Injection molding molds are essential tools in the plastic manufacturing process. They create parts by injecting molten plastic into a mold cavity. The two primary halves of the mold—core and cavity—form the internal and external features of the plastic part. This process involves several precision-engineered components and techniques that ensure high-quality, repeatable production runs for various industries.
This guide provides in-depth information about mold design, material selection, critical design considerations, and maintenance practices, with practical insights into real-world applications across industries.
1. What Are Injection Molding Molds?
Injection molding molds are factory tools used to form molten plastic into a solid shape by injecting under pressure using a plastic material in a mold. That cavity is precisely shaped to reflect the product’s final form, which is why the mold is usually made of two components:
- Core Side: The inner configuration of the molded piece, including things like holes, threads, or other complex shapes. The core side is essential to forming the inner geometry of the product.
- Cavity Side: Defines the outer geometry and characteristics of the part. This side comes into contact with molten plastic directly and shapes the outer surface of the final component.
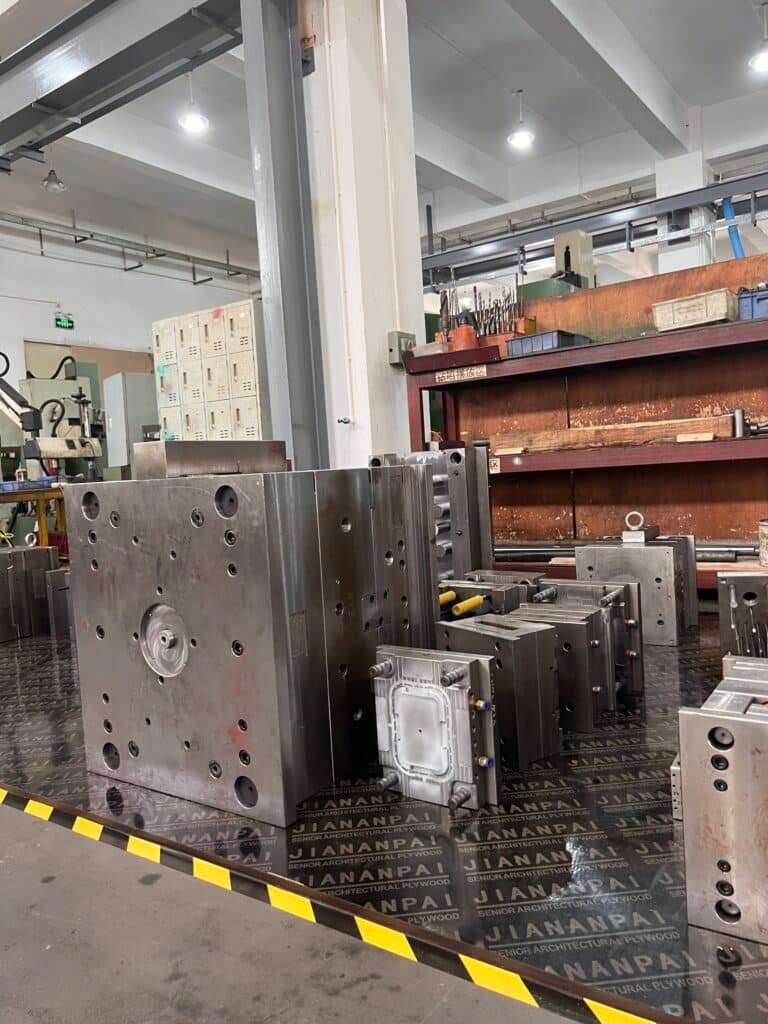
Key Functions of Injection Molding Molds:
- Material Distribution: A network of channels (sprue, runners, and gates) directs the molten plastic within the mold. This way, the material is uniformly distributed in all the cavities and flows to the entire mold section.
- Cooling: Injection molding molds include cooling channels that pass coolant (water most of the time) through the mold. This helps to cool and solidify the liquid polymer that has been injected, allowing parts to be easily removed from the molds without warping.
- Ejection: Once the plastic has coalesced and cooled, operator pins or plates shove the molded component from the catheter. This allows the part to be released safely without damaging the mold or the part itself.
