In the realm of manufacturing, selecting the right materials for injection molding is a critical decision that directly impacts the quality, durability, and overall success of a product. As a customer, understanding the key factors involved in choosing injection molding materials is essential for ensuring that your production process aligns seamlessly with your requirements and expectations. In this guide, we will explore the intricacies of material selection, empowering you to make informed decisions that contribute to the success of your manufacturing endeavors.
Understanding the Basics:
Before delving into the specifics, it’s crucial to grasp the fundamentals of injection molding. Injection molding is a widely used manufacturing process that involves injecting molten material into a mold cavity, allowing it to cool and solidify. The choice of materials plays a pivotal role in determining the final product’s performance, aesthetics, and cost-effectiveness.
Acrylonitrile Butadiene Styrene (ABS)
ABS is kinda like the middle ground – not too strong or weak. But let me tell ya, it can take a hit! It’s resistant to impacts and chemicals, and you can easily process it. And the best part? It won’t break the bank, making it a go-to for keeping production costs low. We use it a lot for making plastic bottles for drinks, cool toys, and even the insides of cars.
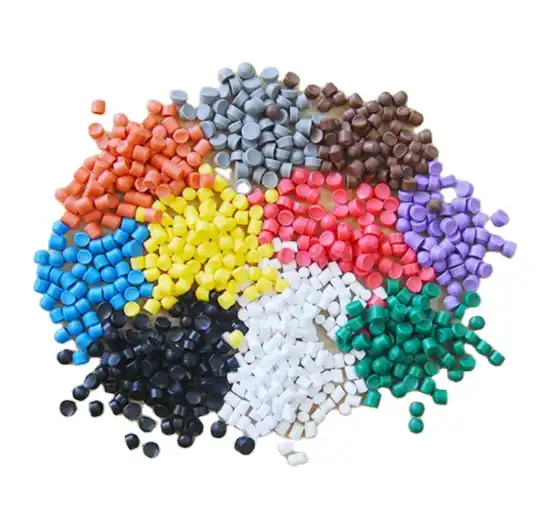
Nylon (Polyamide)
Nylon has some serious heat resistance and can handle chemicals like a champ. Perfect for tough mechanical parts in cars, especially in the hot and heavy world of injection molding.
Acrylic
When you want something see-through, acrylic’s your buddy. It’s tough, can resist scratches, and won’t be bothered by the weather. Perfect for windows and flashy lighting gear. Oh, and it’s even hanging out in fridges, keeping things cool without any funky chemicals.
Polyvinyl Chloride (PVC)
PVC is a solid choice – not too resistant, not too weak. It’s got a bit of strength and plays nice with molds. We use it to beef up other materials, like containers, fences, and flexible parts.
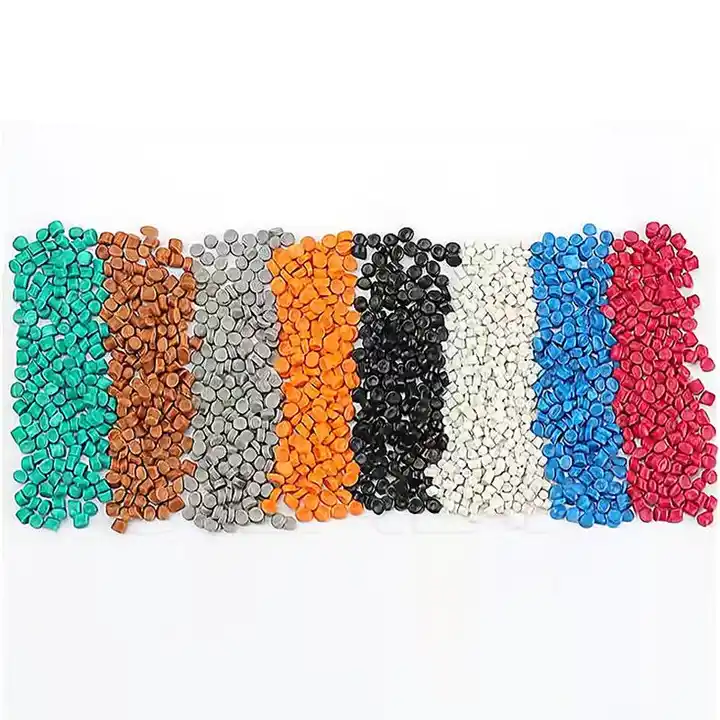
Polycarbonate
Polycarbonate is the tough guy in the group. Strong, predictable, and shrinks uniformly when molded. If you need something stronger than acrylic, this is the one you want.
Polypropylene (PP)
Polypropylene is like the superhero of impact strength, elasticity, and toughness. It’s the go-to for food storage and packaging – no harmful chemicals here!
Polyoxymethylene (POM)
This one’s a heavy hitter in the automotive scene. Gears, fasteners, ball bearings – you name it. Tough, rigid, and perfect for keeping things moving smoothly.
