Computer-aided design (CAD) and Computer-Aided Manufacturing (CAM) software are integral to modern CNC (Computer Numerical Control) machining processes. They bridge the gap between design and manufacturing, enabling the precise and efficient production of complex parts.
1. Design and Modeling (CAD)
Conceptualization and Design: CAD software allows engineers and designers to create detailed 2D and 3D models of parts. These models serve as blueprints for CNC machines.
Precision and Accuracy: CAD provides tools to create high-quality designs, ensuring that the final product meets exact specifications. This is crucial in industries like aerospace and medical devices, where tolerances are tight.
Simulation and Analysis: Before manufacturing begins, CAD software can simulate how a part will behave under various conditions, such as stress or heat. This allows for optimization of the design before physical production.
Customization: CAD allows for easy modifications and customization of designs. This is particularly useful for producing prototypes and for industries where products must be tailored to specific needs.

2. Manufacturing Process Planning (CAM)
Tool path Generation: CAM software translates CAD designs into CNC machines’ tool paths. These tool paths are optimized for efficiency, minimizing material waste and machining time.
Machining Parameters: CAM software allows engineers to specify machining parameters such as cutting speed, feed rate, and tool type. This customization ensures that the CNC machine operates efficiently and within the material’s tolerances.
Simulation: CAM software can simulate the machining process, allowing operators to identify and correct potential issues such as tool collisions or inefficiencies in the tool path. This reduces errors and increases the quality of the final product.
Post-Processing: CAM software generates G-code, the language used by CNC machines. This code contains instructions to machine the part, including movements, tool changes, and speed adjustments.
3. Integration of CAD and CAM
Seamless Workflow: Modern CAD/CAM systems are often integrated, allowing for a seamless transition from design to manufacturing. Changes in the CAD model are automatically reflected in the CAM tool paths, ensuring consistency and reducing the risk of errors.
Data Management: Integrated systems facilitate better data management, as all design and manufacturing data are stored within a single platform. This ensures version control and makes tracking changes throughout the design and manufacturing process easier.
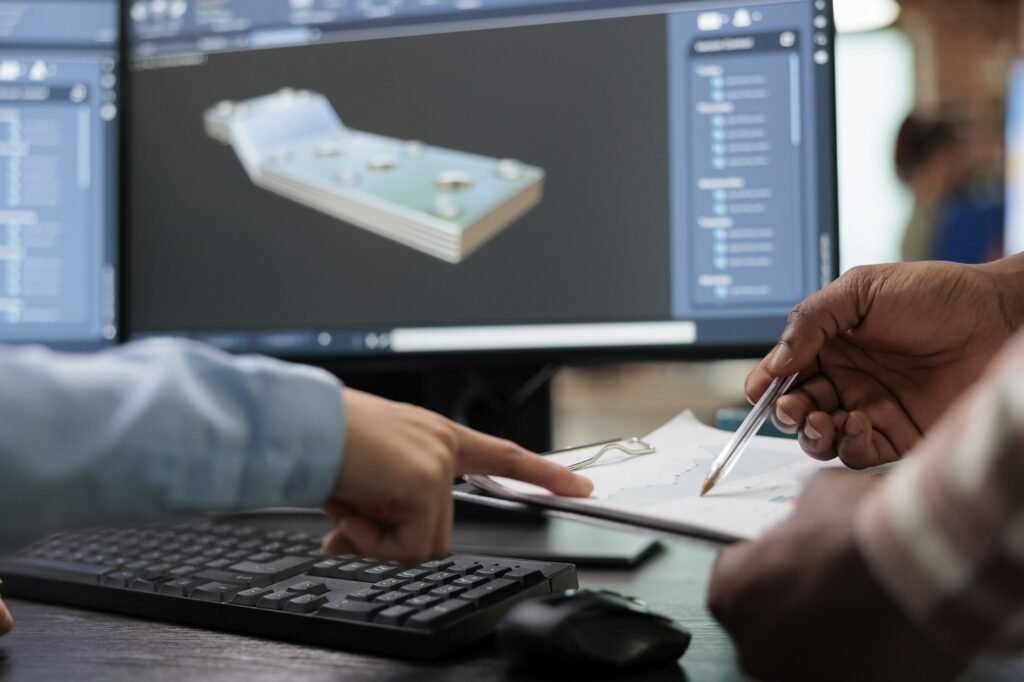
4. Benefits of CAD/CAM in CNC Machining
Increased Efficiency: CAD/CAM software significantly speeds up the design and manufacturing process. Automated tool path generation and simulation reduce the time required to go from concept to finished product.
