Injection molding plays a pivotal role in the LED industry, enabling the production of intricate and high-precision components essential for LED products. This manufacturing process involves injecting molten material into a mold to form specific shapes, which is particularly advantageous for creating complex parts with high consistency and efficiency. The use of injection molding in the LED industry not only streamlines production but also enhances the performance and durability of LED products.
Materials Used in LED Housing
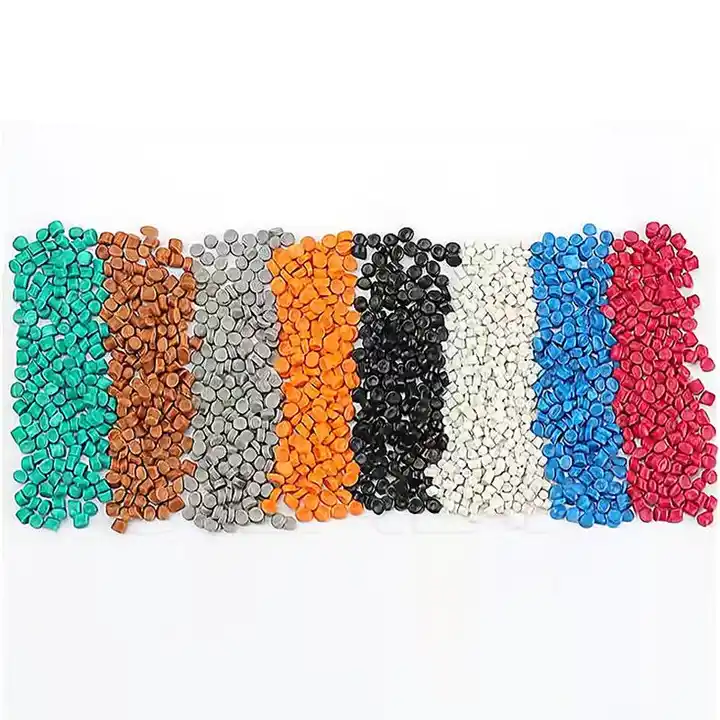
Common Materials
The housing of LED products requires materials that offer durability, heat resistance, and aesthetic flexibility. Common materials used in injection molding for LED housing include:
- Polycarbonate (PC): Known for its high impact resistance and transparency, polycarbonate is often used in applications with critical durability and light transmission, such as in lenses and covers.
- Acrylonitrile Butadiene Styrene (ABS): ABS is favored for its toughness and ease of molding. It is commonly used in LED housing due to its robustness and good insulating properties.
- Polyethylene Terephthalate (PET): PET is used for its excellent thermal and dimensional stability, making it suitable for LED components exposed to varying temperatures.
- Polyamide (PA): Also known as nylon, polyamide offers high mechanical strength and thermal resistance, which benefits components subjected to mechanical stress and heat.
Advanced Materials
For specialized applications, advanced materials are used to meet specific requirements:
- Liquid Silicone Rubber (LSR): LSR is used for its flexibility, high thermal stability, and excellent optical properties, making it ideal for producing lenses and seals in LED products.
- Thermally Conductive Plastics: These materials are engineered to dissipate heat efficiently, ensuring the longevity and performance of high-power LED applications.
