What is Injection Molding?
Injection molding is a highly efficient manufacturing process that involves injecting molten material—typically thermoplastics, silicones, or metals—into a precision-engineered mold cavity. Once cooled and solidified, the material forms a finished part with consistent dimensional accuracy. This method is widely regarded as the gold standard for high-volume production due to its ability to replicate intricate geometries at scale while minimizing material waste.
At the heart of the process lies the injection unit, which heats raw polymer pellets to a molten state (e.g., 200–300°C for ABS) and injects them into the mold under pressures of 1,000–20,000 psi. After cooling, the part is ejected and ready for post-processing or assembly.
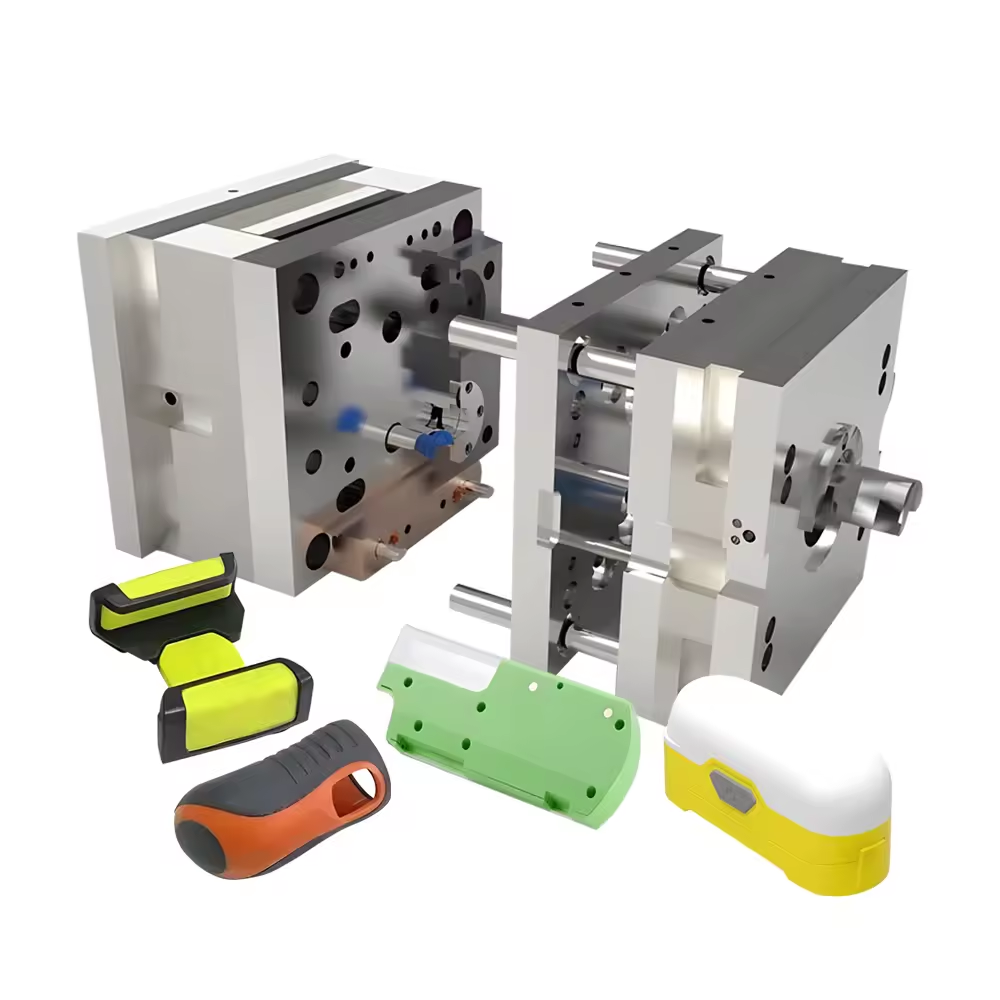
Medical-Grade Injection Molding Solutions: A Critical Application
The medical industry exemplifies the pinnacle of precision in injection molding. Surgical instruments, implantable devices, and diagnostic equipment demand zero-defect production, tolerances as tight as ±0.005mm, and biocompatible materials like PEEK or USP Class VI resins. For instance, a single defective component in a pacemaker could have life-threatening consequences, underscoring why ISO 13485-certified medical molding requires rigorous process validation and cleanroom environments.
