Introduction
As product lifecycles shrink and margins tighten in the hyper-competitive consumer electronics industry, manufacturers face a near-existential challenge: providing high-quality plastic components at lower and lower costs. This challenge was crucial for a leading innovator in wearable health technology since its existing custom injection molding processes drained resources, were delayed in the launch, and didn’t meet precision standards.
Partnering with BFY Mold—the only real breakthrough our client could get on time was reducing total production costs by 40% while accelerating time-to-market and improving product reliability. This case study explores the technical strategies, material innovations, and supply chain optimizations that enabled this transformation, providing actionable intelligence for electronics brands looking to succeed in an increasingly cost-sensitive environment.
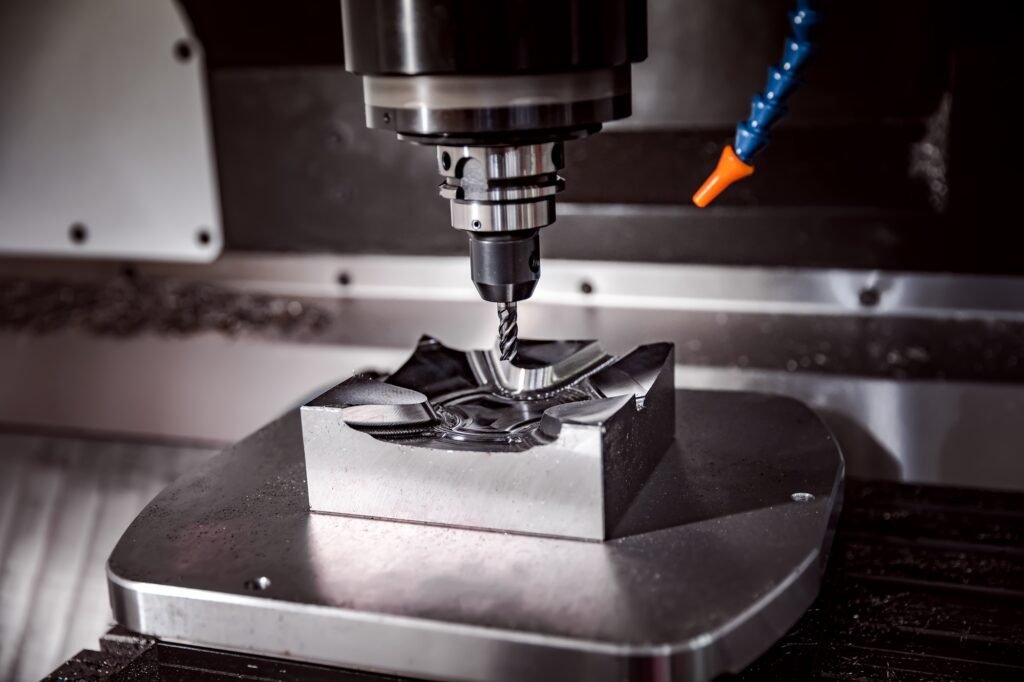
The Challenge: Balancing Cost, Speed, and Precision
For one of our clients, which develops smartwatches and activity trackers with a production volume of 5 million+ units per year, getting the tools to ensure data accuracy proved challenging. Their struggle reflected sector-wide pain points:
- Material Waste: Conventional designs resulted in 15% excess material during mold production (mostly maintained ABS/PC blends).
- Prototyping Time Delays: 2–3 weeks for mold adjustments for every design change stopping product launches.
- Limitation of Offshore Supplier: Though offshore vendors had lower labor costs, they could not support ±0.05mm tolerance requirement, leading to inconsistent quality.
“We needed a partner who understood both cutting-edge engineering and the urgency of consumer electronics,” said Client’s Head of Manufacturing. “Every dollar saved and every day shaved mattered.”
