Injection molding costs can vary widely depending on several factors, including the complexity of the part, injection molding materials used, production size, and the design of the mold itself. Here’s a breakdown of the key cost factors involved in injection molding:
Mold Making Cost
It is estimated that the design phase accounts for 10% of the total cost of an injection mold. For simple parts, Design for Manufacturing (DFM) typically takes 1-2 days, while 3D mold design requires 2-3 days. However, designing complex or large injection molds may take several weeks. Mold design is critical to injection molding as it significantly impacts manufacturing costs. Skilled mold designers can optimize costs while maintaining quality to meet specific requirements accurately.
If you already have a mold, skip to the steps below.
Injection Molding Cost
1. Injection Mold Costs
Prototype Mold:
Simple molds for low-volume production or prototyping can range from $1,000 to $5,000. These are often made from aluminum and have a shorter lifespan.
Production Mold:
For high-volume production, molds are usually made from hardened steel. They may cost anywhere from $5,000 to $100,000 or more depending on complexity, size, and the number of cavities (multiple parts produced per cycle).

2. Injection Molding Material Costs
- The cost of materials varies depending on the type of plastic used. Common plastics such as polypropylene (PP) or polyethylene (PE) are relatively inexpensive, costing between $1 to $3 per pound. Engineering-grade resins like polycarbonate (PC) or ABS can range from $2 to $7 per pound. Specialty materials with unique properties (e.g., flame retardant, UV resistant, medical-grade plastics) can be more expensive, ranging from $10 to $50 per pound.
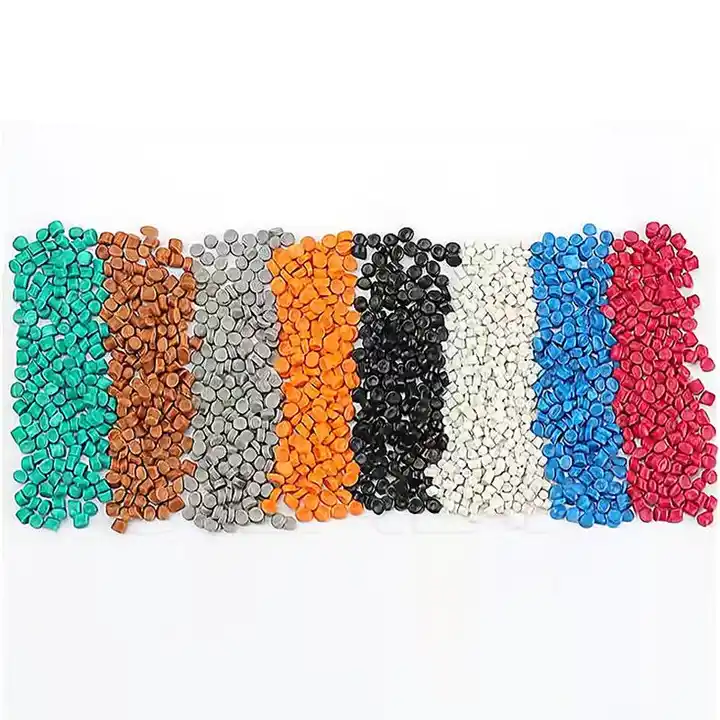
3. Machine Time
- The cost of machine time for an injection molding press can range from $30 to $300 per hour. The rate depends on the machine’s size and capabilities, as well as the region or country where the molding is done. Larger machines that can handle bigger molds and higher volumes will cost more to run.
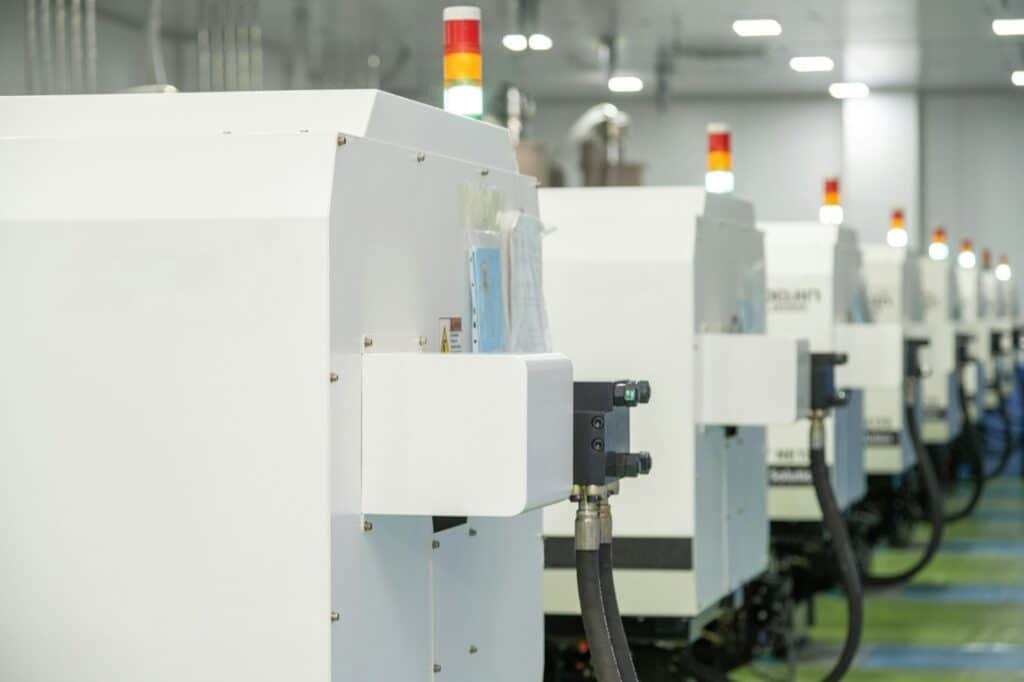
4. Labor Costs
- Labor costs can vary based on the region and the complexity of the molding process. In some cases, labor costs are minimal because the process is highly automated, but additional costs might arise for manual assembly, quality control, or secondary operations. Labor costs typically range from $15 to $50 per hour.