Advantages of Injection Molding in the LED Industry
Precision and Consistency
Injection molding provides unparalleled precision, enabling the production of complex geometries with tight tolerances. This is crucial for LED components that require exact dimensions to ensure proper alignment and functionality. The consistency achieved through injection molding ensures that each part meets the high standards necessary for LED products.
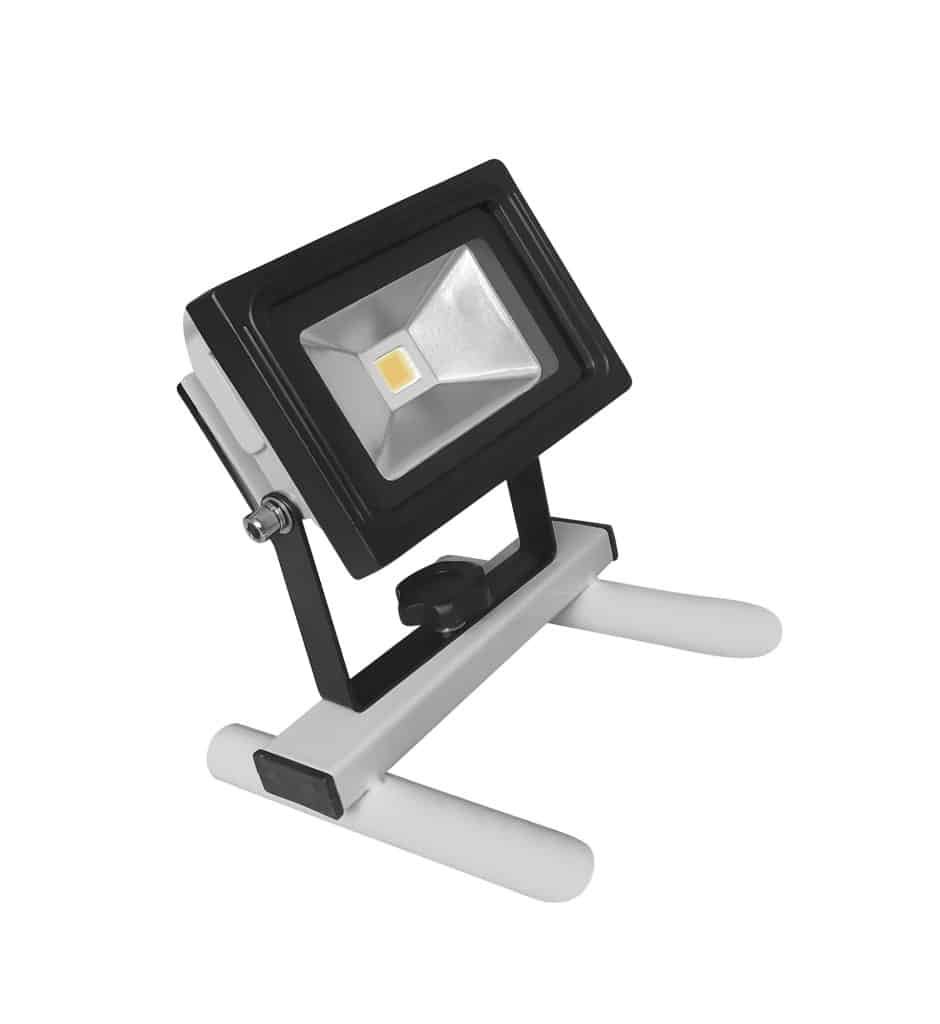
Cost Efficiency
The ability to produce large volumes of parts with minimal waste makes injection molding a cost-effective solution for the LED industry. Once the initial mold is created, the per-unit cost of production decreases significantly, making it an economically viable option for mass production.
Design Flexibility
Injection molding allows for a high degree of design flexibility, enabling the creation of custom shapes and intricate features that enhance the functionality and aesthetics of LED products. This flexibility is essential for developing innovative LED solutions tailored to specific applications.
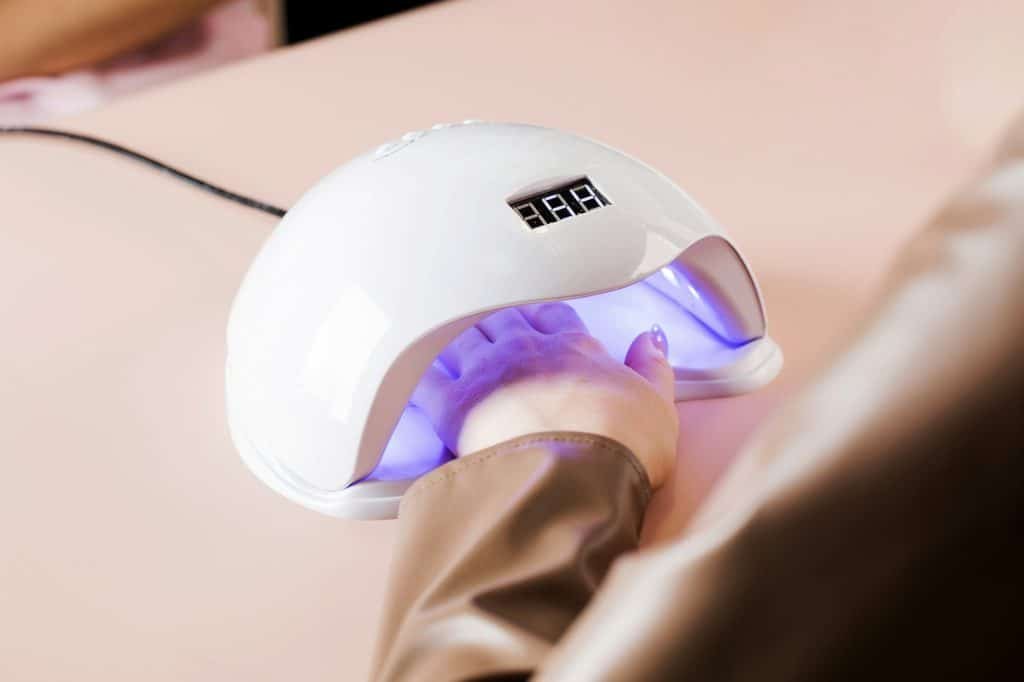
Enhanced Durability
The materials used in injection molding provide excellent mechanical properties and environmental resistance, ensuring that LED housings and components can withstand harsh conditions. This durability is vital for outdoor lighting and automotive LED systems, where components are exposed to extreme environments.
Case of Injection Molding in the LED Industry
Automotive LED Lighting
In the automotive industry, injection molding is used to produce robust and precise housings for LED headlights. For example, a major automotive manufacturer partnered with an injection molding specialist to develop high-performance LED headlight systems. Using polycarbonate for the lenses and thermally conductive plastics for the heat sinks, the resulting products offered superior light distribution and thermal management, enhancing both safety and efficiency.