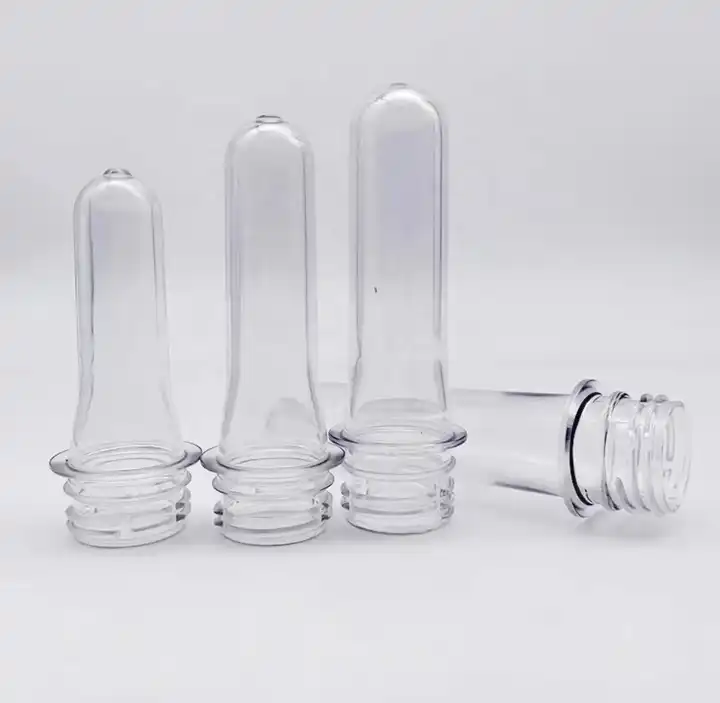
Types of Injection Molding Processes and Their Features
Selecting the appropriate molding technique is critical to meeting project specifications. Below is a comparative analysis of key methods:
Process | Key Features | Ideal Applications |
Standard Plastic Molding | – High-volume output (10,000+ units) – Compatible with ABS, PP, PC | Automotive trim, consumer packaging |
Insert Molding | – Integrates metal inserts (e.g., brass threads) into plastic – Enhances part durability | Medical device housings, electrical connectors |
Liquid Silicone Rubber (LSR) | – Heat-resistant (up to 250°C) – Biocompatible and flexible | Infant care products, respiratory masks |
High-Pressure Molding | – Achieves complex geometries – Reduces sink marks | Microfluidic chips, aerospace components |
Overmolding | – Bonds multiple materials (e.g., TPE over ABS) – Improves ergonomics | Tool grips, wearable device casings |
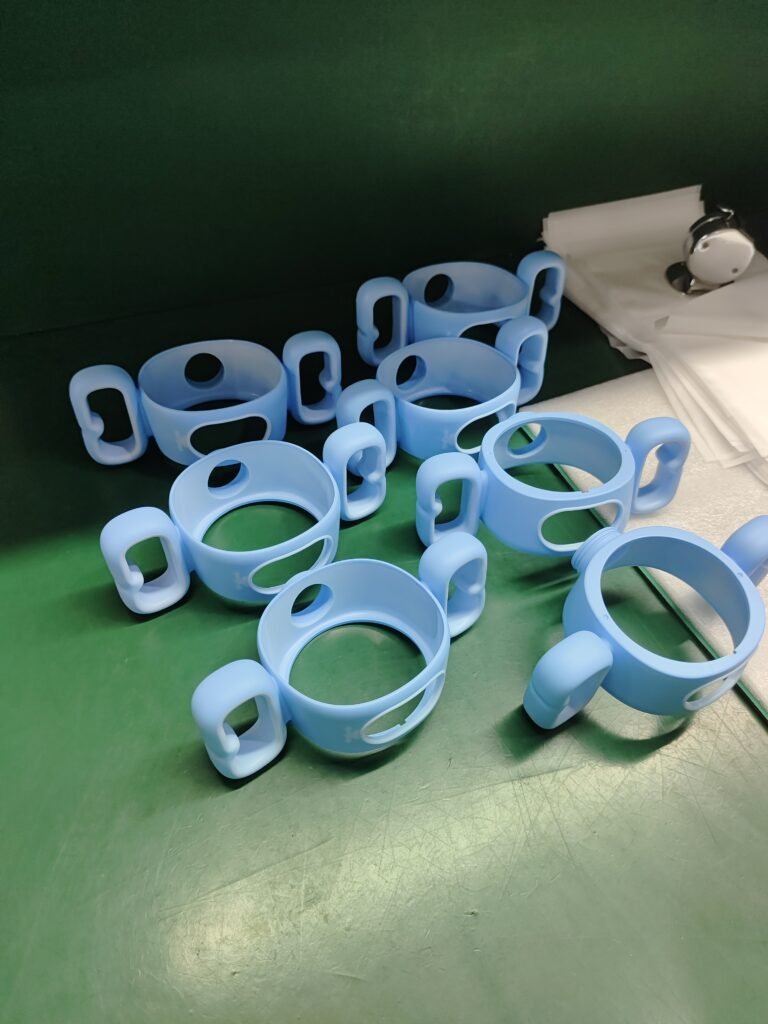
Low-MOQ Injection Molding: Bridging Prototyping and Production
For startups or niche markets requiring 50–1,000 units, low-minimum order quantity (MOQ) services utilize aluminum molds. These offer faster turnaround (2–4 weeks) and lower upfront costs (1,500–5,000), making them ideal for functional prototyping or limited-run medical trials.