2. Core Components of a Mold

Each mold has a series of core components that play vital roles in the injection molding. The following components are essential for optimal mold performance:
Component | Purpose | Material |
Mold Base | Holds and aligns the mold components | P20 steel, 718H |
Cavity & Core | Defines the shape of the part | H13 steel, aluminum (Al7075) |
Ejector System | Pushes parts out after cooling | SKD61, hardened steel |
Cooling Channels | Regulates temperature to maintain efficiency | Copper alloys, stainless steel |
Vents | Releases trapped air and gases during molding | Machined slots (0.02–0.03mm) |
Mold Base
The mold base is an important component that holds all the mold elements in place, ensuring their correct alignment. Often, the base is made of P20 or 718H steel, providing a durable, precision fit that is easily machined.

Cavity & Core
The cavity inside the mold’s surfaces defines the part’s external features, while the core defines its internal features. The parts are either made from heat-resistant and wear-resistant materials like H13 steel or aluminum alloys like Al7075, which is mostly used for low-volume and rapid prototyping.
Ejector System
These allow the finished part to cool, and the ejector system pushes it out of the mold once it’s cool. The purpose of this system is to safely eject the part without damaging the part of the mold using hardened steel ejector pins or plates (e.g., SKD61).

Cooling Channels
Cooling channels are integrated inside the mold to regulate temperature and optimize cycle times. They are typically made from copper alloys and stainless steel, with the high thermal conductivity needed to help rapidly and evenly cool the part.
Vents
Vents are small machining slots or channels that allow trapped air or gas to escape during injection. If not well-vented, the trapped air can create defects in your part (e.g., bubbles or voids, pressure build-up, etc.) and, consequently, part failure.
3. Types of Injection Molding Molds
Injection Molding molds come in various types according to different manufacturing needs, such as high-volume production or specialized applications.
① Two-Plate Molds
Type: The simplest and cheapest mold design consists of two-parting lines. The runner allows the passive flow of plastic into the cavity, and a parting line separates the Core and cavity.
Best For: Parts requiring simple geometries without side actions are best for two-plate molds; examples include bottle caps, automotive clips, and small consumer goods.
Cycle Time: The cycle time for two-plate molds is between 15 and 30 seconds, allowing for high-speed production of straightforward components.
② Three-Plate Molds
Structure: Two parting lines separate the runner system from the parts. Parting lines can be simple or involve more complex designs, such as multi-cavity molds allowing multiple parts to be formed in each mold cycle.
Ideal For: Three-plate molds are ideal for multi-cavity production, which means small electronic connectors or large quantities of consumer goods.
Disadvantage: The main disadvantage of three-plate molds is the additional tooling cost, as these injection molding molds can be 20–30% more expensive than two-plate molds due to their increased complexity.
③ Hot Runner Molds
Structure: Hot runner molds are designed with a heated manifold that keeps the plastic molten as it moves through the runners. There is no sprue, which also reduces waste.
Advantages: Hot-runner molds are more efficient because they eliminate sprue waste, and cycle times are faster (5–15% lower cycle time than cold-runner systems).
Cost: Hot runner systems are typically 30–50% more expensive than cold runner systems because of the complexity of the heating elements and the manifold system.
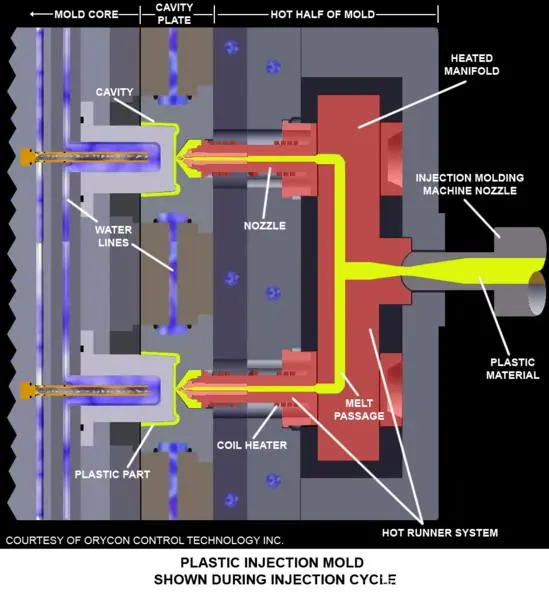
④ Overmolding/Insert Molds
Process: Overmolding is when a second material, generally plastic but also metal, is injected over the surface of an existing substrate. An example is utilizing soft and hard plastics; this process can be utilized to bond two dissimilar materials together.