Improved Quality: By enabling precise design and machining, CAD/CAM software helps produce high-quality parts with tight tolerances and excellent surface finishes.
Cost Reduction: Optimized tool paths and reduced errors in machining lead to lower material waste and decreased machine wear, resulting in cost savings.
Complex Geometry: CAD/CAM enables the production of complex geometries that would be difficult or impossible to achieve with manual machining.
Customization and Flexibility: It allows for easy adjustments to designs and manufacturing processes, providing greater flexibility in production.
Top 10 FAQs for Supplier Selection & Efficiency
1. How does CAD/CAM software improve CNC machining efficiency?
CAD/CAM software reduces programming time by 30–50% through automated toolpath generation, minimizes material waste via simulation, and ensures precision with ±0.01mm tolerance control for critical components.
2. What certifications should CAD/CAM software providers have?
Prioritize suppliers with ISO 9001 (quality management), AS9100 (aerospace), or ISO 13485 (medical devices). These ensure compliance with industry-specific standards for CNC programming and toolpath validation.
3. What are the cost differences between entry-level and advanced CAD/CAM software?
- Entry-level: 2,000–10,000/year (basic 3-axis toolpaths).
- Advanced: 20,000–100,000+/year (5-axis, AI-driven optimization, cloud collaboration).
Advanced tools cut machining time by 20–40%, justifying higher upfront costs.
4. Can CAD/CAM software handle multi-axis CNC machining?
Yes. Top-tier CAD/CAM solutions (e.g., Mastercam, Siemens NX) support 5-axis simultaneous machining, enabling complex geometries like turbine blades or orthopedic implants with tool collision avoidance algorithms.
5. How does CAD/CAM software ensure medical or aerospace standards compliance?
- Traceability: Logs all design changes and toolpath parameters for audits.
- Material validation: Checks against ASTM/AMS specifications (e.g., Ti-6Al-4V for aerospace).
- Surface finish control: Ensures Ra ≤0.8μm for FDA-approved implants.
6. What training support do CAD/CAM suppliers offer?
Leading providers offer:
- On-site workshops: Customized for your CNC machines.
- Certification programs: Mastercam Certified Programmer, Autodesk CAM Expert.
- 24/7 technical support: Resolve toolpath errors in real-time.
7. How does CAD/CAM software integrate with existing CNC machines?
Most CAD/CAM tools export G-code compatible with Fanuc, Haas, or Heidenhain controllers. Verify post-processor libraries for seamless machine communication.
8. What industries benefit most from CAD/CAM-driven CNC machining?
- Medical: Custom prosthetics and surgical tools.
- Aerospace: Engine components, lightweight brackets.
- Automotive: Prototyping, high-precision gears.
9. Can CAD/CAM software reduce material waste in CNC projects?
Yes. Nesting algorithms optimize raw material usage (e.g., 95% efficiency for aluminum sheets), while simulation tools detect errors pre-production, reducing scrap by 15–25%.
10. How do I evaluate a CAD/CAM supplier’s technical expertise?
- Request case studies for your industry (e.g., medical device toolpaths).
- Test software demos with your CAD models.
- Check user reviews on platforms like Capterra or G2.
Conclusion
CAD/CAM software is a cornerstone of modern CNC machining, enabling the production of complex, high-quality parts with precision and efficiency. By integrating design and manufacturing processes, CAD/CAM systems streamline workflows, reduce errors, and contribute to significant cost savings in manufacturing. This technology continues to evolve, further enhancing the capabilities and applications of CNC machining across various industries.