Technological Advancements in Injection Molding
Modern innovations have transformed injection molding into a data-driven, sustainable process:
1. AI-Powered Quality Control
- Machine learning algorithms analyze real-time sensor data (pressure, temperature) to predict defects like warpages or voids, reducing scrap rates from 8% to less than 1% in automotive applications.
2. Micro-Injection Molding
- Produces parts as small as 0.01g (e.g., micro-optics for endoscopic tools) with tolerances of ±0.002mm, enabled by servo-electric presses and ultra-fine nozzles.
3. Sustainable Practices
- Closed-loop systems recycle 95% of sprues and runners. Bio-based resins (e.g., PLA from corn starch) reduce carbon footprints by 30% compared to conventional plastics.
High-Speed Molding for Automotive Components
A German automaker slashed cycle times by 40% (from 50 to 30 seconds) using high-speed electric presses with 4,000-ton clamping force. This allowed the production of 500,000 dashboard panels annually while maintaining ISO 9001 quality standards.
Strategic Implementation of Injection Molding Services
To maximize ROI, manufacturers should:
- Collaborate Early: Engage molders during the design phase to optimize gate locations and cooling channels.
- Leverage Hybrid Tooling: Combine steel cores (for critical features) with aluminum frames to balance durability and cost.
- Audit Certifications: Ensure suppliers meet industry-specific standards (e.g., IATF 16949 for automotive).
Injection Molding Services: Core Principles and Industry Applications
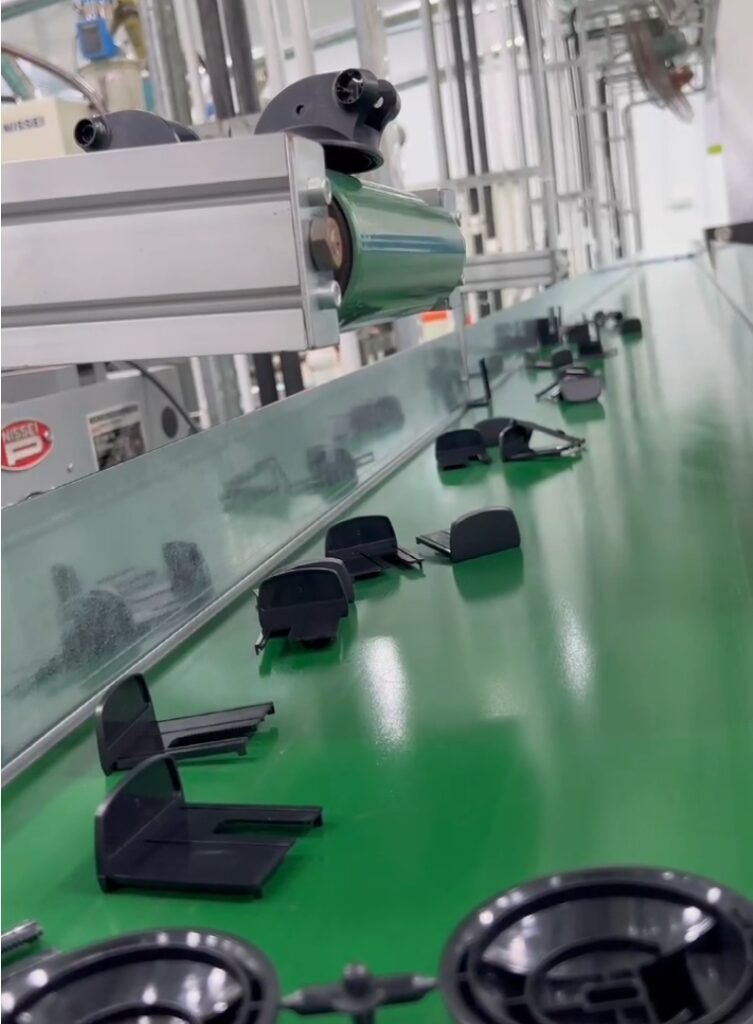
Defining Injection Molding and Its Role in Modern Manufacturing
Injection molding services transform raw polymers into precise components by injecting molten material into custom-designed molds. This process dominates industries like automotive, medical devices, and consumer electronics due to its scalability, repeatability, and cost efficiency. For instance, a single mold can produce 10,000+ parts with tolerances as tight as ±0.01mm, making it indispensable for high-volume production.