5. Production Volume
- The overall cost per part decreases with higher production volumes due to the amortization of mold and setup costs. For small production runs (under 1,000 parts), the cost per part may range from $2 to $10 or more. For large runs (100,000 parts or more), the cost per part can drop from a few cents to a few dollars.
6. Part Complexity
- More complex parts with intricate details, undercuts, or threads may require additional mold features such as slides, lifters, or more precise machining, increasing the mold cost and cycle time (time required to produce each part).
7. Post-Processing Costs
- Additional costs may include painting, printing, assembly, or packaging post-processing operations. Depending on the specific operations required, these can add anywhere from a few cents to several dollars per part.
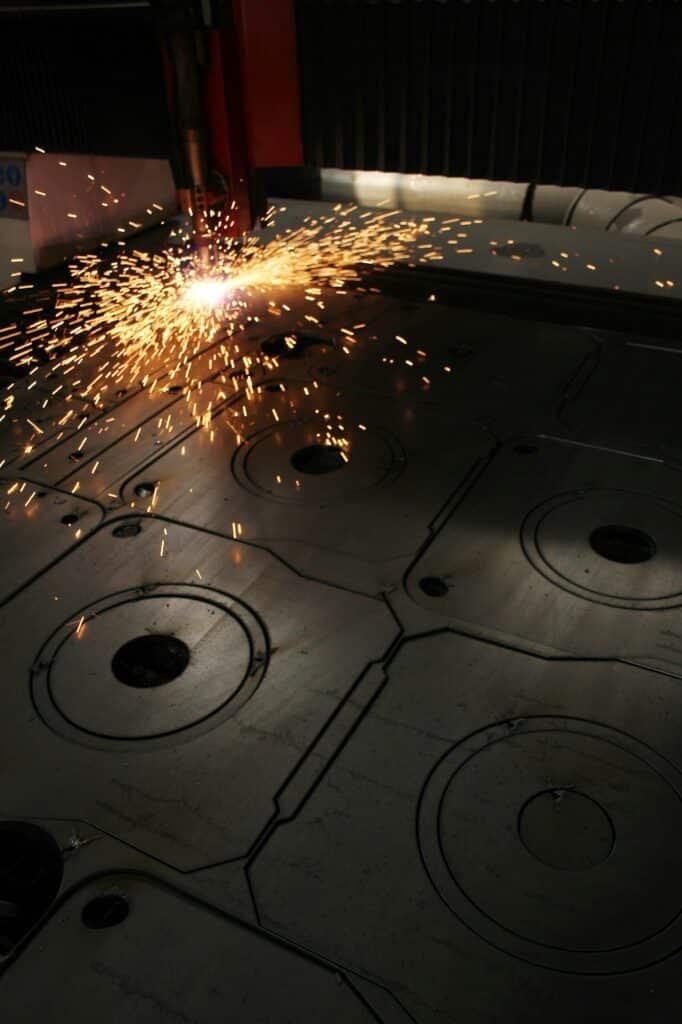
8. Quality Control and Inspection
- Depending on the industry standards and requirements (such as automotive or medical), additional costs may be incurred for quality control and inspection processes to ensure each part meets the required specifications.
