When it comes to manufacturing, choosing the right method is crucial for achieving the desired quality, efficiency, and cost-effectiveness. Two popular techniques are CNC machining and injection molding, each with its advantages and best-use scenarios. This article will compare and contrast these two methods, highlighting when to use each one to optimize your manufacturing processes.
CNC Machining
CNC (Computer Numerical Control) machining is a subtractive manufacturing process that uses computer-controlled machines to remove material from a solid block (or workpiece) to create the desired shape. Common CNC machines include mills, lathes, and routers.
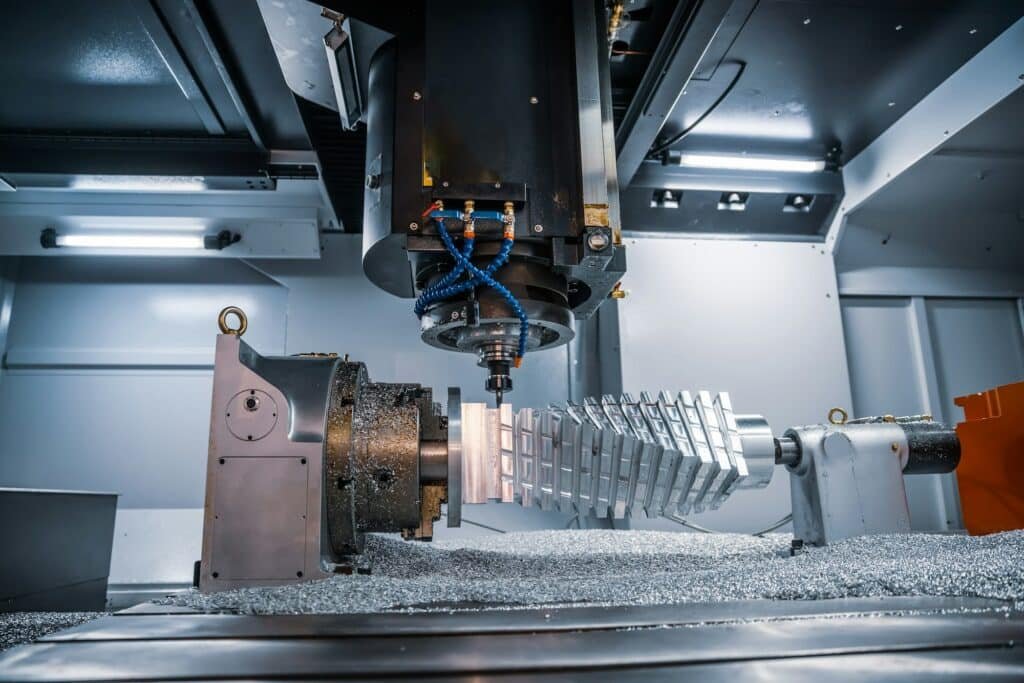
Advantages:
- Precision and Accuracy: CNC machines can achieve very tight tolerances and high levels of detail, making them ideal for complex and intricate designs.
- Flexibility: Suitable for a wide range of materials, including metals, plastics, and composites.
- Prototyping: Excellent for producing prototypes and small batches because it does not require custom molds.
- Customization: Easily adaptable for customized or one-off parts without significant additional costs.
Disadvantages:
- Material Waste: Since it is a subtractive process, CNC machining can produce significant material waste.
- Cost: Higher cost per unit for large production runs due to the time and labor involved in machining each piece.
- Time-Consuming: Generally slower than injection molding for producing large quantities.
