1. Cutting-edge Equipment and Techniques
Utilize high-precision equipment tailored for micro-injection molding, including mirror spark machining and electroforming molds, essential for UAV shell injection molding. Each method has its advantages and drawbacks, such as electrode loss and processing cycle duration.
In micro-injection molding, two trends exist in mold processing. One is mirror spark machining, using graphite electrodes for EDM machining due to their minimal loss compared to copper electrodes. The other method is electroforming molds, ensuring high precision but with longer processing cycles and independent hole processing.
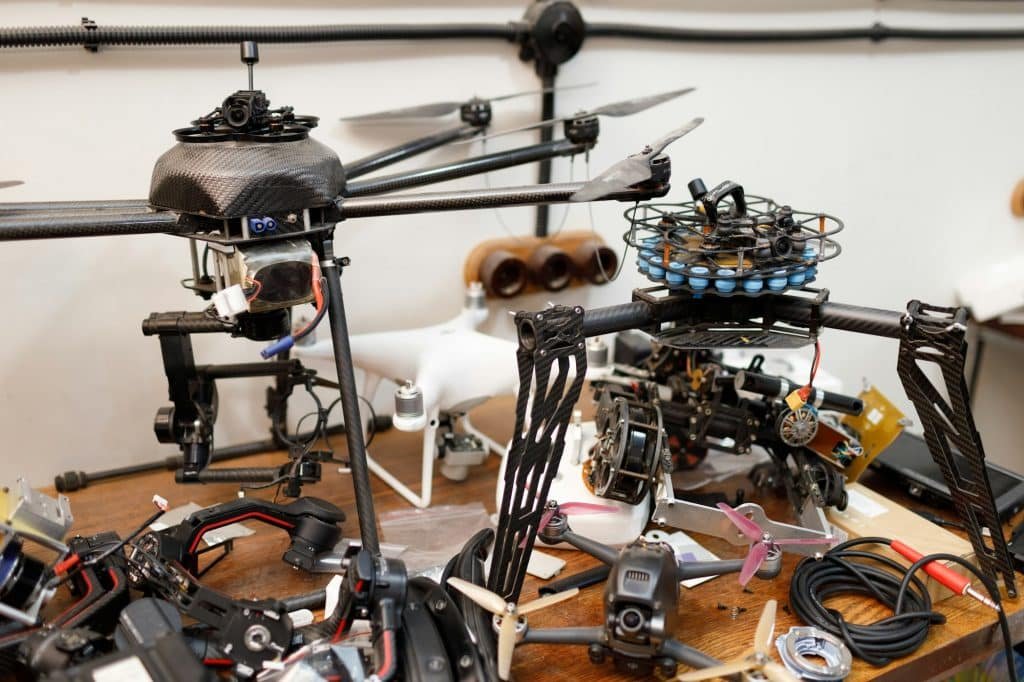
2. Fine-Tuning Mold Temperature
Critical in micro-injection molding, employ rapid heating and cooling systems inspired by high-gloss injection molding, vital for UAV shell injection molding. Optimize mold temperature to aid in filling thin walls and prevent material shortages, while avoiding issues like cycle lengthening and shrinkage deformation.
High mold temperature theoretically aids micro-injection molding, especially for UAV shell injection molding, by preventing thin-wall filling difficulties and material shortages. However, excessively high temperatures may lead to cycle lengthening and shrinkage deformation after mold opening.
3. Innovative Mold Temperature Control Systems
Introduce innovative mold temperature control systems to regulate temperature during injection and demolding, ensuring precise conditions. This system allows precise adjustment of mold temperature, crucial for filling the cavity and subsequent demolding.
4. Ensuring Complete Filling
Maintain proper mold temperature to prevent incomplete filling during the injection process. Control the temperature to ensure efficient cavity filling without rapid cooling, which may cause incomplete filling.

5. Minimizing Material Waste
Utilize warm runner gating systems to minimize material waste in micro-injection molding, particularly for UAV shell injection molding. Traditional pouring systems result in significant material loss due to the small mass of micro-products relative to the material in the pouring system. Warm runner gating systems optimize the injection process, reducing material wastage.
Micro-injection molding, with products weighing milligrams, may experience significant material waste with general pouring systems, a critical concern in UAV shell injection molding. If a general pouring system is used to inject the product, even after optimization and improvement, the mass ratio of the product and the material in the pouring system is still 1:10. Only less than 10% of the materials are injected into micro products, resulting in a lot of pouring system condensate. So, warm runner gating systems address this issue by optimizing material usage and reducing waste.
By focusing on these key points, manufacturers can enhance the efficiency and precision of UAV shell plastic injection mold processing, meeting industry demands for high-quality micro-injection molded parts.