Introduction
Polycarbonate (PC) exhibits high-performance properties. It is durable, has a good light transmittance rate, and is extremely flexible. PC plastics have become widely used in the automotive, electronics, and medical industries. Its advent means that all of these advantages are generally available together with properties such as fatigue resistance and flame resistance. This guide conducts dissections into what the PC is, its manufacturing processes, and the safety and recyclability of different PC products, with the hope of bringing some real actionable insights to those B2B decision makers.
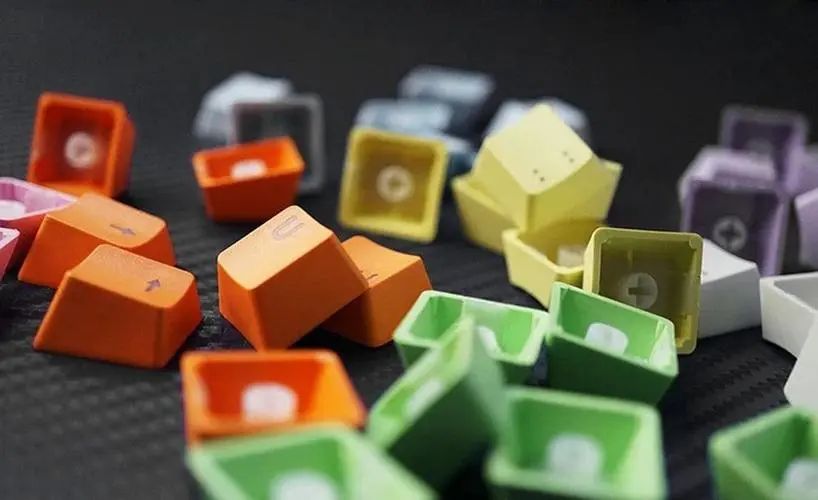
1. What Is Polycarbonate?
Polycarbonate thermoplastics are characterized by their high-impact strength and clarity. In terms of molecular construction, with carbonate groups in the main chain and linked bisphenol-A units at molecular sites nearby–the effect is to bring together toughness and transparency.
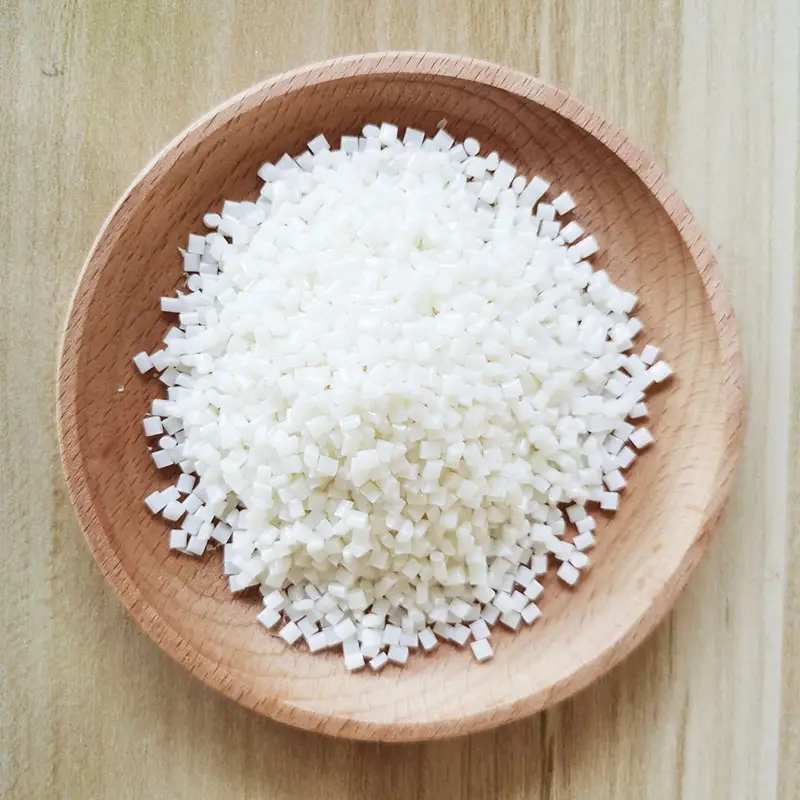
The main characteristics of PC plastic injection molding products include:
- PC Heat Resistance: up to 135°C (275°F), suitable for automotive parts and circuit boards.
- Light: 30% lighter than glass, lower shipping costs.
- Optical Clarity: 89% light transmission, similar to glass.
2. Composition of Polycarbonate
PC plastic is synthesized via the reaction of bisphenol-A (BPA) with phosgene. Modern variants use non-BPA alternatives for food-contact applications.
Core Components:
- Bisphenol-A (BPA): Provides structural rigidity (Note: BPA-free options available).