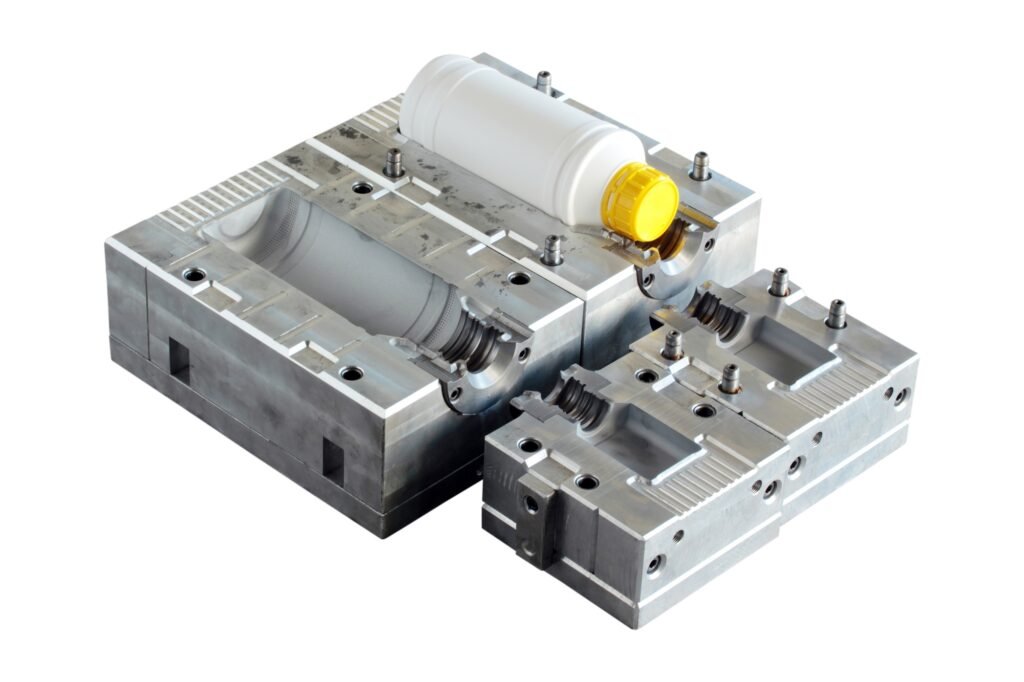
The Solution: BFY Mold’s Three-Pronged Strategy
1. Local Custom Mold Design Optimization
Problem: Outdated trial-and-error mold adjustments wasted time and materials.
Innovation:
- Moldflow Simulation: BFY Mold’s engineers utilized advanced simulation software to analyze polymer flow, cooling patterns, and stress distribution.
- Identified optimal gate locations, reducing material usage by 12%.
- Predicted sink marks and warpage risks, cutting trial iterations from 5 to 2.
- Single-Cavity Efficiency: Contrary to industry norms favoring multi-cavity molds, simulations revealed a single-cavity design with accelerated cycle times (18% faster) better suited to Client’s low-to-mid volume needs.
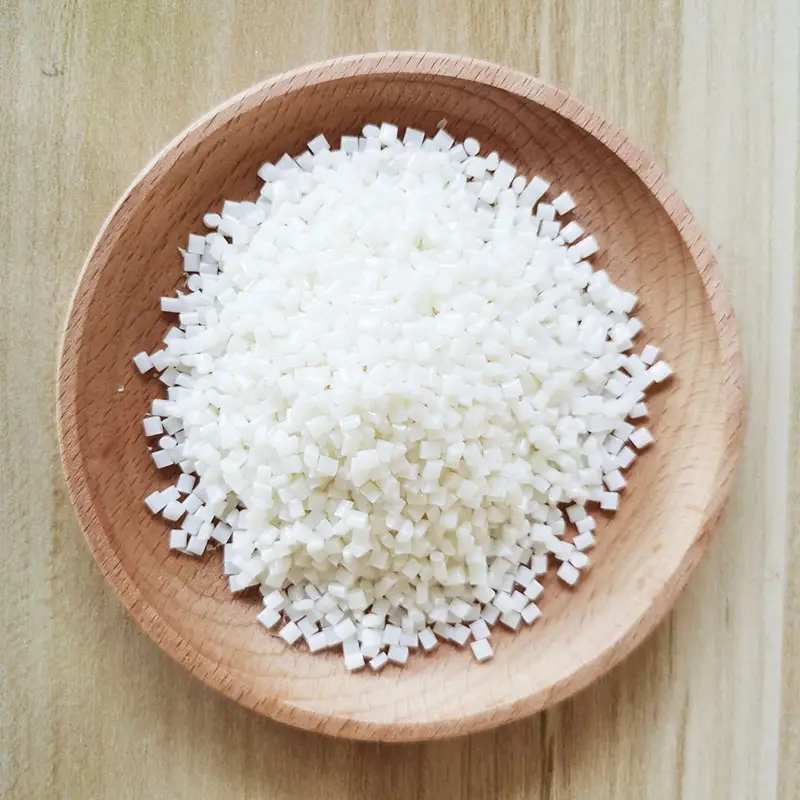
Result:
- 12% Material Savings: Reduced ABS/PC consumption per unit.