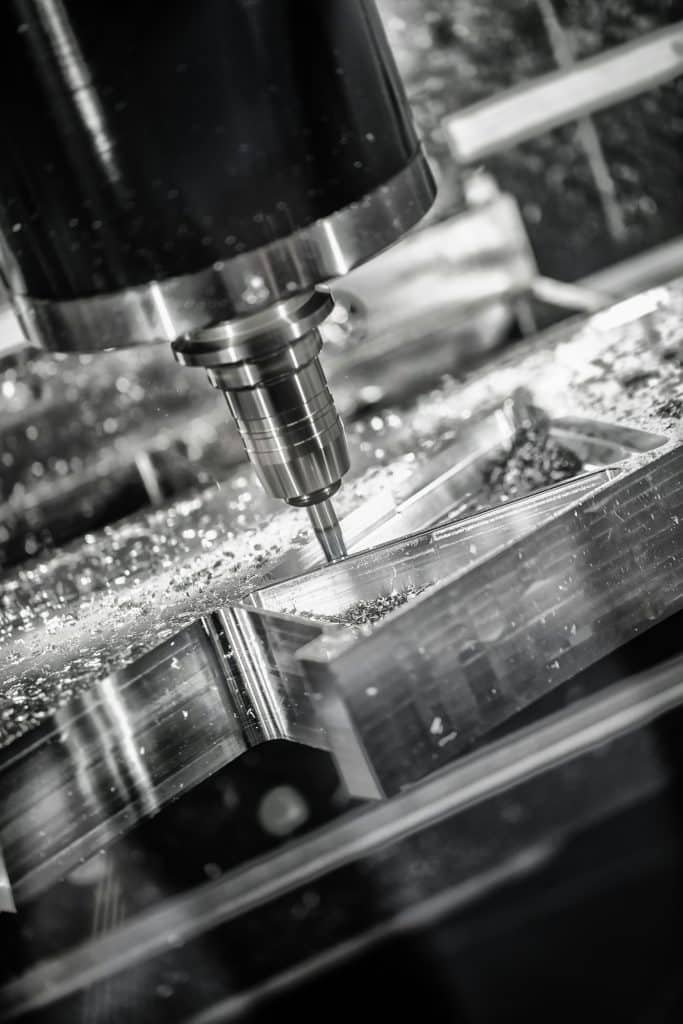
When to Use CNC Machining:
- Prototyping and Small Batches: Ideal for creating prototypes and small production runs due to its flexibility and precision.
- Complex Geometries: Best for parts with intricate details and tight tolerances.
- Custom Parts: Suitable for custom or specialized parts where the design may change frequently.
Injection Molding
Injection molding is a manufacturing process in which molten material, usually plastic, is injected into a mold cavity to form parts. It is primarily used for mass production of identical parts.
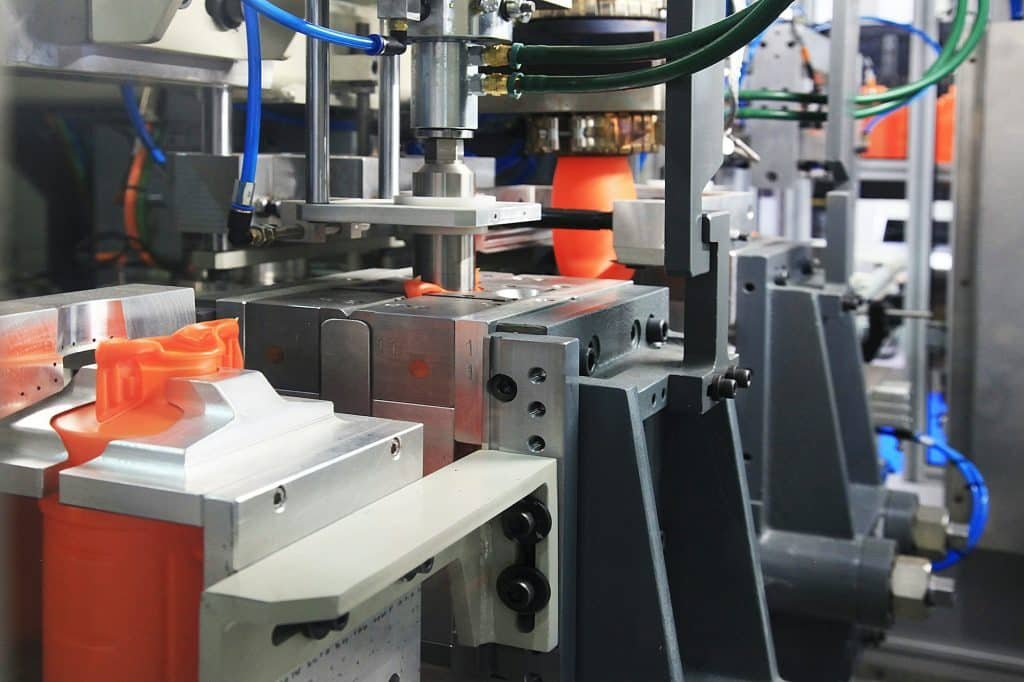
Advantages:
- Efficiency: Highly efficient for large-scale production, capable of producing thousands of identical parts quickly.