Applications: Overmolding is widely used in medical devices with built-in sensors, soft-touch handles for hand tools, and multi-material components in electronic systems.

4. Mold Materials: Choosing the Right Alloy
Selecting the right material for the mold is critical for achieving the desired durability, finish, and performance. Here are some of the most commonly used mold materials:
Material | Pros | Cons | Best For |
P20 Steel | Affordable, good polishability | Low wear resistance | Prototypes, low-volume (<50k cycles) |
H13 Tool Steel | High heat resistance, durable | Expensive, heavy | High-volume production |
Aluminum (7075-T6) | Lightweight, fast machining | Limited lifespan (~10k shots) | Prototyping, low-volume production |
Beryllium Copper | Superior thermal conductivity | Toxic during machining | High-speed cooling zones |
P20 Steel
A common choice in at-the-spot prototypes to low-volume production. (Affordable, really good polishability). Indeed, its wear resistance is inferior compared to other materials, such as H13 steel.
H13 Tool Steel
High-volume production runs are needed, and H13 tool steel is widely used for its superior heat resistance and durability. However, it is more expensive and heavier, affecting the total tooling cost.
Aluminum (7075-T6)
Dave: Lightweight and quick to machine, aluminum alloys (e.g., 7075-T6) are great for prototyping and low-volume manufacturing. Aluminum molds, on the other hand, although they can be fabricated with more speed and cost, typically have a shorter lifespan, so they aren’t as good for high-volume applications.
Beryllium Copper
Beryllium copper is employed in high-speed cooling zones due to its high thermal conductivity. However, it is toxic when machined, necessitating specialized safety precautions.
5. Critical Design Considerations
Mold design is also vital to the injection molding process. Design considerations include various elements that affect the efficiency of the mold, the quality of the final part, and the production cycle times.
① Gate Design
A gate is where molten plastic enters the mold cavity. Types of gates are edge gates, submarine gates, and hot-tip gates.
Edge Gates: best for flat parts, results in very little cosmetic damage to the molded surface.
Submarine Gates: These gates are perfect for small pieces like gears, as they automatically trim any excess material.