- 50% Faster Prototyping: 48-hour simulation cycles replaced weeks of physical trials.
2. Hybrid Mold Manufacturing: Cost vs. Durability Perfected
Problem: Full-steel molds were durable but prohibitively expensive ($28,000 per set).
Innovation:
- Aluminum-Steel Composite Molds:
Aluminum Framing: Lowered cost of mold for manufacturing by 35% ($18,200 per set).
Steel Core Inserts: Maintained precision for 500,000+ cycles, critical for high-volume electronics.
- Conformal Cooling Channels:
3D-printed channels followed the mold’s contours, improving cooling efficiency by 25%.
Cooling time dropped from 15s to 11s, minimizing thermal deformation.
Comparative Data:
Metric | Traditional Mold | BFY Mold Hybrid Mold |
Initial Cost | $28,000 | $18,200 |
Cycle Time Reduction | – | 18% |
Tool Life | 1M cycles | 500K cycles (upgradable) |
3. Localized Supply Chain & Material Sourcing
Problem: Offshore production caused logistical delays and hidden costs.
Innovation:
- Domestic Material Substitution:
- Replaced imported Sabic ST-800 ABS with a locally modified alternative, 22% cheaper yet UL94 V-0 certified.
- Collaborated with material scientists to enhance flame retardancy for wearable devices.
- Integrated Production Hub:
- Established a dedicated facility in Shenzhen, China, co-locating mold fabrication, custom injection molding, and QC.
- Cut lead times from 8 weeks to 4 weeks.
“BFY Mold’s vertical integration was a game-changer,” noted the Business Partner Supply Chain Director. “We eliminated 60% of logistics overhead and gained real-time production oversight.”

Tangible Results: Beyond Cost Reduction
- 40% Total Cost Savings:
- Material: 12%
- Tooling: 35%
- Logistics: 60%
- Faster Time-to-Market:
- Prototyping cycles were reduced by 50%, enabling a 6-week acceleration in product launch.
- Captured 2024 holiday sales, boosting revenue by $2.3M.
- Enhanced Quality Control:
- Dimensional accuracy: ±0.03mm (surpassing initial targets).
- The defect rate dropped from 12% to 2%, minimizing post-production rework.
- Strategic Partnerships:
- Featured in Plastics Today, attracting inquiries from 3 Fortune 500 electronics firms.
- Expanded collaboration with custom injection molding to include TWS earbud casings and IoT sensors.
Why BFY Mold? Technical Edge for Electronics Brands

- Proprietary Moldflow Database: Leverage 1,000+ historical simulations for consumer electronics projects.
- Dual Certifications: ISO 9001 Production Certification, ensuring cross-industry compliance.
- Flexible Production Models: Support low-volume batches (1,000+ units) ideal for iterative tech products.
Conclusion: A Blueprint for Electronics Manufacturers
Their journey underscores a critical lesson: In consumer electronics, innovation isn’t just about product features—it’s about reinventing manufacturing itself. By combining AI-driven design, hybrid tooling, and localized agility, BFY Mold enabled 40% cost savings without sacrificing quality or speed.
Final CTA:
“Ready to transform your custom injection molding process?
Contact BFY Mold’s engineering team by email for a free project audit. Let’s engineer your cost breakthrough.”