Introduction
Aluminum injection molds have become increasingly popular in the manufacturing industry due to their versatility, cost-effectiveness, and efficiency. This blog post will explore the essential aspects of aluminum injection molds, including what they are, the types of aluminum best suited for molds, their lifespan, design standards, benefits, and applications.
What Is Aluminum Injection Mold?
An aluminum injection mold is a type of mold used in the injection molding process, crafted from aluminum alloys. Unlike traditional steel molds, aluminum molds are lightweight and easier to machine, making them ideal for prototyping and low to medium-volume production. They are particularly useful for applications that require quick turnaround times and lower tooling costs.

Aluminum Molds for Injection Molding
What Type of Aluminum is Best For Injection Mold?
Different types of aluminum alloys are used for injection molds, each offering specific properties that make them suitable for various applications. Here’s a comparison of commonly used aluminum alloys for injection molds:
Alloy | Properties | Applications |
6061 | Good machinability, corrosion resistance, moderate strength | Prototyping, short-run production |
7075 | High strength, excellent hardness, low weight | High-strength applications, precision parts |
2024 | High fatigue resistance, good strength-to-weight ratio | Aerospace and automotive components |
5083 | Exceptional performance in extreme temperatures | Specialty molds for high-temperature plastics |
Among these, 6061 aluminum is commonly used for injection molds due to its balanced properties of machinability and strength, making it suitable for most standard applications.

How Long Does an Aluminum Injection Mold Last?
The lifespan of an aluminum injection mold largely depends on factors such as the type of plastic being molded, production volume, mold maintenance, and the specific aluminum alloy used.
- For Prototyping or Low-Volume Production: Aluminum molds can last up to 10,000 cycles or more.
- For Medium-Volume Production: With proper maintenance, molds can achieve between 50,000 to 100,000 cycles.
This durability, while less than that of steel molds (which can last several million cycles), is often sufficient for applications that do not require high-volume production runs.
Design Standards For Aluminum Injection Molds
Designing an aluminum injection mold requires consideration of several factors to ensure optimal performance:
- Wall Thickness: Uniform wall thickness should be maintained to reduce stress and potential warping of parts.
- Cooling Channels: Aluminum’s superior thermal conductivity allows for more efficient cooling, which should be factored into the mold design to enhance cycle times.
- Draft Angles: Adequate draft angles are necessary to facilitate the easy removal of the part from the mold.
- Parting Line: Proper positioning of the parting line is crucial to minimize flash and ensure the smooth release of the molded part.
Following these design standards helps maximize the mold’s efficiency and lifespan while reducing potential defects.
Benefits of Aluminum Injection Molds
Aluminum injection molds offer several distinct advantages:
- Cost-Effective: Lower material costs and faster machining reduce overall production costs.
- Quick Turnaround: Faster machining and cooling times result in shorter lead times.
- Lightweight: Easier to handle and transport, reducing labor costs and downtime.
- High Thermal Conductivity: Allows for faster cooling and shorter cycle times, improving production efficiency.
- Ideal for Prototyping: Perfect for testing and refining new designs due to lower costs and quicker adjustments.
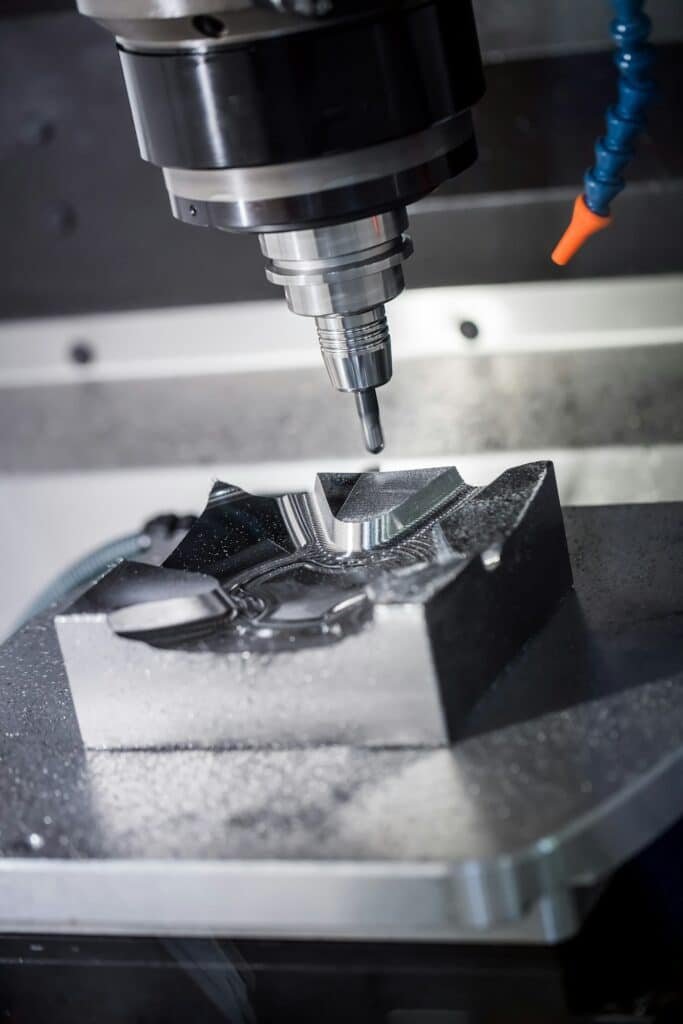
Aluminum Injection Mold
Applications of Aluminum Injection Molds
Aluminum injection molds are widely used in various industries due to their adaptability and efficiency. Common applications include:
- Automotive Industry: Used for prototyping and producing small to medium-sized parts.
- Consumer Goods: Ideal for producing low to medium-volume parts like handles, knobs, and casings.
- Medical Devices: Suitable for prototyping and short runs of medical equipment and components.
- Aerospace: Utilized in the production of lightweight parts that require high precision.
Conclusion
Aluminum injection molds provide an excellent solution for manufacturers looking for cost-effective, efficient, and versatile tooling options. They are particularly valuable in prototyping and low to medium-volume production, offering benefits like quick turnaround times and lower costs.

About BFY Mold
At BFY Mold, we specialize in high-quality injection molding and mold manufacturing. Our comprehensive services include mass production, on-demand production, CNC machining, and mirror spark finishing, all carried out in our state-of-the-art factory. We are dedicated to providing our clients with the best solutions to meet their unique needs, ensuring high standards of quality and precision. Whether you’re looking for prototyping or full-scale production, BFY Mold is your trusted partner in manufacturing excellence.