Hot Tip Gates: feature in hot runner systems to guarantee clean surface finishes and no additional trimming
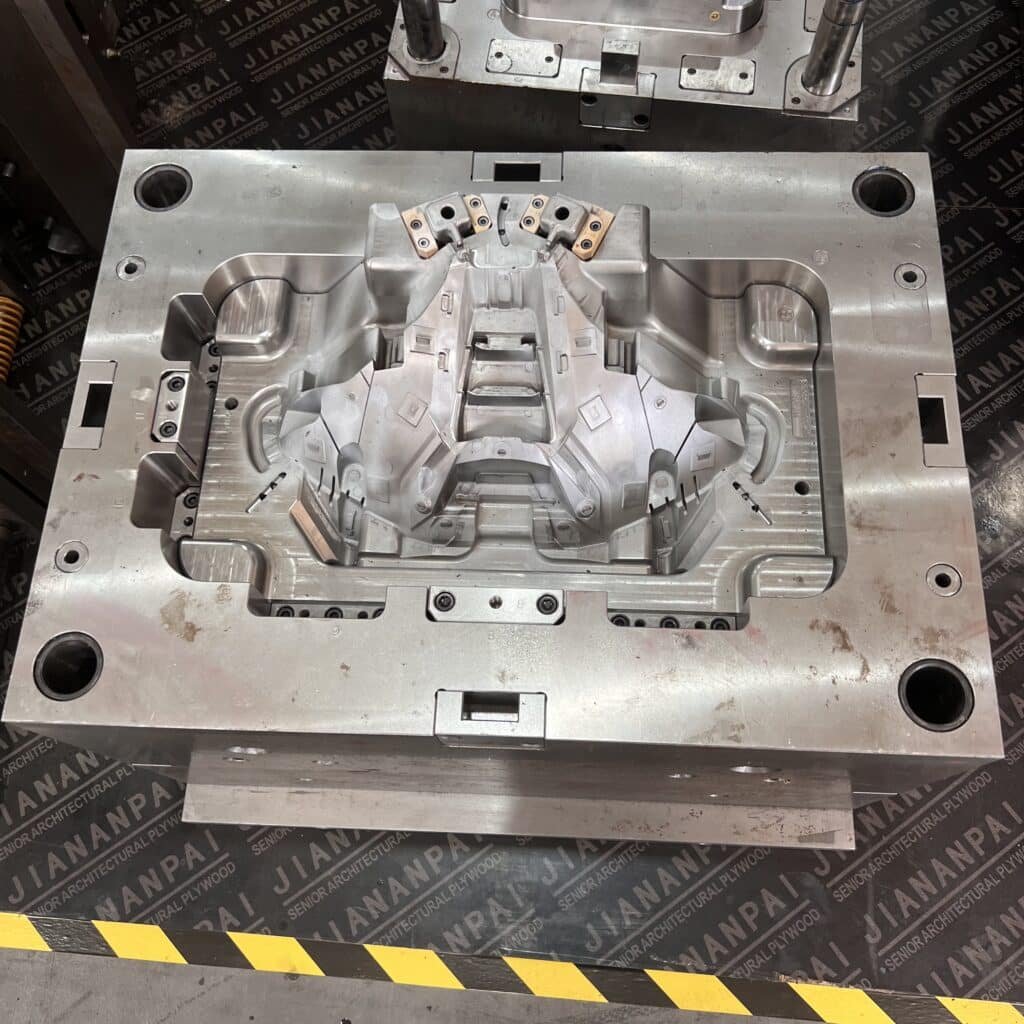
② Draft Angles
Draft angles are the tapers on the sides of the mold cavity that aid in removing the part from the mold. Generally, the minimum draft angle is 1°–2° for textured surfaces and 0.5° for polished cores. Not following proper draft angles can cause parts to stick in the Mold, increasing the scrap rate and reducing overall production efficiency.
③ Cooling Optimization
Cooling is among the most important factors in injection molding. This decline extends production cycle times while also reducing part quality. Cooling time should typically represent 50–60% of the cycle time. Newer technologies, such as 3D-printed conformal cooling channels, can help optimize cooling, resulting in shorter cycle times and improved production efficiency.
6. Maintenance & Lifespan Extension
Proper Mold Maintenance is Crucial for Maintaining the Parts’ Consistency in Quality and increasing the Mold Life. Common maintenance activities include lubricating ejector pins, polishing cavities, and re-hardening steel cores. With proper maintenance, injection molding molds can last for many years with optimum efficiency.
Maintenance Practices:
- Daily: Grease ejector pins, inspect wear, and clean mold faces.
- Monthly: Blend the mold cavities with diamond paste for a smooth surface finish;
- Annually: Re-hardening steel cores via nitriding can extend the mold’s life by up to 100k cycles.
If not maintained properly, the mold’s life span will dramatically decrease. For instance, if H13 steel molds are not regularly maintained, their lifespan can diminish by 40%, leading to more replacements and, consequently, longer downtimes in production.
7. Industry-Specific Applications
Injection molding molds are used across various industries, each with specific requirements for mold design, material selection, and production processes.
Industry | Mold Requirements | BFY Mold’s Edge |
Medical | FDA-compliant materials, ISO 13485 certification | Validated cleanroom molding |
Automotive | High-gloss finishes, tight tolerances (±0.02mm) | In-house CMM inspection & PPAP support |
Consumer Electronics | Micro-molding (<1g parts), EMI shielding | LSR-overmolding for waterproof seals |