Overall Cost Estimation
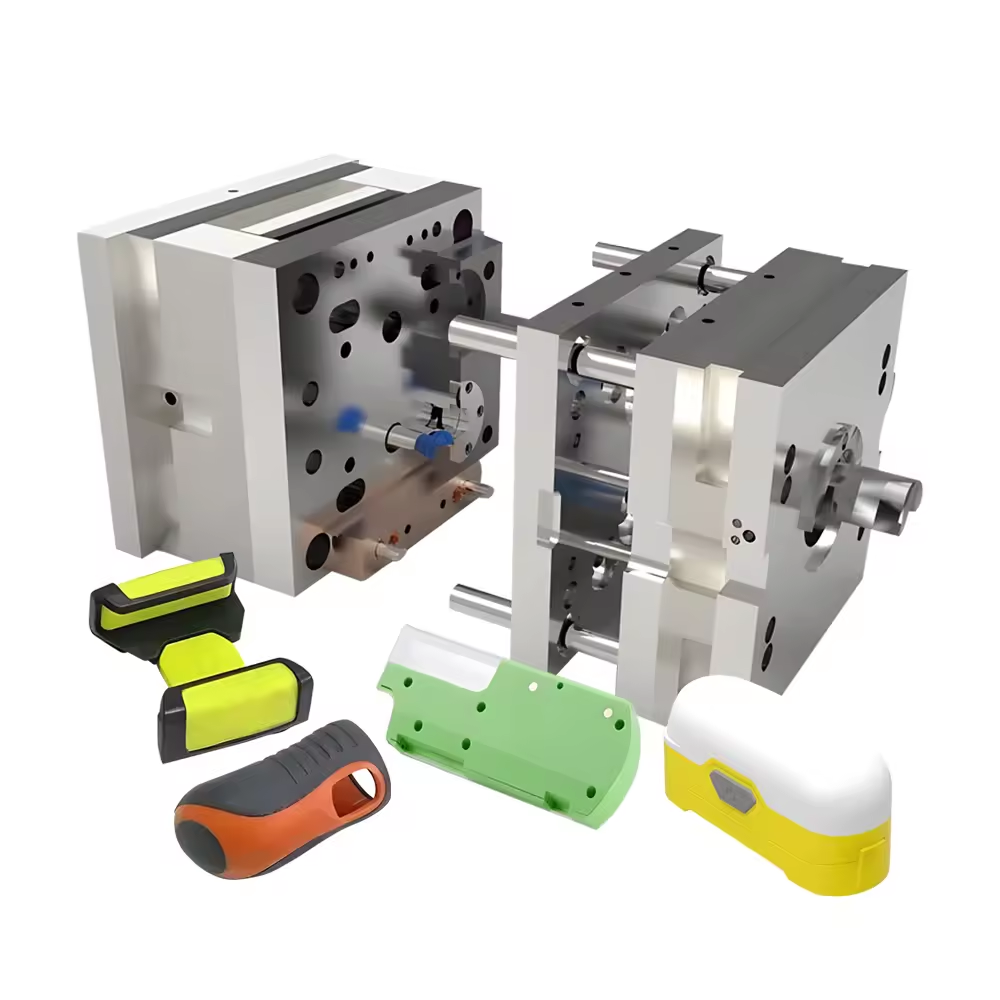
- For a small-scale production (1,000 parts or less), the injection molding cost might range from $3,000 to $10,000.
- For medium-scale production (10,000 parts), the injection molding cost might range from $5,000 to $20,000.
- For large-scale production (100,000 parts or more), the injection molding cost might range from $10,000 to $50,000 or higher.
7 Key FAQs for Injection Molding Cost
1. What factors determine injection molding cost?
Injection mold costs depend on material (steel vs. aluminum), complexity (side actions, micro-features), and cavity count. Aluminum molds cost 5,000–30,000 (prototyping), while hardened steel molds range 30,000–200,000+ (mass production).
2. How does production volume affect per-unit costs?
- Prototypes (50–500 units): $10–50/unit (aluminum molds).
- Mass production (10,000+ units): $0.50–5/unit (steel molds). High-volume orders spread tooling costs, lowering per-unit prices.
3. Why does part complexity increase injection molding cost?
Complex designs require:
- Multi-cavity molds (+20–50% tooling costs).
- Tighter tolerances (±0.05mm) (+15–30% machining time).
- Overmolding/insert molding (+$5–20/part).
4. What post-processing costs should I anticipate?
- Surface finishes: SPI-A1 (glossy) adds 0.50–2/part; EDM textures add 0.50–2/part; EDM textures add 2–10/part.
- Painting/coating: $1–5/part.
- Assembly/QA: $0.50–3/part.
5. How do quality control measures influence overall costs?
- First Article Inspection (FAI): $200–1,000.
- CMM checks: $50–200/hour.
- Certifications (ISO 13485, IATF 16949): Annual audits add $5,000–15,000.
6. Can I reduce costs without compromising quality?
- Design simplification: Eliminate undercuts and standardize wall thickness.
- Material optimization: Use regrind resin for non-critical parts (saves 10–20%).
- Supplier negotiation: Bundle projects for volume discounts.
7. What hidden costs do buyers often overlook?
- Mold maintenance: $1,000–5,000/year for steel molds.
- Shipping/import duties: 5–15% of total costs for overseas suppliers.
- Tooling modifications: $500–10,000 for design changes post-approval.
Conclusion
The exact cost will depend heavily on the project’s specifics, such as the complexity of the design, material choice, volume of production, and geographic location of the manufacturing facility.
If you need a more precise quote for a specific project, consulting directly with a professional injection molding service provider is best.