Introduction to Advanced Injection Molding Techniques
As a key process in modern manufacturing, injection molding allows the creation of intricate components with high accuracy and productivity. Industries, including the automotive and medical sectors, require higher-quality components and, as such, continue to develop advanced molding techniques.
With that in mind, some techniques, such as 2K injection molding and gas-assisted injection molding, among others, significantly enhance the product life of parts, weight reduction, and efficiency of material usage. These technologies improve the product’s performance and decrease their manufacturing’s financial and environmental costs.
Discover why these innovative methodologies are becoming new technologies for manufacturing automotive and medical parts. We’ll also explore their advantages, including increased durability and greater design flexibility.

What is 2K Injection Molding?
How It Works
2K (two-shot) injection molding is a process whereby two different materials or colors are molded in the same process. The first material is injected, and when that layer cures, a second one around or over the first is injected. It enables manufacturers to make parts that incorporate various material properties in a single part.
In a common application, such as vehicles, one material may be hard plastic for the structure of the piece, whereas another can be softer and more high-quality for aesthetic purposes, such as a soft-touch surface or grip area.
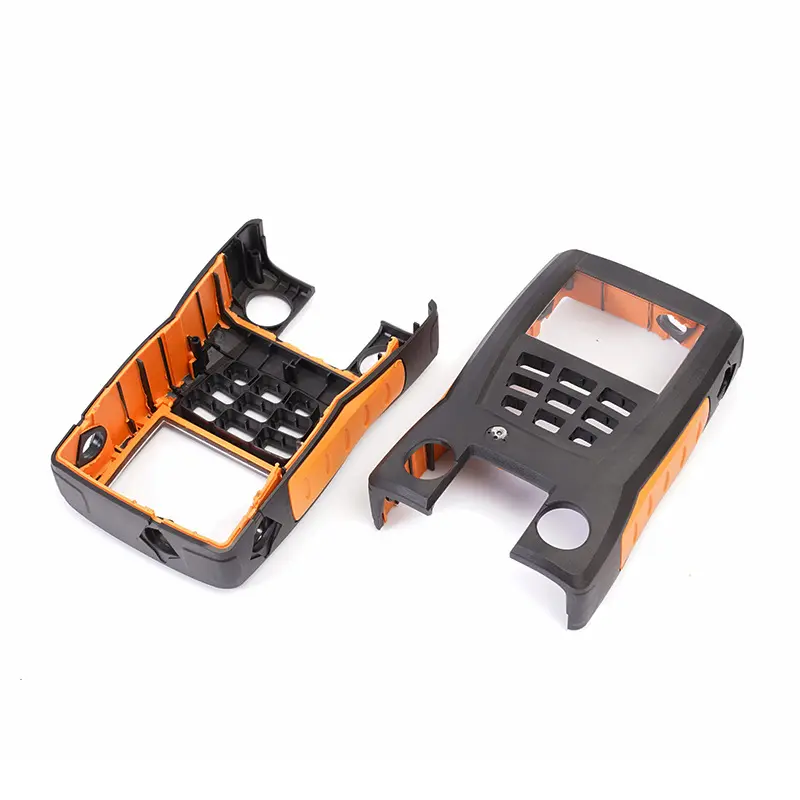
Benefits of 2K Injection Molding in Automotive and Medical Industries
- Enhanced Durability: The ability to composite materials with distinct properties — such as hardness and flexibility — that increase the part’s durability, especially for automotive components that experience significant wear and stress.
- Reduced Production Complexity: 2K Molding can eliminate the need for additional assembly processes, which cuts labor costs and the risk of part defects.
- Enhanced Aesthetics: Components used in medical and automotive applications realize a flawless finish and more complex geometrics that would be challenging or expensive using traditional molding methods.
Gas-Assisted Injection Molding: Revolutionizing Part Design
Advantages of Gas-Assisted Molding
The three most common methods are gas-injected injection molding, which injects a gas (usually nitrogen) into the mold cavity post-injection of the plastic, and gas-assisted injection molding. Expanding the gas creates hollow voids in the part that can dramatically decrease the overall weight of the component without compromising strength. This process is especially useful for automotive parts, exchanging large portions of stamped steel components for world-class quality components, and in the medical device space where weight is paramount.
- Weight Reduction: Gas-assisted molding can lighten the molded part without compromising its strength by forming hollow structures inside.
- Savings on Material: The hollow tubes will utilize less plastic, saving costs and creating a more efficient and sustainable manufacturing process.
- Improved Design Flexibility: Gas-assisted molding allows for more intricate geometries that would be challenging or unfeasible with traditional molding.
Industry Applications: Automotive & Medical
- Automotive: Bumpers, instrument panels, and other components need weight and structural integrity.