- Polycarbonate Resins: Enhance UV resistance and weatherability.
3. Processing and Manufacturing of PC Plastics

3.1 Injection Molding Techniques
PC plastic’s high melt viscosity requires precise temperature control (290–320°C) and slow cooling rates to prevent internal stresses.
Best Practices:
- Use molds with polished surfaces to maintain optical clarity.
- Apply gas-assisted molding for complex geometries.
Case Study: AutoLux Inc. reduced defects by 40% using conformal cooling channels in PC headlight molds.
3.2 Extrusion and Blow Molding
- Extrusion: Produces sheets for bulletproof windows
- Blow Molding: Creates hollow products like medical bottles.
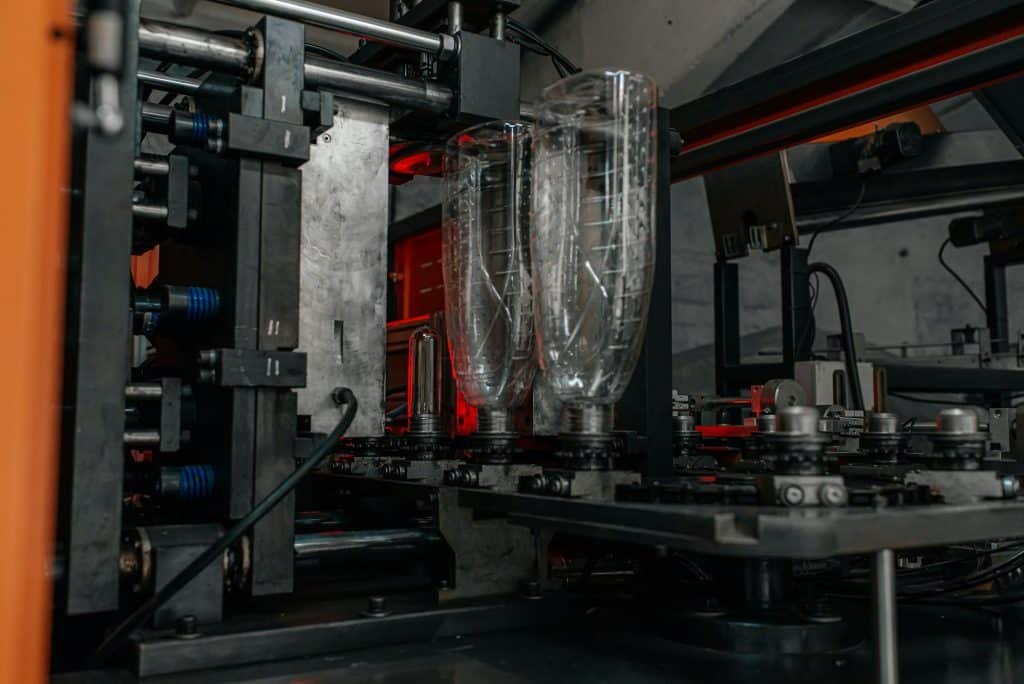
4. Safety and Regulatory Compliance
4.1 Is Polycarbonate Toxic?
In its production process, organic compounds will produce benzene, formaldehyde and other harmful gases at high temperatures, which are harmed. However, as long as they are used and maintained normally, these risks are minimal and not any more likely to generate toxins in the air than your clothing.
- BPA Concerns: Traditional PC contains BPA, which is linked to endocrine disruption.
- BPA-Free PC: Tritan and other alternatives comply with FDA and EU regulations.
4.2 Is Polycarbonate Food Safe?
- FDA Compliance: Approved for food containers (21 CFR 177.1580).
- EU Standards: Meets EC 10/2011 migration limits (<0.05 mg/kg).
4.3 PC Plastic Safety Standards
- ISO 10993: Biocompatible grades for medical devices.
- UL 94 V-0: Flame-retardant certification for electronics.
5. Environmental Impact and Recycling
5.1 Is Polycarbonate Recyclable?
- Mechanical Recycling: Grind scrap PC into pellets (70% efficiency).
- Chemical Recycling: Depolymerize PC into monomers for repurposing.
5.2 Is Recycled PC Safe?
- Contamination Risks: Recycled PC may retain impurities; rigorous washing is critical.
- FDA Guidelines: Permits recycled PC in non-food applications (e.g., automotive parts).