- Low Cost per Unit: Economical for high-volume production runs due to the low cost per unit after the initial mold investment.
- Consistency: Ensures uniformity and consistency across all parts produced.
- Material Utilization: Minimal waste as excess material can often be recycled and reused.
Disadvantages:
- Initial Cost: High initial cost for creating custom molds, making it less suitable for low-volume production.
- Lead Time: Longer lead time for mold creation before production can start.
- Limited Material Choices: Primarily used for plastics, with fewer options for other materials compared to CNC machining.
When to Use Injection Molding:
- High-Volume Production: Best for producing large quantities of parts efficiently and cost-effectively.
- Uniformity: Ideal when parts need to be identical in size, shape, and quality.
- Lower Cost per Part: Most cost-effective for high-volume production runs where the initial mold cost can be amortized.
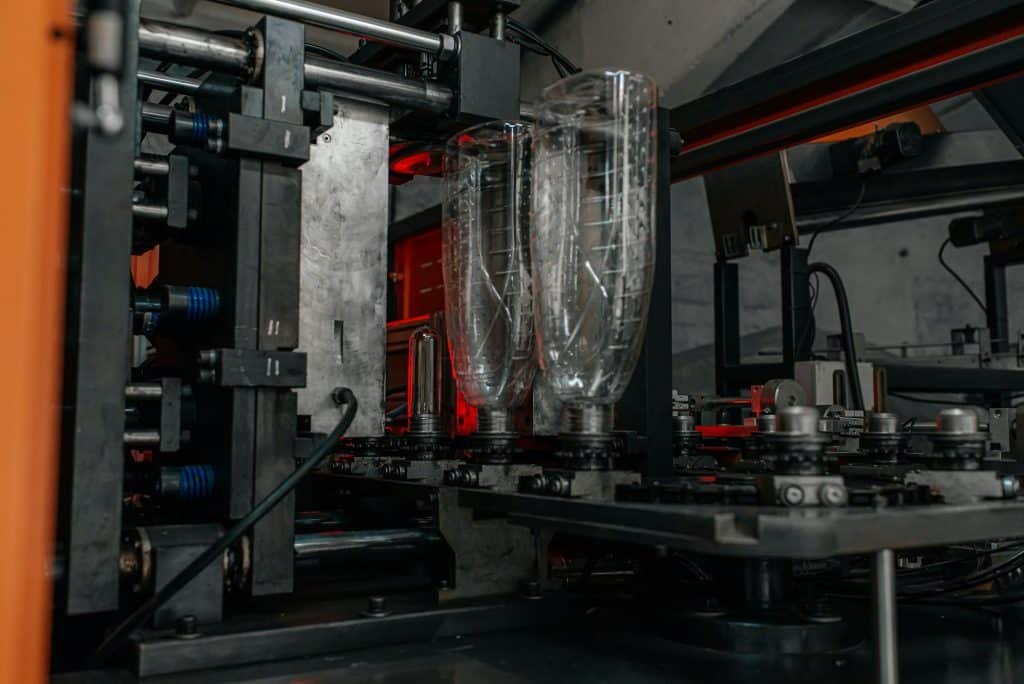
CNC Machining vs Injection Molding
Production Volume:
- CNC Machining: More suitable for low to medium production volumes. The cost per part remains high with increasing volume.
- Injection Molding: Best for high-volume production where the cost per part decreases significantly with larger quantities.
Cost Considerations:
- CNC Machining: Higher per-unit cost due to the labor and time involved in machining each part. However, no need for custom molds makes it more cost-effective for prototypes and low volumes.
- Injection Molding: High initial mold cost but lower per-unit cost for large production runs. Not cost-effective for low volumes due to the mold expense.