- Low-Minimum Order Quantity (MOQ) Injection Molding
- High-Speed Injection Molding for Automotive Components
- Medical-Grade Injection Molding Solutions
Exploring Types of Injection Molding Services
Standard vs. Specialized Molding Techniques
- Standard Injection Molding:
- Materials: ABS, PP, HDPE.
- Applications: Consumer goods, packaging.
- Cost: 0.10–2.00 per unit for orders >10,000 units.
- Low-MOQ Injection Molding:
- Tooling: Aluminum molds (lifespan: 5,000–10,000 cycles).
- Lead Time: 2–4 weeks.
- Ideal For: Prototypes or niche markets requiring 50–1,000 units.
- High-Speed Injection Molding for Automotive Components:
- Cycle Time: As low as 15 seconds per part.
- Materials: Glass-filled nylon, PEEK.
- Machinery: Hydraulic or electric presses with clamping forces up to 4,000 tons.
A Tier-1 automotive supplier reduced dashboard panel costs by 18% using high-speed molding with multi-cavity steel molds, achieving a cycle time of 22 seconds per part.
Cutting-Edge Innovations in Injection Molding Technology
Technologies Redefining Precision and Sustainability
- AI-Driven Process Optimization:
Sensors monitor real-time parameters (temperature, pressure) to reduce defects by 25%.
- Micro-Injection Molding:
Produces parts as small as 0.1g for medical devices like insulin pump gears.
- Eco-Friendly Molding:
Biodegradable resins (e.g., PLA) and in-house recycling cut waste by 30%.
Comparison Table: Traditional vs. Advanced Molding
Parameter | Traditional Molding | Advanced Molding |
Cycle Time | 30–60 seconds | 10–25 seconds |
Energy Consumption | High (hydraulic) | Low (electric) |
Defect Rate | 5–8% | 1–3% |
Material Waste | 15–20% | 5–10% |
Critical Factors in Choosing an Injection Molding Partner
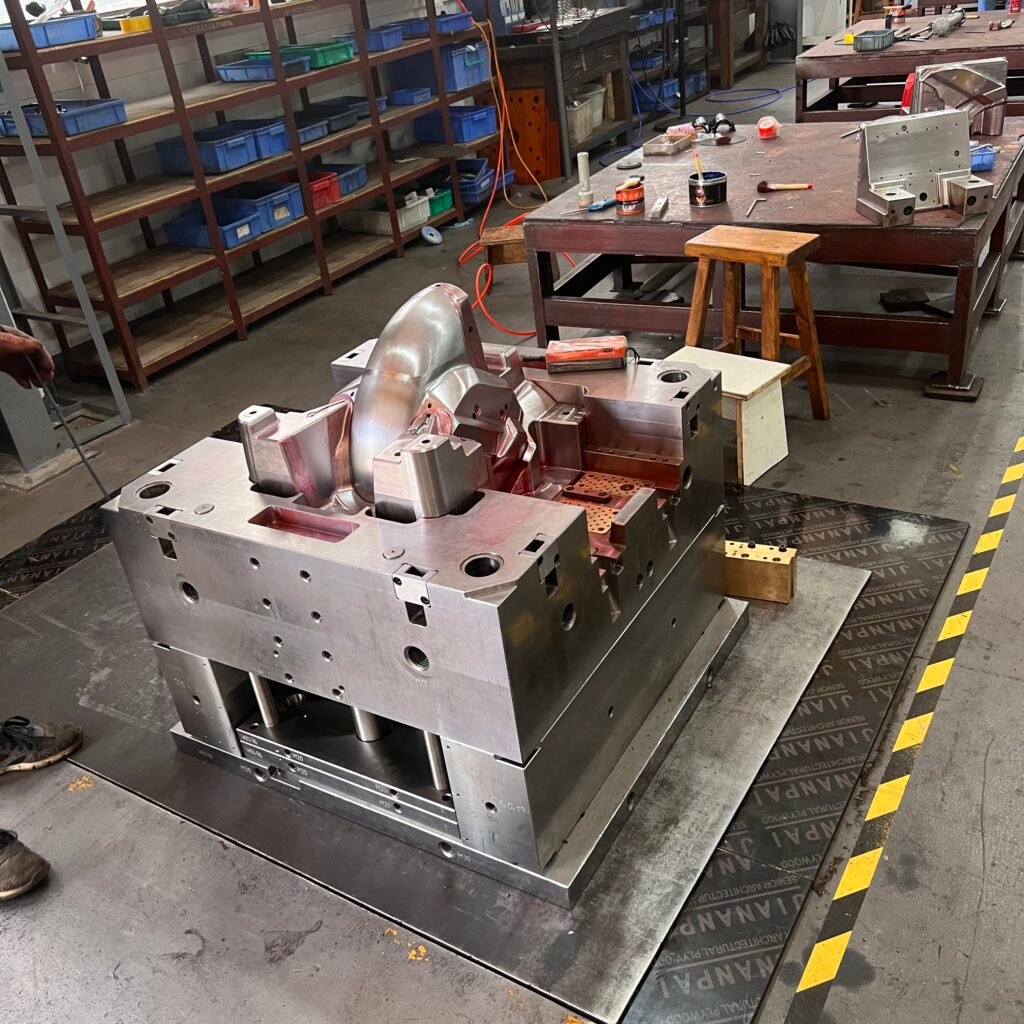
5 Metrics to Evaluate Service Providers
- Technical Expertise:
Look for ISO 9001 or IATF 16949 certifications.
- Material Portfolio:
Ensure support for engineering-grade resins (e.g., Ultem, PPSU).
- Scalability:
Verify capacity to scale from low-MOQ prototypes to 100,000+ unit orders.
- Quality Assurance:
Demand mold flow analysis, CMM inspections, and batch testing.
- Sustainability Practices:
Prioritize suppliers using renewable energy or closed-loop recycling.