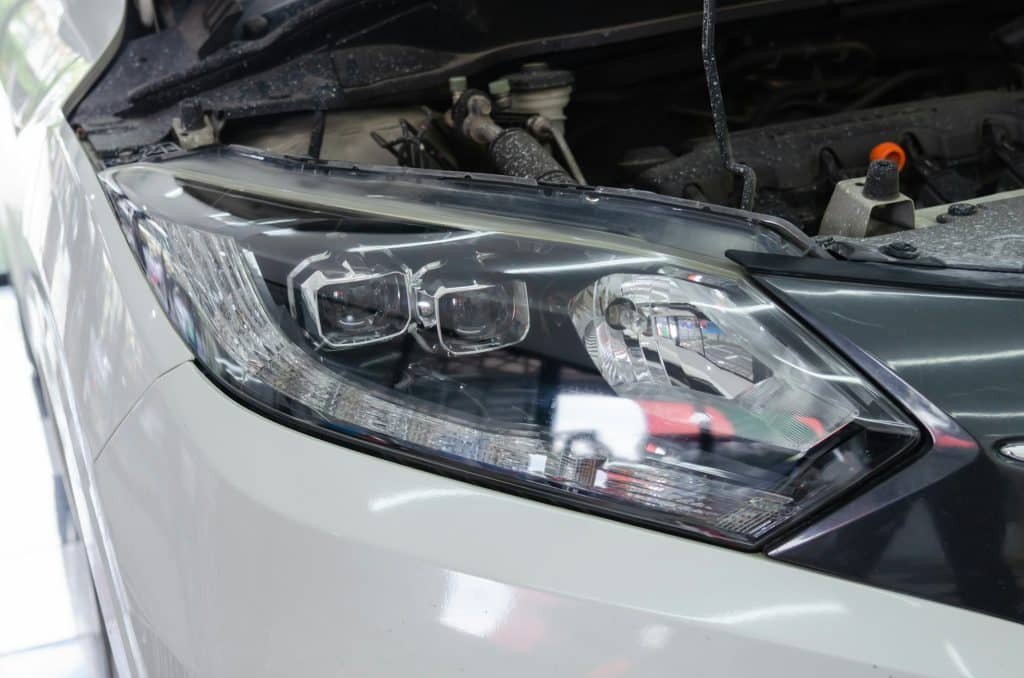
Commercial LED Fixtures
A leading manufacturer of commercial lighting fixtures utilized injection molding to create lightweight and durable housings for their LED panels. By using ABS for the housing and polycarbonate for the diffusers, they achieved products that met rigorous standards for energy efficiency and lighting quality, ensuring uniform light distribution with minimal glare.
Consumer Electronics
Injection molding is also critical in the production of LED backlighting components for consumer electronics. A prominent electronics company used polycarbonate to mold light guides and diffusers for their latest ultra-thin televisions. The precision molding process ensured consistent quality and performance, contributing to the exceptional brightness and clarity of their displays.
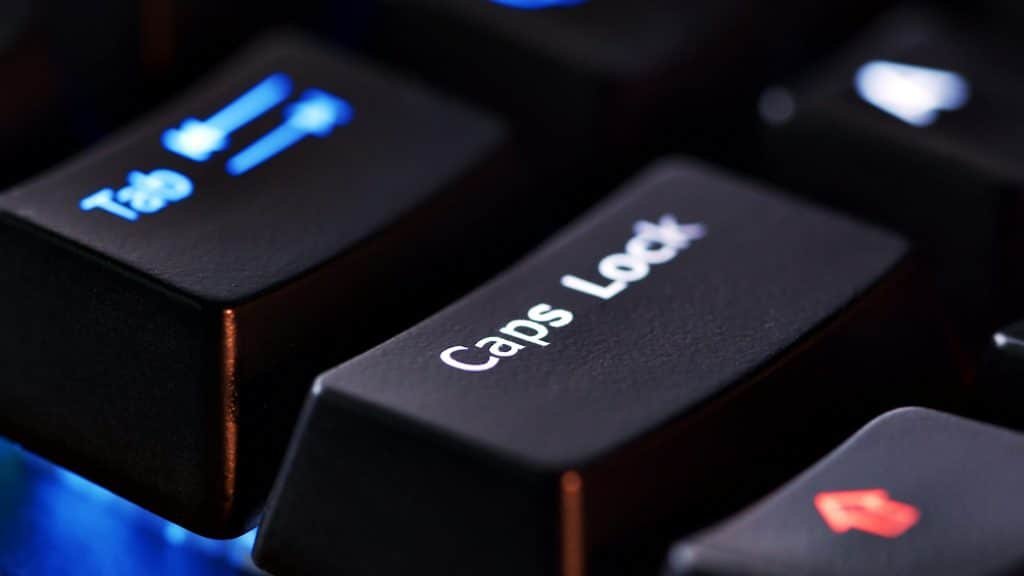
Conclusion
Injection molding is integral to the LED industry, providing a reliable and efficient method for producing high-quality components. The selection of appropriate materials and the advantages of precision, cost efficiency, design flexibility, and durability underscore the importance of this manufacturing process. As the demand for advanced LED solutions continues to grow, injection molding remains a cornerstone of innovation and quality in the LED sector.