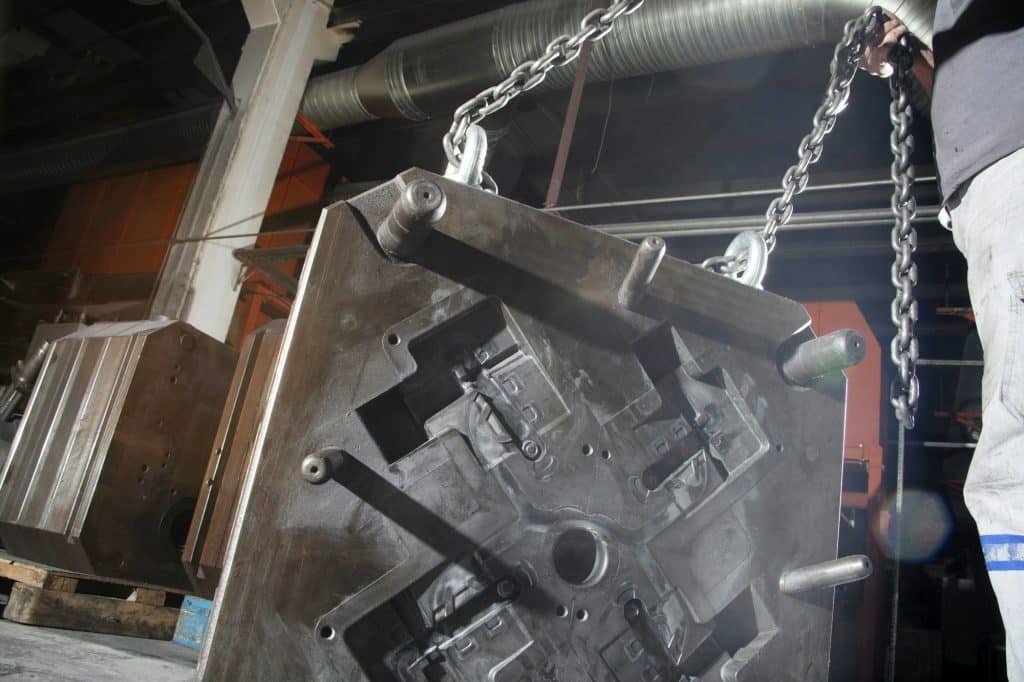
Material and Design Flexibility:
- CNC Machining: Can work with a wider variety of materials, including metals, plastics, and composites. Offers greater flexibility for complex and custom designs.
- Injection Molding: Primarily used for plastics with some limitations on material choices. Better suited for simpler designs that can be replicated in large quantities.
Speed and Efficiency:
- CNC Machining: Slower for large production runs due to the individual machining of each part. More efficient for prototypes and small batches.
- Injection Molding: Extremely efficient for mass production with high-speed production cycles once the mold is created.
Detailed Comparison of CNC Machining and Injection Molding
Feature | Good surface finish can be improved with post-processing | Injection Molding |
---|---|---|
Process Type | Subtractive manufacturing | Additive manufacturing |
Material Types | Metals, plastics, composites | Primarily thermoplastics and thermosets |
Production Volume | Low to medium volume | High volume |
Cost Per Part | Higher for low volumes, decreases with volume | Lower per part at high volumes |
Initial Setup Cost | Lower initial costs | Higher due to mold creation |
Lead Time | Short for prototypes; longer for production | Longer for initial setup; shorter for production runs |
Precision | Very high precision (tolerances ±0.01 mm or better) | Good precision but limited by mold design |
Design Complexity | Excellent for complex geometries | Good for intricate designs; mold complexity affects cost |
Material Waste | Generates waste (cut-off pieces) | Minimal waste; excess material can be recycled |
Surface Finish | A good surface finish can be improved with post-processing | Excellent surface finish with mold design |
Flexibility | High flexibility; easy to adapt to design changes | Low flexibility; changes require new molds |
Post-Processing Needs | Often requires finishing processes | Typically minimal post-processing needed |
Application Examples | Aerospace components, medical devices, custom parts | Consumer products, automotive parts, packaging |
Environmental Considerations | Material waste can be significant | Generally less waste; can use recycled materials |
Conclusion
Choosing between CNC machining and injection molding depends largely on the specific needs of your project. CNC machining offers precision, and flexibility, and is ideal for prototypes and low-volume production. Injection molding, on the other hand, excels in high-volume production with lower per-unit costs and consistent quality. Understanding the strengths and limitations of each method will help you make an informed decision that aligns with your production goals.
About BFY Mold
At BFY Mold, we specialize in providing top-notch manufacturing solutions, including injection molding processing and mold production and manufacturing. Our services extend to mass production, on-demand production, CNC machining, and mirror sparking. With our factory and a commitment to quality, we ensure that our processes and products meet the highest standards. Partner with us to experience excellence in manufacturing.
For more information, visit our website or contact us directly. We look forward to working with you!