- Medical: Device housings, injectors, and various pieces of large diagnostic equipment need to be light, tough, and safe for medical professionals to handle.
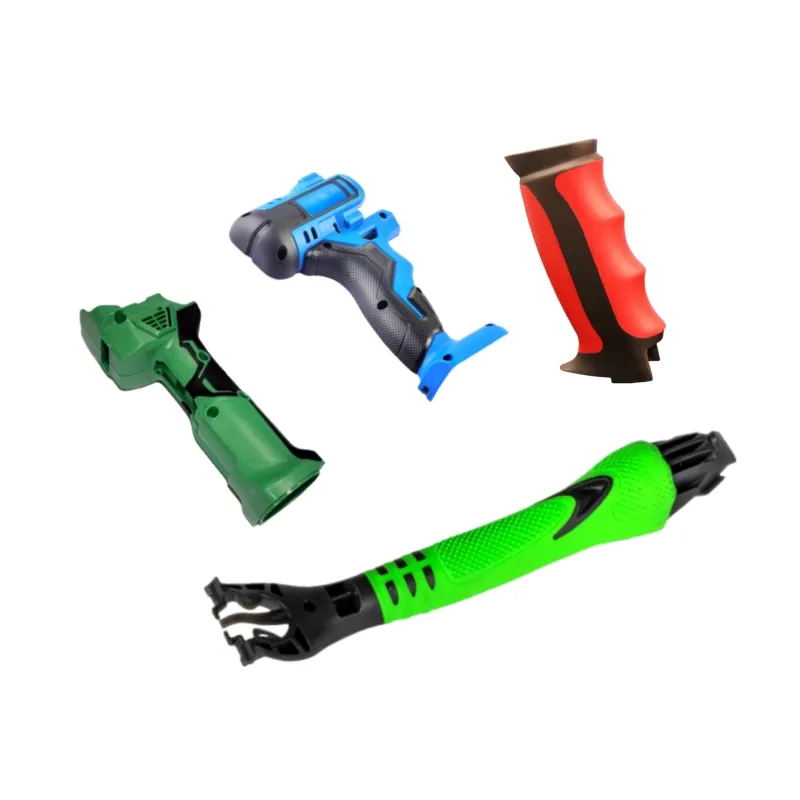
Comparing 2K, Gas-Assisted, and Traditional Injection Molding
Feature/Benefit | 2K Injection Molding | Gas-Assisted Injection Molding | Traditional Injection Molding |
Material Flexibility | High (Two materials/colors) | Moderate (Limited to hollow sections) | Low (One material per mold) |
Durability | High | Moderate | Moderate to High |
Weight Reduction | None | High | None |
Complexity of Design | High | High | Moderate to Low |
Production Efficiency | High (Fewer steps) | High | Moderate to Low |
Real-World Applications: How These Molding Techniques Improve Durability
Automotive Case Study: Enhanced Durability
A leader in automotive manufacturing embraced 2K injection molding for its dashboard parts, utilizing a rigid plastic base for structural integrity and a soft-touch over mold for comfort. The result was a product that lasted forever and gave the driver a better “feel.” The new materials meant a more durable product while reducing manufacturing costs and time.
Medical Industry: Ensuring Safety and Longevity
Accuracy and sturdiness are crucial in the medical industry. Gas-Aided Injection Molding for Complex Injection Pen Housing: A medical device manufacturer used this method to produce a complex housing for an injection pen. The hollow construction cut down on weight, and the gas-assisted molding process ensured the device was strong enough to survive repeated use without failure. This leads to higher patient safety and improved product longevity.
Optimizing Mold Design for Precision and Performance
High-Precision Mold Design and Its Role in Durability
High-precision mold design is critical for ensuring the durability and performance of injection-molded parts. By using sophisticated mold designs and ensuring tight tolerances, manufacturers can produce parts that are not only durable but also meet exacting standards for various industries.
- Advanced Mold Design: Tools like CAD software, CNC machining, and mirror spark erosion allow manufacturers to achieve high-precision molds with minimal variation in the final product.
- Material Selection: Choosing the right material for the mold and part is essential to achieving long-lasting durability.
BFY Mold: Leading the Charge in Advanced Molding Technologies
We are proud to be an industry leader in injection molding at BFY Mold. We have a fully equipped factory and leading-edge equipment that is a specialized organization with a certain scale and strength. We offer custom mold design, precision injection molding, and mass production services. We can accommodate various manufacturing requirements by offering everything from 2K molding to gas-assisted molding to traditional injection molding. We utilize advanced systems for CNC machining and mirror spark with high-tech capabilities to ensure the highest quality on every project.