Introduction
Injection molding has evolved to meet the growing demand for complex, multi-material products—ranging from ergonomic tool grips to waterproof medical devices. Two key processes dominate this space: overmolding and insert molding. While both techniques combine materials, they have distinct applications, cost structures, and design outcomes.
For engineers and product designers, choosing the wrong method can lead to wasted budgets, delayed product launches, or compromised durability. This guide breaks down the pros, cons, and ideal use cases for each technique, empowering you to select the optimal process for your project.
1. Overmolding: Process, Pros, and Limitations
Definition:
Overmolding involves molding a secondary material, such as TPE or silicone, over a pre-formed substrate, which could be plastic or metal.

Typical Workflow:
- Create the substrate via injection molding.
- Place the substrate into a second mold.
- Inject the overmold material to bond with the substrate.
Advantages:
- Enhanced Ergonomics: Perfect for soft-touch grips on tools or toothbrush handles.
- Sealing & Insulation: Creates waterproof seals for connectors (e.g., USB-C ports).
- Aesthetic Flexibility: Enables multi-color designs without assembly.
Limitations:
- Higher Tooling Costs: Requires two molds, increasing setup costs.
- Material Compatibility Issues: Not all materials adhere well together (e.g., ABS and silicone).
Case Example:
A power tool manufacturer reduced user fatigue by overmolding a TPE grip onto a nylon handle. The bond strength exceeded 15 MPa, tested via ASTM D638.
Keyword Integration:
- “Overmolding services for soft-touch components”
- “Multi-material injection molding”
2. Insert Molding: When Precision Meets Efficiency
Definition:
Insert molding involves embedding a pre-fabricated part (e.g., a metal thread or sensor) into molten plastic during a single injection cycle.

Typical Workflow:
- Place the insert (metal, electronic) into the mold.
- Inject plastic around the insert.
- Cool and eject the integrated part.
Advantages:
- Reduced Assembly Time: Embed screws, circuits, or magnets directly during molding.
- Cost Efficiency: Single-cycle production lowers labor costs.
- Structural Integrity: The plastic encapsulates inserts, preventing loosening.
Limitations:
- Insert Temperature and Pressure Resistance: Inserts must withstand high temperatures and pressure (e.g., brass over aluminum).
- Limited Design Complexity: Typically suited for simpler geometries compared to overmolding.
Case Example:
A medical device company used insert molding to encapsulate 316L stainless steel sensors in PEEK housings, achieving ISO 10993 biocompatibility.
Keyword Integration:
- “Insert molding services for embedded components.”
- “Metal-plastic hybrid molding”
3. Head-to-Head Comparison: Key Factors to Consider
Factor | Overmolding | Insert Molding |
Cycle Time | Longer (2+ cycles) | Shorter (single cycle) |
Tooling Cost | Higher (multiple molds) | Moderate (single mold + inserts) |
Material Bond | Chemical adhesion required | Mechanical interlock |
Design Complexity | High (undercuts, textures) | Moderate (insert positioning) |
Best For | Soft grips, seals, multi-color | Metal-plastic hybrids, electronics |
4. How to Choose: 5 Decision Criteria
Material Compatibility:
- Overmolding: Ensure proper chemical bonding between substrate and overmold (e.g., PC/ABS with TPE).
- Insert Molding: Verify the insert’s ability to withstand high temperatures (e.g., no warping at 300°C).

Volume & Cost:
- Overmolding: Best for mid-volume (10k–100k units) due to higher tooling costs.
- Insert Molding: Ideal for high-volume (100k+) production with lower per-unit costs.
Part Functionality:
- Overmolding: Vibration dampening? → Go for overmolding services.
- Insert Molding: Need embedded components like sensors or threads? → Choose insert molding services.
Aesthetic Needs:
- Overmolding: Requires seamless multi-color designs.
- Insert Molding: Minimal cosmetic needs—focuses on functionality.
Supply Chain:
- Overmolding: Partner with experienced multi-shot molding providers.
- Insert Molding: Work with vendors skilled in insert-handling automation.
5. Why Partner with BFY Mold?
- Dual-Process Expertise: ISO-certified facilities support both their processes.
- Material Science Lab: Pre-test adhesion (peel tests) and thermal compatibility to ensure top-quality production.
- Cost-Optimized Tooling: Modular molds reduce upfront costs by up to 30% for prototyping and small-batch production.
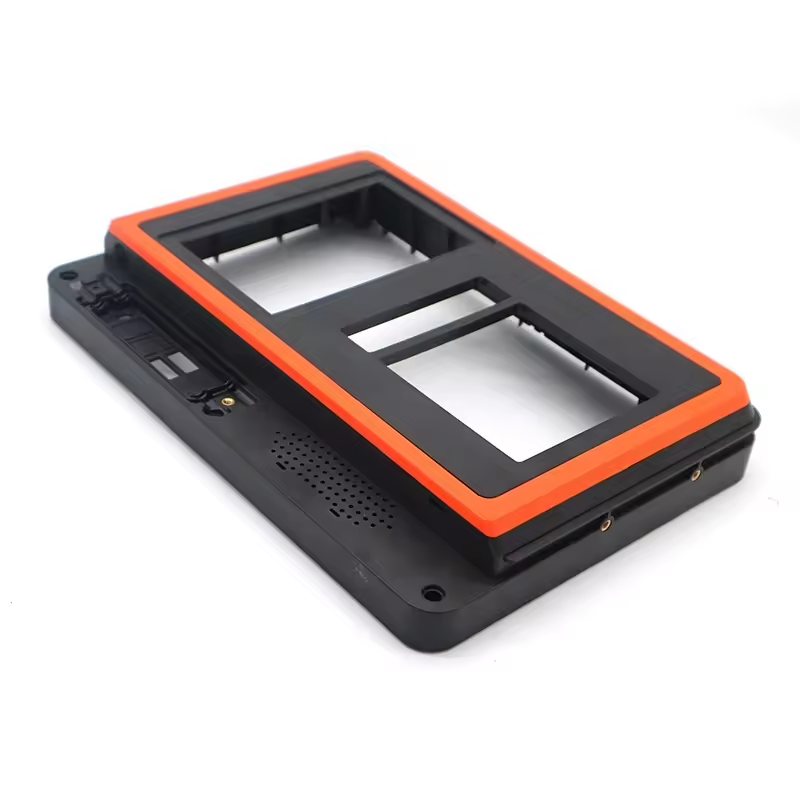
Client Example:
An automotive client saved $120,000/year by switching from overmolded rubber gaskets to insert-molded silicone seals, eliminating the need for post-molding assembly.
Conclusion
Choosing between overmolding and insert molding depends on your product’s specific needs, from material compatibility to design complexity. Overmolding excels in applications requiring ergonomic features and aesthetic flexibility, while insert molding offers a more efficient solution for embedding components in high-volume production.
Still unsure which process fits your project? Contact BFY Mold’s engineers for a free process analysis and material recommendation. Let’s optimize your design for quality and cost.