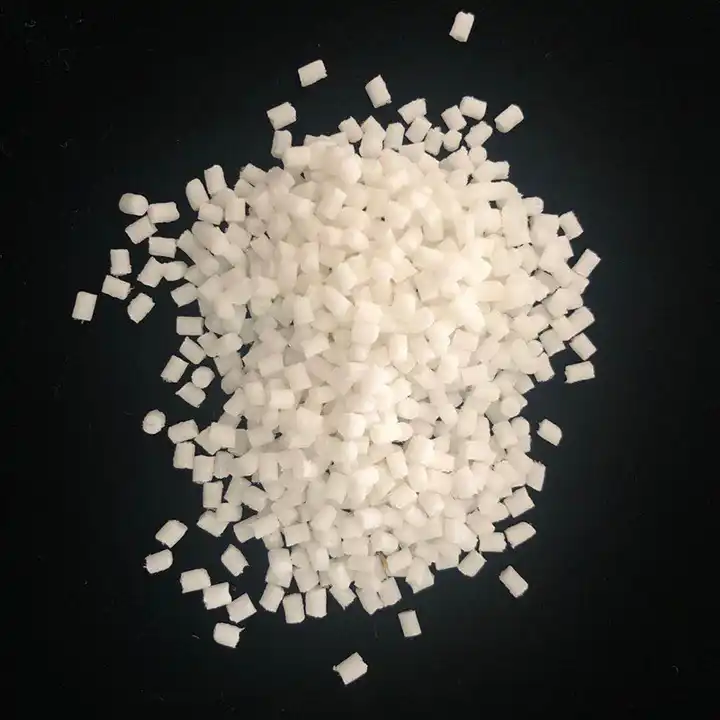
Styrene Acrylonitrile (SAN)
SAN may not be the toughest cookie, but it’s crystal clear and can handle whatever the weather throws. Great for making cosmetic packages, containers, auto parts, and electrical stuff.
Polystyrene (PS)
Now, when it comes to polystyrene, you’ve got choices. High Impact Polystyrene (HIPS) is strong and solid – think hard toolboxes. Conversely, General Purpose Polystyrene (GPPS) is see-through and perfect for everyday household items.
Material Properties
Different materials exhibit varying properties that directly influence their suitability for specific applications. Considerations such as strength, flexibility, temperature resistance, and chemical compatibility should align with the product’s intended purpose. For instance, automotive components may require high-strength and heat-resistance materials, while consumer electronics might prioritize aesthetics and lightweight properties.
Cost Considerations
Balancing performance with cost is a perpetual challenge in manufacturing. While high-performance materials may enhance the product’s functionality, they can also escalate production costs. Assessing your budget constraints and understanding the trade-offs between material costs and product performance is crucial. Striking the right balance ensures a cost-effective production process without compromising on quality.
Material Compatibility with Molding Process

Each material responds differently to the injection molding process. Factors such as melt flow index, shrinkage rates, and cooling times must be considered. Compatibility with the molding equipment and the intricacies of the process itself should be thoroughly evaluated to prevent production challenges and ensure a smooth manufacturing workflow.
Environmental Impact
Considering the environmental impact of chosen materials is imperative in an era where sustainability is a top priority. Eco-friendly and recyclable materials contribute to a company’s corporate social responsibility and align with growing consumer preferences for sustainable products. Evaluate the life cycle of materials and their recyclability to make environmentally conscious choices.
Regulatory Compliance
Different industries are subject to varying regulations and standards. Ensuring that the selected materials comply with industry-specific regulations is paramount. This guarantees the safety and quality of the end product and minimizes the risk of legal complications. Stay informed about the regulatory landscape relevant to your industry and make choices that align with the required standards.
Material Testing and Prototyping
Before committing to large-scale production, it is advisable to conduct thorough material testing and prototyping. This step allows for identifying potential issues, fine-tuning material properties, and optimizing the production process. Investing time and resources in the testing phase can prevent costly errors and ensure that the final product meets or exceeds customer expectations.
Supplier Relationships
The choice of material is intrinsically tied to the relationships with material suppliers. Establishing strong partnerships with reputable suppliers ensures a reliable and consistent supply of high-quality materials. Regular communication and collaboration with suppliers also provide access to valuable insights and updates on new materials or advancements in existing ones.
Conclusion
In the dynamic manufacturing world, choosing the right injection molding materials is a multifaceted process that requires careful consideration of numerous factors. Customers can confidently navigate this complex landscape by understanding the properties, costs, environmental impact, and compliance aspects of materials. Collaborating closely with material suppliers and investing in testing and prototyping further enhances the likelihood of a successful production process. Armed with this knowledge, customers can make informed decisions that meet their immediate needs and pave the way for innovation and sustainability in the long run.