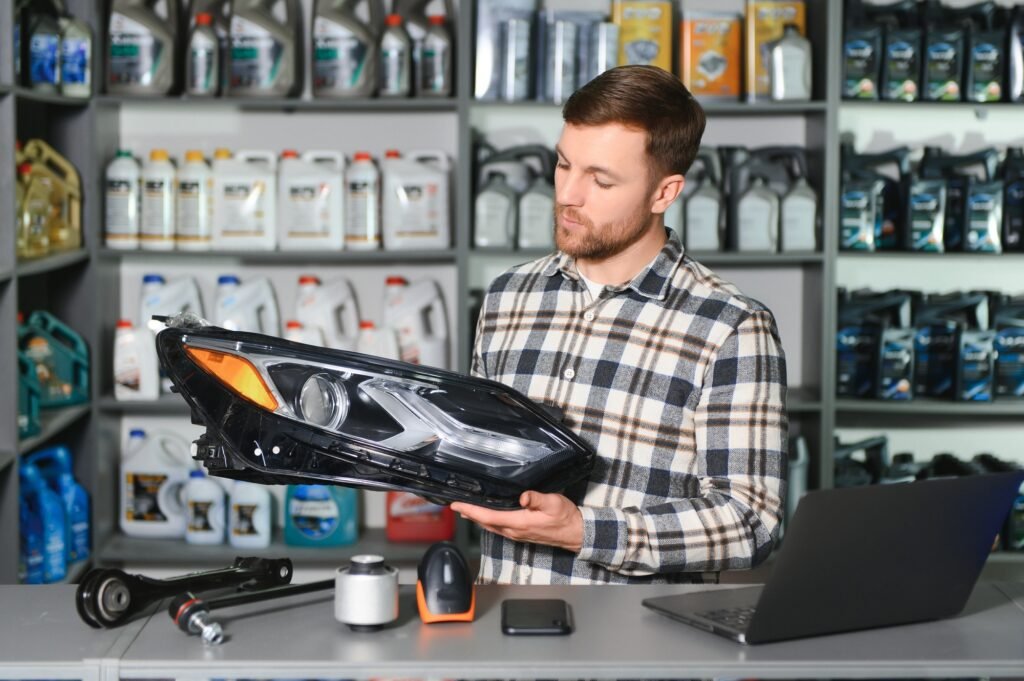
Top 10 FAQs About Injection Molding Molds
1. What materials are commonly used for injection molding molds?
Molds are typically made from hardened steel (e.g., P20, H13) for high-volume production or aluminum (e.g., 7075-T6) for prototypes and low-volume runs. Steel offers durability (500,000+ cycles), while aluminum reduces costs and lead times.
2. How do I choose between steel and aluminum molds?
- Steel molds: Best for >100,000 units, complex geometries, and tight tolerances (±0.01mm).
- Aluminum molds: Ideal for prototypes or <10,000 units, offering 50% faster turnaround and 30–40% lower costs.
3. What is the typical lifespan of an injection mold?
- Steel molds: 500,000–1,000,000 cycles with proper maintenance.
- Aluminum molds: 5,000–10,000 cycles. Factors like material abrasiveness (e.g., glass-filled resins) and cooling methods affect longevity.
4. How much does a custom injection mold cost?
Costs range from 5,000–5,000–100,000+, depending on:
- Material: Steel vs. aluminum.
- Complexity: Side actions, undercuts, or micro-features.
- Size: Larger molds require more material and machining time.
5. What is the lead time for manufacturing a custom mold?
- Aluminum molds: 2–4 weeks.
- Steel molds: 6–12 weeks.
Expedited services may reduce timelines by 30% but increase costs by 15–25%.
6. What quality control measures ensure mold precision?
Reputable suppliers use:
- CMM (Coordinate Measuring Machine): Verifies tolerances within ±0.005mm.
- Mold flow analysis: Predicts and prevents defects like warping.
- ISO 9001 certification: Ensures standardized processes.
7. Can you modify an existing mold for design changes?
Yes, but costs depend on the complexity:
- Minor changes (e.g., gate resizing): 500–500–2,000, 1–2 weeks.
- Major revisions (e.g., adding cores): 3,000–3,000–15,000, 3–6 weeks.
8. How do you handle mold maintenance and repairs?
Providers offer:
- Preventive maintenance: Regular cleaning, lubrication, and component replacement.
- Emergency repairs: 24/7 support for critical issues (e.g., cracked cavities).
- Reconditioning: Polishing or re-hardening worn surfaces.
9. What industries do you specialize in for mold production?
Top suppliers serve:
- Medical: FDA-compliant molds for syringes or implants.
- Automotive: Multi-cavity molds for dashboards or connectors.
- Consumer Electronics: High-gloss molds for smartphone casings.
10. What post-production support do you provide?
- Technical assistance: Troubleshooting part defects or process optimization.
- Documentation: Mold design files, maintenance logs, and material certifications.
- Spare parts: Immediate access to ejector pins, sliders, or heaters.
Conclusion
Injection molding molds are key to producing high-quality plastic components in various industries. The right type of mold, material, and maintenance options can optimize production, cut costs, and ensure product quality. 3D printing and organic photonic devices are examples of specific applications with their own requirements (such as sub-micron feature morphology) that are enabled by optimal mold design and material selection performance.

For precision mold tooling, BFY Mold offers expert support in design-for-manufacturing (DFM), cost-effective hybrid mold systems, and full lifecycle maintenance services. BFY Mold is your Partner for High-Quality Injection Molding Mold, whether in medical, automotive, or electronics.