity control, are essential for maintaining the quality of tooling materials.
- Safety Protocols: Safe handling procedures must be followed to prevent accidents and material degradation.
Tooling Design for Optimal Material Use
- Design Tips for Enhancing Tool Longevity: Incorporating features like cooling channels and uniform wall thickness can extend the life of the mold.
- Techniques for Minimizing Material Waste: Efficient design and precise machining reduce material waste and associated costs.
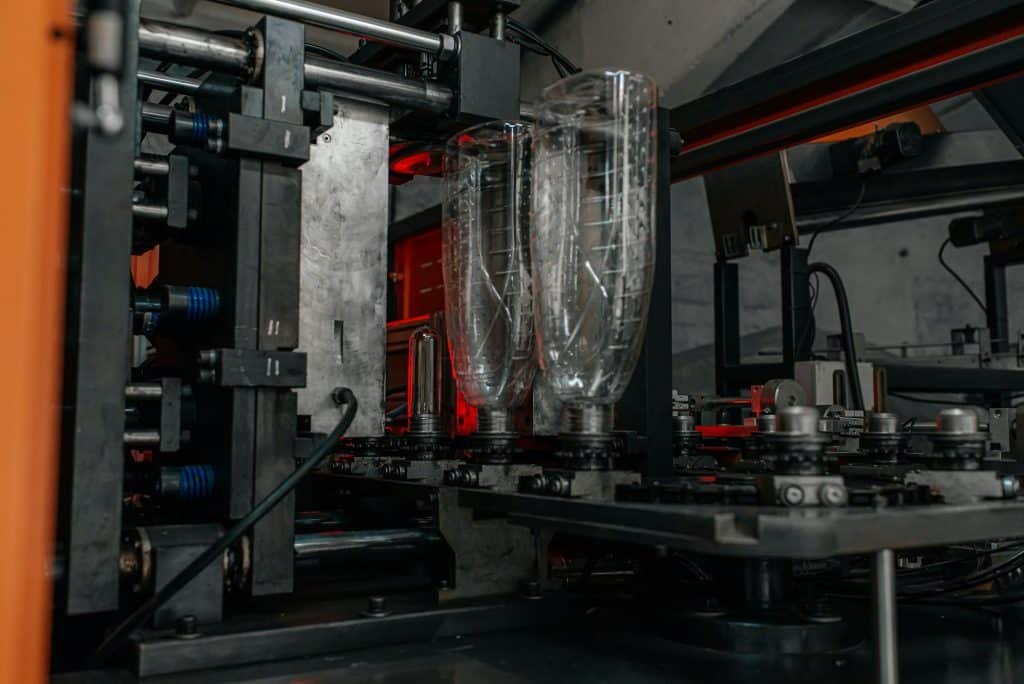
Maintenance and Troubleshooting
- Common Issues and Their Solutions: Regular inspection and maintenance can prevent common issues like wear, deformation, and thermal fatigue.
- Best Practices for Extending Tool Life: Adhering to recommended operating parameters and performing timely repairs can significantly extend the lifespan of tooling materials.
Conclusion
Rapid injection tooling materials are integral to the efficiency and success of modern manufacturing processes. By understanding the properties, advantages, and limitations of various materials, you can make informed decisions that enhance your production capabilities. Whether you are focused on reducing costs, accelerating timelines, or improving product quality, selecting the right tooling material is a crucial step toward achieving your manufacturing goals. This guide provides a comprehensive overview to help you navigate the complex landscape of rapid injection tooling materials, ensuring you are well-equipped to meet the demands of your specific applications.