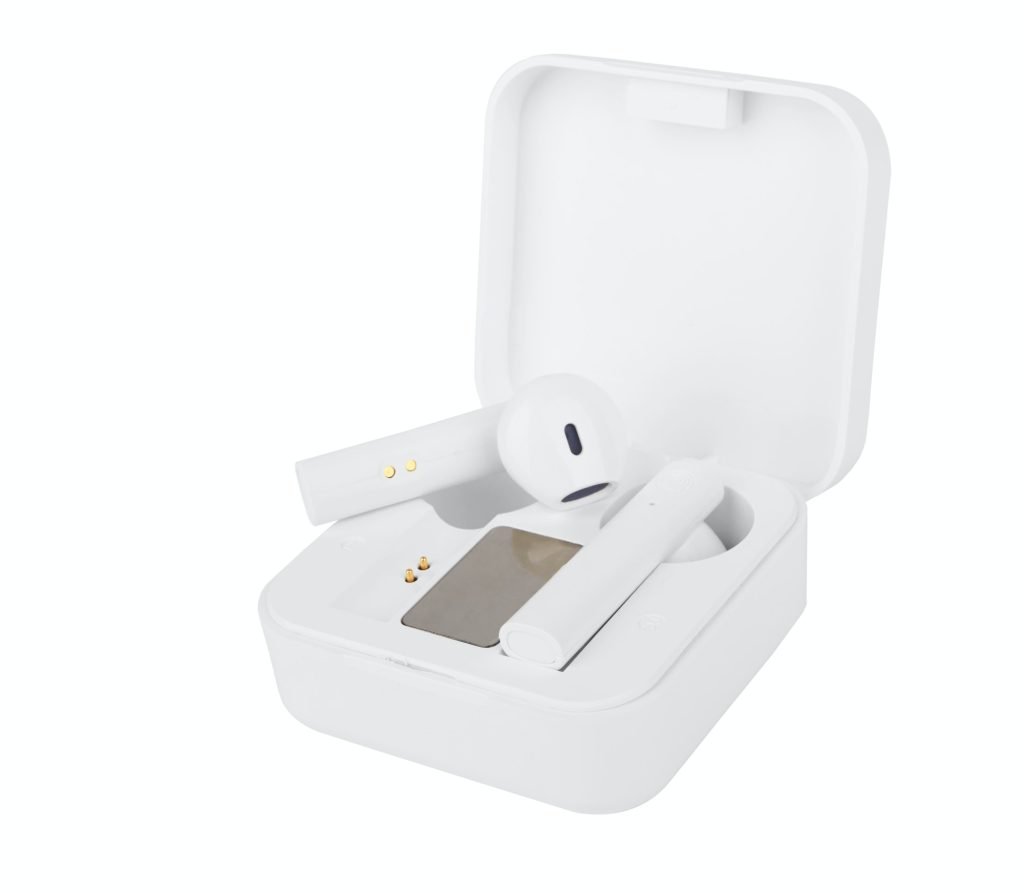
PC vs. Polypropylene: Safety Showdown
Factor | Polycarbonate (PC) | Polypropylene (PP) |
BPA Content | Present in traditional grades | None |
Heat Resistance | 135°C | 100°C |
Food Safety | Restricted (high-temp leaching) | FDA-approved for all food contact |
Recyclability | Complex due to additives | Simple (90% mechanical recycling) |
6. PC Plastic Cost Efficiency in B2B Applications
6.1 Cost Comparison: PC vs. Alternatives
Material | Cost (USD/kg) | Heat Resistance | Impact Strength |
PC Plastic | 3.0–4.5 | 135°C | Very High |
Polypropylene | 1.3–1.8 | 100°C | Moderate |
Acrylic (PMMA) | 2.5–3.5 | 85°C | Low |
Source: ASM International (2024)
6.2 Long-Term Savings
- Durability: PC components last 3–5x longer than acrylic, reducing replacement costs.
- Energy Efficiency: Lower processing temps vs. glass (saves 15% energy).
7. FAQs: Addressing B2B Concerns
1. Can PC plastic withstand sterilization cycles?
Yes, medical-grade PC (ISO 10993) tolerates autoclaving at 121°C.
2. How does PC plastic compare to polypropylene (PP) for packaging?
PC offers superior clarity and rigidity but costs 2x more. Use PP for budget-sensitive items.
3. Are there BPA-free PC options?
Yes, Tritan (Eastman Chemical) and HPX provide BPA-free alternatives.
4. What industries benefit most from PC plastic?
Automotive (lighting), electronics (phone cases), and medical (surgical tools).
5. Is PC plastic suitable for outdoor use?
UV-stabilized PC resists yellowing and weathering for 10+ years.
8. Conclusion
PC plastic remains a top choice for B2B applications demanding heat resistance, optical clarity, and regulatory compliance. By leveraging advanced manufacturing techniques and recycled materials, businesses can achieve cost efficiency while meeting sustainability goals.
Ready to Optimize Your PC Plastic Workflow?
Contact us for a free consultation on material selection and compliance.