A medical device manufacturer achieved FDA compliance by partnering with a molder specializing in medical-grade injection molding solutions, reducing part rejection rates from 8% to 1.5%.
Strategic Collaboration With Injection Molding Experts
Maximizing ROI Through Partnership
- Design for Manufacturability (DFM):
Engineers optimize wall thickness, draft angles, and gate locations to cut tooling costs by 20%.
- Co-Development Prototyping:
Jointly refine designs using 3D-printed molds for rapid iteration.
- Supply Chain Integration:
Seamless material sourcing (e.g., pre-colored resins) reduces lead times by 15%.
FAQs on Injection Molding Services
Top 10 Client Questions
- What’s the minimum order quantity (MOQ) for injection molding?
MOQs range from 50 (prototypes) to 10,000+ units (mass production).
- How do I choose between aluminum and steel molds?
Aluminum: Faster/cheaper for prototypes. Steel: Durable for high-volume runs.
- Can you handle overmolding or insert molding?
Yes, but specify material combinations (e.g., TPE over PP) upfront.
- What’s the cost difference between domestic and offshore molding?
Offshore saves 20–40% but risks longer lead times and quality issues.
- How are tolerances ensured in high-precision molding?
Through CMM inspections, temperature-controlled rooms, and servo-driven presses.
- Do you provide material certifications (e.g., FDA, RoHS)?
Reputable suppliers offer full traceability and compliance documentation.
- What’s the lead time for mold fabrication?
3–8 weeks for steel molds; 2–4 weeks for aluminum.
- Can existing molds be modified for design changes?
Yes, but costs depend on the complexity of revisions.
- How sustainable are your injection molding processes?
Many providers use energy-efficient machines and recycled materials.
- What post-molding services do you offer?
Assembly, laser etching, and ISO-compliant packaging.
Conclusion: Aligning Services With Business Goals
Selecting the right injection molding services requires balancing precision, cost, and scalability. For automotive clients, prioritize high-speed molding and IATF-certified partners. Medical projects demand ISO 13485 compliance and micro-molding capabilities. Always audit facilities, request samples, and negotiate flexible MOQs to mitigate risks.